Industry needs to become wiser when it comes to incident investigations
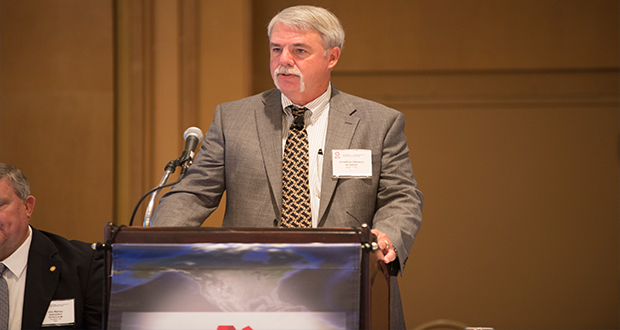
By Kelli Ainsworth, Editorial Coordinator
A company’s response to incidents should result in learning that can be translated into actions to prevent similar incidents from occurring again in the future, Jonathan Henson, Global Well Engineering HSSE Manager at BG Group, said during a presentation at the 2015 IADC Human Factors Conference in Galveston, Texas, on 22 October. “ A smart person learns from their own mistakes; a wise person learns from others,” he commented. Rather than taking a blame-and-shame approach to an incident investigation, companies should focus on training incident investigators to explore how human factors may have contributed to an incident. Based on these learnings, preventive steps should be taken, such as briefing crews on all potential hazards.
Too often, Mr Henson said, when an incident occurs, companies look to find someone to blame, and then disciplines that person. While this may provide a short-term solution, it doesn’t translate into long-term learnings. Further, it fails to consider situational factors that might have led to the error. “It’s not about blame and shame,” he noted. “It’s about why (the employee) did what he did, what the whole team did, and what the OIM was doing at the time, or the drilling superintendent or the companyman.”
Many companies also do not provide incident investigators with training that is thorough enough to delve deeper into the causes of an incident. Mr Henson noted that a sufficient investigation training course should last at least a week and should require attendees to take a test and prove their competence. If more industry employees were certified through such courses, he said, then the quality of the industry’s incident investigations could rise to the level of investigations undertaken by the US Federal Aviation Administration and National Transportation Safety Board (NTSB). “I think we’re rubbish at investigations,” he said. “Just look at NTSB investigations, and look at one of our investigations and compare. They’re pretty good, and I think we can do a lot better.”
A detailed investigation into the causes of an incident might lead to the understanding, for example, that the crew was not aware of all the hazards they face on a rig, Mr Henson said. If they’re unaware that a particular hazard exists, they cannot avoid it. “They don’t know what they don’t know, and if you don’t inform them, how will they know?” he said.
Mr Henson suggested that the learnings that come from incident investigations and discussions with the crew should result in plans that can be followed to avoid similar incidents going forward. These plans should go beyond the bulletins or brief mentions in safety meetings that are often used today, he said. “How many times have we seen a one-pager come out as if that’s going to solve everything?” he said. “It might help, but does it really solve anything?’” Instead, he recommends making what was learned actionable.
One plan of action might be similar to the approach BG Group took on one of its operated rigs in Norway. On this rig, the company had a practice of focusing daily on risk awareness and all the hazards the crew faced. During the entire year-long drilling campaign on the rig, there were only two minor incidents on that rig, and he attributed this to the constant focus on ensuring the crew was aware of all risks and hazards that needed to be mitigated.