Industry hones in on human element to push rigsite safety to next level
Organizations are bolstering training initiatives by addressing communication skills, company cultures and cognitive biases
By Stephen Whitfield, Senior Editor
Companies are constantly re-examining the mechanisms by which they can help their rig personnel avoid potentially dangerous incidents on the rig. In addition to training people to use equipment safely, they are examining the human factors that could lead to error. They have come to understand the importance of soft skills – like communicating openly and effectively about problems, and establishing a culture that encourages that kind of open communication – in helping mitigate those human factors.
“Communication and culture define your protocol,” said Mike Truitt, Director of HSE at Independence Contract Drilling (ICD). “You can have every protocol, procedure and policy in the world, but if you don’t have the culture and the communication driving those policies, it doesn’t matter.”
Understanding the impact that cognitive biases can have on decision making has also become a priority for the industry. Cognitive biases are the predictable, consistent and repeatable mental errors in thinking and processing information that can lead to illogical judgments and even catastrophic incidents. By recognizing how these errors occur, and making efforts to counteract those biases, companies can go a long way in improving safety outcomes.
“If you’re not training and mentoring and providing the guidance to those who are actually out there doing the work, you’re exposing yourself to a new level of risk that nobody in the industry wants to have underneath them,” said Michael Fry, Director at ModuSpec Deepwater Subsea. “The stronger we can make our crews, the stronger we will be as a united team. That’s why we’re looking at new ways to do things in our industry. Why do we have accidents? Let’s understand why that mistake was made, and how do we prevent it from happening again.”
The industry is also working on systems and processes that can help people better understand how to approach potentially harmful behaviors on the rig. For instance, a common military procedure – the Five-Paragraph Order, or SMEAC – has proven valuable for Seadrill in training its offshore supervisors on communicating procedures and managing potential dangers.
“It’s common in the industry to focus on a goal you’d like to achieve and begin creating bespoke plans internally. We often do this when there are, in fact, a plethora of trusted methodologies that already exist externally,” said Neil Forrest, VP of HSE and Sustainability at Seadrill. “I think the key is to try and understand what organizations and industries are doing work comparable to ours. We can learn from them by observing how they manage safety. If there’s a standard that’s effective for them, and our work is similar, it might be effective for us. There’s real value there.”
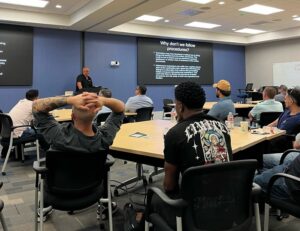
Addressing cognitive biases in safety management
Mr Fry likes to tell the story of an inspection he once performed. He was working on an offshore rig as a Senior Subsea Supervisor, and they were conducting the final inspections on the BOP to ensure that no tools or debris were left on the BOP prior to deployment. He needed to check a component of the BOP that was located in a hard-to-reach location, behind the BOP control pod. It was a check he had done hundreds of times before.
A member of Mr Fry’s team reminded him of the need to put on a harness before climbing up the BOP, yet he decided not to do it. “I’m just stepping up, literally just putting one foot down, stepping up, looking and stepping back down.” However, as he stepped up, the toe of his boot got caught in the pipe work, and he almost fell over the side of the BOP control pod, which would’ve been 50 feet down to the moon pool deck.
This was an example of how cognitive bias can have devastating impacts on safety. Even though he knew the proper protocol for moving around the BOP, he did not follow that protocol because he had never had an issue before, and the check was only going to take less than 20 seconds to complete.
“That was a wakeup call to me that this can happen to anybody. Typically, we accept that things aren’t going to happen to us, and you can develop a cognitive bias just based on not having an issue. And the minute you let your guard down, that’s when something happens to you or someone you know. That’s why we have to reset the way we think about situations,” he said.
Along with BOP inspections, ModuSpec Deepwater Subsea also conducts competency development training, focusing on both traditional well control training, like IADC WellSharp, and what Mr Fry termed “non-traditional” training that looks at crew development, procedural discipline and quality assurance. As part of this “non-traditional” training, the company looks into the relationship between various cognitive biases and safety.
Mr Fry said the industry has a compelling need to see how these psychological processes actually influence real-world operations, and to develop practical approaches to mitigating risk on the rig. For instance, confirmation bias is a type of cognitive bias that refers to the tendency to seek out information that confirms what a person believes to be the state of a situation and ignore information that conflicts with that confirmation.
Addressing cognitive biases on the rig is a top-down process, often requiring a “hard reset” in the way supervisors communicate with personnel on procedures. “When I was working offshore, there were times when my supervisor would tell me, ‘I am your procedure. You don’t need to follow anything.’ When something goes wrong, you find yourself falling into the dilemma of whether I want to keep my job, or I want to do what I know is right but have a supervisor get mad at me? For this to be successful, the crews need to be able to speak up and speak freely.”
Correcting cognitive bias can also be a matter of understanding why people behave the way they do. In ModuSpec Deepwater Subsea’s training courses, participants discuss the “Dirty Dozen” model, which encompasses the various human factors that contribute to errors in different settings. These are lack of communication, distraction, lack of resources, complacency, stress, lack of teamwork, pressure, lack of awareness, lack of knowledge, fatigue, lack of assertiveness, and norms.
Trainees are asked to provide examples of situations where an organization has told them to follow a certain procedure to accomplish a task on the rig, and the trainee chose to do something different because they felt they had a better way of accomplishing that task. Trainees are asked to explain why they felt that way. Oftentimes, Mr Fry noted, the cognitive bias that leads to the failure to follow a procedure is exacerbated by one of the factors in the “Dirty Dozen” model.
“We go through that list, item by item, and we ask people about this,” he said. “Was this a case of a poor procedure? Was there a lack of resources to perform the procedure the way it was outlined by the company? Were there communication problems? As you hone in on it, you start to understand why those problems are taking place, and you can take that back to your organization and identify the habits that you need to fix.”
The industry has grown increasingly receptive to examining cognitive bias, Mr Fry said, noting that drilling contractors are “training their crews to understand the psychology of the way that we think and in the way that we act. And that’s not something traditionally that the oil and gas industry had ever done before.”
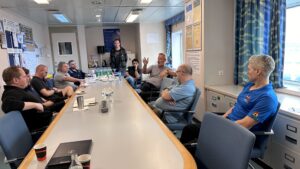
Improving supervisor training
In 2022, Seadrill partnered with E7, a training organization, to incorporate the SMEAC (Situation, Mission, Execution, Administration, Command) methodology into a training program specifically designed for offshore supervisors. The resulting program, SHARED Supervision, reinforces safety learnings with on-the-job “missions” that allow teams to apply the knowledge gained in training sessions in a real-time application.
SMEAC is an acronym used in reference to the “five-paragraph order,” a style of organizing information about a military situation for a unit in the field. It is used by military groups around the world – including the US Army, Navy and Marine Corps – as a guideline for documenting orders and instructions for field operations, so that officers can pass information to their troops effectively.
“SMEAC is a dynamic method for supervisors to look at the skills they need and the topics they need to think about as they’re managing a team,” Mr Forrest said. “It’s defining the elements of what a supervisor should be most concerned with in periods of risk and uncertainty. When we’re on the rig, and we’re doing a job that’s repeatable and pretty straightforward, the risk assessment works pretty well. But when something changes, there’s uncertainty. What looks good now doesn’t look good in 15 minutes or an hour. How do we manage that?”
The SMEAC acronym outlines the procedural framework for organizations to handle issues:
- Situation: Identifying an issue and why the issue is problematic;
- Mission: Identifying what needs to be done about the issue – this is a clear and concise statement of what the organization hopes to achieve;
- Execution: Identifying the steps required to achieve the mission;
- Administration: Identifying the resources needed to execute the mission, and how these resources are to be coordinated; and
- Command: Identifying who’s in charge of executing the mission, who reports to the people in charge and how they communicate with each other.
Seadrill ran a pilot of the SHARED Supervision program on two rigs – one in the US Gulf of Mexico and one offshore Mexico – in 2022. The pilot involved training offshore supervisors in applying the SMEAC framework to their everyday operations. Representatives from E7 held online video conference calls with supervisors over the finer points of the SMEAC framework and the ways in which they can apply that framework to specific issues that the supervisors identified on their rigs – for instance, handling problematic behaviors from rig crews around certain equipment.
Following the conference calls, supervisors took part in week-long “missions” in which they applied the concepts to handle the issues discussed during the call. Supervisors were asked to evaluate their behaviors and the response to the rig crews, and provide a summary for discussion in a follow-up call. The pilot program lasted six weeks on each rig.
“The SHARED Supervision program is aimed at facilitating conversations where peers discuss these topics. It’s not about lecturing someone on theory. Instead, it’s about getting the right conversations going so there’s a common understanding of these concepts,” Mr Forrest said.
The feedback from that pilot was overwhelmingly positive, he added. Initial feedback led to enhancements, which were implemented on four rigs in Brazil and three in Angola. Post-delivery surveys showed 91% positive feedback, with 94% of employees appreciating the practical exercises and over 80% recommending the program to colleagues.
“We are focused on the longevity and sustainability of the program,” Mr Forrest said. “Once the whole fleet’s been through it, we can make adjustments and improvements as we go along. We’ll have a few missions a year and develop classes for new-hires so they can learn. The main thing will be using the missions to maintain these concepts on the rig. We want them established as part of our culture and the way we supervise our teams.”
Communication on the rig
In 2019, ICD noted an uptick in dropped object incidents on its rigs, and “we knew we needed to do something,” Mr Truitt said. That realization led the company to re-examine how it looks at safety management on its rigs. Since then, the company has undergone a shift in philosophy in how supervisors communicate with personnel, and what things to prioritize when inquiring about incidents.
“It’s not about policy or protocols, really. We had to look at how we led and think critically about how we were responding to certain things. There may be a nuance in your body language or tone of voice that makes someone perceive a situation differently than intended, and that perception can become reality in that individual’s mind,” Mr Truitt said.
The shift began with ICD embracing the five principles of Human and Organizational Performance (HOP):
- Error is normal.
- Blame fixes nothing.
- Context drives behavior.
- Learning is vital and deliberate.
- How you respond matters.
Mr Truitt was introduced to the principles while attending the DROPS UK forum in 2019, and in the subsequent year – during which ICD’s operations dramatically decreased due to the COVID-19 pandemic and oil price downturn – he realized the importance they could have in helping better understand the root causes (error traps) of not just dropped object incidents, but all incidents on their rigs.
“Just learning more about human factors and human performance, it made a lot of sense. I felt it was an opportunity to start making that next move. Let’s see how we can fully integrate these principles into our operations.”
This interest manifested in 2022, when ICD conducted offsite learning sessions in Fort Worth, Texas, with its motor hands, drillers and derrickhands. They were provided with an overview of the HOP principles, and the supervisors facilitating the meeting asked for their input on how the company could improve its safety management. Specifically, they discussed where they believed error traps existed within operations or jobs, as well as how they thought the HOP principles could help make safety protocols easier to follow.
Among the topics that came up in these sessions were the importance of communication between supervisors and rig personnel, and the biases that sometimes arise from managers when investigating an incident.
“It’s having to intentionally put aside those biases and pre-conceived notions and go into an investigation or learning session with an open mind and wanting to learn from them. We have to listen to the folks who were involved in the incident and fully understand the processes or the systems that were involved in the incident,” Mr Truitt said. “You can ask people anything after an incident, but if you don’t allow the team members that were involved to express the context of the situation in which the incident occurred, you don’t really know anything, and valuable learning opportunities are lost.”
Following the offsite learning sessions, ICD sent HSE personnel to its rigs to conduct onsite assessments looking at how rig crews handle potential hazards in any activity, from working on the top drive to tripping pipe to cleaning the rig floor. The HSE personnel, working with the drilling superintendents, wrote observations on the hazards they spotted and noted the measures rig crews can put in place to avoid them. Over the past year, the company has conducted more than 300 such assessments, each of which has been incorporated into a document that is available to anyone within the company.
Some of the observations the company has noted in these assessments were behavior related, others were more about physical systems. For instance, in one assessment, the HSE adviser noticed an individual trying to get a magnet out of the possum belly that was collecting metal fragments coming back through the cuttings.
“We’re seeing that he’s having to get on top of a pipe that’s at the bottom of the possum belly to step up less than one foot, to reach over and be able to get this magnet,” Mr Truitt said. “Why did we make the system that way? He’s doing what he thinks is right at the time. He’s just trying to do what he knows needs to be done. That allowed us to sit back and say, we need to fix this. This isn’t right. We need to put a step here. We need to put a platform here. We need to do something to make this more accessible for the employee to do the job.”
The onsite assessments have furthered the application of HOP principles into ICD’s operations because they’ve fostered open communication among rig crews, supervisors and HSE advisers.
“When I first started looking at this, I was apprehensive about how it was going to be received by the folks in the company. But it was eye opening to see how openly they embraced these operating principles. Having conversations with everyone and making sure they understand why we were doing this, and seeing them open their arms and their hearts to accept it, that was eye opening,” he said.
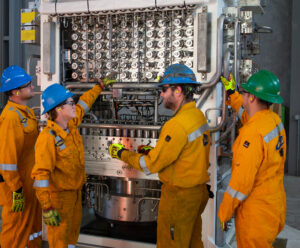
Developing the next generation
For the past 14 years, Noble’s Subsea Development Program has focused on preparing its engineers for maintenance of all the subsea well control equipment on its rigs. Trainees typically come from internal recommendations within Noble, often lower-level rig crew personnel recommended for the program by rig managers. They also include recent graduates of engineering programs, as well as former members of the US military. The trainees spend between 18 and 24 months alternating between classes at Noble’s training facility in Houston, trips to the OEMs that work with Noble, and 28-day hitches on Noble’s rigs to provide comprehensive, immersive instruction.
“We saw a need for our subsea engineers – a highly technical position – to benefit from having an organized training structure, something that’s very challenging to do solely while you’re on the rig,” said Carl Lyle, Well Control Equipment Training and Development Program Supervisor at Noble. “We wanted a lot of that training to happen off the rig, and to put together a complete program for people to come through. And we always have a need for qualified subsea engineers on our rigs, so the training program has helped us push that along.”
In addition to training on the hydraulic equipment, mechanical training, and training on the BOP, classes also cover communications, team building, safe work practices, and learning the policies and procedures critical for safe operation on the rig.
Additionally, practical exercises give trainees experience on specific real-world scenarios. During the rig hitches, trainees are also assigned to designated team leaders to be mentored on the practical application of their classroom lessons. Buford Sullivent, Senior Subsea Engineer at Noble, pointed out that the time on the rig is just as valuable as the time in the classroom. For instance, certain pieces of equipment, like motion compensation systems, are easier to understand on the rig.
“If you go into a classroom and learn about tensioners and CMCs (crown-mounted compensators), it’s great to see pictures and diagrams and training videos, but to actually see it in operation is important. You’re worrying about weighing up the drill string, and actually using the equipment to increase our pressures. That’s really good for the trainees to see that. It’s hard to understand all the training data until you actually see everything moving at once on that ship out in the ocean.”
Along with training on the equipment, Mr Sullivent said, the rig hitches are critical in helping trainees learn how to effectively communicate with others to resolve potential problems on the rig.
“You have to understand how to communicate with different departments on a rig. When I’m out there with training participants, we come up with a scenario for working on a problem, and they need to know whom to call and how to ask them for information. It’s about using those communication channels that we need on the rig. They have to know that part,” he said.
The training program offers a path to advancement within the company. Upon graduation, trainees are assigned to a rig as an assistant subsea engineer, where they receive additional mentorship from the subsea supervisor. Typically, within two years, the graduates are promoted into a subsea engineer position. Several trainees have ultimately moved into senior positions.
“The best way to increase safety is to have properly trained personnel. It’s very important that we can show our customers the level of training and the competency of the people who are working on our rigs, specifically those who come out of this program, because that’s the only metric we have,” Mr Lyle said. “Several of the people working on our well control equipment, or working in the office, have come through that program. They’ve gone all the way up to subsea supervisors or subsea superintendents. Even after that, some of them have been promoted to management and director positions. I think that really shows the quality of people that we have in the program.” DC