Industry 4.0: Oil & gas could benefit from outward search for innovations
Looking externally for automation, digitalization opportunities may prove cost effective amid downturn and R&D budget cuts
By John Barratt, Oil & Gas Innovation Center
As this article was being written in June, there were approximately 300 drilling rigs operating in North America, the US frac spread count was around 50, and every drilling contractor and completions company was suffering financially. Petroleum industry R&D and product development budgets, which were not especially robust prior to the COVID-19 crisis, will likely be reduced even further, along with R&D staffing levels.
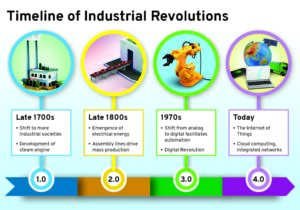
This is one of the most rapid and severe downturns ever experienced by the petroleum industry. However, many other industries are also very cyclical, and they continue to position themselves to survive and prosper by embracing Industry 4.0 automation and digitalization technologies.
Given current operating conditions, it is very challenging for drilling and completion companies to dedicate substantial resources to the development of new technologies. This is unlikely to change until oil prices rise and operating conditions materially improve. Ironically, the drilling and completion sectors would see improved efficiencies, reduced operating costs and better profitability if they widely adopted Industry 4.0 technologies, such as artificial intelligence (AI), wireless sensors, edge computing, augmented reality (AR), virtual reality (VR), digital twins and the industrial internet of things (IIoT). Fortunately, there are substantial opportunities for drilling and completion companies to source relevant Industry 4.0 technologies from other industries and from startup companies.
Industry 4.0, the fourth industrial revolution, builds on existing industrial technologies and adds new innovations. When fully implemented, it will lead to much less human involvement in hazardous manufacturing and production environments, greater automation, smart machines that can analyze and diagnose issues, as well as faster response times to changing business conditions. Coincidentally, the automation and digitalization solutions associated with Industry 4.0 are very synergistic with the future needs of the drilling and completion marketplace.
How AI is changing other industries
The goal of AI is to build smart machines capable of performing tasks normally associated with human intelligence. AI and machine learning, which is a subset of AI, are often touted as technologies of the future. However, AI is already widely deployed in multiple businesses, including the ubiquitous natural language processing tools Alexa and Siri.
A recent report by KPMG, “Living in an AI World,” highlights the impact of AI on five industries: healthcare, financial services, transportation, technology and retail. One conclusion the report draws is: “Within 10 years, we’ll likely be in the passenger seats of autonomous vehicles. In less than five, we’ll access our money without ever swinging by a local bank. And in less than two, we should see big improvements in how we diagnose disease, avoid traffic delays and prevent fraud.”
Any concerted effort to find relevant technologies among early-stage companies needs to look outside of the traditional oil industry states.
AI is sometimes viewed as a threat to humans, but AI is principally a means to augment human capabilities. For example, in healthcare, multiple companies are evaluating AI solutions to read patient X-rays. In hospital tests, one of these AI algorithms reads chest X-rays and detects the onset of pneumonia with an accuracy equal to a trained radiologist. For the latter, manually reading a chest X-ray takes 20 minutes. The AI algorithm accomplishes the same task in 10 seconds, and the algorithm never becomes fatigued. Rather than replacing the radiologist, AI expedites diagnosis and care. In the drilling and completion arenas, AI also has potential to accelerate decision making and improve efficiencies.
Machine-to-Machine Communications and IIoT
Machine-to-machine (M2M) communication allows devices to exchange information and perform actions without the manual assistance of humans. M2M has been deployed for many years in other industries. For example, smart vending machines employ M2M to send an alert to a distributor’s network when restocking is necessary.
IIoT expands M2M communications by adding big data analytics and even AI to collect and analyze data from an almost unlimited array of networked machines or sensors. The insights derived from IIoT deployments reduce downtime, increase efficiencies and improve profitability.
Over a decade ago, Rio Tinto launched its Mine of the Future initiative, an excellent example of a widespread deployment of IIoT. The latest iterations of this program include autonomous drilling machines working in the mines, autonomous trucks for moving ore, autonomous trains for moving ore from the mines to ports, and a centralized command center that monitors the vast amount of data derived from the thousands of sensors on these autonomous systems. In their roadmap, Rio Tinto even has plans for autonomous ships to transport the ore to customers.
Sensors and Edge Computing
The digitalization of industrial sensors is an integral part of Industry 4.0 initiatives. Sensors are becoming smaller and lower cost, require less power and are increasingly compatible with harsh environments. Along with traditional battery-powered sensors, there are also numerous sensors powered by energy-harvesting technologies. Further, several early-stage companies are commercializing millimeter wave, radio frequency and infrared technologies for wirelessly charging the sensors without actually contacting them.
As the number of sensors increases, edge computing becomes increasingly important for processing the sensor data at the source, rather than transmitting to the cloud or a network location. One of the key advantages of edge computing is less latency. Sending data to a central location and waiting for the results takes time. Many of the sensors on autonomous vehicles rely on edge computing because latency imperils the safety of the vehicle occupants and nearby pedestrians.
AR, VR and Digital Twins
AR is an enhancement of the real world with digitally generated overlays, while VR takes this a step further by immersing the user in a completely virtual environment.In addition to obvious gaming applications, AR and VR have many other uses, with AR likely being more applicable in the industrial world. For example, in the construction industry, AR allows managers to walk through a project at various stages of completion to spot potential problems before the project is finished. Meanwhile, VR is emerging as a valuable teaching tool in the healthcare industry. Medical students can now watch VR surgeries and dissect VR cadavers.
Digital twins are are being widely used in manufacturing, healthcare, mining and many other industries. An integral aspect of Industry 4.0 is the interaction between advanced technologies. For example, digital twins can incorporate inputs from wireless sensors and utilize other Industry 4.0 innovations, such as edge computing, AI, IIoT, AR and so forth.
Access to Technologies
Given the current state of oil markets, the best approach is to look externally for Industry 4.0 technologies. This type of outward-looking technology program makes sense because leading companies in other industries spend far more on R&D than their counterparts in this industry. Strategy&, which is part of the PwC network, collects detailed information about how much publicly traded companies spend on R&D. Its 2018 report shows that the 10 publicly traded companies that invested the most on R&D altogether spent an impressive $138 billion. Amazon topped this list, with R&D expenditures of $22.6 billion. No petroleum industry company appears on the list until No. 84, with R&D expenditures of $1.9 billion.
In addition to larger and more established companies, there are also thousands of startups and early-stage companies developing technologies that could be integral to the Industry 4.0 revolution. Increasingly, many of these small companies are not based in the United States. According to work done by the Center for American Entrepreneurship, 20 years ago American companies received 90% of all the funds invested by venture capital firms. Today, American companies receive only 50% of those venture capital dollars. Certainly, there are other funding sources available for early-stage companies, but the steady flow of venture dollars out of the United States confirms that entrepreneurship is increasingly global.
Within the United States, most of the venture capital-funded startups are not located around traditional oil industry hubs. The latest National Venture Capital Association Pitchbook shows that less than 4% of Q1 2020 venture dollars went to companies located in the four-state region of Texas, Oklahoma, Louisiana and Arkansas.
Any concerted effort to find relevant technologies among early-stage companies needs to look outside of the traditional oil industry states and increasingly needs to have a significant international emphasis.
Conclusions
Many of the technologies integral to the Industry 4.0 revolution are also highly relevant for the petroleum industry. Even when oil and gas prices recover, the petroleum industry is unlikely to increase R&D expenditures enough to match the investments of large companies in other industries – or the venture capital dollars flowing into startups that are developing AI, edge computing, wireless sensors, IIoT, AR, VR and digital twin technologies.
For the petroleum industry, the most cost-effective strategy is to look externally for these valuable Industry 4.0 technologies that can drive further automation and digitalization in drilling and completions. DC
Mine of the Future is a trademark of Rio Tinto.