Bishop Lifting expands footprint with Worswick Group Holdings acquisition
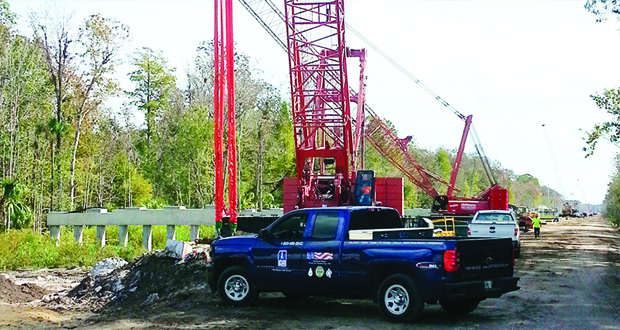
Bishop Lifting completed acquisition of Worswick Group Holdings, with 10 operating locations across Florida. The Worswick family of companies includes Bubba Off-Road Recovery Gear, Florida Wire & Rigging Supply, Secured Global and Academy Training Center.
Worswick Group marks Bishop’s 11th acquisition since 2012 and is the fourth add-on acquisition since Altamont, Bishop’s parent company, acquired the platform in February 2022. While the company recently announced its rebranding to Bishop Lifting, Certified Slings and Supply will maintain its local branding.
“We look forward to partnering with Bishop to build upon the foundation that my family has solidified over decades,” said Doug Worswick, prior Worswick Group Holdings owner who accepted a leadership role at Bishop Lifting in conjunction with the closing. “At our core is a culture of service, quality and teamwork and we are honored to become part of the team that was founded by David Bishop, whose passion for serving his team and customers clearly carries on through Bishop Lifting’s leadership today.”
“We’re excited to continue our growth through this acquisition of a company that contributes great people and culture, as well as establish a physical presence in the Florida market,” said Harold King, President of Bishop Lifting. “Doug and his team have built a reputation for exceptional customer service across a number of end markets including the entertainment and mining industries. We look forward to building on their success as we continue to expand our national footprint to serve customers locally with our deep industry knowledge and high-quality products.”