2016 IADC/SPE Drilling Conference Abstracts
Tuesday, 1 March
Case Studies – Fixing Problems
IADC/SPE 178878
Multi-Zone Intelligent Completions for Interference Test Data Gathering Onshore Kenya. J.S. Ure, Tullow Oil; A.D. Wenk, Tullow Oil.; T.E. Asbey, Tullow Oil; M. Jha, Tullow Oil; P.A. Peytchev, Tullow Oil
Objectives/Scope: This paper presents the completion design selected and the operational challenges which have been overcome by Tullow Oil in appraising its discoveries in the Turkana region in remote north-west Kenya. These fields are characterised by multiple pay zones spread over relatively long intervals of 800 – 1,000 m. Well TDs are typically around 2,300 m MDRT and the productive zones to date have been sub-hydrostatic in initial pressure. The reservoir fluid is a waxy crude oil (35 – 40% wax content) with low GOR. Flow assurance is a key aspect of the completion design, as the reservoir temperature of the shallower zones is close to the wax appearance temperature (WAT). Methods, Procedures, Process: Until late 2013 the testing of discovery and appraisal wells was rig based, with zones flowed in a ‘bottom-up’ sequence. Using this approach, a five zone well test would typically take 50 – 60 days. The initial focus of well design activity was to increase efficiency of the testing operation however Tullow decided to accelerate its area development planning based on the significant exploration/appraisal drilling success in the basin. Subsequently, completion design efforts became driven to meet a subsurface requirement for the acquisition of transient interference test data from Extended Well Testing involving five wells in two of the discovered fields. The approach which has been successfully implemented has been to make all well testing rigless after the installation of a multi-zone intelligent completion. The completion is complex and consists of a Halliburton digital hydraulics controlled Interval Control Valve (ICV) and downhole pressure/temperature gauge at each completed zone. Zonal isolation is achieved using stacked feedthrough packers above each zone. Downhole heating is incorporated via electric cables for flow assurance and performance evaluation of these is achieved in the two EWT production wells with fibre optic cable distributive temperature sensing. Artificial lift is provided by low speed, long stroke hydraulic rod pumps. The completion was originally designed to be installed inside 9.625-in. casing but the opportunity to realize significant well construction cost savings and to minimize environmental impact has also been taken by successfully trialling a slimmer well design using 7-in. production casing in the three observation wells. Results, Observations, Conclusions: This approach, where the rig is moved off after installing the completion, has resulted in rig time savings of approximately 30 days per well, in addition to providing the flexibility to acquire zone specific transient well test data. Novel/Additive Information: The bigger prize is applicability of the approach to field appraisal data gathering in any discovered field enabling the acceleration of development planning and reduction of the time to first oil production. Additionally, adoption of the slimmer well design will result in significant development well CAPEX saving.
IADC/SPE 178780
Solid Expandable Solution to Qualify Existing Non-Sour Service Production Casing. J.D. Contreras, ConocoPhillips; F. Gamarra, ConocoPhillips; J.L. Becnel, ConocoPhillips; G.G. Galloway, Weatherford
Objectives/Scope: In the early development of the EagleFord Field in South Texas, the initial well design equipped wells with non-sour service P-110 production strings. After the early stages of production, some of these early wells were found to produce increasing levels of H2S, which posed the problem of sulfide stress cracking at shallow wellbore depths because of relatively high H2S partial pressures and associated low formation temperatures. To mitigate this risk, production packers were run to protect the production casing in wells with H2S partial pressures more than 0.05 psi. As these wells were depleted to lower flowing pressures, production was maintained by intermittently producing. This method was used because of limited or no artificial lift options for wells with non-sour service production casing. A solution allowing artificial lift was needed to better maintain and sustain production, to extend the utility of these wells, and to allow future recovery of the potential reserves. Methods, Procedures, Process: Expandable casing technology was ultimately chosen as a solution to maintain well integrity and enable implementation of artificial lift (gas lift). This operation involved the running of an expandable liner to cover and protect the section of the casing susceptible to sulfide stress cracking. A solid expandable tubular designed to support the corrosive environment was successfully tested and qualified for sour service in extreme corrosive conditions by ConocoPhillips metallurgists, who adhered to sour service qualification A.2.1.6 and Annex B of NACE MR0175/ISO 15156 standards. Additional testing was performed to ensure that the required length of the chosen liner could be run while being held at surface. Normally, these liners are left free at the top so that they can slightly shrink in length to avoid high tensile forces as they are expanded outward. The liner also passed these tests performed independently by the service company. Results, Observations, Conclusions: The team proceeded to install the solid expandable liner, from 7,047 ft (where the temperature was high enough that H2S effects were minimal) to surface to protect the existing 5 1/2-in. P-110 casing. The ID of the completion changed from 4.776 in. (original id) to 4.140 in. (expanded liner ID). The well was then completed with 2 3/8-in.-tubing, a production packer, and traditional side-pocket-mandrel gas lift. Currently, the well is producing on continuous gas lift with the casing protected by the expandable liner. Novel/Additive Information: It is important to mention that this is the longest solid expandable liner installed in the world (March 2015). The expandable liner provided an enabling solution that allowed implementation of the optimal artificial-lift method to recover additional resources within the drainage area.
IADC/SPE 178786
First Successful Implementation of an Advanced Fibrous Organic Based LCM and Optimized Casing Design in Europa: A Case Study From Drilling a 6022m HPHT Exploration Well in Vienna Basin, Austria. K. Abdelaal, R. KNEZEVIC, K. Ovrevik, OMV Austria; R. Husodo, Drilchem
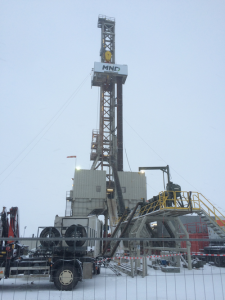
Objectives/Scope: This paper lists technical challenges encountered recently during drilling the HPHT exploration well X to 6022m and describes how these new fibrous organic LCM have proven their value in all sorts of lost circulation applications in the Vienna basin. This case represents the first application of specialized organic fiber LCM in Europa. The author will also elaborate on the narrow mud window available and the main drivers for well design along with contingency concepts. Methods, Procedures, Process: The operator identified a special lost circulation product made of organic fiber which has the characteristics that it is plastic, deformable and can be squeezed into the loss zone. This produces a seal over the loss zone with an internal filter cake rather than forming a high fluid loss filter cake on the wellbore itself. Several pills with this specialized lost circulation products were used achieving excellent results when applied in a very specific manner (described in the paper). Detailed decision-tree charts, characteristics and wettability of fibers, function of the patented material and treatment will be highlighted in the paper. Results, Observations, Conclusions: XYZ field in Austria has a history of mud losses ranging from continuous seepage to severe losses. Several attempts were made to explore the referred to structure without success. The main uncertainties in predrilling the well were the magnitude of the overpressure from Alpine tectonics and the severe losses in Olistolithe (part of Jurassic formation) which was the root cause of failure in previous attempts since its thickness was unknown. The operator was able to control the pressure ramp at 3371 m in the 12 ¼-in. hole. Drilling was resumed but was forced to stop again at 3821 m when severe losses beyond 50 cu m/hr were encountered which prevented the operation’s ability to drill ahead. Several attempts to cure the losses with different lost circulation products were not successful. The choice faced was either to run the casing earlier than planned or attempt a new solution to control the severe losses. By deploying this technology, the Operator was able to continue drilling ahead to 4496 m where the 9 5/8-in. casing was run and cemented. Severe losses were encountered in the 8 ½-in. hole and the operator was able to cure them successfully by applying the techniques developed in 12 ¼-in. hole. Novel/Additive Information: Successful implementation of this advanced technique allowed the operator to drill the well using a three string casing design with a final hole size of 8 ½ in. without reducing the mud weight. The level of success achieved by using these materials means it should seriously be considered as the preferred standard practice for curing any type and volume of losses.
IADC/SPE 178813
Real Time Reservoir Mapping While Drilling Reduces Risks, Geological and Fluid Position Uncertainty in the Gulf of Mexico. S. Leveque, Schlumberger; D. Walz, C. Wolfarth, J. McCarty, ANKOR Energy; L. Castaneda Zigala, M. Alexander, C.L. Fulton, H.O. Kadir, Schlumberger
Objectives/Scope: Reservoirs in the Northern Gulf of Mexico (NGOM) are predominantly drilled with low angle wells. Drilling a well horizontally presents its own set of challenges. Mississippi Canyon block 22/21, operated by ANKOR Energy embodies the significant drilling challenges sometimes found in the NGOM reservoirs. The “H Sand” reservoir is a low resistivity (3 to 5 ohm.m) reservoir bounded by a northeast/southwest fault. The overburden is uniform for more than 200 ft true vertical depth (TVD) above the reservoir, making the landing challenging with conventional well placement techniques. ANKOR Energy was planning a 2,300-ft lateral section to be drilled close to the gas-oil contact (GOC). Early water production was observed in the offset well located at the toe of the planned well, raising questions about the current position of the oil-water contact (OWC). Landing this well was challenging from both a geological and drilling point of view as a 3D trajectory was required to avoid the fault and offset wells. Methods, Procedures, Process: In light of these challenges, ANKOR Energy decided to use the newly commercialized deep directional resistivity (DDR) tool with a detection range of more than 100 ft, enabling the detection of the top of the “H Sand” reservoir long before landing. In the lateral section, the tool was used in conjunction with an integrated petrophysical platform to map the top of the reservoir, detect the OWC, and identify the lithology and fluids present while drilling. Results, Observations, Conclusions: While landing the well, the top of the “H Sand” reservoir was detected 48 ft TVD away, 10 ft deeper than expected. The DDR tool enabled the well to be confidently landed despite the lack of correlation markers and depth uncertainty of the “H Sand” reservoir. The OWC was detected more than 70 ft below during the landing section even though the bit had not penetrated the “H Sand” reservoir yet. The top of the reservoir and the OWC were mapped throughout the length of the lateral section along with the lithology and fluid content. Towards the toe of the lateral section, near a producing offset well, the OWC, still 50 ft below the current trajectory, was observed to be rising up and getting closer to the well. TD was called early to avoid premature water production. Water coning was confirmed as the reason behind early water production in the offset well. Novel/Additive Information: The use of this technology during the landing and the lateral section of the well significantly reduced the risk associated with geological uncertainty as well as the fluid contact position providing critical information for field management planning.
Innovating Drilling Into Extreme Environments
IADC/SPE 178857
A challenging HPHT Operation Supported by Dynamic Real Time Simulation, Forecasting and 3D Visualization. J. Nabadi, R. Rommetveit, eDrilling Solutions; J. Wessel, Maersk Training Centre A/S; L. Scott, Wintershall
Objectives/Scope: Dynamic Real Time Simulation, Forecasting and 3D Visualization was utilized extensively in support of a very challenging HPHT drilling operation in the Norwegian Sea. The well was a vertical exploration well in the Haltenbanken area. Methods, Procedures, Process: In preparation to the operation, an advanced training session was performed using a dynamic downhole training simulator linked to a topside rig simulator, for training of the drilling teams. A real-time link was established with the operation, and WITSML data in addition to all well, fluid and string data was streamed into a dynamic, real-time simulation system. This simulation system provided the following: RT dynamic modelling of the pressure (ECD) and temperature profile in the wellbore; the cuttings distribution and its effects on the ECD; automatic look-ahead simulations of ECD and temperatures on the fly was performed with the calibrated models as support for decisions; RT profiles of simulated versus measured pressure at the PWD, and simulated versus measured standpipe pressure; RT dynamically updated 3D Visualization of the downhole wellbore with a continuously updated risk picture made available for the drilling teams. Seamlessly linked to the RT system was a sophisticated what-if and planning model. 24-hour forecasting of operation was provided every day, and this gave a very good indication of future possible operational impacts. In addition to 24-hour forecasting, pre-planning simulations of upcoming sub-operations as well as what-if simulations on the fly were performed. The results from these simulations were used to update the risk register and made available in the 3D Visualization window. Results, Observations, Conclusions: Three specific cases will be discussed in the paper: pre-simulation of running the 13 3/8-in. casing; pre-simulation of cementing the 13 3/8-in. casing; RT modeling of ESD in case of mismatch between rig calculated and measured values. In these cases the simulations provided valuable results which increased the risk awareness and prevented problems. The paper will also discuss the RT 3D Visualization and its impact on reducing risks and communicating the dynamic risk picture. The operation was successful, and the results from the simulation system was a contributor to this. Novel/Additive Information: The total simulation system with infrastructure, models and challenges will also be presented.
IADC/SPE 178863
The Use of Wired Drillpipe Technology in a Complex Drilling Environment Increased Drilling Efficiency and Reduced Well Times. R. Teelken, B. Van Burkleo, National Oilwell Varco; O. Rossa, Baker Hughes Drilling Services; S. Schils – Van Der Starre, Total Norge A/S
Objectives/Scope: This paper presents and discusses the results of a case study where Wired Drillpipe (WDP) technology was implemented on the Martin Linge offshore field development project in the North Sea for Total E&P Norge AS in Norway. Martin Linge’s resources consist of an oil reservoir and several, deeper, structurally complex, high pressure gas and condensate reservoirs. The oil reservoirs will be developed with long horizontal wells and several deviated wells will be drilled to unlock the gas and condensate reserves. The field was initially discovered in 1975 but proved too complex to develop at the time. Over the years several exploration and appraisal wells were drilled within a narrow pressure window, with multiple BHA runs per section. The complex drilling environment posed many challenges including severe losses, unstable formations and excessive downhole shock and vibrations resulting in poor MWD/LWD signal. Methods, Procedures, Process: WDP telemetry enables bi-directional, high speed data transmission to and from downhole tools at speeds up to 57,600 bps (Olberg et al. 2008). Conventional telemetry methods only provide very limited bandwidth for real-time data transmission and can suffer from signal reliability under adverse conditions, for example: no mud pulse data transmission to surface when pumps off or at flowrates below tool settings, and decoding issues during high levels of downhole shock and vibrations. WDP technology was implemented on the Martin Linge field development from the start. The technology introduction cost off-set against the quantifiable benefits for the project was calculated close to break-even. Furthermore the high upside potential associated with the use of this technology should allow improved well placement and have a positive effect on the quality of the drains drilled. Results, Observations, Conclusions: This paper will summarize how the high-speed telemetry provided by WDP enables wells to be drilled without the typical limitations imposed by conventional telemetry methods. The resulting efficiency gains and quantified time savings of the wells drilled with WDP telemetry when compared to the offset wells, drilled with conventional telemetry system, will be presented. Novel/Additive Information: The analysis will focus on two areas of efficiency and performance improvement. Firstly, the quantified data transmission time savings due to the real time high-speed transfer of critical data between downhole and surface will be discussed in detail. Secondly, the improvement in drilling performance, well placement and reservoir section length due to the real time availability of memory quality formation evaluation data and drilling data, will be discussed.
IADC/SPE 178771
Low Solids Shear Dependent Fluid System to Plugs Zones for Preventing Fluid Influxes and Losses. J.A. Urdaneta, Halliburton; K. Ravi, Halliburton; J. Pacheco, T. Joseph, Halliburton; O. Jaramillo, J. Patiño, Emerald Energy
Objectives/Scope: Lost circulation and influx from sections of high-pressure zones is a recurrent challenge and high-cost event in the oil industry, especially in mature fields or weak-fracture-gradient zones. These can significantly increase the operation cost, non-productive time (NPT), possibility of stuck pipe, and well integrity challenges. Lost circulation can be defined in a variety of ways, from partial losses to total losses, in a variety of formations, including highly-permeable, fractured, or cavernous formations. Loss circulation materials, such as particulates, can be and have been successfully used to plug smaller fractures and permeable zones. The challenge is when the losses cannot be stopped using particulates because of the loss magnitude. The industry has used various chemical solutions to overcome this challenge, with mixed results. Particulates are usually not successful in plugging high-pressure zones to help prevent fluid influx. This paper presents a low-solids loss circulation solution that develops rapid gel strength when the shear rate decreases. The gel strength buildup is based on polymers and nanomaterials in the fluid system. When the fluid enters the formation, it develops gel strength quickly because the shear rate is much lower in the formation. This helps the fluid continuously flow into the zone or be expelled from the zone. Once the gel strength has developed, the system develops nominal compressive strength to adhere to the formation and thus helps prevent displacement during subsequent well operation. The fluid is shear thinning and hence easily enters the formation zone and does not flow continuously, as it gels upon entering the formation. The low solids and low rheology under shear means that it can be easily pumped through the drillbit without having to pull out of the hole. A number of jobs have been successfully completed by pumping the solution through the drillbit. A case study from Colombia is described in this publication. Methods, Procedures, Process: In this study, the described system was pumped into a high-pressure zone to isolate an unconsolidated sand formation. Initial attempts to isolate the zone included a bradenhead squeeze job, which was unsuccessful, and fluid influx from the zone was observed during subsequent well operations. Results, Observations, Conclusions: In this study, the same characteristics described above were successful in preventing fluid influx from a high-pressure zone into the well during subsequent well operations. Novel/Additive Information: The fluid system and process described in this paper should help the industry in shutting off streaks of high-pressure zones and cure loss of fluids into the formation.
IADC/SPE 178788
Fully Mechanical Vertical Drilling Tool Delivers RSS Performance in Vertical Drilling Applications While Providing an Economical Alternative to Conventional Rotary Steerable Systems Set-Up for Vertical Hold Mode. S. Jones, C. Feddema, TurboDrill Industries; J. Castro, Scout Downhole
Objectives/Scope: A fully-mechanical vertical drilling tool has been developed to provide the economics of vertical drilling with a conventional steerable motor and the performance and borehole quality of a rotary steerable system. Through case studies, we examine the feasibility and performance of the vertical drilling system using instrumented downhole sensors. In addition, the 100% mechanical vertical-seeking control system will be explained. Methods, Procedures, Process: The fully-mechanical vertical drilling tool provides autonomous vertical control without the use of high-cost, vibration-sensitive electronics. The tool works in a “push-the-bit” configuration with four mud-operated pads located close to the bit, which continuously push the borehole wall to seek verticality. High-temperature downhole sensors and electronics were instrumented in the tool to examine the effectiveness of the vertical-drilling mechanism. Additionally, a compact, self-contained three-axis inclinometers and three-axis shock sensors were deployed in the tool (3/4-in. diameter and less than 4-in. length) to capture downhole dynamics of the tool. The vertical drilling tool was designed with improved durability for high weight on bit and high-temperature applications. It can withstand the most challenging environments while running peak drilling parameters to improve ROP (rate of penetration). Results, Observations, Conclusions: An operator drilling in West Texas was historically using steerable motors in their vertical sections, however they struggled to maintain verticality due to the high formation dips, fractured formations and faulted zones. Utilizing the vertical drilling tool allowed them to drill 6066 ft of 7 7/8-in. hole at an average ROP of 98.7 ft/hr in 61.4 hr, compared to the nearest offset wells which were taking approximately 160 drilling hr. The average inclination was maintained at less than 0.7˚, while the average inclination of the nearest offset well increased to inclinations of 3˚. To date the vertical drilling system has been used in 1,220 runs, accumulating 77,248 circulating hr and 4,072,335 ft drilled. The data retrieved from the instrumented sensors confirmed the effectiveness of the purely-mechanical verticality-control system, showing at 0.5˚. Inclinations, the tool was self-corrected to steer back to vertical. A compact downhole dynamics tool installed in the vertical drilling tool confirmed high-resolution inclination changes in various drilling conditions and revealed downhole dynamics associated with challenging vertical-drilling applications. Novel/Additive Information: A fully-mechanical vertical drilling tool has been designed and developed with 100% mechanical “intelligent” control system, which autonomously seeks verticality. Because no temperature and/or vibration-limiting electronics are used in the vertical-drilling tool, the system is rugged and durable while providing superior vertical drilling performance and enhanced ROP. Downhole instrumented sensors were used to confirm the value of the above control mechanism. A compact downhole dynamics recording device has provided new insights in challenging vertical drilling applications.
Extended Reach Drilling
IADC/SPE 178859
Long Reach Well Concept. S. Stokka, E. Cayeux, B. Aas, Intl Research Inst of Stavanger; D. Gardner, International Research Institute of Stavanger; A. Saasen, Det Norske Oljeselskap ASA; T. Larsen, Wintershall; H. Kyllingstad, IRIS FI
Objectives/Scope: Current ERD well technology is able to construct well lengths of roughly 12 km with a horizontal departure of approximately 10 km. The paper presents a concept that enables simultaneous drilling and completion with an aim to substantially extend well reach, with an ultimate objective of constructing 30-km long production wells. Longer reach wells can be used to drain remote reserves using existing production facilities as well as provide a means to access reservoirs located beneath environmentally sensitive areas. Methods, Procedures, Process: The key technology elements that enable the concept to construct long reach wells are multiple sliding packer traction units in combination with a dual casing drilling system, comprised of a casing with an inner tubing. The sliding packer traction units provide two main functions; continuous well control along the length of the borehole and traction to overcome axial friction. In addition, the traction packer units provide a stable bottom-hole drilling platform avoiding the occurrence of drilling instabilities such as stick-slip, which can damage conventional BHA’s and the drill bit in particular. The dual casing provides the conduit for drilling fluid circulation to the bit and cuttings transport to surface. The drilling fluid is pumped through the annulus formed between the casing and inner tubing. The drill cuttings are transported to surface through the inner tubing, ensuring efficient cuttings transport with a low pressure loss. Results, Observations, Conclusions: The concept has been developed through a four year project kicked off in 2010. A prototype has been built and tests have shown that each sliding packer traction unit is able to push the drill bit or pull a completion string with a force of 18 tons for the 12-in. hole version. In the paper, elements of the system are described in detail and the results of the full scale yard tests are presented. Novel/Additive Information: The concept represents a new well construction method incorporating advanced completion technology. It enables drilling and completion of long reach wells and can operate in areas with complex pressure regimes such as can occur from pressure depletion due to production or pressurizing as a result of the injection of water or gas. Well control is provided by packers placed in pairs which seal off the annulus over 100-m intervals along the drill string. Production takes place through a large inner diameter. It is a well construction method with no flat time.
IADC/SPE 178812
Drilling from Onshore to Offshore Target Reservoirs: Case Study Demonstrates Value of Diligent Planning and Systematic Execution on an Extended-Reach Drilling Campaign. G. Akinniranye, K&M Technology Group; R. Tikkoo, Origin Energy; B.N. Thearle, Origin Energy Resources; J. French, Origin Energy; S. Amin, Schlumberger; N. Goura, K&M Technology Group
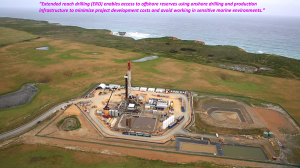
Objectives/Scope: An operator in the Halladale field, offshore Australia, completed its first extended reach drilling project from an onshore location to access offshore targets. The Halladale gas field is located up to 5.5 km offshore and up to 1.8 km below the seabed. The proximity of this and the adjacent Speculant prospect to the coastline enabled the operator to drill wells from onshore using extended reach drilling (ERD) techniques. Methods, Procedures, Process: To mitigate depth uncertainty at the target location, an S-shaped trajectory was selected starting with a shallow kickoff followed by a sub-horizontal section that traveled laterally offshore and ended with a dropoff section to intersect the reservoir target. Advanced drag management techniques were required to install the 9 5/8-in. production casing, 7-in. production liner, and 5 ½-in. intelligent upper completion. The 9 5/8-in. casing was installed using the buoyancy-assisted method (i.e., “floatation”), such that it could be “pushed” and “reamed” in the hole beyond the point of negative weight. As a result of the successes achieved to date, the operator is now exploring drilling longer reach prospects up to 8 km from the onshore drill site. Results, Observations, Conclusions: Technical challenges were overcome and well design solutions and operational practices were developed with the aid of modeling and simulations performed during well planning. The preparation of comprehensive well programs, the use of real-time data to validate the models that were implemented, and the systematic approach to well planning contributed to the success of the project. In addition, a process was adopted to ensure that every member of the team understood the program and was committed to the successful delivery of the wells. These measures resulted in significant project cost savings. The first of the extended reach wells was drilled and completed 16 days ahead of schedule and approximately $7 million below budget. Novel/Additive Information: The 9 5/8-in. casing was run completely empty and required rotation in order to reach TD, however, during the operation of landing-out the casing on the well head, the use of rotation to overcome axial drag was not an option, and adequate contingency planning was required. A casing selective floatation collar was installed to provide additional weight if required by filling the top portion of the string with drilling fluid as TD was approached, but allowing the lower portion of the casing in the high angle interval of the wellbore to remain empty, allowing the drag required to slack the string off and land out the casing to be minimized. This contingency was in addition to the available push-down weight that the top drive could provide, which also formed part of the risk management plan that was in place.
IADC/SPE 178801
Planning, Collaboration and Optimized Drilling Performance for Drilling Extended Reach Wells in the Bakken/Three Forks. N. Nair, P. Bitzan, Halliburton; F. McRobbie, Enerplus Resources (USA)
Objectives/Scope: This paper discusses the methodology involved in evaluating the risks associated with drilling extended-reach wells using conventional drilling tools and adopting a stepped approach towards the drilling optimization of 25,000-ft TD wells, with horizontal legs exceeding 14,000 ft. Extensive planning was carried out over the following areas of the project: well-trajectory design, torque and drag, the fluid program, drilling practices, drillstring design and integrity, hydraulics management, drilling optimization tools, and BHA design. Methods, Procedures, Process: The objective was to drill two extended-reach wells in the Bakken and Three forks formations in North Dakota and to use the lessons learned to drill three additional wells with 50% percent longer laterals. The first two wells of the project were studied to calibrate torque-and-drag models for hole friction, drillstring dynamics with the effects of fluid in-hole drag, effects on ROP with regards to weight transfer while sliding, hydraulic effects of the fluid system, motor output, vibrations analysis, drilling practices through transitions, and parameter optimization while drilling through formation markers through the horizontal leg of the well. Results, Observations, Conclusions: The first two wells were drilled using a drilling-optimization down-hole tool placed above the motor that measures the weight, torque and bending moment across the sub, and the pressure while drilling tool. Tri-axial vibration sensors were used to measure and transmit data in real time to optimize drillsting dynamics and make improvements in the drilling system post run. The improvements in the system and lessons learned were used while three additional extended-reach wells with measured depths over 25,000 ft. Drillstring dynamics from the down-hole sub were studied to identify ways to overcome friction. The data validated the effectiveness of certain friction-breaking tools and proposed areas for improvement in order to orient drill with conventional motors further into the lateral. The limitations with the current system were identified with the first two extended-reach wells. Wellbore-trajectory design and pipe placement were optimized to aid in transferring weight to the bit beyond the 10,000-ft lateral horizontal leg. Alterations in the drilling program were subsequently made to drill further into the lateral based on lessons learned from down-hole optimization tools and surface sensor data. Novel/Additive Information: Three wells were drilled beyond a 25,000-ft total measured depth, with the horizontal leg exceeding 14,500 ft in the lateral. Continuous improvements were made to the system to drill to the limit with conventional motors and to pick up sophisticated rotary steerable tools to drill the last 1,500 ft of the lateral. The approach proved more cost effective to optimize within the constraints of the drilling system before using sophisticated rotary steerable tools.
IADC/SPE 178785
Improved Ecd Prediction And Management In Horizontal And Extended Reach Wells With Eccentric Drillstrings. O. Erge, The University of Tulsa; A. Karimi Vajargah, The University of Texas at Austin; M.E. Ozbayoglu, University of Tulsa; E. van Oort, The University of Texas At Austin
Objectives/Scope: Accurate prediction of Equivalent Circulating Density (ECD) plays a vital role in hydraulic pre-planning and real-time management of drilling operations. Such accuracy is often not available in case of drilling horizontal and extended reach wells, when there is a partially or fully eccentric annulus in a large section of the wellbore. Many hydraulic models, including those widely used in the industry based on e.g. the Narrow Slot approximation, simply ignore the effects of drillpipe eccentricity on annular pressure loss and equivalent circulating density (ECD), thereby generating unreliable estimates for these important quantities. Methods, Procedures, Process: In this study, we discuss the experimental, analytical, and numerical results of a comprehensive investigation into the impact of drillpipe eccentricity on ECD in horizontal and extended reach wells while circulating non-Newtonian drilling fluids. A 91-ft long flow loop with a drillpipe-to-hole/casing ratio of 0.5 (fairly common in conventional drilling applications) was used for the experimental investigation. Drillpipe was placed at the bottom of the hole/casing, thereby simulating a fully eccentric annulus. Four realistic non-Newtonian drilling fluids, which their rheological behavior best described by the Yield Power Law (YPL) model, were used as test fluids. Moreover, a novel numerical model based on a Computational Fluid Dynamics (CFD) approach was developed. Subsequently, the experimental data was compared with both the new proposed model as well as with several other widely used analytical and numerical models previously reported in the literature. Results, Observations, Conclusions: The experimental results confirm – and add to – the historical observations that the annular frictional pressure loss in a fully eccentric annulus is significantly less than the values predicted by the Narrow Slot approach, sometimes by more than 50%. In general, all the evaluated models under-estimated the effect of drillpipe eccentricity on annular frictional pressure loss. However, by comparison, the newly proposed model in this study exhibited by far the least discrepancy with the experimental results. The difference between the estimated and experimental results was found to be proportional to the magnitude of the fluid yield stress and consistency index, and attributed to the complexity associated with simulating YPL fluids. Novel/Additive Information: This study provides valuable insight towards superior hydraulic planning and real-time ECD management in horizontal and extended-reach wells. Its beneficial impact on managing the annular pressure between the fracture and pore pressure in the field to prevent drilling problems such as kicks, mud loss and wellbore instability events is expected to be immediate. Its use will also be key to successful implementation of innovative drilling techniques such as managed pressure drilling and dual gradient drilling, which require highly accurate annular pressure prediction and management.
IADC/SPE 178905
Friction Load Redistribution for Robust and Cost Efficient Design of Extended Reach and Horizontal Well Completions. A.R. McSpadden, R. Trevisan, Altus Well Experts.
Objectives/Scope: In horizontal and extended reach wells where long completions are run into highly deviated or lateral zones, large compression loads arise due to running friction. These loads remain locked into the string when the packer or cement sets. Dissipation of friction during life service due to string vibrations and movements redistributes these friction loads between the wellhead and packer. A numerical approach is presented to correctly calculate the redistributed friction load so that an accurate initial tubing load is implemented in the tubular stress analysis. The proposed methodology offers an opportunity for tubular cost savings by accurate estimation of the stress regime when running friction is locked-in during completion but later dissipates. Methods, Procedures, Process: The numerical approach is a simple 1-D finite element model in which incremental frictional loads are decomposed and redistributed based on relative stiffness of the string uphole and downhole of each local node. Essentially each portion of the string is represented as a series spring system. The methodology requires input of the estimated friction load during running from a standard torque-drag analysis. An analytical solution derived for a simple configuration with a build and hold trajectory is used to validate model accuracy. Results, Observations, Conclusions: The results are particularly relevant for ERD and shale-type multizonal lateral wells, where overestimation of in-service compression above the packer or cement may pose considerable design challenges for tubular components including connections. The common assumption to ignore friction in tubing analysis is non-conservative in that it may underestimate friction loads, especially downhole at the packer. However applying the full slackoff load downhole is also unrealistic and overestimates compression above the packer leading to costly component selection. Results from the numerical model wherein post-dissipation friction loads are redistributed show that only a part of the friction induced compression migrates to the packer. Some of the redistributed friction load results in additional tension at the wellhead. The type of trajectory, kick off depth and deviation angle are important for the load redistribution. Results from a sensitivity study provide some possible guidelines and recommendations. Comparison of the numerical solution with the analytical solution demonstrates that the accuracy of the numerical model depends on the element mesh spacing. Novel/Additive Information: The methodology presented in this work provides an approach for accurate calculation of the amount of friction load transferred to the completion above the packer. The redistributed result which divides the running friction load between hanger tension and downhole compression is not intuitive. This is critical for correct modelling of the initial conditions in the tubing stress analysis with significant impact on tubular cost efficiency and fit-for-purpose design and well integrity.
IADC/SPE 178792
A New Friction Reduction Tool with Axial Oscillation Increases Drilling Performance: Field-Testing with Multiple Vibration Sensors in One Drill String. S. Jones, C. Feddema, Turbo Drill Industries
Objectives/Scope: Weight transfer problems, hanging-up, poor tool face control and diminishing ROP are all problems that are encountered with steerable motors in high angle and horizontal wells. A number of oscillation and/or vibration devices have been introduced to the market over the years to aid these common problems. Both axial oscillation and lateral vibration tools have proven to provide improvements to drilling performance and toolface control. But, as with any device there are always limiting factors, and oscillation and/or vibration devices can cause unwanted vibrations that interfere with MWD systems and even cause component failures. This paper describes the operation and field test results from a new axial oscillation tool. Key component in the string were instrumented to gather critical information on vibration frequency levels throughout the BHA in an effort to optimize system performance. Methods, Procedures, Process: The new oscillation tool uses a mud valve to generate pressure pulses in the string. These pressure pulses are magnified using a specifically designed stroke tool referred to as an intensifier. The mud valve is driven with a short power section from a Positive Displacement Motor (PDM). The lobe configuration of the power section along with nozzle size allows the frequency of the tool to be varied to optimise system performance and reliability. The system was tested with specific MWD systems in a flow loop prior to going downhole to confirm compatibility. The oscillation tool has been designed to be durable over long horizontal runs. A compact, self-contained three-axis inclinometers and three-axis shock sensors (3/4-in. diameter and less than 4-in. length) have been deployed during field testing to capture downhole dynamics. These sensors were strategically positioned in the BHA to gain understanding of vibration propagation distance/pattern and vibration frequency changes over the course of the run. Results, Observations, Conclusions: The data received from the downhole instrumented oscillation tool provided valuable information on drilling dynamics over the course of the field test runs. This data will be discussed and correlated to improvements made during the course of the field test. Strategically deployed vibration recording sensors in the BHA revealed the characteristics of the axial excitation generated from the oscillation tool. This data was used to optimize BHA and tool placement to maximize drag reduction. The new oscillation tool has proven to provide the performance improvements and economics required to compete in this expanding market to aid slide drilling. Novel/Additive Information: Downhole instrumented sensors were used to confirm the value of the axial oscillation mechanism. The use of multiple compact downhole dynamics recording devices has provided new insights in challenging steerable motor drilling applications, assisted with a friction reduction tool.
Deepwater and Subsea
IADC/SPE 178820
Subsea Driving of Conductors: a Cost Effective and Successful Alternative to Pre-drilling on Moho Nord TLP Development. G. Navez, Total E&P Congo
Objectives/Scope: The proposed paper will address the subsea driving of 27 conductors in 800 m water depth offshore Congo, in preparation of the drilling operations from the Moho Nord Tension Leg Wellhead Platform (TLWP). The objectives of the paper are to present part of the experience gained on this project, in particular the reasons for selecting this alternative to pre-drilling of the Conductors in deepwater and some of the main planning, engineering and operational challenges encountered, so as to help preparing and delivering future similar projects in due time, on cost, and without jeopardizing the subsequent drilling operations. Methods, Procedures, Process: The methodology will be that of a case study, described from the perspective of the operator’s drilling entity and in a mostly chronological fashion, from the selection of the installation method to the operations. The main challenges encountered during the project and the solutions found will be addressed, including but not limited to a decision-making process based on technical-commercial data and an engineering process combining geotechnical and mechanical (FEA) analyses. Results, Observations, Conclusions: The selection of this installation method is primarily linked to the significant direct cost savings it allowed in a situation where planning (rig & installation vessel availabilities) and the development specificities (semi-tender assisted drilling from TLP with asymmetric surface/subsea patterns) made the jetting alternative not applicable and the pre-drilling unappealing while synergies with other project entities put the driving method forward. The novelty of using this method for subsea wells led to specificities in the conductor design and engineering, including tubular geometry, connections (pipe-to-pipe welds) and conductor housing, mainly due to the fatigue accumulated during the driving operation but also following specific geometrical and mechanical requirements linked to the installation equipment and procedures (vent holes, driving shoe, shims, etc.) Interfacing among drillers, equipment providers and offshore installation professionals, each with their technical knowledge, constraints and limitations, led to re-engineering of existing equipment (conductor housing) and the design of adapted lifting/handling tools. The actual driving campaign took place as planned and with success in Q4 2014. The actual drilling operations on the Moho Nord TLWP are planned to start in Q1 2016. Novel/Additive Information: Whereas conductor or pile driving has been used extensively in other applications and/or industries (shallow water drilling, offshore construction, etc.), its use in deepwater drilling operations with subsea hydraulic hammers and wellhead systems is recent and the published knowledge accordingly scarce. This paper will add to the body of knowledge by providing offshore development project managers & engineers with first-hand information about this alternative to jetting conductors, its potential benefits, and key engineering and operational challenges to be considered to make it a success.
IADC/SPE 178827
Reduce P&A Cost with Section Milling Technology. T. Ghegadmal, A.D. Ponder, Baker Hughes
Objectives/Scope: Section milling technology is over 50-years-old. Before sophisticated sidetracking systems were invented, a section mill was commonly used to mill away a 75 to 100 ft section of casing to set a ramp for the drilling assembly to sidetrack into the formation. For stabilized milling, section mills were sized close to inside diameter of the casing to be milled, and knives were extended far enough to mill a single casing string. Methods, Procedures, Process: There are times when milling a section of casing must be accomplished below a restriction. In these applications, multiple stabilizing arms are extended along the mill to centralize it inside the casing. Then, cutting knives are extended to cut through the casing wall and mill down, removing the unwanted casing section. Stabilizer arms keep the mill firmly centralized inside the casing being milled. Results, Observations, Conclusions: Recently, such a section milling system was used to plug and abandon (P&A) subsea wells, which required removal of multiple casing strings. The P&A cost of several of these wells in the Gulf of Mexico (GoM) was substantially reduced by using this new section milling system for removing casing which had an inside diameter larger than that of the production riser. The results were substantial, with three days saved on one well, saving the operator approximately $1 million. This was accomplished by leaving the riser, blowout preventer (BOP), and swarf handling equipment in place. Novel/Additive Information: This new section milling system has significant advantages over the conventional system. A full 90˚ extension of knives and stabilizer arms provides greater reach for reliable milling of an intermediate or outer casing string, after conveying the mill through the innermost casing string. A unique method of extending and retracting the milling knives and stabilizer arms provides reliable operation. State-of-the-art tungsten carbide cutting inserts improve milling performance significantly. The knife’s greater reach gives unobstructed access to the mill and eliminates individual runs ordinarily required for removal of multiple casing strings, production riser, BOP stack and other surface equipment, substantially reducing costs and HSE risks. Case histories of offshore applications of this new technology will be presented.
IADC/SPE 178856
A new Method for Determination of Stress and Fatigue in Risers and Wellheads. H. Horn, Ferrx as; A. Saasen, Det Norske Oljeselskap ASA; A. Skogvang, Lundin Norway AS
Objectives/Scope: The scope of the paper will be to present a new and patented non destructive technique for measuring deterioration and cracks in steel structures. Results from stress and fatigue tests with different full scale structures will be presented and related to real applications with respect to life time prediction. Methods, Procedures, Process: The method monitors stress and deterioration in ferromagnetic steel. The material properties magnetic permeability and electrical conductivity and changes in these are determined by analyzing the measured voltage response to injected current pulses. The response is transient voltage drop signals, measured under various conditions, and are the basis for calculating the parameters representing the stress, fatigue and crack nucleation and crack development in the materials. Degree of material degradation can be used to characterize used degree of operational lifetime. Results, Observations, Conclusions: The method has been tested and verified for different types of stress and fatigue in different steel alloys. High sensitivity to elastic stress and early detection of permanent changes for high-cycle fatigue testing have been demonstrated e.g. with fatigue tests of work over riser pipes. High sensitivity to remanent stress, i.e. the steel’s ability to “remember” stress (elastic) is a feature that is proportional to maximum stress since last measurement. This is valuable information when monitoring e.g. steel risers. On risers it can be installed on selected location to give the actual condition in the steel for the most exposed locations and use this information to calibrate the mathematical models used to estimate the condition of the whole riser and by this reduce estimated uncertainty. The technology’s ability to monitor the actual stress and fatigue development in wellhead casing pipe has been described. Novel/Additive Information: A new method is presented which will significantly reduce uncertainty related to the condition of monitored subsea structures. This method provides for directly measurement of actual material deterioration which can lead to fatigue in e.g. steel risers or wellhead pipes, and can predict any crack initiation or fatigue development.
IADC/SPE 178907
A Reliability-Based Approach for Survival Design in Deepwater and High Pressure/High Temperature Wells. P.V. Suryanarayana, D.B. Lewis, Blade Energy Partners
Objectives/Scope: We present a reliability-based approach to demonstrate well integrity under survival load scenarios, which are increasingly driving well design in critical deepwater and HPHT wells. It is shown that the current practice of using standard working stress design for survival scenarios, even with design factors approaching unity, fails to quantify risk of failure, and can lead to design practices and outcomes that are not risk consistent or optimal. A probabilistic, limit-state based approach is therefore necessary to adequately demonstrate integrity and risk under survival scenarios. Methods, Procedures, Process: The paper describes Reliability based design (RBD) and its use in other structural design codes, and shows how it can be used for survival design in critical wells. A distinction is made between operating (service) loads and survival loads. Particular attention is given to Worst Case Discharge and Well Containment loads, which have become design-dictating survival loads in many deepwater well designs. A probabilistic approach in which a deterministic load at its extreme survival magnitude is compared to stochastic strength (from data on strength parameters) is presented to address survival design. Regardless of how low the probability of occurrence of the load is at its survival magnitude, well integrity is demonstrated assuming such a load occurs. The method can be easily implemented by constructing resistance distributions using limit state equations such as the Klever-Stewart Rupture Limit, and the Klever-Tamano Collapse Limit equations, with strength parameter data from API TR 5C3 (ISO TR 10400), manufacturer reports or direct measurement. Statistical approaches to constructing such distributions are presented. Results, Observations, Conclusions: The goal in survival design is to demonstrate survival rather than continued operability. The probability that the deterministic survival load exceeds the stochastic resistance is used as the basis for demonstration of survival. Based on this, acceptable probabilities of failure for typical survival loads are recommended, and contextualized to other design codes. The applicability of this approach to connection selection and brittle failure is also demonstrated. Deepwater and HPHT well examples are presented to illustrate the use of the approach. It is shown that designing to an acceptable probability of failure leads to more robust and risk-consistent designs in critical wells. Further, such an approach allows designers to focus on the specific design or well construction changes that enhance survival. Novel/Additive Information: The approach described in this paper provides a quantitative basis to examine design adequacy of wells under survival scenarios, particularly worst-case discharge and well containment loads. Using stochastic strength data rather than deterministic strength estimates provides a probabilistic basis for design, thus quantifying risk, and allowing more informed decision making. The authors believe this is a much needed, rational approach to optimize design of critical wells under increasingly demanding loads.
IADC/SPE 178835
Differentiate Drilling Fluid Thermal Expansion, Wellbore Ballooning and Real Kick during Flow Check with an Innovative Combination of Transient Simulation and Pumps Off Annular Pressure While Drilling. Z. Yuan, Schlumberger; D.R. Morrell, Schlumberger Information Solutions; A. Garcia-mayans, Schlumberger D&M
Objectives/Scope: To achieve a high level of drilling efficiency, it is paramount to correctly identity reasons of drilling events from available data in a timely fashion. Many surface or downhole events share common root causes. Drilling fluid thermal expansion, wellbore ballooning and formation kick share similarities in terms of surface observation such as pit gain volumes. However, resolution for each of them is completed in a totally different manner. Treating a wellbore ballooning effect in the same way as a kick will likely result in losing the current borehole after days or weeks of unsuccessful operations. Methods, Procedures, Process: In this study, pressure while drilling technologies and software simulations are discussed to analyze variances in the wellbore parameters over time to investigate drilling fluid thermal expansion, wellbore ballooning and formation influx during flow checks in riserless drilling operations. A transient simulation software was used to study the fraction of gas in the annulus and fluid level inside the drillstring on several flow checks following flow and gas bubbles at the well head. Availability of continuous pumps off annular pressure while drilling measurement helps calibrate the simulations and verify its validity. Results, Observations, Conclusions: A new workflow combining modelling, simulations and downhole annular pressure profiling measurement was successfully applied to a riserless pilot hole deep water well Gulf of Mexico. The flow contribution from each drilling fluid thermal expansion, wellbore ballooning, formation influx and u-tube flow was identified and decomposed. Novel/Additive Information: Transient flow simulator working together with pressure while drilling data gave the operator an exact knowledge of wellbore dynamics in an operation usually performed with limited information. This proved extremely valuable in the pursuit of drilling prospect.
Tubulars
IADC/SPE 178858
A New Sour Service 125 ksi SMYS Drillpipe with Sour Service 120 ksi SMYS Tool Joints For Use in Sour Gas Drilling or Non-Sour Offshore Intervention Riser Applications Requiring Higher Load Capacities. A. Uttecht, National Oilwell Varco; M.J. Jellison, L. Hehn, NOV Grant Prideco; L.W. Sanclemente, M. Delahoussaye, Workstrings International
Objectives/Scope: The term “sour” is used to refer to drilling environments containing hydrogen sulfide (H2S). In sour wells, H2S causes sulfide stress cracking (SSC) in carbon low-alloy steels under tensile stress. A form of hydrogen embrittlement, SSC causes sudden, brittle fracture in drillpipe. To combat the effects of H2S exposure, sour service drillpipe has been manufactured to meet IRP Volume 1 – Critical Sour Drilling specifications. IRP requires SS75 ksi, SS95 ksi, or SS105 ksi specified minimum yield strength (SMYS) tubes with all three grades using 110-ksi SMYS tool joints for use in sour operations. However, these lower yield strength IRP grades have limited load capacity which restricts drilling parameters such as total depth (TD) and margin of overpull. Methods, Procedures, Process: Using advanced steel heat treatment methods, a 125-ksi SMYS grade sour service drillpipe has been developed. The 125-ksi tube is mechanically incompatible with the standard 110-ksi IRP sour service grade tool joint because of the large difference in yield strength between the two components. Therefore, a new class of sour service tool joint with an SMYS of 120-ksi was required for the 125-ksi sour service tube. This new higher yield strength tool joint needs to meet the same level of SSC-resistance as the 110-ksi IRP tool joint, i.e., pass testing in solution A method A of NACE TM0177 (100% H2S at pH = 2.7, 720-hr test) at a testing stress of 65% of SMYS. Like the high yield strength 125-ksi tube, advanced heat treatment methods were required to achieve SSC-resistance in the higher yield strength tool joint. Results, Observations, Conclusions: A second application for the 125-ksi drillpipe is as an offshore drillpipe-based intervention riser for non-sour wells. Currently, 105-ksi drill pipe grades are often used but increased demands on load capacity (up to 1,000 kips) makes the 125-ksi drillpipe an attractive alternative. The 125-ksi drillpipe also meets recommended hardness limitations placed on offshore risers in specification API RP 17G (Recommended Practice for Completion/Workover Risers). Novel/Additive Information: This paper introduces an SSC-resistant 125-ksi drillpipe with SSC-resistant 120-ksi tool joints and presents the results of NACE TM0177 testing of this new technology. The new 125-ksi drillpipe will allow for increased load capacity over IRP SS105 ksi grade drillpipe in drilling environments with moderate to low concentrations of H2S. In addition, it can serve as an improved substitute over 105-ksi drillpipe-based offshore intervention risers due to its increased load capacity and controlled hardness.
IADC/SPE 178823
Increasing Long-Term Fatigue Performance of an API Box Boreback Using an Enhanced Non-Truncated Thread Design and Revised Machining Methodology. G. Hauze, S.R. Gokhale, T H Hill Associates
Objectives/Scope: Stress Relief Features (SRF) are commonly added to a Rotary Shouldered Connection (RSC) to increase the fatigue performance of the connection. An SRF aims to lower critical stress at the last engaged thread and improve fatigue performance. The most common SRF found on API box connections is the API Box Boreback. Methods, Procedures, Process: The API Box Boreback SRF is added to an API RSC by boring out both box threads and ID to a specified cylinder diameter and depth from the box shoulder. The API boreback is then finished by profile turning a tapered transition of specified angles and lengths which connects the back of the boreback cylinder to the ID of the component. The traditional method of boring the cylinder diameter due to the tapered threads of API connections causes a removal of thread crests at the back of the box. These truncations of the last engaged threads reduce the contact area of the thread flanks available to support the load. The repercussions of this include an increase in stress concentration, reducing fatigue life, and an escalation in susceptibility to thread wear, which inevitably amplifies the effect of the thread truncation, further reducing the fatigue life and cancelling out the benefits of the SRF. Details of this phenomenon can be found in IADC/SPE128931 (Gerdes&Lee 2010). Results, Observations, Conclusions: Despite its popularity, the API Box Boreback SRF can lose its effectiveness as the thread truncation at the back of the box can accelerate crack initiation and cause premature failures. To remedy this, an experimental study was undertaken to develop a machining method to cut a boreback with an enhanced non-truncated geometry on API box connections. The modified boreback geometry and machining methodology were perfected over multiple iterations, prototyped with a Computer Numerical Controlled (CNC) lathe using various routines and tooling selections. The dimensions were verified to conform to the requirements outlined in API Specification 7-2 and the machining process was validated on multiple API box connection types. Novel/Additive Information: This paper presents details of a modified design and a universal machining methodology developed to cut an API compliant Box Boreback which retains full-height threads at the back of the box, avoiding thread truncation, and preserving the increased fatigue performance a Box Boreback provides well into the life of the connection. The method meets all dimensional requirements outlined in API Specification 7-2, ensuring proper makeup. The machining process can be performed on either a CNC or manual lathe. The enhanced boreback design provides a drastic improvement in fatigue performance over the standard API Box Boreback design, while maintaining all other structural and dimensional design aspects, and without altering Makeup Torque (MUT) or Bending Strength Ratio (BSR) of the connection.
IADC/SPE 178833
Casing Wear: Is it an Enigma or a Conundrum? R. Samuel, Halliburton
Objectives/Scope: This paper examines the current state of casing-wear modeling and simulation and identifies the complexity involved. As more and more complex wells are drilled, an important problem to be addressed is related to casing wear, more specifically, the casing exposed to production. Casing wear is one of the continuing challenges faced by the industry, and an accurate estimation of downhole wear remains a paradox. Methods, Procedures, Process: Presently, there are no guidelines available in the industry, as the severity is felt after long-term production. Short-term effects of improper estimation of casing may not be felt owing to the overdesign of the casings by largely applying excessive safety factors. Various casing-wear estimation techniques have been proposed; however, the accuracy of the models developed is questionable, and companies rely on the outdated model and wear factors. The paper proposes new model and guidelines by integrating the model and wear factor estimation. Results, Observations, Conclusions: This paper aims to bridge this existing knowledge gap and provides a comprehensive treatise on casing wear and, more in general, tubular wear estimations and their underlying model parameters. The paper describes the details and the new calculation methodology of position wear around the casing using the stiff-string method. The wear factors are inherently tied to the friction factor in the modeling process. This paper investigates in detail the dependency of the casing-wear factors on these uncertainties through several example calculations and presents an extensive analysis on the results obtained. It provides a simple set of guidelines to help understand the fundamental concepts for better downhole-wear estimation. An accurate prediction of casing wear is essential to enhance well integrity and further the life of the well. Hence, the paper presents specific examples for casing-integrity analyses and provides recommendations to improve the overall well integrity. Novel/Additive Information: This paper provides a sound engineering basis for future drilling engineers to effectively understand the challenges involved in estimating and quantifying casing wear. The methodology presented in this paper is validated with a scalable mathematical model. The paper provides in-depth understanding of the casing-wear position based on contact points using the stiff-string model. The coupled engineering model provides a basis for well-integrity analysis.
IADC/SPE 178806
Collapse Strength of Casing Subjected to Combined Loads. J.F. Greenip, Viking Engineering
Objectives/Scope: Triaxial evaluation of loads is used extensively for casing and tubing string design and analysis. The paper, proposed for the Tubulars – Production Tubulars technical category, presents a more accurate method of determining the collapse strength of casing and tubing subjected to simultaneous axial and internal pressure loads. It will be shown that casing and tubing subjected to combined loads have higher collapse design factors than current calculation methods predict. Methods, Procedures, Process: A triaxially based formula is presented that simultaneously incorporates internal pressure and axial load into the calculation of casing and tubing collapse strength. The formula is compared to the existing First Edition API TR 5C3 uniaxial method of accounting for internal pressure. The paper compares both the existing uniaxial method and the new triaxial method with API combined load collapse test data, further validating the triaxially based formula. Casing design examples contrast the existing method with the triaxially based method, showing the higher collapse design factors calculated when using the more accurate triaxially based formula. Results, Observations, Conclusions: The First Edition API TR 5C3 formula for calculating the effect of internal pressure on collapse fails to account for the contribution of instability to collapse of higher diameter-to-thickness ratio pipe. In addition, the current effect of internal pressure on collapse formula inaccurately assumes uniform stress across the wall and the formula is inconsistent with moderate and thick-wall stress theory. The paper augments existing First Edition API TR 5C3 formulas for calculating collapse strength in the presence of internal pressure plus axial loads. The triaxially based method generates higher collapse design factors when internal pressure is present. Novel/Additive Information: Common existing graphical methods of triaxial analysis for OCTG do not permit incorporating internal and external pressure simultaneously. The paper provides improved depiction of the triaxial stress state and reflects the impact of combined loads encountered in oil and gas well applications. OCTG string design is improved using the method presented.
IADC/SPE 178791
Casing Integrity: Modeling Strength Degradation. C. Li, University of Houston; R. Samuel, Halliburton
Objectives/Scope: Casing integrity management is of critical importance especially in wells experiencing severe casing wall degradation. It is highly desirable to predict the threshold pressure for degraded casing burst and collapse strength, and design the casing strings considering these wear effects. Knowledge of stress distribution in worn casing helps predict where casing failure occurs first. This study focuses on building a model for stress distribution along casing circumference based on “crescent shape” casing wear. Methods, Procedures, Process: A common method is to estimate the reduction of the casing burst strength in worn casing using API burst strength equation with a linear reduction by the remaining wall thickness or wear percentage equivalent to a “uniform-worn” casing model. However, this approach can be too conservative, resulting in higher costs because of overdesign of the casings. This paper presents a rigorous engineering method to calculate the hoop strength directly, including the local bending in the thinner portion of the “crescent-worn” casing. Results, Observations, Conclusions: A model and correlation to calculate varying hoop strength in the crescent worn shape and non-worn casing have been developed with force and moment balance equations. This paper further delves and builds equations for stress distribution at every section along the circumference in the near critical scenario. The study finds the calculation of strength using the linear wear model to be overly conservative because it only focuses on the stress at the thinnest portion of the worn casing. The study based on the variable worn cross section provides stress distribution at every section along the circumference in the near critical scenario. The hoop strength varies with the angle of the cross section showing that hoop strength increases with the casing wear. It is also observed the hoop strength almost remains constant in the non-wear part of the casing. In addition, hoop strength decreases with the increasing of the half angle of the casing wear part. Novel/Additive Information: The stress predicted in this paper is similar to results obtained from the finite element method (FEM), which validates equations and results obtained from this paper. Simple guidelines presented along with several example calculations using von Mises failure criteria help illustrate the improved tubular modelling aspects. The developed model is generic and can be used for casings, risers, and tubings.
IADC/SPE 178861
Buckling of Tubular Strings in Open Sea. A. Kyllingstad, National Oilwell Varco
Objectives/Scope: An analytical model for steady state lateral buckling of tubular strings is presented. It applies both for drill strings during riser less drilling of top holes and for marine risers. The model represents a tool for predicting critical compression force at the lower end and also critical shortening length of the buckled string in situations when the top site heave compensation or tensioner system fails. Methods, Procedures, Process: The static lateral deflection of the string is described by a fourth order differential equation that can be linearized for small inclinations. Non-trivial analytic solutions include homogeneous and inhomogeneous Airy functions that can be combined to satisfy various boundary conditions and shortening lengths. The effect of a side force is also included in the solutions. The paper discusses the validity of the underlying assumptions, such as linearity, simplified boundary conditions, and the neglecting of dynamic effects. Finally, the theory is also compared with experimental results from a small scale physical model. Results, Observations, Conclusions: Analytically derived formulas are valuable because they provide physical insight of the buckling phenomenon. They can explicitly tell how the buckling load varies with various string properties, such as diameters and length. As an example, the presented theory predicts that both deflection and stress increase proportionally to the square root of the shortening length. Another formula shows that maximum stress is nearly independent of the string length. This is at least true when the length exceeds a few characteristic buckling heights, defined as the cube root of the ratio of bending stiffness divided by the effective buoyant weight per unit length. An important result from the analysis is that a drill string will survive rather large accidental shortening lengths without being plastically deformed. The analytic solutions are successfully compared with the deflection of a small scale physical model having a characteristic buckling height scale of 1:185 as compared with 6 5/8-in drill pipes. The good fit between theory and experiments strongly support the validity of the analytic solutions. Novel/Additive Information: The presented theory provides simple formulas that can be used by engineers to predict critical compression force and critical shortening of tubular strings, such as drill strings and risers in open sea. It can also serve as static benchmark solutions to more advanced numerical and dynamic models.
IADC/SPE 178777
Landing String: Breaking the 2.5 Million Pound Limit. G. Plessis, NOV Grant Prideco; R. Verhoef, S. Ringstad, A. Pangilinan, NOV
Objectives/Scope: With operating companies moving into deeper prospects, it is becoming increasingly more challenging to land heavy casing strings. Solutions are referenced in published papers focused on the optimization of specific aspects of the overall operation. To date, these solutions are used for casing landing operations running up to 2.5 million pounds (1,250 sTon), which is the hoisting capacity of most offshore mobile drilling units. A trend has been established in the oil and gas industry where more frequent requests are being made for landing strings of higher tensile capacity, with ratings of 2.75 or even 3.0 million pounds. Reaching this level of tension in a string is demanding in terms of its own design but also presents additional challenges when it comes to hoisting it on the rig, sitting it on slips, torquing it, and being able to shear it with the BOP if quick disconnect is necessary. This paper focuses on that challenge. Methods, Procedures, Process: This paper addresses the impact of design choices and shows the best options the industry can use at every landing string interface. Often, the system components are selected in isolation bringing partial answers to this industry’s challenge; the true answer goes beyond this and is an integrated solution. The impact that design choices have on capacity are discussed and an integrated solution was developed that focuses on every landing string interface. Results, Observations, Conclusions: This paper presents an array of technologies that allow operating companies to safely run casing string weights greater than what is run today and can serve as guidelines for drilling engineers as they plan deeper prospects. Novel/Additive Information: The challenge is to understand the interactions of these technologies to create a balanced system that leads to safer landing operations.
Directional Drilling
IADC/SPE 178831
Effect of Transient Surge Pressure on Stress Distribution around Directional Wellbores. Z. Zamanipour, S.Z. Miska, University of Tulsa; P.R. Hariharan, Shell
Objectives/Scope: Fluid displacement due to pipe movement into/out of the wellbore generates surge/swab pressure. Surge/swab pressure could result in formation fracturing, lost circulation, kicks, and even blowouts. Transient surge pressure depends on tripping velocity, mud viscosity, fluid compressibility, wellbore expansion, and elasticity of the drillpipe. Considering wellbore stability, sudden pressurization of the wellbore due to surge pressure causes rapid change in stress distribution in the zone near the wellbore that may result in wellbore instability. Therefore, it is necessary to have an estimation of transient surge pressure and stresses for safe and effective tripping operations. Methods, Procedures, Process: In this work, for the first time, stress distribution and the stability around the wellbore are being investigated when transient surge pressure is generated in the wellbore. Firstly, a transient surge pressure model is developed to calculate the pressure along the wellbore during the tripping-in operation. The model is based on transient wave propagation due to fluid compressibility and wellbore expansion. Then, the following steps are taken to obtain stresses around the wellbore: 1- Stress distribution around directional wellbore is calculated based on poroelasticity concept. 2- Induced pressure and stresses due to constant borehole pressure change are calculated. 3- Induced pressure due to transient surge pressure is calculated using Duhamel’s theorem. 4- Induced stresses are calculated and added to existing stresses around the wellbore using superposition principle. Results, Observations, Conclusions: The model is implemented for tripping into a directional wellbore with a trapezoidal velocity profile. The induced pressure, radial and hoop stresses versus radius are calculated at different times. Results show that induced pressure vanishes almost completely at a distance of about six times the wellbore radius. Induced pressure increases with time until it reaches its maximum which is the maximum of surge pressure and then dissipates with time. Induced pressure peak propagates into the wellbore and dissipates with time. Induced radial stress shows the same trend as induced pressure. However, its peak is always at the wellbore wall. Induced hoop stress is tensile with a maximum value of about 30% of induced pressure before it decays and dissipates. Total radial stress peaks about 30% compared to base value. However, same comparison for total tangential stress shows 9% decrease due to induced tensile stress. A failure criterion can be applied to analyze the stability of the wellbore. It is noted that the time rate of surge pressure change and dynamic rock strength must be taken into account in wellbore strength management. Novel/Additive Information: The developed model presents an effective tool for wellbore stability analysis in tripping operations. A few example simulation cases are discussed. The tool can be applied for optimization of tripping operations in vertical and directional wellbores.
IADC/SPE 178825
Changing Drillstring Design to Allow Accurate Calculation of BHA Sag Corrections. S. Hinke, K. Kanji, Halliburton; B. Mracek, C. Slight, R. Happy, L. Zabcic, Brion Energy; R. Diver, Formerly of Halliburton
Objectives/Scope: The SAGD and CSS drilling environment in Northern Alberta has some of the tightest geological control in the world. In many cases there are multiple stratigraphic wells over the length of the vertical section of the horizontal legs. This geological control positioning allows wells to be more accurately proved than survey measurements alone. Through lab and shop testing in a controlled environment, and field validation trials it’s been discovered that the modelling of flex collars in a BHA with wear bands on LWD tools can cause significant deflection across flex collars resulting in sag on the directional sensor measurements and a misrepresentation of the borehole. Methods, Procedures, Process: Changes in the BHA design can significantly reduce the deflection of BHA components, otherwise known as BHA sag. These changes can allow sag modeling of the BHA where previous BHA’s could not be modelled, in particular, existing sag models do not account for the effect of wear bands or external upsets when modeled with flex collars. This compounding survey error, as a result of sag was not previously apparent with modelling software. Results, Observations, Conclusions: Testing and data analysis was performed comparing different combinations of BHA’s in multiple hole and tool size and with multiple survey probes to determine survey accuracy when using flex collars compared to stiffer slick collars with a constant diameter. Through empirical testing it was discovered that flex collars deflect in a manner which BHA modelling is unable to predict when wear bands or other external upsets are present. Other external upsets can include stabilizers, worn BHA components, cross-over subs and when stepping down tool sizes. Modeling the flexure across the length of a flex collar with varying diameters we were able to confirm results that had significant inaccuracy. This prevented predicting deflection of the BHA in the vicinity of survey instruments. Using collars with a constant diameter circumvents this issue. Eliminating variations in diameter across the length of a component allows the modeling software to predict the deflection providing accurate and correctable results. Novel/Additive Information: The results of this study is to provide to the industry a new best practice going forward for the design of bottom hole assemblies. A tool carrier with a constant diameter enables the current software available on the market the ability to accurately model and predict the sag correction.
IADC/SPE 178811
World Record Using the Steerable Drilling Liner Technology to Secure Previously Non Drillable Section in Unstable Shale. V. Bossis, J. Fjorden, G. Grindhaug, M. Eidem, J. Ringstad, Statoil ASA
Objectives/Scope: Challenging environments such as unstable clay formation represent high operational risk when running tubular after drilling is completed. Use of Steerable Drilling Liner (SDL) system combines drilling and casing of the hole, thereby mitigating the risk of not being able to run the liner due to time dependent formation collapse. This case study presents the difficulties encountered with a Semi-Submersible rig on the Åsgard / Midgard field in the North Sea during 7-in. liner running operations in unstable clay formation using the conventional approach (drilling 8 ½-in. section first and then running the 7-in. liner), the planning of a SDL operation, and the execution of the SDL operation as well as results compared to similar operations. Methods, Procedures, Process: The components of the SDL system will be reviewed and explained. Detailed planning is crucial for a successful SDL operation. The simulation work will be described with focus on ECD management and hole cleaning strategy. Torque and drag will also be covered. Actual drilling parameters will then be compared with the simulations. Results, Observations, Conclusions: Two attempts were made to complete the section using conventional technology. It was decided to plan and execute a sidetrack operation with the SDL system after numerous unsuccessful attempts to run the 7-in. liner. Drilling operation with SDL was carried out as planned. No major drag was found over the whipstock despite the high local dogleg. Very smooth drilling operation with steady drilling parameters was experienced and the rate of penetration was comparable to drilling the section conventionally. ECD was slightly lower than simulated but around 2 points higher than with conventional drilling. Good hole cleaning was achieved despite a challenging well geometry and the liner was left in hole after drilling was completed. The liner was then cemented and the liner hanger set and tested. The SDL system allowed drilling more than 1000 m of the 8 ½-in. section, making this operation a new world record and turning the well from an economic disaster to a complete success. Novel/Additive Information: The SDL system is a relative new technology under continuous improvement. The primary application of this system is its use in unstable formation where it is anticipated problems for running the liner conventionally. Indeed, shocks and drilling energy transmitted to the formation is greatly reduced with this system, preventing time dependent phenomena such as hole collapse.
IADC/SPE 178867
Utilizing Short Bit to Bend Motor Technology Allows Monobore Wells to be Drilled in the Niobrara Unconventional Shale Play with a Single Drilling Assembly. N. Augustine, Baker Hughes; B. Jerde, Baker Hughes Solutions; C.R. Fleischhacker, Baker Hughes; B. Peterson, Anadarko Petroleum
Objectives/Scope: The demand for reduced AFE’s for horizontal wells drilled in the Niobrara unconventional shale play has increased the need for improved drilling efficiencies. Better efficiencies can be achieved by utilizing monobore well designs which maintain a single diameter hole size for the vertical, curve, and lateral sections, eliminating the need for an intermediate casing string and the subsequent need to change out drilling assemblies for a reduced hole size. Positive displacement motors (PDM) with short bit to bend technology (SBTB) allow the well to be completed with a single conventional drilling assembly. Methods, Procedures, Process: In order to drill monobore wells in a single run, the following solutions were implemented: • A positive displacement motor with SBTB and reduced bend angle to achieve planned build up rates and prevent component damage. • Optimal motor output torque and speed for desired rate of penetration (ROP) and bit life. • Drillstring and bottom-hole assembly designed for improved drilling mechanics. • Optimized drilling fluid program to maintain wellbore stability in challenging formations. Results, Observations, Conclusions: This paper will compare the monobore well design to the original well design utilizing multiple hole sizes by studying build-up rates (BUR), days on well, ROP, and time spent tripping. The dataset used for this study is composed of six single conventional assembly monobore wells and six representative multiple hole size wells. A consistent drilling efficiency improvement became apparent in the comparison. Novel/Additive Information: This paper will review in detail how short bit to bend motor technology allowed an innovative answer to drilling the Niobrara unconventional shale play with a single conventional assembly.
IADC/SPE 178798
Implementation of Wired Drillpipe saved Multiple Days per Well, by addressing Performance Limiters, increasing Drilling Efficiency. R. Teelken, National Oilwell Varco; C. Jaring, NOV IntelliServ; A.D. Craig, NOV Downhole Tools & Pumping; R.M. Allan, E.ON E&P; N.H. Roberts, E.ON Ruhrgas UK Expl & Prod; A.J. Hatch, EON Exploration & Production
Objectives/Scope: This paper will discuss the implementation of the Wired Drillpipe telemetry on two wells of the Babbage development project in the Central North Sea and will present the quantified efficiency gains achieved across various drilling operations. Methods, Procedures, Process: Wired Drillpipe (WDP) telemetry enables bi-directional, high speed data transmission to and from downhole tools at speeds up to 57,600 bps (Olberg et al. 2008). This enables real-time “recorded” quality MWD and LWD data to be transmitted instantaneously to surface, as well as near-instantaneous commands (“downlinks”) to be sent to MWD, LWD and RSS tools while drilling. Results, Observations, Conclusions: The contribution of WDP telemetry to well placement and Geosteering on the Babbage development project has been published previously (Hatch, et al. 2011). This paper however, will present the efficiency gains and corresponding time savings that WDP telemetry enabled through the instantaneous transmission of data up and down the drillstring. A detailed analysis of the two WDP wells drilled with WDP telemetry will show the quantified time savings when compared to three wells drilled with conventional mud pulse telemetry. The analysis will compare the time spent on several activities including the transmission of downhole data to surface and vice-versa, the frequency of unplanned bit or BHA trips and on-bottom drilling time. The analysis will account for the differences in BHA designs, well paths and controlled drilling practices. Novel/Additive Information: Compared to the Babbage wells, drilled with mud pulse telemetry, a reduction of multiple days per well can be inferred through the increased efficiency of these operations and activities.
IADC/SPE 178873
Remote Directional Drilling and Logging While Drilling Operations in the Arctic. C. Chatar, A. Stepnov, A. Mardyashov, C. Ke, E. Elizondo, Schlumberger
Objectives/Scope: Few locations present as many challenges as drilling in Arctic. How do you drill in the most hostile environments in the world? How do you handle the most remote locations, the toughest logistics and the biggest gap in infrastructure? While the industry has moved progressively over the past decades to meet these challenges, one company’s solution in terms of personnel, cost, safety and the environment was to do the job remotely. Methods, Procedures, Process: We are not only talking about monitoring or support from town offices. We are discussing a fundamental paradigm shift where the directional and MWD crew is not physically located on the rig. In order to accomplish this, there had to be a major transformation. Technologies had to be qualified and workflows had to be modified. Roles and responsibilities were redefined. There was also a major challenge to convince operators to allow the control to come from a source external to the rig. There are many associated risks with such operations. These risks include loss of connectivity, methods for diagnosing tool failure and hardware failure to name a few. Results, Observations, Conclusions: In this paper the authors begin with a brief history of remote operations (RO) indicating major milestones. The challenges of implementation of RO centers are then discussed. Prevention and mitigation of associated risks is also discussed. Given the great success in implementation of a major RO center in the Arctic, the details of methods and technologies used to achieve success is also discussed with specific focus on the Arctic operations. Many of the challenges and methodologies will be supported by details of real world implementation. Novel/Additive Information: Theoretically, wells could be steered and controlled from the comfort of your couch at home; millions of dollars’ worth of technology controlled from thousands of miles away. We have enough data, communication capability and technology to make this a reality. And that was exactly what we did.
Wednesday, 2 March
Rock Breakers
IADC/SPE 178808
Innovative Ability to Change Drilling Responses of a PDC Bit at the Rigsite Using Interchangeable Depth-of-Cut Control Features. K. EVANS, C. Russell, Baker Hughes
Objectives/Scope: Bit designers use the well-established practice of strategically placing depth-of-cut (DOC) control features at strategic heights from the cutter profile to selectively manage drill bit aggressiveness and to maximize drilling performance. But, until now, the elements used for depth-of-cut- control have been a fixed part of the bit. An innovative new feature now enables compact element replacement and/or adjustments at the rigsite using a mechanical locking design. The driller can quickly adjust the bit responsiveness before each run, if wanted, to optimize performance factors such as rate of penetration and tool face control. This paper describes the benefits, ease of use, positive results and reliability of this new technology, with examples from multiple applications for a variety of bit designs. Methods, Procedures, Process: The final design was selected and validated based on a number of evaluation methods including concept screening, simulated laboratory drilling, and field tests. The initial screening tests evaluated the ease of compact installation and removal for various concepts using a small-scale test block. Full bit testing using a full-scale, high-pressure, downhole drilling laboratory evaluated installation, integrity, and aggressiveness response changes based on compact height adjustments. Finally, multiple field tests on wells in North American applications of the Eagle Ford, Marcellus, and DJ Basin formations provided data to refine the mechanical design and improve manufacturing processes to achieve a robust technology. Results, Observations, Conclusions: Field tests proved the new design to be highly reliable, with drilling performance that matched or exceeded the performance of bits with standard brazed compacts in the same fields. This new design provides the unique ability to rapidly optimize bit responses. This paper will describe the technical lessons learned, guidelines for use, and tools developed to maximize the benefit from this innovative new feature. Novel/Additive Information: This new method enables compact element installation and removal within fifteen minutes on the rigsite for the purpose of repair or aggressiveness modification. In contrast, traditional methods of DOC control include long lead times to alter a bit design, manufacturing, and delivery. Drillers are now able to reap the immediate benefits of improved bit performance by changing bit design on the rigsite based on direct feedback of bit aggressiveness and steerability between runs without needing multiple bits on site. Ultimately, this new bit technology provides improved drilling performance and greater efficiency for the operator.
IADC/SPE 178765
Conical Diamond Element Enables PDC Bit to Efficiently Drill Chert Interval at High ROP Replacing Turbine/Impregnated BHA. J. Pahl, Nostrum Oil&Gas; M. Pak, M. Azar, Smith Bits, a Schlumberger Company
Objectives/Scope: Developing reserves in Kazakhstan’s Chinarevskoe field requires the operator to drill an 8 ½-in. vertical borehole through extremely hard carbonates with high concentrations of problematic chert inclusions. The first chert layer is encountered at 3050-3110 m which has 10-50% chert concentration. Penetrating chert with PDC has been challenging and in many cases impossible due to the cutters’ inability to withstand high impact/breakage. A change to impregnated/turbine BHA led to improved run lengths. One impreg could drill 550 m at 3.4 m/hr. Typically it took three bits to reach TD. However, the impreg generated small cuttings and frictional heat altered chip appearance hampering efforts to identify formation lithology/properties. Additionally, the centrifuge was unable to separate the small cuttings from the drilling fluid creating the need for constant mud replacement. Tests with PDC were again attempted but when the bit encountered a chert interval, the cutters were damaged and pulled in poor dull condition (7-6-CR). Drilling with PDC also required correction runs with impreg/turbine. The team conceded the chert could not be drilled with PDC/motor BHA. Methods, Procedures, Process: An R&D initiative was launched that yielded a conical shaped polycrystalline diamond element (CDE) and a new style bit was conceptualized by positioning multiple CDEs behind the main PDC cutting structure from bit center to gauge. The CDE configuration would protect/support the main cutters from impact damage. The concept was validated using an FEA-based model system and a new full CDE on profile bit (CoB813) was produced with 53 conventional PDC cutters backed-up by 27 conical diamond elements. Results, Observations, Conclusions: The 8 ½-in. CoB813 bit was tested on RSS and drilled 615 m at 9.05 m/hr through carbonate that contained 10-40% chert inclusions. Compared to offsets drilled with an impreg/turbine BHA, the CoB bit drilled 12% more meters at 166% higher ROP while providing good wellbore quality and was pulled in excellent dull condition (1-1-CT). The CoB, bit generated larger cuttings enabling geologists to readily identify lithology type/properties. The larger drilled cuttings were easily separated by the centrifuge saving the operator $63,000 in mud cost. The high ROP of the CoB PDC saved six-days rig-time reducing cost/meter by 38% for a total savings of $180,000. Novel/Additive Information: New concept of PDC bit expands the limit of usage in chert contaminated carbonates where previously only roller cone bits or impregnated bit with turibines were used. New type of bit can efficiently drill in those challanging geological conditions improving the drilling time and cost.
IADC/SPE 178815
A Step Change in Drill Bit Technology with Self-Adjusting PDC Bits. J.R. Jain, G.L. Ricks, B. Baxter, C.R. Vempati, V. Peters, J.M. Bilen, R. Spencer, H.C. Stibbe, Baker Hughes Incorporated
Objectives/Scope: The drilling industry now faces the task of drilling diverse sections of the well with a single bit. This is a significant challenge for fixed PDC bits, requiring a compromise that limits vibration mitigation in some sections of the well and/or top end ROP performance in other sections. This paper presents an innovative PDC bit that can self-adjust its DOC control characteristics to the constantly-changing drilling environment and mitigate vibrations while delivering improved ROP. Methods, Procedures, Process: The ability to continuously self-adjust the exposure of DOC control elements is accomplished through a passive hydro-mechanical feedback mechanism encapsulated in self-contained cartridges that are installed inside the bit blades. The DOC control elements mounted on the cartridges respond to the external loads through strategically designed rate-sensitive retraction and extension strokes. During unfavorable dynamic events, the elements engage with the formation and mitigate dysfunctions. During normal steady state drilling, the elements gradually adjust their exposure to enable fast and efficient drilling. Results, Observations, Conclusions: The operating principle of self-adjusting PDC bits is first demonstrated through laboratory drilling tests under confining pressure using full-scale prototype bits. The testing is then expanded to research wells in the field to assess the ability to self-adapt and mitigate stick/slip vibrations. The field test facility offers a controlled yet realistic environment with reduced uncertainty that is often not available in the field. The tests compare stick/slip tendencies of bits by building stability maps in WOB-RPM space based on downhole measurements under similar operating conditions. Bits with the self-adjusting mechanism led to fewer instances of stick/slip than fixed PDC bits in multiple formation types. They significantly expanded the stable operating region and enabled operation at higher ROP. Novel/Additive Information: The self-adjusting bit overcomes several other limitations of fixed DOC control. The technology doesn’t require fixed/pre-designed exposure, prevents over-engagement due to its ability to retract, and eliminates iterative tuning of DOC control currently in practice. The technology is also anticipated to absorb impacts in interbedded formations and reduce damage from improper starting procedures. With a majority of today’s PDC bit drilling applications being torque limited, the technology opens up several possibilities to reduce drilling costs.
IADC/SPE 178822
Innovative Conical Diamond Element Bit Significantly Reduces Drilling Cost of Williston Basin Three Forks First Bench Laterals. J.A. Schilling, E. Cooley, Marathon Oil Co; M.G. Azar, A. White, K.M. Koffler, S. McDonough, J.M. SELF, B. Krough, Schlumberger
Objectives/Scope: The Three Forks First Bench (TF1) in the Williston Basin is attractive to operators for it’s production qualities, but problematic for drilling with Polycrystalline Diamond Compact (PDC) bits. TF1 is an interbedded dolostone, 30-40 ft thick, capped by the abrasive Pronghorn/Sanish formation with high stress variations and laminations. These formation characteristics lead to cutter damage and vibration which cause slow rates of penetration (ROP) and trips due to bit/BHA failure. Methods, Procedures, Process: A revolutionary rock-removal system has been designed. The system implements Conical Diamond Elements (CDE) to work in unison with PDC cutters. Conventional PDC bits complete the 10,000-ft TF1 laterals in 1-bit/BHA only one out of five attempts. The most common reason for tripping is bit/BHA failure due to the harsh characteristics of the TF1. The CDE’s unique geometry applies a concentrated point load to fracture formation more efficiently and its ultra-thick diamond layer provides superior impact strength and wear resistance. The CDE’s withstand the demands of the application where conventional PDC’s alone cannot. Results, Observations, Conclusions: Bits utilizing CDE’s average 5447 ft at 82.8 ft/hr (IADC hours) when placed as the first bit in the lateral. The performance is 10% farther and 15% faster than non-CDE offsets. Analyzing actual down-hole data, CDE’s have proven to mitigate BHA vibrations compared to conventional PDC bits. All of these performance step-changes have led to operators’ one-bit TF1 lateral success rate to go from one out of five to an astounding one out of three. One operator in particular has been raising the technical bar of CDE bits. Since January 2014, this operator’s 1-bit. BHA success rate using conventional PDC bits was 17%. On wells where they utilized CDE’s they improved that rate to 43% providing considerable savings in non-productive time (NPT) tripping. Depending on depth, a trip could cost $80,000 and 16 hr in NPT. The average performance of CDE drillouts for this operator has been 7049 ft at 116.4 ft/hr drilling 18% farther and 14% faster than non-CDE bits for the operator. The reduction in NPT in tripping and improvement in performance has led this operator to prefer drilling with CDE’s. Novel/Additive Information: The use of CDE’s coupled with the conventional PDC cutters is a novel rock-removal system. The CDE’s point-load is always in contact with formation and greatly reduces vibration leading to longer tool life and fewer trips. The CDE’s inherent properties allow the element to maintain shape and sharpness though the application. The PDC cutters maintain a sharp cutting-edge from the support of the CDE’s. Overall bit/BHA life is extended.
IADC/SPE 178880
Unique Range of High Performance Drill Bits with Select PDC Cutter Technology Deliver Breakthrough Performance in Specific Applications Globally. T.S. Roberts, A. Garcia, NOV – Drilling and Intervention
Objectives/Scope: Polycrystalline Diamond Compact (PDC) fixed cutter drill bits have provided significant breakthrough to the drilling industry by extending the boundaries from softer formations, such as shale into harder rocks, such as limestone. The emphasis of this technology is on reducing costs by drilling faster through shale formations, maintaining steerability and stability in increasingly complex wells and ensuring greater durability through abrasive sandstone or tough limestone. The combination of drill bit design and PDC cutter technology affects all of these, though performance is limited when bit balling occurs or the cutter structure suffers from overload or thermal degradation. Methods, Procedures, Process: Several engineering teams were formed, one focused on dynamic bit modelling to better understand the forces on the drill bit cutting structure. All aspects of the bit and assembly were considered and modelled using newly developed software, to ensure optimal performance. Another studied hydraulic design to understand bit balling and improve drilling performance. This included the effect of nozzle orientation, nozzle count and blade height as well as a new flow guide added to the blade front. Computational Fluid Dynamics (CFD) was used to hydraulically design the drill bit for shales. Following CFD simulations, experimental tests in a Pressurized Drilling Lab (PDL) were performed to validate the CFD results. A third team focused on PDC cutter technology by defining the principal failure criteria for each application and engineering a range of PDC’s with the precise properties to overcome these. Following detailed laboratory tests designed to simulate down hole cutter failures, a new Cutter Index (CI) was formed. The CI ranked the cutter technology according to its resistance to three primary failure mechanisms identified: thermal degradation, abrasion, and impact damage. Results, Observations, Conclusions: The teams utilized both numerical and experimental approach to tackle these challenges. Full scale bits were built and tested in the laboratory. The hydraulic team illustrated a Rate of Penetration (ROP) increase of up to 35% compared to baseline bits using improved nozzle orientations and the new flow guides. The new cutter technology including specialized cutter treatments, illustrated several performance advances, the greatest in sandstone, where they demonstrated a 150% improvement in ROP during full scale testing. Novel/Additive Information: By combining extensive dynamic drill bit modelling, improved hydraulics and a strong focus on the true failure mechanisms of the operation, the team was able to prove that improvements in both drill bits and cutter technology can yield breakthrough performance. Several applications clearly show the benefit of both the dynamic and hydraulic modelling and how matching the correct cutter characteristics to the application can yield a remarkable improvement in ROP. This increase in bit performance has permitted operators to drill further and faster, resulting in significant cost savings.
Competence and Training
IADC/SPE 178889
A Paradigm Shift in Well Control Training and Assessment. M. Denkowski, B.G. Kelly, IADC; M. Garvin, Patterson-UTI Drilling
Objectives/Scope: Human factors experts agree that about 80% of incidents in the oil and gas industry are a result of human error. Proper training and assessment is critical to reducing these incidents. Therefore, the upstream sector has implemented a program that represents a paradigm shift in well control training and assessment worldwide. This program focuses on the safety-critical knowledge and skills required for specific rig-based positions. Methods, Procedures, Process: Members of the Well Control Committee of the International Association of Drilling Contractors (IADC) came together post-Macondo to redesign the well control training and assessment standard. They agreed to the following foundational elements of the new standard, called WellSharp: Five “levels” of training; curricula that are focused on the safety-critical job responsibilities of rig personnel; a standardized, proctored online knowledge assessment; enhanced use of simulation for individual trainees; clarified and enhanced instructor qualifications; and the expectation that trainees will complete the training and renew their credentials at the level appropriate to their job position. Results, Observations, Conclusions: The new standard requires trainees to be more engaged in the learning process and to undergo individual skills assessments. The knowledge-assessment database identifies specific knowledge gaps, allows instructors to review and close these gaps with each trainee before the completion of training, provides metrics regarding the alignment between the course taken and the trainee’s job position, and affords analysis of instructor performance. Trainees have reacted positively to the knowledge gaps feedback and the blending of theoretical and practical knowledge in the standardized assessment. Several unexpected benefits have been realized through this collaboration: 1) Development and implementation of the new standard is raising awareness of operational inconsistencies not only from company to company, but also globally. 2) Industry stakeholders can come together to find and agree on solutions and to address industry, public, and regulatory concerns. This effort represents a new kind of commitment to safety, one in which we hold ourselves and others accountable for the benefit of all. Novel/Additive Information: When experts representing the primary stakeholders (operators, contractors, and industry trainers) came together voluntarily to develop and agree on this new standard, they were acknowledging that safety is a part of the non-competitive space of the oil and gas industry. Perhaps more importantly, they were acknowledging the significance of the human element in effective well control.
Wellsharp is a trademarked term of IADC.
IADC/SPE 178845
Industry Initiative – Testing, Certification & Training of Drilling Supervisors to Improve Safety and Performance. P. McAteer, Sysmax Limited; K. Dimitriadis, Tullow Oil; C.R. Taylor, Tullow Oil.; G. Selbie, Premier Oil; N. Whatson, OMV (UK); C.M. Kelly, Nexen Petroleum UK
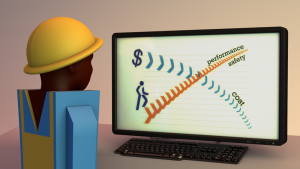
Objectives/Scope: The paper will outline a new industry initiative and system supported by a group of Operators to reduce NPT and enhance safety performance. It addresses competency of Well-Site Supervisors with a group of Operators aspiring to create industry-wide certification. Its paradigm is well control certification which it will complement, addressing all other areas. Competence and experience validation requires a systematic, reliable and repeatable approach. The paper will outline the challenges and response of an Operator group to Well-Site Supervisor Testing, Certification and Training. The Vision is to set the hallmark for quality Well-Site Supervisors globally by providing regularly updated certification. The objective is to: •Prevent repetitive mistakes that cost the industry $billions each year •Differentiate reliable people and support those that need assistance •Measure reactions to simulations of events that occurred •Provide tools to improve and measure individual’s development •Share the resource of quality graded Drilling Supervisors •Incorporate ‘Human Factors’ to test interaction The downturn represents a unique opportunity to set a new standard for an upturn when there will be shortages of quality personnel. Operators will be able to identify qualified personnel and train those that don’t yet meet requirements, providing more quality personnel to share. Methods, Procedures, Process: This initiative; •is focused on reducing NPT and improving Safety performance •certifies the standard reached by the individual in assessments •creates a central knowledge bank of quality Drilling Supervisors to be shared amongst members •will provide online training to support individual and corporate performance improvement •may be extended to Drilling Contractor personnel to enhance learning and capability •enables the industry to reduce cost whilst paying for quality people The system provides centralized certification of modules passed at differing grades, identifying strengths and weaknesses of personnel. It will analyze the team strengths and weaknesses to ensure all skill requirements are covered. The certification provides a true assessment of a supervisor’s capabilities and removes risks associated with CV’s. Results, Observations, Conclusions: This initiative will provide a substantial return on investment by reducing those common mistakes, ensuring supervisory personnel have the right skills and by improving the skills of the nomadic community of Well-Site Supervisors. It will address the Great Crew Change by bringing quality checks and training to people that may not have access to training in some of the subjects of concern. It will also provide evidence of competency for statutory compliance. Novel/Additive Information: The personnel challenges the industry faces and the need for Operators to work together to solve them will be discussed. The views of the member companies and the initiatives direction will be described. An overview of the system will be given during the presentation incorporating simulation of scenarios that actually happened.
IADC/SPE 178824
Crew Resource Management: A Proven Model for Leadership Impact in the Oilfield. P. Tower, L. Motruk, Sanjel
Objectives/Scope: An established leadership model is presented that uses tactics, techniques and procedures from high reliability organizations such as commercial aviation and health care to enhance situational awareness, communication skills, teamwork, task allocation, and decision making among frontline oilfield teams. The positive impact on operational safety and efficiency is drawn from corporate HSE&Q data and anecdotal evidence from field operations. Methods, Procedures, Process: This approach is based on Crew Resource Management (CRM), a leadership model initially developed by NASA for the commercial aviation industry to reduce human error and increase the effectiveness of flight crews. CRM is a human factors approach to operational execution that targets knowledge, skills and abilities, mental attitudes, and motives related to cognitive processes. A high level curriculum is provided and strategies for ease of implementation and real world integration within frontline oilfield operations are described in detail. Results, Observations, Conclusions: Empirical evidence collected pre and post implementation from corporate HSE&Q data established an increase in safety and service quality at the tactical level operations. Three field case studies are analyzed to demonstrate the effective application of CRM in oilfield operations and describe its positive impact in optimizing efficiency in the execution of operations while mitigating risks and maximizing crew safety. Significant findings of this research include overcoming cultural challenges in embedding CRM in an organization. This paper discusses strategies to break down barriers to acceptance by leaders and operators at all levels of the organization. Novel/Additive Information: The novelty of CRM in frontline oilfield operations is that it will enable all crew members to better understand human behavior in order to detect, communicate and avoid or handle significant threats to an operation, action, or task by applying proven and standardized tools which minimize risk and improve efficiency.
IADC/SPE 178889
A Paradigm Shift in Well Control Training and Assessment. M. Denkowski, B.G. Kelly, IADC; M. Garvin, Patterson-UTI Drilling
Objectives/Scope: Human factors experts agree that about 80 percent of incidents in the oil and gas industry are a result of human error. Proper training and assessment is critical to reducing these incidents. Therefore, the upstream sector has implemented a program that represents a paradigm shift in well control training and assessment worldwide. This program focuses on the safety-critical knowledge and skills required for specific rig-based positions. Methods, Procedures, Process: Members of the Well Control Committee of the International Association of Drilling Contractors (IADC) came together post-Macondo to redesign the well control training and assessment standard. They agreed to the following foundational elements of the new standard, called WellSharp: Five “levels” of training; curricula that are focused on the safety-critical job responsibilities of rig personnel; a standardized, proctored online knowledge assessment; enhanced use of simulation for individual trainees; clarified and enhanced instructor qualifications; and the expectation that trainees will complete the training and renew their credentials at the level appropriate to their job position. Results, Observations, Conclusions: The new standard requires trainees to be more engaged in the learning process and to undergo individual skills assessments. The knowledge-assessment database identifies specific knowledge gaps, allows instructors to review and close these gaps with each trainee before the completion of training, provides metrics regarding the alignment between the course taken and the trainee’s job position, and affords analysis of instructor performance. Trainees have reacted positively to the knowledge gaps feedback and the blending of theoretical and practical knowledge in the standardized assessment. Several unexpected benefits have been realized through this collaboration: 1) Development and implementation of the new standard is raising awareness of operational inconsistencies not only from company to company, but also globally. 2) Industry stakeholders can come together to find and agree on solutions and to address industry, public, and regulatory concerns. This effort represents a new kind of commitment to safety, one in which we hold ourselves and others accountable for the benefit of all. Novel/Additive Information: When experts representing the primary stakeholders (operators, contractors, and industry trainers) came together voluntarily to develop and agree on this new standard, they were acknowledging that safety is a part of the non-competitive space of the oil and gas industry. Perhaps more importantly, they were acknowledging the significance of the human element in effective well control.
WellSharp is a trademarked term of IADC.
IADC/SPE 178845
Industry Initiative – Testing, Certification & Training of Drilling Supervisors to Improve Safety and Performance. P. McAteer, Sysmax Limited; K. Dimitriadis, Tullow Oil Intl; C.R. Taylor, Tullow Oil; G. Selbie, Premier Oil; N. Whatson, OMV (UK); C.M. Kelly, Nexen Petroleum UK
Objectives/Scope: The paper will outline a new industry initiative and system supported by a group of Operators to reduce NPT and enhance safety performance. It addresses competency of Well-Site Supervisors with a group of Operators aspiring to create industry-wide certification. Its paradigm is well control certification which it will complement, addressing all other areas. Competence and experience validation requires a systematic, reliable and repeatable approach. The paper will outline the challenges and response of an Operator group to Well-Site Supervisor Testing, Certification and Training. The Vision is to set the hallmark for quality Well-Site Supervisors globally by providing regularly updated certification. The objective is to: •Prevent repetitive mistakes that cost the industry $billions each year •Differentiate reliable people and support those that need assistance •Measure reactions to simulations of events that occurred •Provide tools to improve and measure individual’s development •Share the resource of quality graded Drilling Supervisors •Incorporate ‘Human Factors’ to test interaction The downturn represents a unique opportunity to set a new standard for an upturn when there will be shortages of quality personnel. Operators will be able to identify qualified personnel and train those that don’t yet meet requirements, providing more quality personnel to share. Methods, Procedures, Process: This initiative; •is focused on reducing NPT and improving Safety performance •certifies the standard reached by the individual in assessments •creates a central knowledge bank of quality Drilling Supervisors to be shared amongst members •will provide online training to support individual and corporate performance improvement •may be extended to Drilling Contractor personnel to enhance learning and capability •enables the industry to reduce cost whilst paying for quality people The system provides centralized certification of modules passed at differing grades, identifying strengths and weaknesses of personnel. It will analyze the team strengths and weaknesses to ensure all skill requirements are covered. The certification provides a true assessment of a supervisor’s capabilities and removes risks associated with CV’s. Results, Observations, Conclusions: This initiative will provide a substantial return on investment by reducing those common mistakes, ensuring supervisory personnel have the right skills and by improving the skills of the nomadic community of Well-Site Supervisors. It will address the Great Crew Change by bringing quality checks and training to people that may not have access to training in some of the subjects of concern. It will also provide evidence of competency for statutory compliance. Novel/Additive Information: The personnel challenges the industry faces and the need for Operators to work together to solve them will be discussed. The views of the member companies and the initiatives direction will be described. An overview of the system will be given during the presentation incorporating simulation of scenarios that actually happened.
IADC/SPE 178824
Crew Resource Management: A Proven Model for Leadership Impact in the Oilfield. P. Tower, L. Motruk, Sanjel
Objectives/Scope: An established leadership model is presented that uses tactics, techniques and procedures from high reliability organizations such as commercial aviation and health care to enhance situational awareness, communication skills, teamwork, task allocation, and decision making among frontline oilfield teams. The positive impact on operational safety and efficiency is drawn from corporate HSE&Q data and anecdotal evidence from field operations. Methods, Procedures, Process: This approach is based on Crew Resource Management (CRM), a leadership model initially developed by NASA for the commercial aviation industry to reduce human error and increase the effectiveness of flight crews. CRM is a human factors approach to operational execution that targets knowledge, skills and abilities, mental attitudes, and motives related to cognitive processes. A high level curriculum is provided and strategies for ease of implementation and real world integration within frontline oilfield operations are described in detail. Results, Observations, Conclusions: Empirical evidence collected pre and post implementation from corporate HSE&Q data established an increase in safety and service quality at the tactical level operations. Three field case studies are analyzed to demonstrate the effective application of CRM in oilfield operations and describe its positive impact in optimizing efficiency in the execution of operations while mitigating risks and maximizing crew safety. Significant findings of this research include overcoming cultural challenges in embedding CRM in an organization. This paper discusses strategies to break down barriers to acceptance by leaders and operators at all levels of the organization. Novel/Additive Information: The novelty of CRM in frontline oilfield operations is that it will enable all crew members to better understand human behavior in order to detect, communicate and avoid or handle significant threats to an operation, action, or task by applying proven and standardized tools which minimize risk and improve efficiency.
Well Pressure Integrity-Challenges and Solutions
IADC/SPE 178884
Deepwater Tieback Cementing Design Challenges and Engineering Approach – Gulf of Mexico Case Study. M.I. Dooply, A. El Hancha, Schlumberger; B.E. Koons, M. Saleh, Chevron Corporation; N.C. Flamant, Schlumberger
Objectives/Scope: The Worst Case Discharge (WCD) criteria imposed by the Bureau of Ocean Energy Management, Regulation and Enforcement (BOEMRE) in Deepwater Gulf of Mexico, led to the inclusion of additional tieback strings in casing designs. Challenges in cementing design achieving the ultimate goal of safe placement and effective mud removal, the limitations of current cementing design tools in tieback configurations, then the application of engineering techniques to overcome them with several case studies are discussed. Methods, Procedures, Process: Deepwater tieback cementing designs now include engineering techniques defining the optimum top of cement (TOC) to mitigate the annular pressure build-up (APB), managing high placement pressures resulting from tight annular clearances to keep within the casing hardware limits, optimizing centralization and fluids properties for safe cement placement and effective mud removal, and estimating hook load variations while cementing to prevent premature running tool release. Besides common data inputs, tieback cementing design also need to address the following parameters: •Tieback casing or liner hanger pressure limit •Previous casing and previous liner hanger burst/collapse limits •Tieback string lift / hook load loss Results, Observations, Conclusions: Applications of these engineering techniques resulted in successful cementation of several tieback casings/liners configurations in Deepwater Gulf of Mexico. Several observations on these jobs include the following: •Density differential of 10% is not possible between displaced and displacing fluids •Displacement efficiency is mainly affected by friction pressure rather than density hierarchy •Pumping lower viscosity fluid ahead reduces ECD and allow achieving higher TOC •Fluids rheology to meet friction hierarchy is adjusted based on the lowest shear rate, and not to exceed the pressure limits while achieve optimum displacement efficiency •Stage pre-job mud circulation to understand expected ECD/SPP and adjust the model/design •Hookload must be monitored during the job to ensure the tieback hanger stays in tension •Calipered casing IDs and ODs should be used in hydraulic simulation •No fluid U-tubing is observed (flow-in = flow-out) •Small volume batch-mixed cement slurry with extended slurry setting time is designed •Fluid intermixing while descending inside tiebacks can influence surface pressure •Dynamic hookload can be obtained from dynamic buoyancy and hydrodynamic drag calculations •Commercial cementing hydraulic simulator does not consider rheology and friction pressure changes due to fluids intermixing and eccentricity effect in friction pressure drops. Novel/Additive Information: Learnings from several case studies resulted in the adoption of never applied new design considerations. •Calculation of previous casing and previous liner hanger burst limits based on burst ratings and assumed hydrostatic pressure behind. •Calculation of hookload loss due to applied surface pressure and friction pressure while cementing. Hookload loss is mainly produced by dynamic buoyancy proportional to surface pressure, and affected by hydrodynamic drag proportional to fluids rheology, annular clearance and tieback OD area.
IADC/SPE 178854
A New Method to Mitigate Annular Pressure Buildup by Using Sacrificial Casing, Case Study: Deepwater Well X, Indonesia. R. Rizkiaputra, Institut Teknologi Bandung; Y.R. Costamte, I.T. Wibowo, Chevron Indonesia; S. Mabunga, Halliburton Software and Asset Solutions
Objectives/Scope: The aims of this study are to provide knowledge of new annular pressure buildup (APB) mitigation by using sacrificial casing in aspects of design and its application in deepwater well X, Indonesia. It is expected that the study can be used as reference in future application in other deepwater wells as to mitigate APB by using sacrificial casing. Methods, Procedures, Process: In recent deepwater installation (well X), the subject well firstly has the burst disk as an APB mitigation method, but in the process, the burst disk is no longer reliable option due to non-technical reason, the only option left is using an alternate APB mitigation method that is sacrificial casing. First, three major parameters is needed to successfully mitigate the APB by using sacrificial casing, there are reservoir conditions, formation characteristics, and wellbore configuration. After inputting the parameters, the pressure and temperature model is created. After the models created, the APB analysis with the sacrificial casing scenario is conducted by using multistring analysis (service life condition) which results the final casing configuration. The sacrificial casing in well X is 20 inch 154 ppf X-56 casing, three scenario which are drilling operations, production operations and worst case discharge (WCD) operations in the sacrificial casing section will be discussed in detail in this paper. Results, Observations, Conclusions: Well X is planned to have the sacrificial casing in 20 inch 154 ppf X-56 casing string. First is the drilling operations, the maximum mud drop for this case should not exceed by 4800 ft MD with 9.6 ppg to keep collapse design factor >= 1, string integrity is sufficient for the rest of the drilling operations modeled. Second is the production operations, during production with the 20″ x 13-5/8-in. annulus sealed and without the presence of the 20-in. burst disk, the maximum anticipated APB on the 20-in. x 13-5/8-in. annulus will result in triaxial safety factor of 1.163 for the third string section, which expected as the ‘sacrifice casing zone’, string integrity is sufficient for the rest of production operations modeled. Third is the WCD, maximum APB present on the 20-in. x 13-5/8-in. annulus for the WCD load case modeled does not pose string integrity issues, string integrity is sufficient for the rest of the WCD operations modeled. To conclude, sacrificial casing has been successfully used to mitigate the harmful effects of APB by sacrificing the 20-in. 154 ppf X-56 casing in the third string section (5793 ft – 6234 ft). Novel/Additive Information: This study gives a breakthrough of generating new method to mitigate the APB by using the sacrificial casing. Furthermore, it could be a basis of APB mitigation by using sacrificial casing in deepwater well project across the globe.
IADC/SPE 178807
Modeling and Simulation of Annular Pressure Buildup (APB) Mitigation Using Rupture Disk. Z. Liu, R. Samuel, A.C. Gonzales, Y. Kang, Halliburton
Objectives/Scope: Annular pressure buildup (APB) in a deepwater well could result in wellbore failure, even during drill-ahead operations (Pattillo et al. 2004). Manufactured to burst/collapse at a specific pressure difference and installed in the casing wall, a rupture disk is a common device used to mitigate APB and protect casing strings. This paper focuses on the modeling and simulation of the effects of a rupture disk burst/collapse event on APB in casing/tubing annuli. Its aims include more accurate casing/tubing load analyses and, consequently, more confident wellbore design with a sufficient safety margin at an acceptable cost. Methods, Procedures, Process: After the rupture disk bursts (or collapses), fluid will move through the open disk from one annulus to another, resulting in changing pressures. In this work, three pressure balance models (piston model, miscible fluid model, and immiscible fluid model) were established to calculate the annulus fluid pressure and volume changes after the rupture disk opens. The piston model, assuming no fluid exchange between two annuli, provides the simplest solution. It is accurate if the two annuli contain nearly identical fluids. The miscible fluid model is intended for annuli with the same fluid type, but with different density values. The immiscible fluid model is intended for annuli with different immiscible fluid types, such as oil-based mud in the internal annulus and water-based mud in the outer annulus. The pressure balance models were implemented and integrated into a commercial casing and tubing design software platform. A numerical approach was used for trapped and connected annuli; an analytical approach was used for connected annuli with at least one ventilation or leakoff point. This combination provides optimized simulation performance and accuracy. When multiple annuli are connected with open rupture disks, global pressure equilibrium is reached through iterations of handling two connected APB regions at a time. Results, Observations, Conclusions: In a case study in which the casing ballooning effect is negligible, numerical simulation results were found to be consistent with the results of analytical calculation; the difference is within 0.1%. The application of the rupture disk for APB management was also demonstrated in another case study using field data. The simulation results show that the rupture disk is a viable and cost-effective option for APB management. Simulations using different pressure balance models were compared, and the difference and possible deviation range of the results were estimated. Novel/Additive Information: To our knowledge, no other modeling and simulation work on APB mitigation with rupture disks has been reported. Combined with thermal flow and APB simulators, the implementation of rupture disk pressure balance models can provide valuable information to assist well design engineers in the design of deepwater wells with long term well integrity.
Unconventional Drilling
IADC/SPE 178851
A Gear-Reduced Drilling Turbine Provides Game Changing Results: An Alternative to Downhole Positive Displacement Motor. S. Jones, C. Feddema, Turbo Drill Industries
Objectives/Scope: Drilling turbines have historically been used for hard rock applications in conjunction with diamond impregnated drill bits. Their use in North America land was typically restricted by rig stand pipe pressure limitations. Now, the latest generation rigs in North America land have sufficient stand pipe pressure to make use of drilling turbines. Reducing the bit speed of a drilling turbine can provide significant advantages. Reducing the bit speed and increasing torque now makes the turbine suitable for a wider range of drilling environments, including very high temperature wells. High performance Positive Displacement Motors (PDMs) generate significant vibration which can reduce the life of MWD systems. On the other hand, Drilling Turbines produce very little vibration hence the life expectancy of BHA components can be increased. Drilling with less vibration will lead to a more efficient drilling system. This paper describes the operation and field test results from a new Gear Reduced Drilling Turbine (GRDT). Key components in the GRDT were instrumented vibration/shock and temperature sensors to gather critical information on vibration, shock, temperature, RPM and stick-slip events. Methods, Procedures, Process: A GRDT has been designed to provide superior performance in specific formations. The drilling results from the GRDT will be compared to PDM drilling the same formations. Both PDM and GRDT Bottom Hole Assemblies (BHA) were instrumented with three-axis inclinometers, three-axis shock sensors and two redundant temperature sensors to capture and compare downhole dynamics of the tools. The drilling performance, downhole dynamics data, temperature distribution of the tools and BHA post run condition will be compared to show the improvements gained from the new GRDT. The paper will also compare the economic gains between PDM and GRDT. Results, Observations, Conclusions: The data received from the downhole instrumented devices provided valuable information on drilling dynamics to compare PDM and GRDT performance. This data will be discussed and correlated to improvements made during the course of the field test. Comparing the distributed shock/vibration and temperature data in PDM and GRDT showed a significant difference in the drilling dynamics signature of both systems. The GRDT produced a more stable drilling signature that improved drilling energy transfer to the bit and ultimately led to improved rate of penetration. The new GRDT has proven to provide significant drilling performance and economic improvements. Novel/Additive Information: A GRDT has been instrumented to provide critical downhole data while under field test. The data gathered from the instrumented sensors helped make critical decisions in the development stage and early prototyping stage of the product. These instruments were used to gather information such as shock, vibration, inclination, RPM, temperature and stick-slip.
IADC/SPE 178870
Case Study – Using Wired Drill Pipe, High Speed Downhole Data, and Closed Loop Drilling Automation Technology to Drive Performance Improvement Across Multiple Wells in the Bakken. D.K. Trichel, M.R. Isbell, Hess; B. Brown, Hess; I. Fonseca, National Oilwell Varco; M. Flash, NOV Downhole Tools Division; M.W. McRay, J. Nieto, National Oilwell Varco; F.T. Kpetehoto, Baker Hughes Inc; B. Vogt, Baker Hughes
Objectives/Scope: Many modern operators use internal optimization processes to drive continuous improvement by identifying and removing ROP limiters to reduce well delivery time and cost. Optimization processes typically include three basic performance improvement cycles. Each of these cycles moves at a different pace. The first cycle, moving at a fast pace, is the real time management of drilling parameters to safely maximize penetration rate and drill bit run length with the drilling system currently in the hole. The second cycle comes from recognizing the drilling system configuration needs changing based on performance data collected during the run. These changes can only impact the following bit run or the same interval on a future well. The third performance improvement cycle involves the technology and methods for the entire drilling system and moves the slowest. The third cycle requires detailed post-well analysis of performance trends and massive amounts of digital data collected over multiple wells to identify root causes of performance limiters which is then applied to the drilling system re-design. Lessons-learned can be developed and applied to drilling programs from all three cycles reducing drilling time and cost. Methods, Procedures, Process: This paper will describe drilling an 8 ¾” hole section across multiple wells using a scientific approach to continuous improvement with a real-time closed-loop system as a tool to enable rapid learning for continuous improvement. The optimization process adopted key elements from lean manufacturing concepts and the operator’s drilling practices. The optimization process uses the Plan, Do, Check, Adjust (PDCA) as the four basic phases, with the drilling system and the provided data impacting each step. The drilling automation system can be described as an intelligent system with software applications controlling and integrating surface and downhole measurement. This system controls drilling parameters and ultimately improves the penetration rate. Results, Observations, Conclusions: To date, seven of ten 8 ¾-in. hole intervals drilled with this system exhibited top quartile performance from a rig that had not drilled a top quartile well for at least 2 years. One well had at least 45 hr of invisible lost time removed from on-bottom drilling in a single hole section, compared to average performance for the last three pads drilled with this same rig. Lessons-learned have been collected and implemented across the operator’s rig fleet in the Bakken. All three continuous improvement cycles are ongoing, but the slow-moving cycle is now driving a formal “Design of Experiments” BHA optimization effort.
IADC/SPE 178875
Team Approach to Horizontal Drilling Optimization in the Marcellus Delivers Record Setting Performance. D.A. Livingston, Baker Hughes; R. Coffman, K. Gorr, Consol Energy; D. Andes, M. Czerneski, S. Bauer, Baker Hughes
Objectives/Scope: The Marcellus tight gas shale formation in the northeast Appalachian region of the USA represented 40% of total domestic production in 2014 and 2015, and is strategically positioned close to its gas demand. To increase production and improve well economics, operators are drilling from multi-well pads, requiring complex well profiles. This is driven by local logistics and environmental requirements. This paper will discuss the main drilling challenges faced by one operator and their directional drilling provider, while drilling more than 1 million feet in this area, and the evolution of effective drilling practices including bit and bottom hole assembly (BHA) design, drilling parameter optimization and reservoir navigation techniques. This resulted in the achievement of a drilling record of a mile a day on the most recent pad. Methods, Procedures, Process: Typically steerable motor assemblies require multiple runs to drill the curve and lateral sections of a directional well. Different formations in the curve may yield different build-up rates (BUR) requiring close attention to well planning and execution to land in the target zone. Longer laterals for optimal lease development may cause undesirable torque management issues. A drilling system with near bit inclination capability and near bit gamma is ideal for TVD control to stay in the producing target zone. Recent advancements in rotary steerable systems (RSS) have resulted in high build-up rate designs that meet these requirements. To address these challenges, the operator, engineering and service companies created a drilling program for eight wells with the objective of drilling the 8 ¾-in. hole section in one run, including 3D well profiles, matched bit and BHA designs, optimized drilling parameters for each curve and lateral portions of the well, and reservoir navigation techniques. The 8 ¾-in. hole section length ranged from 4,400 to 14,700 ft including curves varying from 8°/100ft to 10°/100ft and an average lateral section length of 9,700 ft. Results, Observations, Conclusions: The results of this team approach and optimized drilling program delivered improved rates of penetration (ROP) by 10% compared to previous pads and an average of 1.12 runs/well. The two most recent wells set drilling records of a mile in a 24 hour period resulting in 31% and 30% reduction in drilling time while staying 100% in the target zone compared to 97% average from previous pads. This successful collaboration between all parties involved resulted in optimized drilling time, reduced operational costs and financial predictability and consistency. Novel/Additive Information: The authors will explain the process used and show examples of this outstanding drilling performance using case histories from the program in the Marcellus shale play.
IADC/SPE 178883
Improved Drilling Performance in Extended Horizontals Using Clean Brines in the Williston Basin. B. Thompson, QEP Resources; H.L. Dearing, S. Jones, J.M. Shipman, Newpark Drilling Fluids
Objectives/Scope: Innovation, technology development, and drilling efficiencies are vital to the successful development of an oil and gas well. This is particularly important as lateral lengths increase. Due to the low permeability of the Williston Basin, long lateral lengths maximize production. However, lateral length is limited by the frictional losses caused by torque and drag. Therefore, the operator required a drilling fluid that would maintain low lubricity coefficients. Historically, these long laterals were drilled with a weighted oil-based fluid. The operator wanted an environmentally sound and cost-effective alternative. An under-balanced high-performance brine drilling fluid (HPBDF) was proposed. Methods, Procedures, Process: This paper presents the innovation and adoption of HPBDF in drilling over 100 Bakken wells and the challenges that were overcome. It also discusses the equipment and techniques for evaluating lubricity correlating it to torque and drag. The HPBDF required different strategies than the oil-based fluid. Suspended solids in drilling fluids increase abrasivity, which can lead to increased torque and drag and directional tool failures. In the HPBDF system, accumulated solids were eliminated with a dewatering system. The system produces a clean brine by flocculating the solids and removing them with a centrifuge. A brief outline of the Williston and Bakken formations and its mineralogical and geological composition via x-ray diffraction will be presented as well. Results, Observations, Conclusions: Rates of penetration (ROP) were increased and pipe wear was decreased by monitoring and managing torque with a drilling performance enhancer additives. Field measurements of lubricity coefficients ensured the maintenance of an adequate concentration of the additives. The increased ROP shortened drilling days (originally 17-20 days to 11-14 days), reducing the operator’s spread costs by 20%. Wellbore cleaning was achieved by minimizing the viscosity of the brine, allowing turbulent flow to aid cuttings transport. This allowed for reduced time spent on clean up cycles and tripping compared to offset wells drilled with oil-based fluids. Solids content was minimized by the reduced need for barite as the brine base-fluid has a higher density than an oil base-fluid. Novel/Additive Information: The HPBDF explored in this paper illustrates a drilling fluid that is in balance with the environment and overall cost overruns. The additives have been discussed previously and are well understood. This paper will illustrate the unique challenges the Williston Basin presents and how this drilling fluid was versatile enough to meet the operator’s needs.
IADC/SPE 178897
Pursuing Drilling Improvements in the Eagle Ford – More than 40% Reduction in Drilling Time and Cost in Just Two Years. C.J. Coletta, S. Mendenhall, C. Arias, Statoil ASA
Objectives/Scope: Drilling time and cost have been considerably optimized in the Eagle Ford through the implementation of several techniques and processes that allowed to archive more than 50 % improvement in time and 40% cost reduction. This paper will discuss the drilling problems encountered and detail the actions taken to overcome these problems. Methods, Procedures, Process: Drilling wells in the Eagle Ford is a challenge because of the difference in lithology throughout the well, pore pressure profiles, high temperature, geosteering requirements and casing design. These challenges needed to be addressed in the design and execution phases of these wells. In Addition, multiple trips due to downhole tool failures and low ROP contributed to increased non-productive time (NPT) with the associated costs. When Statoil took over the operatorship in the Eagle Ford an integrated approach to engineering and operations was key to optimize performance and gain understanding of the area. In addition, application of adequate technology along with standardization of operations have resulted in continuous performance improvement. Results, Observations, Conclusions: Several factors played a role in the drilling performance improvements, including detailed planning and execution, standardization of drilling operations, application of rotary steerable, implementation of an optimized casing design, contractor performance management, communication between the teams, implementation of a performance incentive, and properly managing risk. Novel/Additive Information: Over the past two years, more than 80 wells have been drilled in the Eagle Ford by Statoil. The techniques and procedures applied to optimize operations have resulted in valuable lessons learned that can be applied to a variety of wells in the Eagle Ford and similar areas.
IADC/SPE 178885
Multi-Laterals in the Mississippi Lime. R.A. Meize, SandRidge Energy Inc; L. Reid, F. Dano, SandRidge Energy
Objectives/Scope: Resource plays are constantly challenged with ways to reduce costs and cycle times. The Mississippian carbonate reservoir offers thickness and rock strength together with stacked pay conducive to multi-lateral techniques and their inherent cost savings. A multi-disciplinary team has drilled and completed 25 multi-laterals of various configurations to test the mechanical feasibility along with associated cost and production benefits. This presentation covers details on operational techniques needed to successfully build the multi-lateral wellbore, pro’s and con’s associated with the different concepts and some of the initial cost and production results. Methods, Procedures, Process: Open hole sidetracks along with cased hole whipstocks have been used to initiate the multi-laterals. The reservoir requires stimulation which necessitates running a packer and sleeve system typically run on a 4-1/2-in. liner. After stimulation, the casing is cut-off in the open hole leaving each leg open to the multi-lateral junction to produce into a common wellbore. Several of the full-section developments utilize simultaneous operations with frac work done with the drilling rig on location. Results, Observations, Conclusions: Over 25 multi-laterals have been completed with 100% mechanical success. Directional techniques and completion systems make this a viable alternative to single well laterals enabling cost reductions on a field-wide development. These cost reductions provide needed benefit in a reduced oil price environment. Novel/Additive Information: SandRidge Energy started work in the Mississippian play in Oklahoma & Kansas beginning in 2009. The use of horizontal drilling techniques in this mature carbonate reservoir together with an aggressive infrastructure strategy has led to over 1,200 horizontal wells being drilled. The multi-lateral program is ongoing, so additional production information and results can be shared by time of final publication.
Smart Systems and the Internet of Things
IADC/SPE 178814
Systems Architecture and Operations States for Drilling and Completion: The foundation to real performance measurement and drilling systems automation. J.P. de Wardt, DE WARDT & Co.; C. Inabinett, SPE; M.L. Laing, SAS Institute.; J.D. Macpherson, Baker Hughes
Objectives/Scope: The highly fragmented nature of drilling and completion operations results in complex interactions that inhibit performance and systems automation. Reorganization into interconnected systems in a designed architecture aligned to key performance requirements and constraints solves this fragmentation. This realigned systems architecture provides a solid foundation to effectively measure and drive system performance, and implement drilling systems automation. In current wellsite activities, the “operation state” identifies activities in drilling and completion operations, and is critical to accurate performance measurements, in managing automation modes, and in activating automation controls. Although definition of operation states related to drilling (“drilling states”) exists, there is significant work remaining to validate a complete spectrum of these states, and to define completion states, wellbore states and other operation states. Methods, Procedures, Process: Systems architecture developed through systems engineering is a well-established practice in the automobile, aviation and aerospace industries. It enables multiple suppliers to coordinate their efforts toward commonly agreed performance criteria. Applying systems architecture to drilling and completion operations will concurrently enable more appropriate performance measures and drivers while creating the necessary foundation for effective drilling systems automation. Drilling performance measurement from sensor data has become a common practice. Processing relies on defining the drilling state at any time by detecting various machine operations, and then measuring the duration of the defined state to understand its effect on cycle time for drilling and completing a well. Current practice relies on the machine operations of raising and lowering the blocks, rotating pipe and pumping fluid. The system is usually blind to those activities that do not involve these operations. The drilling systems automation roadmap (published in SPE 2014) recognized the need to use defined drilling states, and other operational states, to match the correct control application with the current rig activity, borehole condition, equipment condition, etc. Results, Observations, Conclusions: This paper will describe the concept of systems architecture as applied to land based repetitive horizontal shale wells and offshore exploration wells. It will explain how to develop systems architecture for specific drilling projects. The paper will discuss the development of a range of operational states for performance monitoring and systems automation. These guidelines will enable all parties involved in either monitoring performance or implementing systems automation to use a common framework in a coherent and effective manner. Novel/Additive Information: A robust systems architecture combined with fully vetted operational states enables highly complex autonomous operations in automotive and aerospace applications. Implementation of these concepts in drilling and completing wells will support the effective application of systems automation as well as have a significant positive impact on measuring and improving performance.
IADC/SPE 178821
Next Generation Kick Detection During Connections: Influx Detection at Pumps Stop (IDAPS) Software. B. Tarr, D. Sanchez, D. Ladendorf, Shell International E&P Inc.; M. Milner, CoVar Applied Technologies
Objectives/Scope: At least 25% of all influx events on exploration wells occur while making connections but few rig contractors employ kick detection alarms to alert the driller during a connection. Due to the transient flow characteristics associated with connections, kick detection during connections is the most challenging to automate effectively. The Influx Detection at Pumps Stop (IDAPS) software was developed to provide early warning of abnormal flow back conditions during connections. Methods, Procedures, Process: During IDAPS operation, pumps-off occurrences are automatically detected and saved as unique events, with associated bit depth, flow-in, flow-out and pit volume data. Machine learning algorithms are applied to recent pumps off event data patterns to adaptively calculate limits for “normal” events. The adaptive nature of these limits allows IDAPS processing to adjust to changes such as increasing hole depth. Existing flow-in, flow-out and pit volume sensors are used; no additional sensors are required. Particular attention was paid to achieving high probability of detection (Pd) at low false alarm rates (FAR) to minimize nuisance alarms, and fast influx detection times to reduce kick volumes. Results, Observations, Conclusions: IDAPS has been deployed in an operator’s real-time operations center for monitoring critical offshore wells since 2014. Each new pumps-off event is evaluated in real-time and statistically meaningful deviations from the recent “normal” limits generate corresponding influx alarms at one of four confidence levels (low, medium, high, and confirmed). Additionally, based on data pattern recognition algorithms, the software detects and notifies the user of circulation system data validity issues that could otherwise impair influx detection performance, e.g., malfunctioning flow sensor, unusual pit volume gains, etc. Overlay plots of current and historical flow and pit volume data have been shown to be valuable in significantly reducing the time required by the user to validate anomalous pumps-off event data automatically identified by IDAPS. Based on extensive validation, using a combination of historical real-time data (from over 30 wells and 10,000 hours of operation) and kick simulations, the demonstrated false alarm rate for IDAPS is five per 1,000 connections with a 100% influx detection rate. The use of IDAPS to reliably detect influx has improved safety, operational efficiency, and driller situational awareness. Novel/Additive Information: IDAPS represents a new generation of kick detection software that uses an automated “finger printing” method for generating kick alarms (based on confidence level) during connections that is faster and more reliable than other available methods.
IADC/SPE 178787
Data Ownership for Drilling Automation – Managing the Impact. J.D. Macpherson, Baker Hughes; J.P. de Wardt, DE WARDT & CO.; M.L. Laing, SAS Institute.; N. Zenero, Chesapeake
Objectives/Scope: Drilling systems automation depends on timely flow of accurate and relevant data from multiple sources to control equipment, machines and processes. The fragmented nature of the drilling operations business means that data must be shared between the various companies contracted to perform services, and the various companies must trust that data. This paper describes the issue of data ownership in terms of the application of drilling systems automation, and proposes solutions. Methods, Procedures, Process: Various parties in a drilling operation measure, collect, report, and analyze data. These various parties take actions to avoid problems and improve performance, using information derived from the data. Data is used both in real-time by those operating the drilling rig and various drilling tools, as well as periodically to advise the onsite drilling team. The data flow loops range from high frequency, low latency response loops at the wellsite to low frequency, high latency response loops in remote centers. The SPE Drilling Systems Automation Technical Section (DSATS) has identified OPC UA as the most suited communications protocol for multi-directional fast loop control systems. In these environments, there is a high likelihood that a controller from one supplier will use data created by another supplier. Results, Observations, Conclusions: Drilling systems automation requires structured and organized data sharing between parties. Data exchange adds value to the drilling process. A conceptual data model describes at least three classes of data generated while drilling, and all lie within the confidentiality envelope of the operator or governmental agency. There is data that is the property of the generator (such as equipment condition monitoring data), there is data that is restricted (such as formation evaluation data), and the third class is data shared in an “open data pool” for the purposes of drilling systems automation. Since ownership means responsibility for data quality, it is important that each data generator own its contribution to the shared data pool. The data aggregator – the party managing the shared data pool – is therefore not the owner of all the data in the pool, but a caretaker of that data. Novel/Additive Information: This paper will describe the history of data measurement, data flow and data ownership in the drilling industry. It will address data ownership issues pertaining to both drilling systems automation and drilling performance improvement. Analogies from other industries will assist in understanding how those industries advanced their automation applications and processes in a multi-supplier environment. The paper will present a data ownership and data sharing solution that will provide an environment for drilling systems automation.
IADC/SPE 178871
Field Performance of Automated High-Speed mud Pulse Telemetry System. W. Emmerich, I. Ben Brahim, A. Greten, O. Akimov, Baker Hughes
Objectives/Scope: Present logging-while-drilling (LWD) technologies have substantially increased the amount of information collected downhole. Mud pulse telemetry (MPT) is the core real-time data transmission technology in the oil industry, and it must deliver answers while drilling with equal log densities despite the increased number of services. Ultimately, higher real-time data rates are required when a compromise between rate of penetration (ROP) and log density is not an option. Especially when using high-density and high-plastic viscosity oil-based muds in deep wells, transmitting data at high rates presents challenges due to the harsh transmission channel conditions. Methods, Procedures, Process: We describe improvements to the MPT system, enabling reliable data transmission with physical data rates of 10 bits/s and higher. Special signal sequences are used to automatically adjust adaptive filters. The pulser sends out the sequences regularly, enabling the surface system to tune the adaptive filters for changing channel conditions. The filter performance is tested and saved into a data base with quality indicators, empowering field personnel to optimize decoding quality through better decision making. Enhanced signal processing algorithms on the surface significantly increase the success rate of this automated system, as well as improve the decoding quality and reliability. Results, Observations, Conclusions: This improved MPT system has been effectively run in challenging fields in different regions. It has achieved improved operational performance and higher system reliability compared to offset runs. Complex BHAs with many LWD services can be deployed with outstanding data density and without ROP reduction. Its ease of use enables the increase of real-time data rates and timely decisions when decoding quality indicators start to decrease. Furthermore, the new system introduces higher automation level, which allows the field service engineer to concentrate on delivering more answers to the operator. Novel/Additive Information: By enabling high-speed data rates in a wider variety of environments as well as higher data rates in standard settings, the improvements in MPT increase the safety while drilling and lower the overall cost of drilling wells.
IADC/SPE 178873
Remote Directional Drilling and Logging While Drilling Operations in the Arctic. C. Chatar, A. Stepnov, A. Mardyashov, C. Ke, E. Elizondo, Schlumberger
Objectives/Scope: Few locations present as many challenges as drilling in Arctic. How do you drill in the most hostile environments in the world? How do you handle the most remote locations, the toughest logistics and the biggest gap in infrastructure? While the industry has moved progressively over the past decades to meet these challenges, one company’s solution in terms of personnel, cost, safety and the environment was to do the job remotely. Methods, Procedures, Process: We are not only talking about monitoring or support from town offices. We are discussing a fundamental paradigm shift where the directional and MWD crew is not physically located on the rig. In order to accomplish this, there had to be a major transformation. Technologies had to be qualified and workflows had to be modified. Roles and responsibilities were redefined. There was also a major challenge to convince operators to allow the control to come from a source external to the rig. There are many associated risks with such operations. These risks include loss of connectivity, methods for diagnosing tool failure and hardware failure to name a few. Results, Observations, Conclusions: In this paper the authors begin with a brief history of remote operations (RO) indicating major milestones. The challenges of implementation of RO centers are then discussed. Prevention and mitigation of associated risks is also discussed. Given the great success in implementation of a major RO center in the Arctic, the details of methods and technologies used to achieve success is also discussed with specific focus on the Arctic operations. Many of the challenges and methodologies will be supported by details of real world implementation. Novel/Additive Information: Theoretically, wells could be steered and controlled from the comfort of your couch at home; millions of dollars’ worth of technology controlled from thousands of miles away. We have enough data, communication capability and technology to make this a reality. And that was exactly what we did.
IADC/SPE 178900
Efficiently Transferring and Sharing Drilling Data from Downhole Sensors. T. Baumgartner, Y. Zhou, E. van Oort, University of Texas at Austin
Objectives/Scope: The drilling industry has begun to cherish the value of data collected from downhole sensors, often gathered at high frequencies. Moreover, it has started to capitalize on the availability, analyses and credibility of this data through step-changing knowledge gains that have enabled meaningful drilling performance improvements. As a result, topics like data quality, data ownership, and data integration are now routinely being discussed among stakeholders as data from downhole memory tools slowly starts to integrate into routine well planning and optimization workflows.The collectors of data usually are not the sole owners and main beneficiaries of such data. Large amounts of data have to be transferred from the service provider to various collaborators within and across companies. The process of agreeing on data formats, relevant accessory information and means of transfer, is currently laboriously repeated on a project-by-project basis. This practice not only consumes unnecessarily resources on both ends, but also carries the risk of losing crucial contextual information. WITSML standards are often unsuitable for large high frequency data files and do not provide enough flexibility for certain contextual information. Methods, Procedures, Process: This work proposes a file format, with which downhole sensor data can be securely stored and shared across all stakeholders, providing both flexibility and simplicity. The proposed file format implements a set of specialized horizontal and vertical dividers to structure contextual information on the well, the run, and the sensors, and to store them in the same file as the measurements. Among other things, well and section information, responsible personnel, equipment and sensor properties, time calibration, and operational parameters may be specified. The inclusion of both required and optional inputs ensures both flexibility and essential context, and allows the coverage of a variety of applications. It is comparable to the Log ACSII Standard (LAS) file that quickly found wide acceptance in the well logging community and beyond after its introduction in 1990. Results, Observations, Conclusions: The implemented dividers enable easy access to the data files by variety of programs and comfortably viewed by human eye using any standard spreadsheet or text file application. Importing and exporting applications will be provided to the users, who can then easily produce these files from raw data for transfer or integrate them into existing data management systems. Novel/Additive Information: Stakeholders, such as operators, service companies, and tool manufacturers are involved with the creation of this standard file format to ensure consent amongst all users. The standardization of downhole sensor data files proposed in this work marks an important step towards automated analysis of downhole data, reduction of data loads and data integration. Our approach is illustrated using various examples of how the new standard can be applied on actual field data.
IADC/SPE 178900
Efficiently Transferring and Sharing Drilling Data from Downhole Sensors. T. Baumgartner, Y. Zhou, E. van Oort, University of Texas at Austin
Objectives/Scope: The drilling industry has begun to cherish the value of data collected from downhole sensors, often gathered at high frequencies. Moreover, it has started to capitalize on the availability, analyses and credibility of this data through step-changing knowledge gains that have enabled meaningful drilling performance improvements. As a result, topics like data quality, data ownership, and data integration are now routinely being discussed among stakeholders as data from downhole memory tools slowly starts to integrate into routine well planning and optimization workflows.The collectors of data usually are not the sole owners and main beneficiaries of such data. Large amounts of data have to be transferred from the service provider to various collaborators within and across companies. The process of agreeing on data formats, relevant accessory information and means of transfer, is currently laboriously repeated on a project-by-project basis. This practice not only consumes unnecessarily resources on both ends, but also carries the risk of losing crucial contextual information. WITSML standards are often unsuitable for large high frequency data files and do not provide enough flexibility for certain contextual information. Methods, Procedures, Process: This work proposes a file format, with which downhole sensor data can be securely stored and shared across all stakeholders, providing both flexibility and simplicity. The proposed file format implements a set of specialized horizontal and vertical dividers to structure contextual information on the well, the run, and the sensors, and to store them in the same file as the measurements. Among other things, well and section information, responsible personnel, equipment and sensor properties, time calibration, and operational parameters may be specified. The inclusion of both required and optional inputs ensures both flexibility and essential context, and allows the coverage of a variety of applications. It is comparable to the Log ACSII Standard (LAS) file that quickly found wide acceptance in the well logging community and beyond after its introduction in 1990. Results, Observations, Conclusions: The implemented dividers enable easy access to the data files by variety of programs and comfortably viewed by human eye using any standard spreadsheet or text file application. Importing and exporting applications will be provided to the users, who can then easily produce these files from raw data for transfer or integrate them into existing data management systems. Novel/Additive Information: Stakeholders, such as operators, service companies, and tool manufacturers are involved with the creation of this standard file format to ensure consent amongst all users. The standardization of downhole sensor data files proposed in this work marks an important step towards automated analysis of downhole data, reduction of data loads and data integration. Our approach is illustrated using various examples of how the new standard can be applied on actual field data
IADC/SPE 178778
Analysis of Bottlenecks in the Efficient Thermal Dissipation from Electronics in a Drilling Tool. A. Sur, K.M. Rashid, Halliburton; S. McPheeters, QuEST Global Inc.; D. Winslow, Halliburton
Objectives/Scope: A direct consequence of ensuring enhanced control and sensing capabilities in drilling tools is a substantial increase in the electronic devices in these tools. To ensure reliability of the electronics, especially in the harsh operating environments (ambient temperatures of 175°C and pressures of 25,000 psi), effective thermal management techniques must be implemented. This paper identifies and assesses bottlenecks and their effects on the thermal transport process in a BHA component. Methods, Procedures, Process: A combination of experimentation and numerical computation was used to identify the areas in a design that play a significant role in thermal dissipation in a drilling tool. The experiments were conducted at controlled boundary conditions; FEA-based numerical models were developed to simulate the experiments. Multiple test assembly configurations were used in the experiments, and simulation models were developed for each configuration. Numerical model results were compared with experimental measurements, and the sensitivity of various factors which contribute to the overall thermal resistance was investigated. Finally, a parametric design study was performed using the developed numerical model. Results, Observations, Conclusions: The experimental results show that the temperature of the electronic devices is more sensitive to the power dissipation rates than to the convective heat transfer coefficient for the range of values tested in this study. The numerical results show an excellent agreement with the experimental measurements, validating the developed numerical model and the associated assumptions for the various assembly configurations investigated in this work. In the developed numerical model, the effect of contact thermal resistances on the temperature of the electronics was studied. The contact thermal resistances were calculated by using applicable correlations from the literature, and the calculated value was used in the simulations. These correlations account for the effect of surface finish, bolting pressure, surface hardness, and interstitial material choice. Overall, the maximum temperature attained by the electronic components was found to be sensitive to the contact thermal conductance, thermal conductivities of the different materials, and the total thermal path. This paper presents a model design analysis methodology using numerical models to evaluate and identify design parameters for optimizing thermal management in drilling tools and highlights the benefits of performing such analysis for developing designs with a high degree of reliability. Novel/Additive Information: The harsh operating environments of the drilling tools and the effects of a tool malfunction require an optimized thermal management strategy to ensure operational reliability. This paper demonstrates the significance of developing a thorough understanding of a drilling tool design with respect to efficient thermal management. This work assesses the major thermal transport bottlenecks in drilling tools and provides a baseline framework for design methods for developing and implementing optimized thermal management solutions.
Drilling Dynamics
IADC/SPE 178852
Advanced BHA/ROP Modeling Including Neural Network Analysis Of Drilling Performance Data. G. Evangelatos, D.E. Mouton, BP America; M.L. Payne, BP
Objectives/Scope: Operators and drilling service and equipment providers collect, record and store massive amounts of data pertaining to the performance of bits, bottomhole assemblies (BHAs) and bit-mud motor combinations. In the recent years, a significant volume of research on BHA vibrations in conjunction with the continuous improvements in the performance and durability of polycrystalline diamond cutter bits (PDC) using fluid mechanics simulations has increased drilling efficiency, typically measured via rate of penetration (ROP), and reduced downhole wear related problems. Even though several analyses and modelling have been performed by the industry, most of the BHAs and especially bit and mud motor combinations are heuristically chosen and tried. As a result, most optimization efforts are driven through the use of the laborious and costly ‘trial and error approach’, where several bit-motor combination options are tried and the best performing ones are chosen for future use based on past experience. Methods, Procedures, Process: In this paper, the differential equations describing the motion, dynamics and impact of the BHA with the wellbore are solved. Secondly, the dynamics of this motion are coupled with a neural network model that is calibrated on previous bit runs. It is then shown that this approach renders significant improvements in predicting the performance of different bit-motor combinations and provides a reasonable estimation of the ROP without having to actually run those combinations and re-calibrate the model. The neural network is used to identify and calibrate a model of the bit-rock interaction, essentially de-coupling the effects of the BHA from how each bit drills the formation. Several parameters affecting the drilling process are used as input and help uniquely identify the bit-rock interaction for a range of drilling parameters. Results, Observations, Conclusions: This approach allows for a reasonable extrapolation of the bit’s behavior on a different BHA for different drilling parameters. The ROP vs depth vs drilling parameters are taken as time histories from field runs of different BHA and bit-motor combinations and analyzed using an artificial neural network model. The calibrated model derives heuristically the governing equations of the process involving all salient variables and can with reasonable effect predict and/or extrapolate ROP based on the input parameters. This model is enhanced by the partial knowledge of the process due to the BHA/drill string characteristics and numerical simulations. In this way, the accuracy and efficiency of planned drilling optimization are increased by addressing a number of the contributing process factors where the mechanics are known and hence avoiding, or at least minimizing, the ‘black box’ modeling approach. Novel/Additive Information: Several example applications are presented and show reasonable performance extrapolations versus actual field measurements from drilling onshore wells in the Wyoming Almond and Erickson formations.
IADC/SPE 178848
Successful Design and Operational Practices to Mitigate Common Bit Damage Mechanisms in Hard Laminated Formations. C.B. Mann, F.E. Dupriest, S.F. Noynaert, Texas A&M University
Objectives/Scope: An extensive data collection, training, and field trial program has been implemented to develop practices to mitigate the most common form of bit damage in hard laminated formations. Analysis improved understanding of the physical phenomena causing the damage and a variety of practices and redesign have resulted in reduced levels of bit dysfunction, increased life and increased drill rate. Methods, Procedures, Process: In hard laminated formations bit life is often limited by severe damage occuring in only the two outside cutter rows. In 2014, the operator began a performance improvement program in the Greater Green River Basin, which included investigating the physical process through which bits were being damaged. High frequency downhole vibrations data was recorded on multiple wells in both the string and at the bit. Analysis showed as the bit drilled the laminated interfaces, high levels of stickslip and synchronous torsional oscillation(STO) occurred. Negative bit rotation was observed during the stick phase, while elevated and synchronous lateral and tangential bit accelerations were observed during STO within the slip phase. The lateral acceleration magnitude during STO was unexpected. This combination of bit vibrations appears to be responsible for the unique location and mode of damage on the PDC cutter face and blade. Bit forensics confirmed backward rotation was pulling the edges of the cutters from the studs, while the damage location on the shoulder and lateral beach marks are consistent with high lateral impact from whirl. Results, Observations, Conclusions: The conventional view of whirl and stickslip is they don’t have high magnitudes simultaneously, so mitigations are typically applied to address either one or the other. In this case, stickslip is the root issue, and the high level of whirl is a product of very high accelerations of the drillstring mass combined with low depth-of-cut in hard streaks which reduces lateral stability of the bit. Field trials were conducted with design changes attempting to address both, including RPM step tests to determine non-resonant rotational speeds, WOB step tests to identify the onset of full-stick, bits designed with depth-of-cut control to reduce torsional oscillation, roller reamers to ensure stabilizer drag wasn’t contributing to stickslip, and extension of bit gauge length to improve lateral stability of the bit. Novel/Additive Information: Direct measurement, using high frequency downhole data, showed it possible to achieve moderate reduction in bit dysfunction. However, the very low torsional stiffness of the four inch drillstring severely limited the ability to apply additional WOB, without which significant gains in ROP cannot be achieved. This work may have implications for operations in other unconventional plays, such as the Marcellus, Utica, Niobrara, Permian Basin, Haynesville, and Granite Wash, where laminated formations, small hole sizes, and small diameter drillpipe are common.
IADC/SPE 178872
Along String Dynamics Measurements Reveal Isolated Potentially Damaging Upper String Vibration Environments. N.G. Cardy, F. Hjortland, S.J. Wilde, NOV Wellbore Technologies; N.B. Muecke, A.S. Wroth, Vermilion Energy
Objectives/Scope: While dynamics studies of drilling bottomhole assemblies (BHAs) have been common since the introduction of vibration measurement subs, little attention has been given to the dynamic environment in the upper drill string. By using distributed recorded mode dynamic subs both in the BHA and higher in the drill string, it has been possible to identify dynamic dysfunctions in the drill string that are not evident from BHA based sensors. Methods, Procedures, Process: This paper examines offshore wells from the North West Shelf, Australia and Norway which exhibit these potentially damaging vibrations. Data was collected from the down hole measurement tools and merged with surface data to allow the investigation of the BHA and drill string dynamic environments. In addition, high speed data bursts were investigated to understand the finer details of the dynamics. Modelling of the BHA and string to predict the critical vibration modes, resonances and contact forces was also carried out. Results, Observations, Conclusions: The analysis of the wells showed that while the bottom hole assemblies displayed very little torsional or lateral vibration, the upper drill string components were exposed to high energy lateral vibrations. The high energy lateral vibration environments were typically either bound by the rig drive system and contact forces between the drill string and the cased hole or between localized high contact forces in the upper sections of the well. Contact forces can isolate the drill string into distinct dynamic environments, potentially creating high energy destructive events in one section while relatively normal conditions are maintained in the other sections. These isolated drill string dynamic dysfunctions can potentially lead to accelerated drill pipe or casing wear with no obvious cause. Novel/Additive Information: This paper shows how using distributed dynamics sensors throughout the BHA and drill string enables a detailed view of the drilling dynamics in the upper drill string, which previously has only been discussed theoretically. The study also highlights the potential risk for accelerated wear to both drill pipe and casing.
IADC/SPE 178773
Vibration Monitoring and Mitigation – An integrated measurement system. J.A. Greenwood, Halliburton
Objectives/Scope: Dynamic dysfunctions of the drillstring are extremely complex to model, and it is difficult to produce timely results to keep up with the continually changing conditions during drilling operations. This paper describes an integrated measurement system that mitigates the effects of damaging downhole vibration and allows the driller to instantaneously respond and evaluate the effectiveness of corrective actions. Methods, Procedures, Process: Failure to measure all of the correct parameters will leave the driller blind to the existence of damaging vibration and lead to sub-optimal performance or equipment and drillstring failures. The integrated system of downhole and surface measurements combines a significant amount of surface, downhole, and formation information to help the driller correctly identify the vibration mechanism and determine the appropriate response. The system measures the movement of the bottom-hole assembly, the levels of energy generated during episodes of vibration, and the energy going into the system. Results, Observations, Conclusions: The capability to present the results of analysis to the driller in a clear and concise manner and produce recommendations for the correct mitigation strategy is a powerful tool for mitigating downhole vibration. Monitoring surface weight on bit, torque, rpm and standpipe pressure and a performing frequency analysis helps identify vibration signatures for stick-slip and bit bounce. Mechanical specific energy (MSE) calculations determine drilling efficiency. Downhole accelerometer, gyroscope, magnetometer, bending, tension and torsion measurements used alongside formation evaluation data identify bit bounce, bit whirl, BHA whirl both forward and backward, torsional resonance, bit chatter, modal coupling and lateral shocks. A three tier system of warning brings attention to the presence of vibration, supplies the mechanism and corrective actions, and provides detailed analytical information to the expert. Tracking environmental exposure of downhole equipment allows the driller to determine if the operating limits of weight on bit, rotary speed, temperature, and dogleg severity as well as axial, lateral, and torsional vibration are being approached or exceeded. Novel/Additive Information: This smart system reduces the reliance on expert analysis to identify the correct actions to mitigate the problem leading to an increased speed of response. Combining the ability to identify all vibration mechanisms with the tracking of the environmental exposure and the representation of this information in an easily understood manner provides a powerful tool for the control of drilling operations.
IADC/SPE 178874
Prediction and Mitigation of Torsional Vibrations in Drilling Systems. A. Hohl, Baker Hughes Solutions; M. Tergeist, IDS, University of Braunschweig; H. Oueslati, Baker Hughes; C. Herbig, Baker Hughes Solutions; M. Ichaoui, Baker Hughes; G. Ostermeyer, IDS, University of Braunschweig; H. Reckmann, Baker Hughes
Objectives/Scope: Drilling systems are subject to torsional vibrations that are excited by bit-rock or by drillstring formation interaction forces. These torsional oscillations can be distinguished by mode shape and frequency. Well-known stick/slip oscillations are characterized by low frequencies (usually below 1Hz) and affect the entire drillstring. High-frequency torsional oscillations (HFTO), in contrast, name the excitation of a high-order natural mode (reaching 400 Hz). In case of HFTO, the bottomhole assembly (BHA) is exposed to high dynamics loads. Torsional vibrations compromise drilling efficiency and tool reliability. To address these challenges, we are proposing a method for automated BHA optimization based on mechanical drillstring models. Methods, Procedures, Process: Through extensive analysis of high-frequency (1400 Hz sampling frequency) data from field measurements, an analytical, verified, and easy to use criterion for the prediction of the excited torsional mode and the corresponding loads was derived. The criterion is based on the comparison of the resulting excitation from cutting forces at the bit and the damping of a torsional mode. The criterion is unique for every torsional mode and can be used to rank the susceptibility of torsional modes for HFTO or stick/slip. A software application (Torsional Oscillation Advisor, TOA) has been developed for user-friendly interpretation of the underlying analytical method towards practical issues. Results, Observations, Conclusions: The use of the TOA provides valuable input for drilling optimization: For stick/slip, the influence of various drill pipe sizes and the length of the drill pipe section on torsional stick/slip mode are analyzed. It is shown that the limit for stable drilling in case of bit induced stick/slip can be extended by stiffer drill pipes whereas the influence of the length of the drill pipe section is marginal. The material of the bit and its mass distribution is shown to have a considerable influence on the excitation of HFTO. The software also enables automated BHA optimization in both new product development and tool operation phases. A numerical optimization approach is used to minimize the susceptibility of the bottom-hole assembly for stick/slip and HFTO for given constraints of the geometry and material parameters. Herein, a significant increase of stable drilling conditions regarding weight on bit and bit rotational speed with respect to torsional oscillations is achieved. Even small changes in the drilling system design have a visible impact on the torsional stability. Novel/Additive Information: The ability to identify and predict modes of stick/slip and HFTO that are most likely to be excited while drilling, an extension of the stable drilling zone and the estimation of loads before field deployment will result in higher drilling efficiency, more reliable tools and lower non-productive time.
IADC/SPE 178817
A New Damping Model for Nonlinear Drill String Dynamics: Understanding the Effects of Rotation, Eccentricity, and Confined Fluid Flow and Their Impact on Unconventional Drill String Design. J. Wilson, Scientific Drilling International, Texas A&M University; S.F. Noynaert, Texas A&M University
Objectives/Scope: Since the pioneering work of Bailey and Finnie in 1960, drillstring dynamics continues to be an active area of research within the industry. While much effort is put into developing accurate descriptions of the complexities associated with the downhole environment, proper modeling of the various damping mechanisms acting on the drillstring remains underdeveloped. A typical approach to modeling the damping downhole consists of calibrating a generalized, or proportional, damping model based on measurements of the actual system response. This technique can be fairly useful when done properly but does not actually quantify the effects of various environmental or operational parameters, such as fluid characteristics or string rotation, on the overall behavior of the drillstring. Methods, Procedures, Process: This study presents a nonlinear semi-analytical fluid damping model specifically developed to account for the various downhole characteristics that contribute to energy dissipation such as pipe eccentricity, lateral velocity and acceleration, rotation speed, fluid rheology, and flow rate. This newly established fluid damping model is combined into an already proven drillstring model which was developed to embody the fully coupled flexibility of the drillstring, arbitrary wellbore curvature, frictional contact, and complex tool geometry. Through this implementation, the paper analyzes the nonlinear behavior of drillstrings in modern unconventional wellbores. Specific attention is given to studying the damping effects on the dynamic response of the drillstring and BHA during rotation with a Rotary Steerable System (RSS) as well as while slide drilling with a steerable mud motor and Vibration Inducing Devices (VIDs). Results, Observations, Conclusions: The results shown through this investigation help to quantify the dynamics associated with modern drilling operations. The effects of fluid properties, flow rate, and rotation speed on the nonlinear behavior of the drillstring is quantified through numerical studies. Advanced visualizations of the time domain simulations also reveal key characteristics to understanding what is taking place downhole. The possibility of using advanced models, such as this one, with respect to drilling automation is also discussed. Novel/Additive Information: By combining the fluid damping presented in this paper with a prior drillstring dynamics model, a robust dynamic drillstring simulator has been developed with the potential for significant impact on the drilling industry. Using a physics-based approach while attempting to make the model one which is realistic and efficient, the authors feel that the resulting work is a comprehensive, and yet practical, way to analyze the drillstring and BHA. The model presented cannot only be applied to unconventional and ERD operations but to any application where drillstring and BHA dynamics are performance-limiting issues. In addition, the model was developed with drilling automation in mind as an understanding of drillstring dynamics is critical to trajectory control, ROP optimization and bit-damaging vibration mitigation efforts.
IADC/SPE 178849
Mitigating Vibration Induced Drillstring Failures Using Data Analytics: Workflow and Case Study. A. Mirani, University of Houston; R. Samuel, Landmark Graphics Corporation
Objectives/Scope: Failures associated with drillstring vibration continue to occur despite the use of risk quantification techniques based on vibration intensities and root mean square (RMS) accelerations. This paper introduces the concept of modified vibration stability plot as a practical tool to minimize and predict vibration. Further, it integrates it with data analytics and statistical modeling to forward predict drillstring failures caused by torsional and lateral vibration. Methods, Procedures, Process: The modified stability plot provide optimum operating parameters (WOB, rev/min, and ROP) to minimize vibration. However, actual real-time drilling parameters are not always optimum. Hence, deviation of real-time parameters from the optimum values are used to calculate “deviation vectors” using statistical tools. These are then used to generate operating stability clusters to detect outliers in the drilling data that signify potential vibration events. Safe operating limits and operating times have been proposed by integrating the clustering technique with vibration risk index and cumulative vibration intensity plots to mitigate failures. Results, Observations, Conclusions: The workflow has been applied to cases where severe and moderate vibration were encountered downhole and at the surface, respectively. Extensive simulations have been performed to compare the data from downhole vibration sensors. Results show that the workflow closely predicts the occurrence of sustained vibrations before an actual downhole string failure event. Prolonged operations outside the stability circle can cause failures, depending on the fatigue strength of the material. The occurrence of outliers outside the stability clusters are calibrated with actual drillstring failures to correlate cumulative vibration intensity plots with the time duration of a vibration event. This helps in defining a vibration risk index that can trigger decisions to stop drilling or change operating parameters before a failure occurs. The workflow also manages to simultaneously predict which type of vibration are dominant in the system and causing failures. The study concludes by providing guidelines to integrate the vibration stability chart with data analytics and explicates the significance of a statistics based risk index to initiate real-time procedures to prevent drillstring integrity failure. Novel/Additive Information: The workflow proposed, and validated with case histories, strives toward cost-effectiveness and increased productivity. This paper goes a step forward to implement data driven techniques for risk quantification. The results and the methodology for determining risk index and operational limits is robust, and can be applied as a starting point for other string configurations in similar downhole environments.
IADC/SPE 178819
Improvements in the Root Cause Analysis of Drillstring Vibration. J.A. Greenwood, Halliburton
Objectives/Scope: Drillstring vibration is a leading cause of downhole tool failure and premature wear of downhole equipment. The main challenges faced during drilling is performing rapid analysis to determine the root cause of the vibration, clear identification of the active mechanism, and implementation of the appropriate corrective action quickly enough to prevent failure. This paper describes a comprehensive methodology created to identify root causes, all vibration mechanisms, and methods to reduce or eliminating drillstring vibration on a range of different operations. Methods, Procedures, Process: A BHA and drillstring has six degrees of freedom and three dominant modes of vibration, axial, lateral and torsional. This movement is used to describe the different vibration mechanisms, such as stick-slip, bit bounce, bit whirl, BHA whirl both forward and backward, torsional resonance, bit chatter, modal coupling, and lateral shocks. Data is collected from downhole and surface sensors and cutting analysis that measures modes and magnitudes of vibration, tension, compression and bending within the (BHA), drilling parameters, fluid properties, and lithology and rock properties. The methodology uses some or all of these factors to identify the root cause and is enhanced by the ability to summarize the distribution of vibration levels across a run, histogram analysis, and the ability to filter across time or depth ranges and further filter based on rig activity codes. Results, Observations, Conclusions: There are a combination of factors that generate or influence drillstring vibration, the energy inputs of weight on bit (WOB) and torque (TRQ), bit type, BHA design and stabilization, lithology type, geological structures, bit- lithology interaction, borehole size and BHA size, hole trajectory, backreaming or rotating off bottom, hole enlargement, the rig electrical system, and on offshore floating vessels rig heave. The methodology is able to identify and isolate which factors are the root cause of a specific mechanism by incorporating time based analysis with depth based logs and plotting a to-scale BHA to identify correlations of the bit position, stabilizer, and other BHA components to formation types and boundaries, hole size changes and casing positions. The methodology enables significantly faster analysis of data and a more rapid assessment of the root cause of the vibration. Novel/Additive Information: A comprehensive methodology is applied to confirm the root cause and specific benefits delivered by identifying and then reducing or eliminating drillstring vibration on a range of different operations.
IADC/SPE 178834
Selecting Optimum Drilling Parameters by Coupling Vibration and Drilling Efficiency Models. M.F. Al Dushaishi, R. Nygaard, Missouri University of Science & Tech; A. Saasen, Det Norske Oljeselskap ASA; M. Andersen, NOV Downhole Tools Division; C. Jeffery, National Oilwell Varco
Objectives/Scope: Drilling related problems such as drill stem vibration is one of the important causes of premature failure of drill stem components and drilling inefficiency. In severe cases, drill stem vibration will lead to wellbore instability that will result in an increase in the operation cost. High vibrations level has been linked to bottomhole assembly (BHA) configurations, bit design, selection of operating parameters, and frequent lithology changes. To avoid severe vibration, different drill stem vibration models are used to predict and avoid resonance regions by selecting operating parameters such as weight on bit (WOB), RPM and BHA components. Drilling efficiency is evaluated using either mechanical specific energy model or inverted rate of penetration (ROP) model. This paper addressed the impact of drill stem vibrations on the overall drilling performance. The object of this study is to couple drilling stem vibration model with a real time analysis tool using the inverted ROP model to improve drilling operations. Methods, Procedures, Process: Drill stem vibration model was created using nonlinear finite strain theory including coupled axial, torsional and lateral vibration modes. The model takes into account initial stresses created due to static WOB, shear forces, gyroscopic effect due to the drill stem rotation and the influence of drilling fluid and circulating dynamic pressures. The vibration model was than coupled with an inverted ROP model to obtain the highest drilling rate that could be achieved to complete a specific section. The vibration model calculates the critical speeds for a given BHA and target depths for a predicted lithology. The model is than simulated for different operating parameters that avoids severe vibration regions. The simulation data is than used to obtained ROP and bit wear for different lithology that’s expected to drill through. Based on the simulations obtained from the model, operating parameters are adjusted to optimize ROP to reach the target depth with the designed bit wear. Results, Observations, Conclusions: The use of coupled vibration and an inverted ROP model to optimize drilling operation by analyzing drilling variables such as WOB, rotary speed, BHA, bit design, and bit wear with low vibration and maximum cumulative ROP rather than instantaneous ROP is addressed. The model was verified by analyzing field data collected from a well located in the North Sea, the measured data consisted of downhole vibrations and downhole operating parameters such as WOB and RPM. The model correlated well with the measured field data. Novel/Additive Information: The combined proposed model has not previously addressed. The model links drill stem vibration to drilling performance directly to improve drilling performance by optimizing ROP from vibration point of view, BHA configuration, and drill bit wear to reach a certain target depth with fewer amounts of trips.
Thursday, 3 March
Well Placement I
IADC/SPE 178843
OWSG Standard Survey Tool Error Model Set for Improved Quality and Implementation in Directional Survey Management. S. Grindrod, Copsegrove Developments; P.J. Clark, Chevron Energy Technology Company; S.V. Pham, ConocoPhillips; J.D. Lightfoot, Occidental Development Co; N. Bergstrom, Devon Energy Corporation; L.S. Grant, Noble Energy
Objectives/Scope: Understanding wellbore position and the associated uncertainty is fundamental to all drilling operations and reservoir management. Without consistency in predicting to known uncertainties, activities involving positional uncertainty, such as risk mitigations for collision avoidance, cannot be performed reliably with known confidence. For the first time, industry has a common controlled set of uncertainty models thus allowing for transparency in error estimation. Reservoir targeting and subsurface hazard avoidance can be compromised resulting in unrealized stranded reserves and/or intersection of faulted, undesirable formation. Overly optimistic estimations can result in wellbore collisions where the risk of collision is assumed to be very low or can result in a missed well intersection during relief well first ranging point operation. Conversely, overly conservative estimations can result in excessive targeting constraints or directional control requirements. Methods, Procedures, Process: An analysis of industry survey of error codes being utilized across companies was performed, both vast inconsistencies and significant gaps were realized. A case for action was determined and a collaborative work group was formed under the Operator Wellbore Survey Group (OWSG). OWSG is a subcommittee of the SPE Wellbore Positioning Technical Section (WPTS), also known as Industry Steering Committee on Wellbore Surveying Accuracy (ISCWSA). It was determined that many of the error codes being utilized in industry were based on survey tool error models established in SPE 67616 and SPE 90408, but there were uncontrolled changes, miss matched versions, and alterations in error assumptions (that were not vetted) being unknowingly utilized. Inspection revealed that the error models, although loosely based on ISCWSA, were varied across both service and operator companies and in some cases were varied internal to individual companies. Results, Observations, Conclusions: The collaborative work group developed a Standard Survey Tool Error Model Set based on the SPE 67616 and SPE 90408 publications, the current work of the ISCWSA error model subcommittee and with contributions from industry’s leading subject matter experts. The result of the work is a series of 5 sets of OWSG Survey Tool Error Models. The sets have a Model Selection guide with a Standardized naming structure.The Standard Survey Tool Error Model Set has been released it into the public domain to improve Survey Management Quality and has been adopted by numerous companies (both services and operators). The OWSG error model set facilitate easy implementation in all common directional well planning software platforms; hence reducing risk of incorrect models leading to poor understanding of wellbore position and improving consistency of error estimation. Novel/Additive Information: The Standard Survey Model set has been compiled with contributions from industry’s leading subject matter experts. The Error Model series were publicly released in June, 2015.
IADC/SPE 178796
Advanced Trajectory Computational Model Improves Calculated Borehole Positioning and Tortuosity. M.F. Abughaban, SPE, Colorado School of Mines; B. Bialecki, Colorado School of Mines; A.W. Eustes, SPE, Colorado School of Mines; J.P. de Wardt, SPE, DE WARDT & CO.; S.V. Mullin, SPE, Gyrodata
Objectives/Scope: Wellbore tortuosity is a critical element in managing torque and drag while drilling horizontal wells. Current three-dimensional well trajectory modeling represented by the minimum curvature computation method tends to mathematically smooth the wellbore path between survey stations. This creates an artificially low tortuosity causing underestimation of torque and drag magnitude. It can also miscalculate the actual true vertical depth and northing and easting coordinates, which impacts subsurface earth models. This study was conducted to develop an advanced trajectory computation model using spline curves to mitigate these limitations. Methods, Procedures, Process: The developed model procedure in this study takes two major steps to achieve its goal: (1) Developing a robust three-dimensional trajectory model and (2) Applying Slide Sheet Analysis. The trajectory gives realistic results and accurately calculate the spatial course of the wellpath. The principal method proposed using an Advanced Spline-Curve (ASC) is a step toward more accurate presentation of wellbore trajectories, compared to other methods using minimum curvature or tangential calculations. This curve, parameterized by the arc-length and determined using interpolation conditions for its tangent vector, has continuous derivatives up to the second order. It is relatively simple and flexible to calculate complex, three-dimensional wellbore trajectories. Applying Slide Sheet Analysis is a technique that provides an estimate of the true dogleg severity performance of a BHA by interpolating surveys at all salient points. After completing new surveys for all the events in the run, the data can be reprocessed using ASC. This technique gives a better modeling of tortuosity and more accurately represents the wellbore position. Results, Observations, Conclusions: This paper presents a new model with high accuracy in predicting wellbore trajectory and tortuosity. Various applications of ASC and the results have been validated using two approaches: (1) an academic wellbore example of a known trajectory path, and (2) the use of continuous rate gyroscopic survey data (inclination and azimuth) collected at high spatial density at one survey per foot as opposed to the typical 90 to 100 ft between surveys. The calculated trajectories using ASC showed significantly better accuracy as compared to all previous models. A higher degree of accuracy was observed using slide sheet analysis. These findings allow better wellbore positioning while drilling highly deviated wells, helping to evaluate drilling equipment and procedures for extended horizontal wells. Novel/Additive Information: A continuous rate gyroscopic survey recorded at high spatial density provides the highest level of wellbore positioning and tortuosity accuracy; however this data is usually obtained after the wellbore had been drilled and thus an advanced mathematical method, such as ASC, brings value while drilling the well. ASC while drilling will improve the knowledge of wellbore tortuosity and the calculated position accuracy for correct landing in the reservoir.
IADC/SPE 178826
New Instrument Performance Models for Combined Wellbore Surveys Facilitate Optimisation of Survey Program. A.G. Ledroz, J.L. Weston, J. Bang, Gyrodata
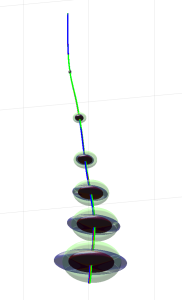
Objectives/Scope: In order to determine confidently the path of a wellbore, established practice involves the collection of multiple survey data using the various methods that are available to the industry, such as measurement while drilling methods, using either magnetic or gyroscopic measurements, or surveys taken after a section of the wellbore has been completed, normally using gyro tools. The survey deemed to be of the highest precision, based on published survey system error models, is commonly selected to be the “definitive survey” for that section of the well and all other data is discarded. However, by combining multiple data sets through the use of survey averaging techniques, it is possible to obtain a more accurate estimate of wellbore position. Methods, Procedures, Process: Having generated a “combined survey” by such an averaging method, i.e. a survey generated by combining two or more surveys that may be of the same or different type, it is then required to quantify the accuracy of that survey. This may be expressed in the usual manner as a sequence of error ellipsoids at intervals along the path of the well. At present, however, this can only be done by rigorous calculations analogous to the survey averaging itself. This is a complex analysis, which is one important reason why survey averaging has not been generally implemented and adopted as a standard analysis practice. Results, Observations, Conclusions: Error models for individual survey tools are usually specified in terms of Instrument Performance Model (IPM) files in accordance with methods and procedures derived through the work of the SPE Well Positioning Technical Section. The IPM files, along with wellbore trajectory data, form the inputs to standard error model software packages through which survey uncertainty is calculated to a specified level of confidence. This paper demonstrates how new IPM files can be generated for combined surveys. The error analysis resulting from the new IPM file is shown to be consistent with the results obtained through the rigorous mathematical analysis of the individual surveys. Novel/Additive Information: The introduction of new IPM files offers an easy and efficient method for operators to utilize all available survey information in a consistent manner. This may help to optimize the surveying program, with implications for both positional uncertainty assessment and safety aspects. Furthermore, the improvement in the positional data as well as the reduced uncertainty that can be achieved by combining surveys is a great advantage when considering highly congested fields and it could turn unfeasible projects involving small targets and very long extended reach wells into achievable ones.
Advanced Fluids Research
IADC/SPE 178877
Automated Drilling Fluid Analysis using Advanced Particle Size Analyzers. E. van Oort, The University of Texas At Austin; B. Hoxha, The University of Texas at Austin; L. Yang, A.H. Hale, The University of Texas at Austin
Objectives/Scope: The era of drilling fluid property analysis carried out manually by a mud engineer is rapidly disappearing. Novel measurement tools and techniques are now making it possible to carry out sophisticated drilling fluid analyses using largely automated equipment. This paper anticipates and highlights the important role that automated particle size analyzers will play in future drilling operations. Methods, Procedures, Process: A comprehensive experimental study was carried out using a new generation of particle size analyzers (PSA) to investigate their utility for automated drilling fluid analysis. The pieces of equipment that were evaluated were the Canty Microflow LPA (which uses imaging microscopy), the Mettler Toledo G400 ParticleTrack (which uses FBRM laser diffraction) and the Malvern Zetasizer (which uses Dynamic Light Scattering). These instruments were used in conjunction with in-house flow loops and shearing facilities to test (1) degradation of the particle size distribution (PSD) of lost circulation and wellbore strengthening materials under the influence of shear, (2) the behavior of the emulsion droplet size distribution (DSD) of invert emulsion mud systems (oil-based and synthetic-based muds) under a variety of influences including shear and temperature, mud contamination, mud treatments, etc. Results, Observations, Conclusions: Verifying and maintaining the PSD of lost circulation/wellbore strengthening materials is of crucial importance to prevent severe mud loss events that still continue to plague the industry at a trouble cost of many billions of dollars per annum. Our PSA analyses show that the PSD’s of such materials, particularly those of medium to coarser sizes, is far from stable and degrades over time, primarily due to the influence of shear. It will be shown that automated, inline PSA equipment allows for the degradation to be monitored and managed in real-time to maintain optimum drilling performance. In addition, such equipment can be used to monitor and optimize the DSD of an invert system, which is an extremely quantity that influences many important mud performance characteristics such as rheology, emulsion stability, fluid loss behavior, osmotic membrane efficiency, etc. Novel/Additive Information: The work involves a comparative study of novel PSA’s, ranking them by accuracy, ease of use, automation potential, real-time monitoring capability etc. It presents novel, non-intuitive data on the degradation of lost circulation/wellbore strengthening materials and practical ways to deal with this degradation. It also presents, for the first time, a comprehensive study into the behavior of invert mud droplet size and its impact on oil-/synthetic-based mud performance, with associated guidelines on how to optimize this performance.
IADC/SPE 178832
Modeling Real-Time Sag in the Wellbore. S.D. Kulkarni, D.E. Jamison, J. Gollapalli, Halliburton
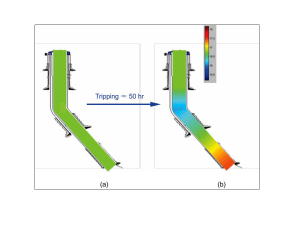
Objectives/Scope: Weight material sag occurs during drilling operations when drilling fluids remain idle in the wellbore for time periods ranging from hours to several days at static or low-shear conditions. The paper presents a novel method of predicting real-time sag behavior in the wellbore. The method also accurately predicts the fluid mud weight collected at the surface as it is circulated out after a sag event, providing a significant advancement in drilling fluids engineering. Methods, Procedures, Process: Weight material sag is broadly viewed as the settling of barite particles in drilling fluids (primarily oil-based) under various mechanisms. Fluid composition (barite size/concentration and oil/water ratio) and fluid properties (such as rheology) influence the barite settling rate. The well geometry (such as inclination and diameter) also affects sag behavior. In addition, well operating conditions (such as temperature, pressure, and time for which fluid is uncirculated) also influence sag severity. A comprehensive computational approach was developed to model the sag behavior in wellbores using fluids composition/properties and wellbore geometry/conditions information. Results, Observations, Conclusions: The wellbore sag model predicts real-time information about dynamic fluid composition along the wellbore depth as affected by sag, when the fluid in the well is under idle conditions (static or low shear). Specifically, for a wellbore section of a given inclination, the model provides quantitative density/rheology estimates of the barite-depleted zone at the top of the section and the barite-accumulated zone at the bottom. As the sag-affected fluid is circulated out after an idle period, the model also predicts the varied mud weight of the fluid collected at the surface and the corresponding transient bottomhole ECD. The wellbore sag model predictions, especially the variation in the mud weight of the fluid collected at the surface after the sag event, were tested on several wells and fluid systems. The model provided good correlations between measured and predicted fluid density, typically less than 0.1 lb/gal. The model accurately demonstrates how certain fluids show good sag resistance in some wells, yet fail in some complex wells. The model also shows excellent sag resistance of certain specialized fluids in complex wells, which is in agreement with the field observation. Novel/Additive Information: A method to accurately determine real-time sag in the field has been a long-standing need. The successfully validated wellbore sag model, which captures the combined effect of fluids composition/properties and wellbore geometry/conditions, could serve as a useful tool for mud engineers to evaluate the sag behavior. It could also enable fast decision-making at the rig site to optimize fluid formulations and operating conditions for sag management.
IADC/SPE 178804
Non-Aqueous, Salt-Free Drilling Fluid Delivers Excellent Drilling Performance with a Smaller Environmental Footprint. J. Walker, J.T. Hovan, Halliburton; T. Mander, Formerly of Halliburton; K.J. Burrows, Halliburton
Objectives/Scope: Disposal of drill cuttings from non-aqueous drilling fluids (NAF) can be a significant expense and logistical issue for the operator of a drilling rig. NAFs typically contain high levels of salts, commonly calcium chloride or sodium chloride, in the internal phase of the emulsion. These salts are highly beneficial for wellbore stabilization performance but pose issues for disposal of drill cuttings because the salts do not biodegrade and can accumulate in high concentrations in soil. Methods, Procedures, Process: A salt-free NAF has been developed and field validated in the Western Canadian Sedimentary Basin in Alberta, Canada. The system uses a biodegradable organic to provide an internal phase with equivalent water activity to traditional salt-containing systems. This results in a fluid system with the performance and benefits of a conventional NAF while potentially allowing for greater cuttings disposal options. Depending on local regulations, the system has the potential to reduce environmental and long-term liability concerns by being able to land-farm drilled cuttings without hindering plant growth. Results, Observations, Conclusions: Three wells on a seven-well pad were drilled with the salt-free NAF; the other four with a conventional invert emulsion fluid (IEF). The salt-free fluid performed the same as or better than a conventional fluid while drilling. Observed improvements over conventional NAFs included less required fluid maintenance, greater inhibition of the formation, and less fluid losses in part due to reduced oil on cuttings (OOC). A bioremediation study was conducted to analyze the cuttings for total petroleum hydrocarbons (TPH), electrical conductivity, and plant growth. Cuttings were sampled from each type of well and delivered to the lab for testing and analysis. Laboratory testing showed that when mixed with top soil, the salt-free cuttings allowed for viable plant growth. In comparison, the conventional cuttings did not allow plant growth. The paper will discuss in detail the field trial and bioremediation study of the salt-free NAF. Novel/Additive Information: A salt-free NAF has been developed in the lab and successfully validated in the field. The salt-free system showed equivalent or better performance to conventional NAFs used on other wells on the same pad. Additionally, cuttings from the salt-free system showed superior plant growth when compared to conventional, salt-containing systems. This system is expected to offer expanded options for cuttings disposal and ultimately reduce the cost and liability associated with using NAFs in many areas.
IADC/SPE 178860
Gas Influx in Oil-Based Drilling Fluids and its Effect on Flow Properties at HPHT Conditions. A. Torsvik, J. Skogestad, H. Linga, SINTEF Petroleum Research
Objectives/Scope: Oil field exploration in extreme areas represents additional requirements to drilling fluid performance and hydraulic models for well control. In general, there is little knowledge about the drilling fluid properties at HPHT conditions, and kick models are based on extrapolations. To verify the validity of these extrapolations, increased knowledge about drilling fluid behavior under HPHT conditions is required. In this work we have experimentally determined the effect of gas absorption on saturation pressure, density and viscosity at temperatures up to 392°F and 14500 psi. Results have been used to validate computational predictions. Methods, Procedures, Process: We have developed an experimental setup for studying the effects of natural gas dissolved in petroleum fluids under conditions appropriate for drilling operations. The equipment comprises a sample cylinder in which drilling fluid and gas can be mixed at exact mass fractions, and the saturation pressure can be determined at desired temperatures. The gas-loaded drilling fluid is transferred to a rheometer with a 14500 psi pressure cell and to a HP densitometer for viscosity and density measurements, respectively. The software PVTsim was used to compare the prediction performance of a commercial software to the experimentally determined fluid densities and phase envelopes. Results, Observations, Conclusions: In this study we provide accurate measurements of different degrees of methane solubility in two oil-based drilling fluids (OBDF) with similar composition except for the type of base oil. One is based on a refined deep-water oil and the other is based on a linear paraffin oil. For various CH4/OBDF combinations, density and viscosity are measured at pressures and temperatures ranging from standard conditions to HPHT. The OBDFs have similar flow behavior, but the one with linear paraffin base oil has a stronger gel structure and a stronger shear-thinning effect. This fluid is also able to absorb more gas at lower pressure than the fluid with a base oil especially designed for deep water conditions. We here show how the experimental results form an important basis for tuning the software model to fit thermodynamic properties of gas loaded drilling fluid at HPHT conditions. Novel/Additive Information: Efficient and safe well operations depend on proper knowledge about the behavior of gas influx in petroleum fluids and the impact of relevant temperature and pressure changes in the well. A major weakness in current kick models is the lack of experimentally verified data in the HPHT region. Drilling fluids are commonly analyzed according to international standards, describing atmospheric conditions and only a few selected temperatures. Data from this study will be analyzed and used to validate extrapolations used in computational models. Improved understanding of the two-phase gas-drilling fluid flow in the well allows better prediction of gas absorption and improved operational safety.
IADC/SPE 178774
Size Degradation Studies of Lost Circulation Materials in a Flow Loop. S. Savari, D.L. Whitfill, Halliburton
Objectives/Scope: Recently, there has been significant interest to understand the material properties of lost circulation materials (LCMs), including size degradation studies from mechanical compression tests and from shear flow. These types of tests are currently of particular importance, especially because of increased drilling activity in mature fields that often require LCMs to be used as a background material. The objective of this work is to present the size degradation of LCMs from flow loop tests. Methods, Procedures, Process: A flow loop test was performed to study the size degradation of LCMs, mainly ground marble (GM) and resilient graphitic carbon (RGC). A pre-determined amount of GM and RGC was added to an 80-bbl synthetic-oil-based drilling fluid. The flow loop consisted of 3-in. diameter flow lines. One circulation through this flow loop required approximately 8 min, which is equivalent to one circulation in the actual field application. The fluid with LCM was circulated through the flow loop at a 400-gal/min flow rate. Fluid samples were collected at different stages, and a wet sieve analysis was performed to determine the amount of material in the drilling fluid retained on each sieve. Comparing the amount after the flow with the amount before flow allowed estimations of the LCM size degradation. This provided the size degradation that the LCM would experience as a result of flow through the loop. Another objective was to study the effect of a turbine, which was anticipated to be part of the bottomhole assembly, on the size degradation rate of LCMs. To evaluate this, a turbine was incorporated in the flow loop, and the fluid with LCM was again circulated at a 400-gal/min flow rate. Again, samples were collected at different times, with a wet sieve analysis performed to determine the size degradation of LCMs when flowing through the turbine and the flow loop. Results, Observations, Conclusions: GM was subjected to a 35% size reduction resulting from the flow loop alone, compared to only a 16% size reduction of the RGC. When the turbine was added to the flow loop, GM was almost completely degraded (a total of 75% reduction) to a smaller size after only one circulation through the loop. Concurrently, the RGC experienced only a 20% reduction in size, even after 160 min of flow (20 circulations) through the loop and the turbine. Novel/Additive Information: Size degradation studies of LCMs were conducted for the first time in a flow loop, at a 400-gal/min circulation rate. The results show the importance of using a resilient LCM, such as RGC, as part of a LCM background package when drilling lost circulation problem zones in mature fields.
IADC/SPE 178789
Modeling Real-Time ECD during Transient Pumping and/or Tripping Using Time-Dependent Fluid Properties. S.D. Kulkarni, D.E. Jamison, V. Pereira, A. Porter, Halliburton
Objectives/Scope: Drilling operational parameters, such as pump rate and pipe tripping and drilling fluid characteristics change, which can impact dynamic wellbore fluid pressure (equivalent circulating density [ECD]). It is important that ECD at any instant remain between fracture and pore pressure gradients (drilling window). Modeling ECD for transient wellbore conditions is presented, demonstrating that the model predictions match pressure while drilling (PWD) measurements obtained from several wells. Methods, Procedures, Process: Drilling fluids exhibit time-dependent rheological response, particularly at static or low-shear conditions. The fluids develop gel microstructure attributed to interaction between polymers, colloidal particles, and emulsion droplets. As pumping is initiated or pipe moved, ECD spikes occur because of the developed gel microstructure and the microstructure then breaks down gradually with shearing. Understanding the mechanism of gel formation and breakdown under various shear, temperature and pressure conditions improves accuracy of the ECD modeling for transient fluid characteristics. Results, Observations, Conclusions: Pump rate can accelerate or decelerate during several operations (e.g., during pipe connections). Another operational parameter, tripping speed, can exhibit variation. For example, pipe speed can accelerate from static to the highest speed and then decelerate to static. Furthermore, the fluid can be pumped during tripping operations to help manage wellbore pressure; in addition, such pumping helps speed up tripping, saving rig time. The coupled effect of momentum change during these transient operational parameters in addition to time-dependent fluid properties on ECD response is investigated, exhibiting that improved understanding of transient effects improves ECD modeling accuracy for such conditions. Novel/Additive Information: The developed models for ECD response were validated on several wells. Fluid properties, real-time pump rate, and tripping speed information were used as model inputs, while outputs were compared with PWD data obtained from the wells. With successful validation, these models can now be used for improved design of operational parameters and fluid characteristics for wellbore management.
IADC/SPE 178761
Novel Low Density, Direct Emulsion Drill-In-Fluid System Targeted To Minimize Formation Damage in Mature Field Applications. N. Collins, Schlumberger
Objectives/Scope: A low-density direct emulsion (DE) system has been successfully formulated to minimize formation damage in mature depleted fields. Key objectives for the DE system are to provide all the functions of traditional reservoir drilling fluids (RDF) in terms of efficient cutting suspension and carrying characteristics, effective fluid loss control and friction coefficient, while minimize overbalance on depleted formations. Excessive overbalance on the formation would potentially cause severe losses and could result in formation damage, with negative impacts on the environment, and an increase in overall fluid cost. Novel oil-in-water DE system consists of a dispersion with oil as the internal phase, and water as the external phase. It targets densities with minimal overbalance on formation while providing all the benefits of an emulsion system – enhanced friction reduction, effective fluid-loss control, superior rheology for hole cleaning and ECD reduction, and effective clay inhibition. Numerous attempts of using DE systems in oil field drilling fluids have been made in the past. However, DE systems have never been fully adapted in industry due to difficulties to maintain the emulsion stability and its sensitivity to common contaminants. It is well known that DE systems could be unstable and prone to emulsion breaking, or undesired reversibility (commonly referred as a “flip”). Novel thermodynamically stable DE system has been successfully used to drill a well with no excessive losses or emulsion stability issues. The paper will present a detailed study of the laboratory development of the DE system along with field application data and lessons learned.
MPD/UBD
IADC/SPE 178810
Bridging the gap between MPD and Well Control. T. Pinheiro Da Silva, L. Hollman, G.P. Puerto, P.R. Brand, Blade Energy Partners
Objectives/Scope: A comparison well control bridging document is provided with the intention to demonstrate the required updates specifically on the well control policies Methods, Procedures, Process: The growing use of MPD has proven to enhance drilling operations in narrow margin, HPHT and even conventional operations, but it is also challenging the drilling process, drilling contractors, operators policies, and standards. Conventional drilling practices for connections, flow checks, tripping, and well control have been long understood and standardized across all forms of conventional drilling. With the addition of a MPD system to a drilling operation, inclusive of the recommended practices, it becomes necessary to bridge the gap between conventional policies and standards with those of MPD, merging the two into a formal standard, specific to each project and/or operation. Results, Observations, Conclusions: When a new drilling campaign is initiated the operator typically begins designing a well plan and high level drilling plan by defaulting to their current standards and policies. Once a drilling contractor is selected and service contracts signed, the challenge begins by bridging the drilling contractor’s policies with the operator’s standards. The inclusion of MPD then adds an additional layer of complexity to the established bridging document, by challenging the standard operating procedures, and forcing operators and contractors to create step-outs from their policies. It is often seen as an operational requirement that a MPD well control bridging document supplements the standard drilling contractors and operators bridging document. Instead it should be viewed as a way to enhance the currently acceptable policies and practices. The intent of this paper is to highlight the specific areas where conventional policies are challenged by MPD operations, and attempts to offer guidance implementing and managing this technology. It is also to be used as a tool to raise awareness to ensure operations are carried out in a safe and efficient manner according to the agreed upon policies, procedures, and standards currently in place, as well as, to minimize the potential risk to personnel, environment and equipment. A comparison well control bridging document is also provided with the intention to demonstrate the required updates specifically on the well control policies. Novel/Additive Information: Specifically to the note of well control, the drilling contractor remains responsible for well control and well monitoring at all times. The Driller will continue to monitor the well using standard drilling contractor operating procedures, and observing key drilling parameters with the enhancement of MPD early kick detection indicators. The MPD system is used in addition to standard conventional down hole event detection methods, and allows rapid and accurate control of bottomhole pressure, therefore enhancing the primary barrier, but does not replace the drilling contractors or operators well control polices or procedures.
IADC/SPE 178805
PMCD Technique Enables Coring & Wireline Logging Operations in Total Lost Circulation. M. Idris, W. Purnomo, PETRONAS Carigali Sdn Bhd; N.H. Houng, J.F. Gallo Zapata, M-I SWACO, a Schlumberger Company
Objectives/Scope: This paper records the planning, execution, and post well analysis of carbonate sections, including the general methodology for the logging and coring operations in PMCD mode, risk and hazard assessment of the operations, results and observations of successful operations in Malaysia with elaboration of issues encountered, and recommended solutions. Methods, Procedures, Process: In the first well, the operator retrieved core samples from three different zones in a gas bearing carbonate reservoir. The coring operation with PMCD, which was the first of its kind in the Asia Pacific Region, created new frontier for carbonate formation evaluation by allowing the acquisition of rock property data from wells once considered to be impossible to drill to TD. In another well, PMCD wireline logging operations were conducted safely and successfully. Open hole to 509 m was drilled with PMCD, and upon reaching TD the wireline logging pressure control equipment was rigged up to commence the PMCD wireline logging operation. In addition to the comprehensive planning and execution procedures, the increased riser pressure limitation was a main enabler for the PMCD wireline logging operations. Eight wireline runs were performed, collecting critical data for the field development plan (FDP). The gas water contact for the field was determined accurately despite the total lost circulation. Results, Observations, Conclusions: Running wireline logging and coring operations with PMCD allowed the operator to not only drill once perceived impossible-to-drill wells, but also to retrieve crucial and valuable data from the well at TD. These operations reduce field volumetric uncertainty. Novel/Additive Information: Pressurized Mud Cap Drilling (PMCD), a variant of Managed Pressure Drilling (MPD) technology, is a technique that enables the operator to drill to target depth (TD) in total losses conditions accompanied by a potential influx of reservoir fluid. The PMCD technique is typically used in carbonate or fractured basement formations where huge karsts or connected vulgular fractures normally occur. This technique does not intend to cure or prevent losses. After reaching TD with PMCD, risks associated with total lost circulation (including potential gas migration and unsustainable fluid logistics) have led to the perception that wireline logging and coring operations in PMCD are not feasible. However, with proper planning and procedures in place these operations are possible. Recent carbonate drilling operations in offshore Sarawak, Malaysia, have proven coring and wireline logging operations can be completed in PMCD conditions.
IADC/SPE 178881
Swab and Surge Pressures with Reservoir Fluid Influx/Loss Condition during MPD. R. Lovorn, R. Samuel, Halliburton
Objectives/Scope: With managed pressure drilling (MPD), there is a need to have precise control on the profile of annular pressure during drilling and cementing. However, current methods using conventional calculations for controlling bottomhole pressures in MPD wells do not properly take into consideration elasticity of drillpipes under reservoir fluid influx. This study investigates the dynamic motion of the drillstring when there is a formation fluid influx with particular interest in the effect at the bottomhole pressure. Methods, Procedures, Process: This paper presents a coupled swab/surge model; whereby, wellbore bottomhole pressure can be predicted more accurately with reservoir fluid influx. Full balance of mass and momentum for pipe and annulus flow are solved. The model also includes the effects of fluid inertia and compressibility, wellbore elasticity, axial elasticity of the pipe, and temperature-dependent fluid properties. Transient gas reservoir model coupled allows investigating the effect of produced gas when the formation pressure exceeds the bottomhole pressures. The model allows measuring the influx as a function of pipe movement and predicting the amount of influx as a function of time. Results, Observations, Conclusions: Increased underbalanced and managed pressure drilling operations have necessitated predicting wellbore pressures more accurately as they allow reduced fluid loss and reservoir influx. While drilling through or reciprocating in a potential reservoir zone in which the borehole and formation fluid pressures are in a narrow margin under managed pressure condition, the swab pressures can cause the wellbore to go underbalance for a short period of time. At certain times incremental influx for even a short duration might be potentially detrimental. Neither the steady-state model nor the transient model is comprehensive to predict the wellbore pressures correctly as they neglect the reservoir fluid influx or fluid loss under this condition. The practical usefulness of the theory backed by the fundamental analysis is demonstrated with two numerical cases. The effects during underbalanced conditions have been analyzed and several non-intuitive transient effects such as observation of reduction in surge effects while swabbing and vice versa are highlighted. Novel/Additive Information: The new model provides the capability to adjust the choke pressures more accurately by taking into consideration the friction forces; and thereby, proper account of the pipe elasticity under fluid loss and fluid influx condition. The results of these calculations can be coupled to a real-time hydraulics model to determine a setpoint pressure for the MPD choke system.
Well Placement II
IADC/SPE 178869
Improved Wellbore Quality Using a Novel Real-Time Tortuosity Index. Y. Zhou, The University of Texas At Austin; D. Zheng, P. Ashok, University of Texas at Austin; E. van Oort, The University of Texas At Austin; C.A. Gongora, Genesis RTS
Objectives/Scope: Tortuosity is an important metric in evaluating wellbore quality. A tortuous well path frequently leads to stuck pipe conditions, poor cementation, and early equipment failures. The industry currently lacks a readily usable real-time tortuosity index to enable the driller to make real-time corrections during the drilling process. This paper presents a new tortuosity index that can be derived while the well is being drilled and validates this index using field data. Methods, Procedures, Process: Until the last decade, average and maximum dog leg severity were the main indicators of wellbore tortuosity and quality. More recently, indirect quantities such as wellbore friction, bending moment, elastic energy etc. were first measured or modeled and subsequently translated to some measure of tortuosity. However, such an indirect process is prone to introducing random errors and other inaccuracies. Another recent approach produces high-precision 3D wellbore profiles to assist in characterization of the tortuosity of the well. This, however, requires additional downhole sensors at additional effort and cost. To overcome these shortcomings, this paper proposes a new methodology that draws upon techniques used in optometry to determine the tortuosity of the narrow veins in human eyes. Results, Observations, Conclusions: The methodology is geometry based, and has the ability to capture wellbore tortuosity present at different length scales (from 1 foot to 10,000 ft). The methodology requires only conventional directional survey data and generates a normalized number, the tortuosity (density) index, in real-time. The methodology was applied on the horizontal sections of 20 unconventional shale wells drilled in 2014. The tortuosity indices derived from these wells were not only compared against other tortuosity assessment techniques, but also against reports of stuck pipe and equipment failure, as well as ultimate hydrocarbon production from hydraulic fractures. The tortuosity index generated correctly identified problematic wells that had a high probability for stuck pipe incidents and downhole equipment failures during drilling. Moreover, preliminary investigations also show high correlation between the index and the production output. The real-time index can therefore be used as not only as a pro-active tool to prevent drilling problems but also help to maximize ultimate hydrocarbon recovery. Novel/Additive Information: This new real time index provides a holistic view of wellbore tortuosity. Its aim is to proactively prevent well problems and inefficiencies before they might occur, while at the same time offering a direct path to better hydrocarbon production. No new sensors or special practices are needed for the adoption of the method. It is also robust to changes in survey distance, and provides indication of micro-tortuosity when continuous/high frequency gyro data is available.
IADC/SPE 178830
Statistical Analysis Between Different Surveying Instruments to Understand the Reliability of MWD/RSS High Resolution Surveys and its Effect in Well Trajectory Characterization. L.C. Monterrosa, M. Ferreira Rego, E. Zegarra, R. Lowdon, Schlumberger
Objectives/Scope: Obtaining further understanding of wellbore TVD placement and tortuosity characterization by qualifying the accuracy of 3 m interval high resolution MWD surveys using statistical comparisons against micro dogleg continuous north seeking gyro listings as well as dual inclination analysis between MWD and Rotary Steerable Systems. Methods, Procedures, Process: The study uses drilling data from various projects worldwide to be able to cover a large range of well trajectories, drilling conditions and BHA types. To understand how accurate the TVD placement and tortuosity effects given by high resolution surveys are, two main comparisons were made: – Micro-dogleg continuous gyros versus high resolution MWD listings over the same interval to prove that two independent sensors measuring well trajectory under difference conditions are following the same trends. Also, that the standard deviations between the inclination measurements are within the statistical limits. – High resolution surveys processed with two independent D&I packages sensors in the same BHA (MWD and RSS) and drilling conditions. Results, Observations, Conclusions: Over 10 runs analyzed indicated that high resolution surveys characterized the well trajectory in the same way as micro-dogleg gyro listings, and the standard deviation for inclination measurements along the drilled interval is low and well within the statistical limits described by the current error models. Additionally, it was possible to demonstrate cases in which the static surveys usually taken every stand do not represent the real description and tortuosity of the trajectory, while the high resolution listing does and this is further backed up when correlating with the continuous gyro data. In another assessment, several runs were compared between high resolution surveys processed with continuous inclination from the MWD and the RSS in the same BHA, providing, as predicted, more accurate results from the previous comparison. Operational considerations need to be accounted for, such as high shock and vibration drilling conditions and low angle wells, in which the continuous data will require stricter quality control to ensure that high resolution surveys represents the true description of the trajectory and wellbore positioning. The results and correlations do not simply ratify the fact that high resolution surveys enhance TVD wellbore positioning and well engineering simulations, but more importantly that the results provided are consistent and reliable, proving a step forward in real time decision making process and allowing drilling operations to be more efficient with fewer HSE risks involved. Novel/Additive Information: Several success stories have being presented on the benefits of high resolution surveying for well placement enhancement and well engineering simulations, however nothing has been published regarding how well high resolution MWD survey results correlate with the different surveying instruments using statistical analysis. In addition, this study will trigger future evaluations of TVD error modeling enhancement.
IADC/SPE 178794
What Causes Depth Errors in Surface-Based Drilling Sensor Systems? S.W. Lai, M. Pawson, J. Wang, N. Mukanov, T. Wilson, Pason Systems Corporation
Objectives/Scope: Drillstring depth is one of the most important parameters measured by drilling sensor systems. Accurate depth is crucial in directional steering applications, and depth serves as a key reference point for most drilling parameters measured at the rig. Ideally, depth is tracked using the knowledge of travelling block position, in-slips/out-of-slips condition, and length of each pipe in the pipe tally. However, the depth reading on an electronic drilling recorder (EDR) often diverges from the pipe tally, and requires periodic adjustment to remain aligned with the pipe tally total. In this study, we investigate what causes these depth tracking errors and quantify their magnitude in onshore wells. Methods, Procedures, Process: This investigation is performed with two main efforts. First, the tracking error is characterized by analyzing the corrections made to EDR depth during the drilling of several land-based wells. Driller-initiated adjustments to depth are captured for 30 wells and 7 rigs, and are analyzed statistically to quantify their magnitude and frequency of occurrence. In the second effort, we examine the workflow used by drilling crews to keep the EDR depth consistent with the pipe tally. Comprehensive interviews are performed with 21 crew personnel, and the various methods for maintaining depth calibration are analyzed to expose pitfalls with current industry practice. Results, Observations, Conclusions: This paper contains quantitative and qualitative results which reveal the source of depth errors in surface-based systems. Analysis of a large number of depth corrections shows that depth errors can be classified into 3 groups: offset errors, accumulation errors, and workflows errors. Accumulation errors, caused by encoder inaccuracies, and offset errors, related to depth reference ambiguities, result in the majority (75%) of depth corrections. Workflow errors account for a minority (25%) of depth corrections but have extremely large magnitude and account for over 60% of the total per-footage error. Interviews with several rig personnel reveal that different crews use different workflows to set and calibrate depth. Different workflow types are not found be specific to any geographical region and appear to vary from crew-to-crew. Novel/Additive Information: This paper is novel because it is first time that depth accuracy has been characterized using a large body of data. The most surprising result is that the largest contributor to depth error is not encoder inaccuracy, but is, in fact, related to the workflow used for EDR depth adjustments. This paper is also novel because it details a comprehensive user experience investigation into the method used by drillers to transfer the pipe tally to the depth reading on an EDR. The findings reveal that different drillers have different approaches to depth tracking, and an industry recommended practice would be useful to reduce errors in surface-based systems.
Applied Fluids for the Hole Conditioning
IADC/SPE 178766
Invasion and Movement of Fluids in Shale Formations and Wellbore Stability. W. He, E. Jimbi, M. Chamberlin, M-I SWACO, Schlumberger; A. Zakaria, Intertek/Westport Technology Center
Objectives/Scope: The invasion and movement of drilling fluids through shale formations can significantly contribute to wellbore instability. This paper will present experimental results of the invasion and movement of fluids in shale formations near wellbore. By combining the experimental results with the microstructural studies of core samples, we will examine the invasion and movement of fluids in shale, including the mechanisms, rates, affecting factors, and impact on shale stability. This study will help optimize drilling fluids that minimize wellbore instability in shale formations. Methods, Procedures, Process: Pre-test core studies provided insight into rock composition, structure, fracture distribution, water activity, and pore-fluid composition. Pore-fluid transmission tests were conducted on preserved shale cores from four different formations, each with a different water activity measurement. The first set of tests used synthetic pore fluids to understand the pressure transmission and fluid invasion through shale formations, which are primarily controlled by hydraulic pressure or capillary pressure. Next, pore pressure transmission tests were conducted with non-aqueous drilling fluids of different water activities to quantify the transport driven by gradients in pressure, concentration, and chemical potential. Thin section analyses of post-test cores were conducted to evaluate shale-fluid interactions and the impact of fluid invasion and movement on shale stability. Results, Observations, Conclusions: Test results clearly showed reverse osmosis out of the shale. The reverse osmosis increased with an increasing difference of water activity between the shale’s pore fluid and the drilling fluid. A water activity difference of >0.07, and the resulting pore-pressure drop (caused by the reverse osmosis) subdued the impact of fluid invasion from drilling fluid to formation and led to a net decrease in downstream pressure. Reverse osmosis could cause downstream pressure below the initial value in a few minutes. A pore-pressure drop due to reverse osmosis may improve the stability of wellbore due to an increase in effective mud support. However, testing showed that strong reverse osmosis could cause fracturing from over-dehydration of the shale. Testing also indicated that invasion along fractures increased pore pressure, even with a potential of strong reverse osmosis. Adjusting the water activity of drilling fluids to closely match that of the shale formations while minimizing fluid invasion along fractures and other fluid channels reduces wellbore instability. Novel/Additive Information: In many cases, the measured reverse osmosis is low, but testing reported in this paper clearly shows reverse osmosis occurs. The quantitative relationship between osmosis and water activity is determined. The transport mechanisms, including the role of fractures in fluid invasion, and their impact on shale stability are evaluated.
IADC/SPE 178862
Use of a Transient Cuttings Transport Model in the Planning, Monitoring and Post Analysis of Complex Drilling Operations in the North Sea. E. Cayeux, A. Leulseged, N. Saadallah, Intl Research Inst of Stavanger; G. Salevik, Intl Research Institute of Stavanger; R. Kluge, Statoil ASA; J. Haga, Talisman
Objectives/Scope: Inadequate hole cleaning during a drilling operation may result in immediate problems like excessive torque or pack-off situations, or it can lead to delayed problems like while running in hole with a casing/liner or a completion string in a leftover cuttings bed. It is therefore desirable to provide quantitative information about hole cleaning conditions: at the planning stage, while drilling or when investigating incidents. Methods, Procedures, Process: Because the ability to transport cuttings particles varies with their position in the borehole and the current drilling parameters, hole cleaning modelling is a history-dependent problem. The precise modelling of the movement of solid particles during a drilling operation gives the possibility to estimate whether they are in suspension in the drilling fluid, settling on the low side or being eroded from a cuttings bed. These estimations may be confirmed or infirmed through the change of the active volume or by the increase of downhole pressure, when PWD (Pressure While Drilling) measurements are available. Results, Observations, Conclusions: A transient cuttings transport model has been used in the planning and monitoring of an ERD (Extended Reach Drilling) well drilled in the North Sea. The model has been used to compare the expected performance of different mud systems on both hydraulic and mechanical limits that could be expected prior to drilling. While drilling, predictions made by the model for the formation of cuttings bed, have been used to confirm the observations like surface torques and pick-up/slack-off weight. For another challenging drilling operation, the model has been used to post analyze the sequence of actions that led to problems while running in hole with a liner. Here also, the observations tended to confirm the predictions made by the hole cleaning model. Novel/Additive Information: Furthermore, an active use of such advanced hole cleaning model may help determining the time required for circulation procedures prior to pull out of hole. This can help reducing the flat time associated with circulation procedures and at the same time decrease the duration by which the hole stays open thus reducing the risk for hole instabilities.
IADC/SPE 178790
Forming a Seal Independent of Formation Permeability to Prevent Mud Losses – Theory, Lab Tests and Case Histories. H. Wang, Sharp-Rock Technologies.; S. Savari, Halliburton Co.; D.L. Whitfill, Halliburton; Z. Yao, Hess Corp.
Objectives/Scope: Conventional lost circulation materials (LCM) may have to depend on formation permeability to form a seal to an incipient induced fracture in order to prevent mud losses. However, weak formations we drill through daily are not always permeable. Furthermore, permeability is reduced in permeable formations due to the fact that drilling fluid, especially non-aqueous drilling fluid, tends to have excellent control over fluid loss by forming a tough mud cake instantaneously on a newly fractured surface. A permeable formation therefore may behave as if impermeable. It is important to recognize that it is desirable that forming a seal does not depend on formation permeability. Methods, Procedures, Process: Induced fractures are hydraulic fractures. The fluid volume invading a fracture widens the fracture progressively. In order to form a seal to an induced fracture, it is important that the seal forms after only a small volume fluid flowing into the fracture. This fluid volume is actually the spurt loss of the LCM fluid. Therefore controlling the spurt loss to low values so as to not open the fracture too wide is critical. In order to quantify the spurt for good and reliable performance, two new “Fast-Sealing LCM” are created and tested. Each of these products has a maximum sealing width defined by its largest particle size. The Fast-Sealing LCM is then characterized with a slot disk for its spurt loss at various concentrations. Furthermore, for a specific rock with specified mechanical properties, the maximum allowed invasion volume for an induced fracture, before the fracture opens to the maximum sealing width of a Fast-Sealing LCM, can be calculated using a textbook hydraulic fracturing theory. Adding enough of the Fast-Sealing LCM to control the fluid spurt volume smaller than this maximum allowed invasion volume is the necessary criterion to ensure the seal forms before the induced fracture opens too wide to seal. This paper will demonstrate how rock mechanical properties are linked to the concentration of the standardized Fast-Sealing LCM. Furthermore, it is demonstrated that a seal can form even when there is no fluid loss leaking into the formation. In other words, this engineering allows forming a seal independently of formation permeability. Results, Observations, Conclusions: It will be demonstrated how a wellbore strengthening job can be designed and implemented with multiple successful case histories of drilling operations on land and offshore. Furthermore, it will also be demonstrated why the reliability of the application may not be compromised even when rock data are not accurately known. Novel/Additive Information: 1)A process to ensure a seal to an incipient induced fracture independent of the formation permeability; 2)Special particulate formulations to provide high efficiency in sealing fractures with low spurt losses.
IADC/SPE 178799
The Role of Filtercake in Wellbore Strengthening. J.M. Cook, Schlumberger; Q. Guo, Schlumberger Cambridge Research; P.W. Way, Schlumberger; L. Bailey, Schlumberger Cambridge Research
Objectives/Scope: Recent experiments and associated modelling on wellbore strengthening have revealed the importance of the filtercake in inhibiting the growth of the fractures that would otherwise cause lost circulation. As a result, this increases the pressure that the wellbore can sustain, during both drilling and cementing. Methods, Procedures, Process: In preventive wellbore strengthening treatments, the rock formation is assumed to have no open fractures. Fractures are induced during the drilling process and the treatment inhibits their growth. This technique is most often used in drilling through depleted formations, and has proven to be very effective. The basis of design is that particles of loss prevention material (LPM) in the drilling fluid are sized to enter the fractures, form a bridge within them, and then restrict fluid flow to the tip. Results, Observations, Conclusions: A second mechanism has also been identified. Several hundred block tests on sandstone samples have been performed using various fluids, from drilling muds to cements, under various treatment conditions. These tests revealed the importance of filtercake in preventive wellbore strengthening. Particles sized to block a specific fracture were not needed. Provided that the filtercake itself can bridge the very narrow fractures that form at early times, it can prevent the fluid flow into the fracture that then allow the fracture to extend and widen. Novel/Additive Information: The properties of the fluid that lead to beneficial filtercake formation have been determined through these tests. For example, block tests using cement slurry showed that a high concentration of very small particles can produce excellent wellbore strengthening. Test results also showed the effects of particle size, concentration, and fluid loss. Various filtercake characterization methods were used to identify the root cause of filtercake effects on wellbore strengthening performance.
IADC/SPE 178892
Case History: An Enhanced Solids Control Strategy “Selective Flocculation Process” Allows for Reduced Dilution Rates and Costs in Water-based Drilling Fluids in Auca Field, Ecuador. A. Bastidas, J. Enrqiue, Petroamazonas; S. Costa, K. Maiquiza, M.A. Serrano, Halliburton
Objectives/Scope: This paper presents the application of selective flocculation, an enhanced solids control strategy that increases the efficiency of the drilling fluid and the solids control equipment. Removing fine drill solids from the fluid system is a key parameter to increase drilling efficiency and develop a successful overall drilling operation. Methods, Procedures, Process: While the process focuses on highly efficient centrifuges, a detailed evaluation of all solids control equipment on the drilling rig should be completed. Centrifuges should be installed in simple barite removal/recovering systems, and manifolds for the concentrated flocculants solution (a specialized mix of polymers) injection should be installed. The flow stream necessary for centrifuge operation is separated from the drilling fluids surface circuit to the flocculation system. A specialized polymer solution is injected, and injection rates are fine-tuned until a clear output effluent with a clay content value (measured by a methylene blue test) at or near zero is obtained. Results, Observations, Conclusions: Efficient removal of drilled solids, especially smaller or colloidal sizes, improves the performance of the drilling fluid products used to mix the mud, since more product is available to interact with the borehole. This generates not just a stable hole but a cleaner and more effective drilling fluid. In this process, side effects and benefits are realized, but more important are reduced water consumption, a reduction in additional fluid needed for dilution, reduced consumption of products for sustaining mud properties for rheology and filtration control, and an increase in inhibition. When the treatment is evaluated, an improvement of solids control equipment efficiency is about 10%, and a reduction of approximately 12 to 30% in total new drilling fluid volume generated at the rig is realized. Reductions in water consumption and cost savings are directly proportional to the reduction in product consumption. Novel/Additive Information: At a time when the challenge of reducing operating costs is common and environmental protection is required, a reduction in the use of water resources is extremely important. The selective flocculation process is an interesting alternative to meet requirements for water and cost savings. Since the initial investment is no greater than what is necessary to maintain the solids control equipment, the cost/benefit ratio is optimized, and clean drilling fluid for efficient drilling is obtained.
IADC/SPE 178803
Lost Circulation Management in Naturally Fractured Formations: Efficient Operational Strategies and Novel Solutions. S. Savari, D.L. Whitfill, Halliburton
Objectives/Scope: Managing severe to total lost circulation can be very challenging in naturally fractured formations. Particulate lost circulation materials (LCMs) have been used to manage lost circulation for many years. However, current LCMs are not efficient in terms of size and application methods when it comes to curing severe to total losses, such as highly fractured formations. Methods, Procedures, Process: In the present paper, preventive (proactive) and remedial (reactive) operational strategies will be discussed. Along with the operational strategy, this paper will also present novel additives in the form of engineered composite LCM solutions (ECS) with multi-modal particle-size distribution (PSD) that were successfully used to manage severe to total loss situations in naturally fractured carbonate formations. The multi-modal particle-size distribution will help manage any uncertainties in fracture sizes, and the presence of larger particles will also aid in plugging large fractures. Case studies will be presented for applications in the mid-continental USA, Middle East, and offshore East Africa. Results, Observations, Conclusions: Preventive strategies are recommended to reduce the potential for lost circulation (LC). It is recommended that LC management be considered from the wellbore planning/design phase and that all engineering analyses be performed prior to the start of drilling the well. It is very important to have remedial strategies in place if the preventive plan does not work. This includes putting loss contingency plans in place should unexpected loss events occur. Examples will be discussed as to how previous knowledge and lessons learned can play a critical role in developing contingency engineered solutions to effectively cure losses. When managing severe-total losses in highly-fractured formations, particulates alone may not be effective. The combination of a large multi-modal PSD LCM, a swellable component, and chopped synthetic fibers were proposed as a candidate for dealing with such high losses. While drilling highly-fractured formations, this combination was applied after all conventional LCM applications failed. In most cases, the combination was pumped open-ended, and losses were totally cured so that circulation could be re-established. To conserve rig time, the use of a treating sub is recommended as part of the BHA for handling high concentrations of large PSD LCMs for curing severe losses. Novel/Additive Information: The use of operational strategies (LCM applications) and novel LCM solutions for curing severe to total losses in naturally fractured formations will be the novel information presented in this paper.
New Tools for New Times!
IADC/SPE 178829
A New On-Command Integrated Expandable Under Reamer Technology Enabled Unique Drilling Solutions: Lowering Operational Risks and Saving Operational Cost. L. Fang, Baker Hughes; A. Manseth, INTEQ; K. Stue, Baker Hughes Norway; B. Johansen, J. Skappel, Wintershall Norge AS
Objectives/Scope: This paper presents the technical features and the associated benefits of a new integrated expandable under reamer technology, and showcases the field testing of the technology in the Brage field in Norway and the achieved results. Methods, Procedures, Process: Historically, the overburden stratigraphy at Brage field has been challenging for drilling. The unstable green clay and Draupne shale formation and the casing programs necessitate hole enlargement while drilling. In particular, the 12 ¼-in. section has a planned Total Depth (TD) right below the Draupne shale, inside which the calcite stringers also present, and a near bit reamer significantly increases the likelihood of getting down the 10 ¾-in. casing. A new integrated under reamer technology was utilized to address the challenges in drilling two sections of a well in Brage: 14 ¾ -in. X 17 ½-in., and 12 ¼-in. X 13 ½-in.. The new under reamer is fully integrated with the company’s rotary steerable system, which enables unlimited on-demand activation and deactivation cycles through downlinking with each cycle taking less than 5 minutes, flexible and optimal placement of the reamer in the bottom hole assembly (BHA), and real time feedback from downhole. The flexibility of the placement in BHA allows the reamer to be used as a near bit reamer, a main reamer, or both. When used as a near bit reamer, the reamer can reduce the rat hole length to a minimum of 4 m in the same drilling run, eliminating the need of a dedicated rat hole elimination run. The real time feedback includes confirmation of the blade activation status and a hole opening diameter log, reducing operational uncertainty for under reaming and saving rig time for a shoulder test that is otherwise required. Results, Observations, Conclusions: The technology proved its effectiveness as a reliable main reamer as well as a near bit reamer for rat hole elimination while satisfying all requirements for directional drilling and enabling MWD and LWD measurements. For the 12 ¼-in. X 13 ½-in. section, both main and near bit reamers were activated while drilling the last 70 m to TD and a good drilling performance was achieved. Novel/Additive Information: The new technology provides unique features such as unlimited cycles of activation and deactivation through downlinking, flexible placement in the BHA and real time feedback from downhole. The paper will describe these features, and demonstrate how they can help the operators to reduce operational risks and save cost. It will also showcase a unique drilling application where three cutting / reaming elements in the BHA are actively present simultaneously and the associated drilling performance.
IADC/SPE 178795
Downhole Drilling Dynamics of Innovative Rathole Elimination BHA in Hole Enlargement While Drilling Operations. Y. Wang, N. Fuller, V. Saheta, Schlumberger
Objectives/Scope: Hole enlargement while drilling (HEWD) is now widely used in deepwater applications. It provides reduced-clearance casing programs, improves drilling in swelling formations, and helps equivalent circulating density management. HEWD applications commonly use an underreamer in a BHA with a rotary steerable system (RSS). Currently, traditional reamer placement results in a long portion of unenlarged hole _ rathole _ which requires an extra trip to enlarge. A new BHA design is desired to eliminate the second trip requirement and the objective is to find a feasible solution. Methods, Procedures, Process: Placing the reamer closer to the bit would forgo the need for a second trip; however, traditional reamer’s placement is limited by its design. In response to the limitation, a solution is proposed to design a rathole elimination (RHE) BHA which includes a lower reamer, between MWD/LWD and RSS tools. During HEWD, the lower reamer is in passive (off) mode while a traditional reamer is active. Upon reaching TD, the BHA is tripped back to position the lower reamer above the rathole and then activated to enlarge the rathole. This RHE BHA design thereby eliminates the second trip requirement. Results, Observations, Conclusions: This paper discusses the operational learnings and drilling performance of the proposed RHE BHA design. A field test in Texas is presented which documents the downhole dynamics performance of the single-trip BHA. Drilling dynamics measurement modules (DDMM) were positioned near the reamers to measure the downhole drilling dynamics. This run captured data for traditional HEWD operations and rathole elimination operations. To ensure stable drilling operations a time-based dynamic simulation carried out prerun parametric sensitivity study to help identify optimum parameters which could deliver high ROP, low vibration, and low stick-slip. A road map was made for operation guidelines based on simulation analysis. The test was successfully accomplished with stable HEWD and RHE operations observed. After completion of the run analysis of the DDMMs, measured downhole dynamic data showed stable downhole drilling dynamics during both HEWD and RHE operations. RHE operation generated similar levels of vibration and stick-slip at the reamer, RSS, and MWD/LWD tools compared with HEWD operation. This field test shows a single-BHA design can deliver stable drilling dynamics in both HEWD and RHE operations, and demonstrates the capability of the innovation solution in eliminating the second trip requirement. Novel/Additive Information: This single-trip RHE BHA design will not only reduce the operational costs but also lower the HSE risks with less BHA handling on the rig floor.
IADC/SPE 178816
Remotely Operated Cementing Methods for Drilling With Liner Installations. S.M. Rosenberg, Weatherford International; B. Hagen, Weatherford; R. Dalzell, Weatherford Completion Systems; T. Gudmestad, J. Zavala, R. Malone, R. Mogensen, Weatherford
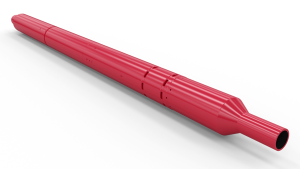
Objectives/Scope: A North Sea operator experiences sustained annulus casing pressures in wells in a mature chalk field due to insufficient hydraulic isolation methods after a 9-5/8-in. drilling liner is drilled through a pressured shale overburden interval into a depleted chalk interval with the liner typically becoming stuck. An international oilfield service provider collaborated with the operator and designed a cementing solution using a series of strategically positioned remotely operated cementing port collars on the drilling liner to meet the required cementing objectives. This paper will present the drilling with liner system design process with the procedures enabling the cementing port collars to be remotely activated with the liner having the ability to be rotated above the stuck pipe section with cementing operations commencing almost immediately after reaching total depth. Methods, Procedures, Process: The remotely operated cementing port collars are strategically postioned on the liner and activated with pressure pulse and/or RFID methods without exposing the formation to pressure surges enabling the cement operation to be conducted in single or multiple stages. Also included on the drilling liner are a metal expandable annular casing packer and hydraulic casing swivel designed and configured to be fully compatible with the planned hydraulic DwL system. Results, Observations, Conclusions: This remotely operated cementing process enables cementing to commence directly after the liner reaches its planned depth with the cementing port collars selectively opened and closed. The hydraulic casing swivel allows the liner to be rotated above its stuck point should it become stuck during the liner drilling operation. The metal expandable annular casing packer is designed to handle the rigors of liner drilling while still retaining the mechanical and hydraulic integrity to support the planned cement column. Novel/Additive Information: The remotely operated cementing process will allow for conducting multiple stage cementing operations in narrow pressure profile windows without exposing weak formations to pressure surges. This technology will enhance wellbore integrity over the life of the well by greatly increasing the potential for complete hydraulic isolation of the annulus while mitigating or eliminating the potential for annulus gas flow with the resulting sustained annulus pressures seen with conventional cement jobs.
IADC/SPE 178866
Integration of Time-Based Dynamics Simulation with Milling and Underreaming System to Implement Reliable Single Trip Solution in Plug and Abandonment Operation. Y. Wang, M. Vos, A. Karimpour, M. Fearn, H.d. Besten, T. Stanko, J. Bain, Y. Shen, Schlumberger
Objectives/Scope: A trip saving Well Abandonment technology was recently developed to prepare wellbores for the installation of abandonment barriers where poor annular cement quality exists at the required plug location. The trip saving technology uses a hybrid section milling and under-reaming single trip BHA design to remove casing from the wellbore and underream to virgin formation to eliminate all potential leak baths from the cement barrier. This single trip BHA is a step change in conventional industry practice whereby the service is typically provided in two dedicated trips: one to mill and one to underream. This paper presents the successful application of the single trip BHA with the aid of a time-based simulation system in a challenging environment. Methods, Procedures, Process: The single trip BHA was required by an operator in Netherlands, where challenging well conditions and abandonment requirements resulted in the need for underreaming to a 20in. hole size from a wellbore tool restriction OD of 8.5-in.. This ultra-high ratio reamer arm opening generates significant dynamic loadings on the BHA. To achieve a successful single trip operation, a 3D time-based drilling dynamic simulation system was employed as a technical solution to ensure: •Maximum ROP to meet client requirements whilst balancing with BHA limits of operation. •The underreamer would behave as intended and create a concentric and balanced hole opening across the full hole profile. The dynamic simulation first carried out pre-run parametric sensitivity study to identify the optimal parameters with high ROP and low vibration/stick-slip ratio. Then the underreamer off-center distance was examined to ensure sufficient new virgin rock exposure in all directions for subsequent cement plug setting. Results, Observations, Conclusions: This dynamic simulation outcome was the creation of a prejob planning roadmap which enabled the job to be executed seamlessly at the rig site whilst achieving the client Plug and Abandonment (P&A) objectives and ensuring the optimal utilization of each component of the single trip BHA. The pre-job planning roadmap was calibrated against operational performance by recorded stable operation data, observed good reamer arm dull conditions and good Caliper logged hole quality. In addition, the field test data was found to be highly in line with the simulation predictions, validating the accuracy of the time-based dynamic simulation system. Novel/Additive Information: The single trip operation saves operator more than 20 hours of rig time to underream one 20-in. opening hole. The successful application shows the capability of the single trip BHA in conjunction with dynamic simulation in saving rig time and delivering reliable service, which can help operators reduce costs and lower HSE risks with less BHA handling on the rig floor.
IADC/SPE 178837
Quantifying Asphaltene Content from Downhole Optical Spectral Data During Sampling While-Drilling Operations. K. Indo, J.J. Pop, K. Hsu, J. Qi, S. Ossia, Schlumberger; A. Garcia-mayans, Schlumberger D&M; S.A. Haq, J. Varughese, Schlumberger
Objectives/Scope: Downhole fluid analysis (DFA), which uses visible and near-infrared spectrometry during formation tester operations to estimate downhole fluid properties, has, during the past two decades, proven to be one of the most effective means for obtaining accurate and detailed reservoir fluid property information. In a previous publication (SPE 166464), a methodology was introduced for estimating, from downhole optical spectrometer data acquired during sampling operations, fluid properties, such as fluid type, hydrocarbon composition (C1, C2, C3, C4, C5, and C6+), carbon dioxide content, and gas/oil ratio (GOR). We have extended the methodology introduced in the previous publication to the real-time estimation of asphaltene content of black oils. Methods, Procedures, Process: The equation derived for quantifying the asphaltene content of crude oils uses measured optical densities (OD), the absorption coefficients of asphaltene and resin, stock tank oil (STO) density, resin content, and formation volume factor (FVF). The ODs are measured using downhole optical spectrometry. In the process of deriving the asphaltene content, a new method was devised for estimating FVF from optical data. The remaining parameters and the uncertainty in the estimate of asphaltene content are calibrated against a database that contains asphaltene content data and the corresponding optical spectral data of various crude oils. Using the derived equation, a maximum likelihood estimate of asphaltene content of crude oil and its associated uncertainty can be obtained. Results, Observations, Conclusions: The accuracy of the method for estimating FVF and asphaltene content together with their uncertainties was verified and validated using laboratory crude oil data. The method was also applied to downhole optical spectral data acquired during a sampling-while-drilling (SWD) operation. It was found that the estimated asphaltene content and FVF obtained from the measured downhole spectral data showed very good agreement with the results of laboratory pressure/volume/temperature (PVT) analysis performed on captured fluid samples. Novel/Additive Information: Understanding reservoir fluid properties plays an important role in assessing, planning, and developing reservoirs. Obtaining real-time reservoir fluid property information makes this critical information available as early as possible in the life of the reservoir. This work demonstrates that such information can be obtained during while-drilling operations. We believe the most appropriate categories under which this work should be classified are Downhole Tools (01e) and Innovative Technologies (06a).
IADC/SPE 178818
A New Steady Weight-on-Bit Tool Reduces Torque and RPM Variations and Enhances Drilling Efficiency and Bit/BHA Life. S. Jones, Turbo Drill Industies; C. Feddema, Turbo Drill Industries
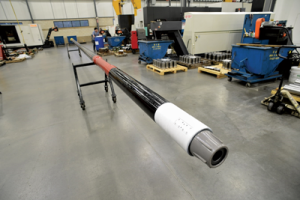
Objectives/Scope: Maintaining a steady weight on bit while drilling long horizontal sections can be difficult due to drill string flexibility, wellbore friction and downhole dynamics. Variable slack-off weights and drill string buckling results in unsteady Weight on Bit (WOB) that generates string- and bit-induced stick-slip and torsional vibration. Variable string RPM and differential pressure causes changes in length of the drill string. These changes in length are directly acting on the drill bit and the result is a very chaotic drilling situation that is extracting energy from the drilling process. This paper describes the operation and field test results from a new tool designed to maintain steady WOB. Key component in the string were instrumented sensors to gather critical information on inclination, temperature, vibration, shock, RPM and stick-slip events. Methods, Procedures, Process: The fully-mechanical anti-WOB-fluctuation tool has been designed to change its tool length in coordination with the drill string. As the drill string increases in length, the tool decreases in length and as the drill string decreased in length the tool increases in length. This allows a steady WOB to be maintained downhole. It was critical to gather high-frequency downhole data to understand the operation and effectiveness of the tool. Downhole sensors and electronics were instrumented in the tool to examine the response of the steady WOB mechanism. These sensors included 3-axis inclinometers, 3-axis shock sensors, and 2 redundant temperature sensors, which are packaged in a compact pressure housing (¾-in. diameter and less than 4-in. length), including a communication port and high-temperature lithium battery. The sensors were used to capture downhole dynamics of the tool. Results, Observations, Conclusions: The data received from the downhole instrumented devices provided valuable information on drilling dynamics over the course of the field test runs. This data was merged with the surface data to understand the effectiveness of the tool that provides active downhole control of WOB. The data analysis result is discussed and correlated to improvements made during the course of the field test. The tool significantly reduced cutter-induced torque, WOB variations and string stalls; thus improving rate of penetration. With active downhole WOB control, the downhole dynamics were prevented from damaging the bit and instead this energy was uses to optimize the bit-rock interaction. The new steady WOB tool has proven to provide significant drilling performance improvements and to extend the life of downhole equipment and bits. Novel/Additive Information: A fully-mechanical steady WOB tool has been field tested with downhole electronic instruments to gather critical information such as shock, vibration and stick-slip. The data gathered provides a clear picture of the downhole dynamics improvements with the steady WOB tool incorporated into the BHA.
IADC/SPE 178800
Benefits of Using Downhole Vibratory Casing Tools in the Niobrara/Codell Formations. R. Schultz, TTS Drilling Solutions; M. Warner, Kaiser-Francis Oil Co.
Objectives/Scope: In recent years the construction of horizontally drilled wells has become commonplace. The horizontal sections of these wells have continued to increase in length as equipment and methods used in constructing these wells have improved. As lateral lengths have increased, so have the challenges associated with drilling and completing these wells. The high TMD/TVD ratios seen in many wells often presents challenges during the installation of casing and liners. The primary issue is the friction associated with horizontal well profiles and the absence of adequate vertical casing weight. In order to combat the problems associated with getting casing/liners to bottom, operators are increasingly using downhole vibratory tools to aid these operations. Vibratory downhole tools primarily help by breaking the static friction between the workstring and wellbore or casing. These tools are commonly used in horizontal well drilling operations but more recently these tools have also begun to be run on casing strings with great success. Methods, Procedures, Process: In this paper, the results of field tests using a downhole vibratory casing tool on a group of wells in the Niobrara and Codell formations are presented. Eight (8) wells were considered during the study. A vibratory casing tool was run in four (4) wells. Casing was run in four (4) additional wells in which no vibratory tool was used. The wells involved in the testing were completed with 4-1/2” 13.5# P-110 liner in 2-section laterals. Results, Observations, Conclusions: Evaluation of the data shows a 38% average increase in running speed while rotating the liner in the hole when using the vibratory casing tool resulting in an average of an 11 hour (36%) decrease of rig time per run. Additionally, less torque at higher rotary speeds was seen on the wells in which the vibratory tool was run. Novel/Additive Information: The associated physics, operating methodology and effectiveness of these tools will also be presented.
Efficient Rig Design and Strategies
IADC/SPE 178902
Avoiding the “Money Pit” Effect: The Renascence in Delivering Complex Drilling Facilities. D. Reid, T. Yost, National Oilwell Varco; T. Cheung, Keppel Offshore & Marine; I.J. Russell, KCA Deutag LLC
Objectives/Scope: Highly engineered, unique platform designs begin with a simple, solid plan to succeed and often fail, whereas Mobile Offshore Drilling Units (MODU’s) have seen a revolution in operational efficiency. This paper will look to apply lessons learned and understand why drilling facilities on platforms have missed the mark. In practice, that plan with platform rigs is to follow the benefit of experience of the prime facility architects in order to deliver a more efficient and better designed facility. The challenge is that the project then evolves to focus on managing complexity rather than an informed attempt to eliminate it. Despite all the great intentions and promise of experience, challenges emerge that cause delay and cost overruns. This paper illustrates lessons learned from MODU’s and the business and technical mechanisms that make on-time, on budget platforms unreachable without a radical change in methodology, measurement and leadership. Methods, Procedures, Process: To understand the methods in successful complex drilling rig construction, the focus will be specifically on the experience and observations as well as calculation of experts to illustrate avenues for future solutions. One component of a platform that we will target as low hanging fruit is the drilling facilities, which are as guilty as any component of adding severely complex infrastructure. Results, Observations, Conclusions: This paper highlights the specific business and technical challenges faced in facility deliveries. Those who have partaken in the recent change in MODU projects claim to have experienced a business anomaly where all parties were generally satisfied with the outcomes. The focus on shared targets and alignment helped the supply chain master the art of on time delivery and lower costs, facilitated in large part by integrated single supply package ownership. Examples of how costs can multiply and some specific applications where the outcomes can be simply assessed will be shared. The underlying principal that seems to be driving inefficiency in platform construction has been an ancient practice of building a Frankenstein money pit that has become the mark of historic MODU’s and remained the norm for the modern drilling platform. Novel/Additive Information: It is time for the platform construction model to benefit from the experience on “informed simplicity” and for change to become more than a theory at inception. This market with a low oil price is set perfectly for the MODU construction renascence to start affecting other more complex drilling and production applications.
IADC/SPE 178890
New Wireline Extreme Pull Systems Reduce Gulf Of Mexico Deepwater Fishing Incidents Saving Operators 12 Days of Deepwater Rig Time and USD 8 Million. B. Fisher, B. Daugherty, Deep Gulf Energy; S.A. Sarian, J. Tucker, D. Robinson, D. McManus, C. Babin, J. Varkey, Schlumberger
Objectives/Scope: The combination of a newly developed extreme-tensile-strength steel wireline cable armor and polymer encapsulation technologies has recently created a second generation of low-torque, extreme-strength wireline cables. The high-pull system is complemented with high-capacity surface data acquisition winch units, tension-relief capstans, and downhole well accessories. The resulting surface pull capacity of wireline conveyance reaches 26,000 lbf, a 25% increase over the strongest system available previously. Methods, Procedures, Process: When the 21,000-lbf system was introduced in 2010, deepwater fishing incidents dropped to less than 1% of total descents. However, with three days per fishing operation, associated deepwater fishing time remains high. The new high-pull system has been deployed in the Gulf of Mexico since October 2014. Pulls exceeding 21,000 lbf made it possible to prevent four instances of otherwise unavoidable fishing incidents, saving more than 12 deepwater fishing days and $8 million of rig time. Results, Observations, Conclusions: Gulf of Mexico operator, Deep Gulf Energy deployed the extreme-pull system to carry out the wireline logging operations in their deepwater Gulf of Mexico well, in preference to a pipe conveyed (TLC) lengthy operation. At one critical fluid sampling point the toolstring became stuck. A pull in excess of 21,000 was applied to free the toolstring, avoiding a four day fishing job, the loss of valuable reservoir fluid data, saving $850,000 per day and totaling $3.4 million of rig time. Novel/Additive Information: The second-generation high-pull system integrating extreme-strength polymer-encapsulated wireline cables, fit-for-purpose surface equipment, and downhole conveyance accessories has brought a step change in deepwater wireline conveyance operations. Tool fishing incidents are minimized while high-quality advanced wireline data acquisition is assured with minimal operational and HSE risk.
IADC/SPE 178759
Spare Parts Strategy Based on RAM Analysis Extends Drilling Supervisory and Control Systems’ life. D. Cao, BP American; N. Moralez, BP America
Objectives/Scope: As components within the drilling supervisory & control system (DSCS) approach their end of design life, different approaches are leveraged to improve availability. Common practice is to replace the entire DSCS thus eliminating obsolescence. An alternative solution is to employ a spare part strategy on the existing system to prolong its life, which can realize considerable savings. This paper describes implementation of a spare part strategy to extend the life of the DSCS. It provides a case history of quantitative analysis of system availability versus the number of spare parts so as to find the best number of spare parts to maximize system availability. Methods, Procedures, Process: For each critical component in the DSCS, the MTTF and MTTR are estimated. Based on DSCS network architecture drawings, the reliability, availability, and maintainability (RAM) model is created using a reliability block diagram. The simulation method is chosen to perform the RAM analysis. A sensitivity analysis is also conducted to see the impact of the number of spare parts on the system availability. Finally, the genetic algorithm is implemented to find the optimal spare part combinations to maximize availability. Results, Observations, Conclusions: Preliminary results from a pilot RAM analysis on a single component within the DSCS are shown in the figure (table) attached. The upper part of the table shows the fleet availability versus the number of spare parts. The results indicate that if proper number of spare parts is maintained, it is possible to eliminate obsolescence and extend the life of the system while minimizing the impact on drilling operations. The lower part of table shows the expected failures versus the number of spare parts. As the number of spare parts increases, the expected number of failures also increases because after a spare part is installed, it may fail too. This indicates that the method of using the expected number of failures to determine the number of spare parts is not recommended (this method is commonly employed in drilling community). A RAM analysis is the best way to conduct a spare part analysis. Novel/Additive Information: 1.Within the drilling community, the number of spare parts is usually determined by experience or by the expected number of failures. The empirical spare part management practice can be enhanced by reliability methodologies. This paper tries to use reliability methodologies to provide a scientific way to guide the spare part strategy in the drilling community. 2. In the past, when the DSCS became obsolete, the whole system was replaced/upgraded, entailing high replacement/upgrade cost. For the first time, we are trying to employ a spare part strategy (which is supported by reliability methodology) on the existing system to extend its life and reduce the overall maintainability cost.
IADC/SPE 178776
Drill Pipe Makeup Torque – It’s Not What You Think! N.F. Zenero, Chesapeake Energy; W. Schneider, Pason; S.R. Koneti, T H Hill Associates
Objectives/Scope: Declining marginal profits demand that operating companies and drilling contractors review their practices and examine ways to optimize processes and reduce unplanned expenditures. One area that has been largely overlooked is iron roughneck makeup torque. Until recently, most iron roughnecks had no manufacturer’s recommended method to field-verify their accuracy and no way to digitally record or transmit the torque applied to one or more connections. This has undoubtedly resulted in unnecessary expense from lost and damage drill pipe and other downhole tools. The economic impact of the problem is significant and warrants structured, collaborative approach a solution. Methods, Procedures, Process: In mid 2014, a collaborative group, including an operator, a drilling contractor and multiple vendors and OEMs, began the first parts of the six-sigma DMAIC cycle to improve makeup torque. The effort involved the manufacture of a fit-for purpose tool to measure applied torque and an exhaustive study of multiple makes, models, contractors, operators and operating conditions. Results, Observations, Conclusions: The results of the study demonstrate that the process of making up drill pipe with iron roughnecks is uncontrolled (from a statistical perspective). It is also shown that the tools, as they currently exist, deviate significantly from customer defined process capability. Novel/Additive Information: Further study is required to address all the common and special cause variations in the process. Moreover, OEMs, contractors and vendors must work together to implement process controls.
IADC/SPE 178864
An Instrumented Topdrive Sub System: Enabling Greater Drilling Efficiencies via Innovative Sensing Capabilities. T.M. Bryant, APS Technology
Objectives/Scope: While innovations and advances in drill rig and downhole drilling technology have enabled operational efficiencies and productivities far beyond that achieved even a decade ago, most rigs today still lack suitable instrumentation that can be utilized to achieve a higher level of drilling performance. Operating with the disadvantages associated with inadequate, inferior, sometimes poorly maintained, and often uncalibrated rig sensors, these rigs are unable to obtain the efficiencies increasingly being demanded by operators and owners. To address this situation, a single point of service has been developed that contains a suite of surface rig sensors for acquisition of measurements essential for operations such as drilling optimization. These sensors, housed within a surface sub, include block height; drillstring tension, torsion, bending moment, bending angle, and rotation speed; mud flowrate, density, pressure and temperature; and drillstring vibrations. The sensor measurements are direct, calibrated, acquired simultaneously at user-configurable sampling and recording rates, and possess degrees of accuracies well beyond those of standard rig instrumentation. Methods, Procedures, Process: Using aerospace, medical, industrial and proven oilfield technologies, such as laser rangefinding and thin-film strain gages, an instrumented sub system was developed to provide for direct acquisition of the most critical measurements required for drilling optimization. The sub was designed to be located at the top of the drillstring. Primary design considerations included high accuracies of measurements, with traceability of calibrations; simultaneous acquisition of all measurements; preservation and extension of battery life via sophisticated sensor and battery management; very low bit error rates and robustness of radio telemetries; and ease of use tied to flexibility of user customizations. Results, Observations, Conclusions: Early and limited testing of the system indicates accuracies of measurements of hookload, torsion, bending moment, rotation speed, pressure and temperature to be in the range of 1 to 2% or better. While characterizations of accuracies for the laser-derived height measurement, volumetric flowrate, and mud density are in the process of being determined, these measurements are innovative and enabling with respect to the unique location in which they are sensed. Assessment of the accuracy of all sensors is intended to be ready in time for inclusion in the manuscript. The acquisition of synchronous measurements facilitates and enhances processing, manipulation and ultimate interpretations of mixed data. Data are telemetered wirelessly from the sub to a surface-based computing and display device. Novel/Additive Information: Uploadable standard and configurable tasking tables allow the user to fine tune the sampling frequency, averaging, and frequency of transmission of each individual sensor, and to characterize, as desired, these differing schemes as particular activities. Via operations designed for minimization of power draw, the rechargeable battery pack provides electrical power for extended periods of time without the need for frequent replacement.
IADC/SPE 178775
Offshore Drilling Improvement Through Automating the Rig State Detection Process – Implementation Process History and Proven Success. G. Lima, C.A. Zank, A.F. Costa, H.M. Mendes, L.F. Henriques, M.R. Mocelin Junior, PETROBRAS PETROLEO BRASILEIRO S.A.
Objectives/Scope: A rigorous initiative was undertaken in Brazil 3 years back to identify invisible lost time with the objective to improve safety and performance of the pre-salt drilling program. Methods, Procedures, Process: This was only possible by combining the following (explained in detail in the paper): •Rigorous drilling data quality assurance and recording. •Use of automation to correctly identify the rig state using a proven known product. •Using an appropriate commercial algorithms and web reporting systems to clearly help analyze the results on both safety and invisible lost time. •Building a team of performance engineers to analyze and work with the contractor to help identify areas of safety and performance improvement – the data shows that these two items go hand in hand. A safe crew works consistently well that directly affects performance. •Constant re-training and interacting with contractors to ensure that they get to see and understand the variability in their routine operations and perform route cause analysis with the aid of the automation tool. Results, Observations, Conclusions: Among many of the examples presented in the paper will be one on weight to weight connection time of an entire fleet of rigs (23 rigs) that reduces in 17% inform 2012 to 2014 through the elimination of unnecessary reaming (that wasn’t clearly measured before this effort). Also the variability among contractors is 50% in a wellbore conditioning time per connection that is a huge difference when comparing how similar these operations really were. The paper will also present actual total savings considering several KPIs of about 252 offshore rig days that translates in more than a quarter of a billion dollars. Novel/Additive Information: The conclusion is that a lot can be saved by combining automation, processes, and management commitment at the appropriate mix level – just throwing money at problems isn’t necessarily the solution.
Cementing and Zonal Isolation
IADC/SPE 178768
Engineered Solutions to Address Deepwater Remedial Cementing Challenges. G.A. Fuller, S. Mercado, Shell International E&P Co.; C. Mead, Shell International E&P
Objectives/Scope: Performing cementations in a deepwater environment poses many unique challenges during the drilling and completion operational phases in the Gulf of Mexico. These challenges add further difficulty and risk to an already complex operation. Methods, Procedures, Process: During the course of constructing the wellbore, it may be necessary to perform unscheduled remedial cementing operations to acheive the main objectives. Squeeze Cementing performed to remediate undesireable well conditions which may have resulted during the drilling phase (i.e. major mud losses) or as a result of a poor primary cement job (i.e. insufficient zonal isolation) must be thoroughly investigated to understand all the critical parameters needed to execute the right plan. Results, Observations, Conclusions: When designing for a squeeze job, key decision factors during the planning process must be addressed for a successful outcome. The success or failure of a squeeze cement operation relies on 1) understanding what is the objective of the squeeze operation 2) determination of the optimum cement placement depth, 3) development of an effective placement procedure with proper technique and down-hole tools employed, 4) proper design of cementing fluids, 5) flawless execution with a detailed pressure/rate/volume record of fluid injection, and 6) a meaningful post evaluation of the squeeze operation’s results to determine if objective was met. Novel/Additive Information: This paper will provide guidance on addressing the key decision factors, development of a proper placement strategy, general design guidelines for appropriate cementing fluids to employ, and how to evaluate if the objective was met. Results will be presented from recent deepwater case histories to illustrate the successful application of this methodology for squeeze jobs and the techniques used.
IADC/SPE 178840
Cement Placement with Tubing Left in Hole During Plug and Abandonment Operations. J. Sorbo, Int Research Institute of Stavanger; B. Aas, Intl Research Inst of Stavanger; A. Saasen, Det Norske Oljeselskap ASA; R. Godoy, Statoil ASA; O. Lunde, ConocoPhillips; H.I. Olsen, Wintershall Norge A/S; J. Mo, Lundin Norway; T. Vralstad, SINTEF
Objectives/Scope: Well abandonment operations can be very time-consuming and costly, and thousands of wells need to be permanently plugged and abandoned offshore Norway during the upcoming years. One possible solution to reduce costs during P&A operations is to leave the tubing in hole, as this would save significant rig time. However, a major concern with such an approach is whether the cement can be properly placed in the annulus due to the lack of tubing centralization. In this paper, we demonstrate by full-scale experimental tests that it is possible to obtain good cement placement when tubing is left in hole. Methods, Procedures, Process: Several cement displacement tests have been performed in full scale inside 9 5/8-in/ casings and 7-in. tubings, where some of the tubings where equipped with control lines. The cement was pumped using conventional equipment by one of the major cementing companies. Tubing collars and control line clamps provided the only means for centralizing the tubing. For comparison, both neat Portland cement and an expandable cement system were used. The quality of the cement placement was verified by pressure tests with different fluids and by visual inspection after cutting. Results, Observations, Conclusions: The results show that cement was properly placed inside and outside the tubing for all tests, but pressure tests indicated presence of microannuli when neat Portland cement was used. No significant microannuli were detected when expandable cement was used. It can therefore be concluded that it is possible to obtain a good seal after P&A when tubing is left in hole. Novel/Additive Information: The paper reports in detail full-scale experimental results. These findings can have significant value for operators and service companies when planning P&A operations. Furthermore, these findings and conclusions can serve as input to P&A guidelines and to change governmental regulatory requirements which today does not accept tubing left in hole in most of the North Sea area.
IADC/SPE 178772
New Approach In Lifting Cement In Highly Depleted And Naturally Fractured Formations. R. Diarra, J. Carrasquilla, S. Shwayat, Schlumberger; R.A. De Napoli Flensborg, Apache Corporation
Objectives/Scope: The problems associated with lost circulation during drilling and cementing need no introduction. Ultimately, they are costly in remediation and/or fines from regulatory agencies. This paper presents how moving the use of an engineered loss circulation material (LCM) from the spacer to the cement slurry itself helps providing tailored treatment delivery to the thief zones while cementing a well under loss circulation conditions. Methods, Procedures, Process: Traditionally losses prior to, or during, cementing operations are addressed primarily by loss circulation pills that are placed ahead of the lead slurry. Such pills are normally small in volume compared with the loss interval and may bypass the loss zone before the losses occur. They may also pose a challenge for correct cement slurry placement if they are too viscous, impacting the frictional hyerarchy. The solution being presented consists of using the cement slurry as the carrying fluid along with an inert solid package. A fiber is added on-the-fly to boost the plugging efficiency especially in naturally occurring fractures. The on-the-fly addition of the fibers allows a job design tailored to the well conditions any time prior to pumping. Results, Observations, Conclusions: The results are tangible, with the solution applied successfully in over 300 treatments in the Permian Basin, for multiple operators. In one of the oldest basins in the world characterized by highly depleted reservoirs and a complex lithology, such performance is unprecedented. The predictability of the results has allowed operators to comply with local regulations without incurring any remedial work, and has extended the life of the completion across highly corrosive formations. In spite of this progress and the encouraging results, additional optimization of the solid package and fibers can potentially improve the performance even more. The end results will be an improved understanding of how the LCM affects the rheological properties of the fluids coupled with improved the fluid placement. Novel/Additive Information: The methodology proposed is applicable for loss circulation cases in highly depleted zones and naturally fractured formations in other basins. Tangible results have proven the efficiency of the approach.
IADC/SPE 178876
The Anatomy of High Performance Float Equipment and Potential Failure Modes. D.B. Farley, I.A. Barannikow, B. Bourg, Weatherford
Objectives/Scope: Currently, float equipment performance is loosely defined by the recommended practices in API RP10F. With newly proposed API 10F standards, the industry has recognized the need to better define the performance properties of float equipment by refining performance characteristics for flow endurance, temperature and back pressure. However, this much needed and improved specification does not address drillability, reverse flow, and plug-bump ratings. Float equipment comes in a variety of configurations, including conventional poppet float and flapper valves, and numerous methods of flow- and ball-activated auto-fill equipment used to either increase trip speed or reduce surge pressure on the formation. Methods, Procedures, Process: This seemingly simple technology has highly engineered nuances that may not be readily apparent. The careful balance of flow endurance, high pressure resistance, and debris tolerance while still maintaining quick drillout properties has been achieved through many years of refinement and testing. Even the concrete used in the manufacture of float equipment is highly engineered to provide ultrahigh compressive strengths and shear bonding, which not only creates a drillable product but produces a seal between the steel hull and the valve. If these nuances are not clearly understood, the selection of high-performance, cost-effective float equipment can be compromised, leading to remedial intervention, poor cement placement, and added drillout costs. More importantly, poor cement placement reduces well integrity. Results, Observations, Conclusions: Failure modes are often attributed to design flaws or manufacturing errors and in some cases this is accurate. But a detailed understanding of performance properties and accurate compressibility calculations can mean the difference between allowing sufficient flow back and recording a float failure. Pipe management and standardized cementing practices are also important to success. Novel/Additive Information: This paper will explore the design practices and manufacturing methods for various types of float equipment and the need to dovetail the newly proposed API 10F standards and future iterations into the selection criteria for cost effective, reliable float equipment. This discussion will also review case histories of reported float failures and the root causes behind these incidents.
IADC/SPE 178886
Design and Performance of APB Mitigation Techniques- A Unified Approach. U.B. Sathuvalli, A. Gonzalez, A. Gupta, P.V. Suryanarayana, R.M. Pilko, Blade Energy Partners
Objectives/Scope: To ensure integrity, deepwater wells may use Annular Pressure Build-up (APB) mitigation devices. Type I mitigation techniques control APB by reducing lateral heat loss from the production tubing to the wellbore. Type II techniques work by controlling the flexibility (psi/°F) of an annulus by modifying its contents and boundaries.Though the physics of APB mitigation is well understood, the reliability of a mitigation strategy or its interaction with other parts of the wellbore is not always quantifiable. This is partly due to lack of a unified approach to analyze mitigation strategies, and partly due to lack of downhole data after well completion. Simply stated, the engineer is hard pressed to find computational-predictive methods to assess alternative scenarios and strategies within the framework of the design basis during the life of the well. Methods, Procedures, Process: In this light, our paper has two goals. First, we review 21 APB mitigation techniques that have been conceived, tested and/or tried. We evaluate the suitability of each method with respect to field installation, downhole performance and reliability during well-life. Historically, the most successful mitigation strategies include rupture disks, solid syntactic foams, nitrified gas-caps and vacuum insulated tubing. More recently, gas-laden fluids, hollow glass spheres fabricated to crush, buckle or compress at predetermined pressures, downhole pressure compensators based on mechanical actuators, shrinking polymeric fluids and tools to access the wellhead via ROVs have been proposed and/or tried. Also, special muds with settling-resistant solids that cannot clog an open shoe have been suggested. Our second goal is to present a unified quantitative approach to design mitigation strategies and to establish a rational basis for comparing them. Results, Observations, Conclusions: Irrespective of the technique used, the design involves identifying a “pre-determined operating point” at which the mitigation strategy is activated. The design is linked to the notion of “allowable APB” in an annulus, which in turn, is tied to the design of the casing strings, and thus to wellbore integrity. Since Type I strategies suppress convection in Annulus A and/or increase the resistance of the tubing to conduction, their design is a intimately linked to the heat exchange at the tubing and the flow character of Annulus A fluids. Type II strategies are based on the pressure-temperature response of a given annulus and the mitigation device & the pre-determined operating point. Determination of this operating point and the design basis involves judiciously chosen thermal and APB sensitivity analyses. These principles are illustrated with appropriate models and examples. Novel/Additive Information: The paper aims to provide the industry with the knowledge to analyze, compare and select APB mitigation techniques applicable to an operator’s well and field situation.
IADC/SPE 178793
Development of Geopolymer-based Cement Slurries with Enhanced Thickening Time, Compressive and Shear Bond Strength and Durability. S. Salehi, University of Louisiana at Lafayette
Objectives/Scope: The primary objective of this work is to investigate through laboratory experiments geopolymer-based cement slurries with enhanced properties such as suitable thickening time, high compressive and shear bond strength and durability in severe conditions. Methods, Procedures, Process: A set of experimental matrixes were designed for three circulating temperatures of 150°F, 200°F and 250°F. Each matrix included various mix designs based on change in Alkaline/Geopolymer ratio, molarity of Alkaline, Alkaline/Silicate ratio and amount of retarder/super plasticizer added. A set of different experimental modules including compressive and shear strength, thickening time; shrinkage and SEM were utilized for this research. Results, Observations, Conclusions: Class H cement sample was used as control mix in comparison to geopolymer mixtures. On average geopolymer mixes achieved 1800 psi compressive strength in 24 hours and more than 2500 psi after 48 hours (Figure 1). Optimizing thickening time was challenging. Results indicated strong adverse effect of molarity and Alkaline/Silicate ratio on thickening time. With optimization of testing matrix, more than four hours thickening time (considering 70 BC) was achieved for optimized mixes in all the three temperatures (Figure 2). In higher temperature (250°F), geopolymer slurry reacted very fast where up to 3% of organic based retarder was used to achieve suitable thickening time (4 hours). Shear bond strength tests results showed significant enhancement in the shear bond strength compared with strength of class H cement (up to three folds increase). This reached an optimum peak at Alakaline with molarity of 10 used in mixes (Figure 3). SEM results showed formation of early gels at this molarity (Figure 4). A more ductile material behavior and higher fracture toughness were observed for optimum geopolymer mixes. Final observations confirm applicability of these materials for oil and gas well cementing with circulating temperatures up to 250°F. Novel/Additive Information: Previous research on application of geopolymers in oil/gas wells was mainly unsuccessful due to failure to achieve a reasonable thickening time. The study here presents geopolymer slurries that have high compressive strength and shear strength, enhanced thickening time and high durability. Slurries developed in this work are durable when prone to sulphate/chloride or any other acid attack that might be encountered during cementing operations.
Performance Drilling
IADC/SPE 178850
True Lies: Measuring Drilling and Completion Efficiency. J.P. de Wardt, DE WARDT & CO.; H.J. Kile, Wellpro AS; P. Rushmore, Rushmore Reviews; P.W. Scott, Technical Limit Engrg.
Objectives/Scope: Drilling efficiency is an often used term for various measures that purport to represent the relative difference between current performance and some reference performance. Non Productive Time (NPT) is globally used as an analogue for efficiency. Many reported efficiency measurements are in the 90% range and NPT in the 20% range when the overall drilling and completion times are some 50% or slower than best in class. Current measures of drilling efficiency and NPT are both misleading and poorly defined. This paper will evaluate these misleading measurements and describe the development of a real measure of drilling efficiency. Methods, Procedures, Process: Means to estimate overall performance potential including Technical Limit (TL), Theoretical Maximum Performance (TMP) and benchmarking will be explained in their historical context and current applications. These provide the future state target for gap analysis to current state performance. This gap allows the quantification of Invisible Lost Time (ILT) whose reduction is the means to true performance improvement over deficiency correction as measured by NPT. ILT commonly gets included in Productive Time (PT) as logged in daily report data-base systems and can remain invisible without such a gap analysis. It is as important a measure of performance efficiency as both NPT and the often used ‘uptime’ of a drilling rig. Measurements of industrial process (construction, manufacturing) efficiency will be presented and, through analogy, applied to drilling. The result will be a robust methodology for the industry to measure drilling efficiency. A simple and comprehensive well complexity index methodology will be described that can be applied to adjust the calculated time estimation and TMP to each well operation to reflect the opportunity and where to look for improvements to target 100% performance. An approach to establish an international benchmark complexity index for drilling will be described. Results, Observations, Conclusions: A drilling efficiency model and calculation method will be available for the industry to measure the real gap to 100% efficiency. This will in general produce vastly lower efficiency numbers for current performance than some of the inappropriate efficiency calculations currently used. It will provide organizations with a more accurate view of the improvement potential they could aspire to reach, and become an enabler for the global oil and gas industry to improve and reduce cost of wells. Novel/Additive Information: The recommended methodologies and efficiency measure will provide the first realistic number for drilling efficiency. It will be a wake-up call to the industry and initially show much lower efficiency numbers than many organizations currently calculate and report. It will be an eye-opener to managers who want to truly assess the performance of their drilling operations and provide them the information to set new performance goals.
IADC/SPE 178888
Stuck Pipe Prediction Using Automated Real-Time Modeling and Data Analysis. K.P. Salminen, C.A. Cheatham, Weatherford International; M.A. Smith, Weatherford Drilling
Objectives/Scope: A real-time method is presented to predict impending stuck pipe with sufficient warning to prevent it. The new method uses automated analysis of real-time modeling coupled with real-time data analysis. It can be applied to all well types for any well operation including drilling, casing running, completion activities, and re-entries. The method uses leading indicators of stuck pipe that were identified using historical data sets of 27 stuck pipe incidents in the Eagle Ford, Utica, Permian, and Gulf of Mexico. Five case histories show the utility of the new method in four shale horizontals and one offshore well for both drilling and casing running operations. Methods, Procedures, Process: The new method combines two types of analysis: (1) deviation of real-time data from real-time model predictions using hydraulics and torque and drag software, and (2) trend analysis (i.e., rate of change) of real-time data. Parameters used are pump pressure, flow rate, torque, rotary speed, hookload and drag, weight on bit, rate of penetration, and gamma ray along with static inputs such as BHA and drillstring configuration and directional surveys. Additional parameters such as downhole ECD are used when available and improve the results. But the method is designed to monitor all well types and provide a stuck-pipe-risk log even using only basic instrumentation. A novel algorithm predicts the probability of stuck pipe which is presented in a real-time log. Results, Observations, Conclusions: Results demonstrate there is no single leading indicator present in all stuck pipe incidents. Consequently, relying on a single specific pattern (such as increasing pump pressure at constant flow rate) leads to inability to predict stuck pipe in some cases. Our early detection method relies on multiple indicators to strengthen the likelihood of detecting an increase in stuck pipe while avoiding false alerts. Deviations of parameters from model predictions have been used with success in the past by experts but the new method provides contextual awareness and provides thresholds that automate the process. A key element is the use of filtering for rig activity. Rate of change calculations provide valuable insight into rapidly deteriorating wellbore conditions when deviation from model predictions does not respond quickly enough over a short depth or time interval. The figure below shows an example from the historical data set used to train the method. The stuck pipe risk increased from low to high over about a one-hour period, which would have been sufficient time to prevent the stuck pipe incident. Novel/Additive Information: The novelty of the method is real-time automation of the prediction of stuck pipe based on trend analysis and deviation of actual data compared to physics-based models. The result is presented in a real-time log for easy understanding and decision making.
IADC/SPE 178901
Use of Historic Data to Improve Drilling Efficiency: A Top-down, Data-driven Method and Trial. S.D. Kristjansson, Pason Systems Corp; S.W. Lai, Pason Systems Corporation; D. Tremaine, Axia NetMedia Corporation; J. Wang, Pason Systems Corp
Objectives/Scope: Despite the collection and storage of ever-increasing amounts of data on all aspects of drilling operations, few E&P companies or operators exploit the data’s full information content to optimize drilling practices. In this paper, we first present a new machine learning method that uses historic, surface-based sensor data from group offset wells to guide drilling parameter settings for the next well to be drilled. The algorithm is designed to automatically select drilling parameter settings from the offset wells that are associated with both improved drilling speed, defined as on-bottom rate of penetration (higher ROP) and drilling efficiency, defined as mechanical specific energy (lower MSE). We also present results from a trial of the new method. Methods, Procedures, Process: We selected, as offsets, a group of eight land-based wells that were similar in geometry, were drilled in the same formations and used similar bottom-hole assemblies (bit sizes and mud-motors). We extracted (at 0.2m resolution) depth-based measurements of ROP, MSE, revolutions per minute (RPM), torque, weight on bit (WOB) and differential pressure (DP) from a historic database. The algorithm identified, simultaneously, the depth intervals and drilling parameter settings (WOB, RPM, DP) that were associated with optimal drilling outputs (ROP, torque, MSE) from among all available offset data. The depth intervals defined by fast and efficient drilling (and the associated drilling parameters settings) were selected to build a drill plan for the trial well. The drill plan comprised a set of recommended parameter settings (i.e., reference traces) that were displayed on the driller’s EDR. Separate drill plans were created for surface, intermediate and lateral sections. Results, Observations, Conclusions: Results indicated that the drillers followed the drill plans, and compared to the offset wells, better rates of penetration were achieved in each section of the trial well. Specifically: i) for the surface section, the average ROP was 47.9m/hr in the best offset and was 52.4m/hr in the trial well (~9% increase); ii) for the intermediate section, the average ROP was 28.4m/hr in the best offset and was 31.3m/hr in the trial well (~10% increase); and iii) for the lateral section, the average ROP was 35.4m/hr in the best offset and was 40.1m/hr in the trial well (~13% increase). Further, the trial well’s lateral length exceeded that of the longest offset well by 298m. Novel/Additive Information: This paper is novel because it demonstrates that a machine learning algorithm that simultaneously considers drilling outputs, drilling inputs and hole depth can extract hidden information in large historic data sets, and this information can be used to significantly improve drilling performance and cut cost.
IADC/SPE 178842
Method for Pore Pressure Estimation Using Mechanical Specific Energy and Drilling Efficiency. R. Majidi, M. Albertin, N.C. Last, BP
Objectives/Scope: Prediction of formation pore pressure and real-time detection of the pore pressure to recognize deviations from the expected pressures, is crucial in terms of the cost and safety of drilling operations. A method is proposed to determine pore pressure from a combination of downhole drilling mechanics parameters and in-situ rock and stress data using the concept of mechanical specific energy (MSE) and drilling efficiency (DE). This pore pressure estimation method (termed as DEMSE) is based on the theory that energy spent at the bit to remove a volume of rock is a function of the differential pressure (i.e. wellbore pressure – pore pressure) that the rock is subjected to during drilling. Methods, Procedures, Process: A work-flow is provided that illustrates the steps needed to be taken to convert drilling parameters and rock/stress data into pore pressure estimates. Pore pressures predicted using this method are tested against post-drill pore pressure interpretations made using conventional pore pressure prediction techniques such as sonic-derived pore pressure for a deep water well in the Gulf of Mexico. Pore pressure estimates from the DEMSE method generally agree in magnitude and trend with the pressure estimates derived from sonic log data. Results, Observations, Conclusions: The results of this method have also been compared with pore pressure estimates from the classical d-exponent (dXc) methodology; Unlike the d-exponent methodology which is an empirical correlation that considers only weight on bit (WOB), DEMSE is an energy based approach that takes into account both torque and WOB. Moreover, the normal compaction trendline (NCT) used in the DEMSE method can be correlated to a normal compaction porosity trendline; the same NCT used for most log-based pore pressure estimates. This gives a significant advantage over the dXc method, in terms of predictive capability, by reducing the subjectivity that is involved in dXc-based pore pressure estimates. Novel/Additive Information: Finally, the importance of use of downhole vs. surface data for pore pressure estimation purposes, specifically at the bit torque measurements, is illustrated through a field example. These findings suggest that downhole drilling mechanics data, when properly utilized, can be used both as a reliable and independent method for estimating pore pressure in real-time at the bit (while drilling), and for post well analysis to assist with constructing pore pressure forecasts.
IADC/SPE 178836
Repurposing Proven HSE Techniques For Use Outside Safety Reduces Non-Productive Time (NPT) and Improves Drilling Efficiency – A Case Study On Application Of “Chronic Unease” To Improve Drilling Quality..T.M. Redlinger, T H Hill Associates; M. Hurtado, TH Hill Associates; M. Wright, Shell
Objectives/Scope: Health, Safety and Environment (HSE) practices and regulations have been of paramount importance to the Oil & Gas industry for decades. Drilling operations represent a major HSE risk and therefore robust programs have been put in place by operators and service companies to minimize the risks and ultimately reduce incidents. The success and sustainability of these programs has been well documented with quantifiable results, but the techniques have been rarely expanded to other operational areas. This paper reviews the field application of these HSE techniques on other areas of drilling operations and describes the results of the implementation over several years. Methods, Procedures, Process: One of the HSE techniques used in this case study is described as “Chronic Unease”. “Chronic Unease” is a state of mind that has been successfully integrated into safety programs to build a methodology based on the recognition (detection) and reaction to weak signals that could potentially lead to significant events and therefore presents strong similarities with the early detection of drilling risks that could be prevented through quality programs. Results, Observations, Conclusions: This paper re-introduces the concept of “Chronic Unease” and presents how it can be mapped to Quality Assurance and Quality Control techniques in drilling operations. Novel/Additive Information: The paper includes the field application of other HSE techniques and describes the results of the implementation over several case studies in offshore drilling operations. Ultimately the case studies illustrate a correlation between drilling efficiency and the successful re-purposing of proven HSE techniques.
IADC/SPE 178784
Enhanced Extended Reach Well Design in Saudi Arabia Leads to Optimized Drilling Performance and Significant Cost Reduction. G.A. Munoz, P. Balseiro, B.N. Al Dhafeeri, A.S. Baim, Saudi Aramco D&WO
Objectives/Scope: Saudi Arabian Oil Company (Saudi Aramco) operates one of the principal high profile extended reach drilling (ERD) projects in the world. This is accomplished by the development of a sizable number of horizontal wells categorized according to the total depth. Wells with the shortest vertical displacement have been significantly optimized during the project execution thereby minimizing room for enhancement. The drilling engineering team conducted a comprehensive evaluation of the existing casing scheme and problematics along the M field. A new approach was devised to redesign wells with a total depth up to 17,600 ft. The aim was to achieve a substantial improvement in drilling performance and potential savings for the remainder of the project. Methods, Procedures, Process: M-L1 and M-O1 wells were selected as candidates to implement the novel alternative; both to be drilled from different platforms where several wells have been previously completed using the conventional design. Drilling troubles, such as loss of circulation and hole instability, occurred during the execution of such wells leading to major lost time. The solution comprised the optimization of the well trajectory, slim-down the upper hole sections and combine the lower ones, drill longer intervals and set casings deeper to cover problematic zones without compromising the well integrity. The detailed engineering study included a probabilistic analysis to evaluate the economic viability of the landmark application. Results, Observations, Conclusions: Two wells were successfully drilled and completed applying the downsizing strategy. The impact of anticipated challenging events in both 12-1/4-in. and 8-1/2-in. holes was decreased as a result of the new design. The implemented preventive plans led to a rapid elimination of encountered challenges. This optimization produced a 26% reduction in drilling time, and minimal non-productive time (NPT) with associated cost savings of 20% compared to a large hole string design. Novel/Additive Information: Finally, this new approach in a still ongoing project along with the feasibility of extend it to other areas will lead to potential improvement in well delivery and operating cost.
IADC/SPE 178828
Pipe Sticking Prediction Using LWD Real-time Measurements. J.M. Hess, Baker Hughes
Objectives/Scope: In addition to formation evaluation, logging-while-drilling (LWD) measurements can also be used as a real-time solution to issues that arise during the drilling process. For example, LWD measurements can be interpreted to help determine if increasing mud weight would be useful, if you should slow down the rate of penetration (ROP) because you are entering a pressure zone, and other drilling considerations. What if measurements made with LWD tools could help predict whether or not your drillstring will become stuck while drilling? This paper describes a model that was created to predict situations with high risk of the tool becoming so they can be addressed during the planning phase as well as the execution phase. Much like an experienced person, the model learns, or builds on each job experience, to improve future decisions. Methods, Procedures, Process: Most experienced individuals directly involved in the drilling process understand the different ways that a drillstring can become stuck and factors that contribute to it becoming stuck. Many different variables are commonly attributed to causing a drilling bottomhole assembly (BHA) to become stuck during drilling operations. This paper explains the variables that were used in the model and why they were used. Some measurable variables are wellbore characteristics, BHA characteristics, downhole pressure and temperature, drilling practices, and mud properties. These variables were gathered from old wells drilled in years past on the GOM shelf from 42 wells. More specifically, the information was gathered from end of run reports, annular pressure logs, LWD databases and surveys. Results, Observations, Conclusions: After the model was created, the model was tested against seven additional GOM shelf wells. The model predicted correctly that in three of the seven wells the drillstring would be permanently stuck. In another three of the seven the drillstring was temporarily stuck while the model claimed it would be permanently stuck. In the final well the model predicted that the drillstring should be stuck, while it was not; however, the client made decisions while drilling the section which indicated that they were fearful of getting stuck. Novel/Additive Information: If it can be shown that there is a risk of the drillstring becoming stuck in a well, preventative as well as after-the-fact measures can be used to adjust the mud system and other drilling parameters. Additionally, fishing services can be prepared early or even moved to location earlier to cut down on non-productive time (NPT). A model such as this provides an indication of the need to try preventive measures to mitigate the situation before the problem occurs, or at a minimum provides additional time to take the best course of action.