Fit-for-purpose testing, improved handling techniques, better use of well data among innovations for sour-gas well completions
Technology development keeping pace with increasing activity in mild sour environments, deeper well depths, evolution of rig designs
By Kelli Ainsworth, Editorial Coordinator
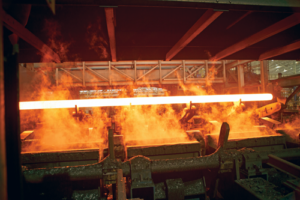
Each year, corrosion costs the oil and gas industry an estimated $1.32 billion, according to NACE International, a global organization focused on corrosion control.
At a time when the industry is doing everything possible to cut costs, it’s critical to implement solutions during sour gas completions that minimize or eliminate the potential for corrosion. In speaking with several service and equipment providers, DC found that they are focused on delivering optimized sour-service materials for tubing and casing, and on handling systems that will not damage these materials and leave them vulnerable to corrosion.
Companies also continue to work with operators to adapt existing technologies for sour-gas environments.
Sour-service materials
Today’s wells are challenging casing and tubing manufacturers to increase the yield strength of their materials without compromising their H2S resistance, said Heather Byers, Technical Sales Manager for Vallourec. “H2S reacts less severely with lower-strength grades, so the lower the yield strength, usually the better H2S resistance,” she said. “But because of how deep drillers are going these days and the pressures, temperatures and longer laterals they’re seeing, they need as high a strength as possible.”
When yield strength is increased, the material tends to get harder and more brittle, making it easier for H2S molecules to penetrate the steel. Vallourec is increasing the yield strength of its tubing and casing without increasing hardness through proprietary chemistry and a proprietary quenching process, during which the steel is rapidly cooled down after being heat-treated.

The company’s VM110 SS is a high H2S corrosion-resistant alloy steel with a 110-kpsi yield strength that has been used in high-pressure, severe sour environments in the deepwater Gulf of Mexico, Ms Byers said. The VM125 HCSS sour service-rated steel alloy has an even higher yield strength, at 125 kpsi, as well as increased collapse resistance above API requirements. High collapse resistance casing is often used when reservoir pressure is expected to be high. “It’s a much higher-strength product,” she said. “You don’t usually see a 125 yield strength product that also has sour-service capabilities because those higher strengths are usually susceptible to H2S.” Both of these products meet all NACE qualifications and standards, according to Vallourec.
In mildly sour environments like parts of the Eagle Ford, such robust, high-grade products are typically not needed. “When 2013 and 2014 hit, people were just trying to drill everywhere they could and were coming up on these mild sour environments onshore,” Ms Byers said. “We started seeing a need for a cost-effective solution because onshore margins are slimmer, but operators still needed that mild H2S resistance.”
As a result, the company says, it has seen increasing demand for its P110MS products, which were first developed in 2006 and provide a 110-ksi yield strength and mild sour-service capabilities. As these products are not expected to perform in severe sour environments, they are not tested to the strictest NACE requirements. A NACE Series A test is still performed at a 90% actual yield strength stress level. However, the concentration of the testing solution is lower and has been modified to mimic a mild sour environment. Like standard NACE A tests, this modified test is performed for 720 hours.
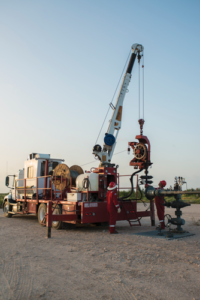
NACE classifies sour service into three regions, with Region 1 being the least sour and Region 3 being the most. The regions are determined by the pH and H2S partial pressure of a given area. For wells that lie within Region 3, NACE recommends a very high sour-service grade material, such as API grade T95. However, condition-specific testing might reveal that the operator could use a less robust grade, Ms Byers said.
“If you go straight with these NACE charts, they might tell you that you need a robust and expensive material to combat H2S, where we can suggest a lower-grade material that fits the specific conditions of an operator’s well.”
Increasingly, Vallourec has been performing more of this fit-for-purpose testing to determine the best material solution for operators. Conditions that can be factored into the testing include H2S content, temperature, pressure and stress among others. “Operators are targeting specific conditions, which can result in a more optimized and cost-effective solution for their wells,” she added. “Only using the material that you really need, instead of spending extra money on a product that’s more than you need, helps with costs.”
Handling with care
Once operators have selected the right material for their casing and tubing, these materials can still succumb to corrosion if they’re handled improperly. “You must make sure that minimal damage or, better yet, no damage is done to the tubulars because as they are subjected to corrosive environments. Damage done during handling can accelerate the failure of the tubular,” Jeremy Angelle, Senior Vice President of Technology and Engineering at Frank’s International, said.
“When the handling equipment grips a tubular to hoist it, support it or make a connection, the gripping inserts often leave bite marks in the tubular. In a non-corrosive environment, this usually isn’t a problem,” Mr Angelle said. “However, in a sour well, these bite marks can succumb to stress corrosion cracking or sulfide stress corrosion cracking. The resultant crack can quickly propagate through the tubular and cause it to fail with the potential for a catastrophic loss of well integrity.”
Tubular failures are not new to the global oil and gas industry and have been well documented. The industry has greatly increased its understanding of stress corrosion cracking and sulfide stress corrosion cracking and what causes the failures in sour-gas environments. At Frank’s International, the focus has been on understanding how handling techniques can contribute to cracking.
“We have a metallurgical lab here at Frank’s where we’re able to simulate the advanced stages of a corrosion cracking so we’re able to look at different equipment designs,” Mr Angelle said. “We know that the risk of corrosion failure is a serious threat to well integrity. And while these types of corrosion failures are quite complex, the key to reducing or, better yet, eliminating the risk of failure is proper handling from cradle-to-grave. This includes using truly non-marking technologies to eliminate bite marks and eliminate corrosion-inducing contamination of the tubular.”
Through its research, Frank’s International has developed and patented a fully non-marking handling system for corrosion resistant materials. This system includes the Collar Load Support (CLS) system and Fluid Grip handling technology. The CLS system picks up a joint and suspends it in the derrick, while the Fluid Grip technology uses a urethane-pressurized bladder to make up the connection via friction. Once the connection is made up, the CLS lowers the string into the well.
Adjustments to CLS and fluid grip technology must be made routinely to keep up with industry trends, particularly as wells become deeper. “We’ve had to continually evolve to accommodate bigger diameters and heavier string weights as the result of deeper wells,” Mr Angelle said.
The evolution of the CLS has also been driven by the evolution of drilling rigs. The latest version of the system was released in late 2015 and was designed to be easily installed on land rigs in various parts of the world where sour wells are common. R&D for future generations of handling equipment will focus on making it compatible with the rig of the future. “We’re looking at automation as a tool to drive efficiency, and we’re looking at automation to increase safety on the rig floor,” Mr Angelle said. “Our handling equipment fits into that strategic vision.”
The company believes it’s important to keep pace with innovations to drilling rigs because the need for non-marking equipment is likely to increase as the industry deals with more sour-gas wells. “We’ve done the easy wells, and we specialize in the more complex ones. Sour wells are becoming more common, and they’re becoming even more complex with the concentrations, the pressures, the temperatures and the well architecture,” Mr Angelle said.
Adapting old products to meet new needs
For service companies, one challenge that remains is educating operators on what sort of well data is needed in order to make recommendations for sour-service equipment design. “We have to make sure we get the right data from the customer upfront as far as the well conditions they’re expecting and what their tests have shown regarding H2S levels,” James Bracken, Global Business Unit Manager for Capillary Systems at Weatherford, said.
When operators don’t provide this information, it could be because they’re entering a field for the first time and simply don’t have a lot of data. It could also be that they are not be aware of what data are needed by the service provider. “It’s a business partnership between the service company and the operator, and if we act as business partners, then we can design and implement the best equipment,” Mr Bracken said.
Having this level of engagement has enabled Weatherford to adapt its Renaissance WCS system for a sour-gas well in 2014. The system was originally designed to replace subsurface safety valves in offshore wells. “The system enables Weatherford to put an insert into the subsurface safety valve and basically replace that valve with an operational valve,” Mr Bracken said. Subsurface safety valves can become worn out or cut as wireline or tools are run down the hole and through the valve. Wear or damage to the valve can prevent the valve from properly closing and providing a 100% seal.
The Renaissance WCS system can be run down the well to the valve. The valve’s flapper is locked open, and an insert containing a replacement flapper is locked into the valve. “This gives the operator an option of running down an insert and locking it into the profile,” Mr Bracken said. “Now they have an operational safety valve without the expense of bringing out a workover rig.”
Two years ago, an operator of a well that had high levels of H2S needed to replace a subsurface safety valve. While the Renaissance WCS system presented a way to restore operations without a rig, the standard system contained rubber seals that would not hold up in a sour-gas environment. Weatherford’s engineering team in Lafayette, La., tested alternate rubber seals through a flow loop at temperature. Weatherford was able to deploy the re-engineered system in the gas-producing Canadian well, which had a depth of 15,275 ft.
The industry will always have to grapple with sour gas wells, but technical improvements coupled with experience have enhanced safety and efficiency, Mr Bracken said. “If you went back 15 to 20 years ago and you said the words sour gas, it made a lot of people extremely nervous,” he said. “Now, if you manage the risk with your personnel and equipment, those wells are just like any other normal, everyday wells. They can be effectively completed, operated and maintained to provide a benefit to the operator and the industry for a long time.” DC