Shelf Drilling secures two-year contract offshore Nigeria
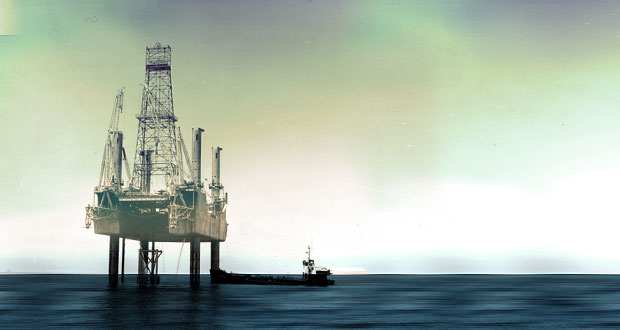
Shelf Drilling secured a two–year contract for the Shelf Drilling Scepter jackup for operations offshore
Nigeria. The contract value for the firm period, including mobilization revenue, is approximately $118 million. The contract also includes a one–year option, and the planned start–up of operations is
May 2023.