Tyler Smith, Nabors: IADC provides valuable space to share learnings, spark new ideas
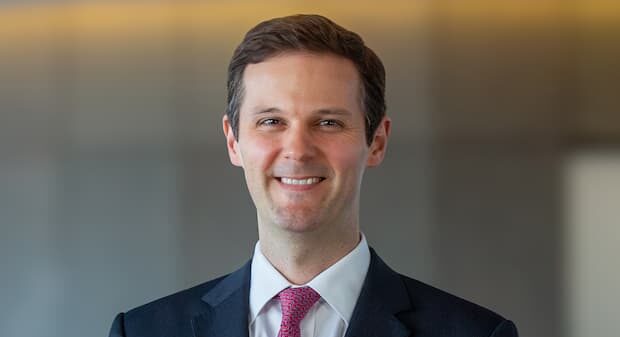
By Stephen Whitfield, Senior Editor
For Tyler Smith, Associate General Counsel at Nabors and Chairman of the IADC Contracts Committee, participating in IADC meetings provides an opportunity to learn more about the industry at large by interacting with people representing different companies. The discussions and ideas shared in those meetings allow the industry to continuously improve.
“The ideas we share just by attending the meetings provide different perspectives,” he said. “Sometimes it happens in the breakroom – maybe we say we’re having to adapt our contracts to account for the commercialization of our energy transition products. Just collaborating with people in this industry is very helpful, and I love bringing that back to my company.”
Not surprisingly, the law has been a huge part of Mr Smith’s life for about as long as he could remember. His father, a litigator who was once nominated to serve a federal judgeship, loved having discussions at home about all things related to the law. And even though he went to Rhodes College to study history, law school was always on the back of his mind. He took the LSAT exam in his senior year, and over the next four years he spent time as a Legislative Correspondent in the United States Senate and as a Judicial Intern in the Texas Third District Court of Appeals.
While attending law school at the University of Houston, Mr Smith interned at the US District Court for the Western District of Texas and at Brown Sims, a litigation firm. These experiences were valuable in helping him to figure out his career path – that he wanted to work in the private sector, and he wanted to work as an in-house counsel for a company rather than working for a law firm.
After graduating from UH Law School in 2013, Mr Smith joined Nabors as Contracts Counsel. It was his first foray into the world of oil and gas, and upon taking the job he started visiting rigs and taking training courses for various rig jobs to better understand the company’s core business.
From a legal perspective, Mr Smith had to familiarize himself with the specific types of contracts the company negotiated with its customers. Aside from dayrate contracts for the rigs, he also had to learn about various licensing contracts as Nabors began developing its own software systems, such as SmartROS and RigCloud.
“Of course, becoming familiar with the IADC Daywork Contract we use for land was important, but Nabors also has a completely different contract for offshore rigs, and then as you get into the software and technology side, you also have software license agreements. There’s a huge learning curve around the different risks I need to focus on, and it’s very dependent on what the commercial offering is,” Mr Smith said.
After five years as Contracts Counsel and five months as Senior Contracts Counsel, Mr Smith moved on to serve as Legal Counsel in July 2018. In October 2021, he was named Senior Legal Counsel. This role shifted him away from drafting and reviewing individual contracts into a general handling of the company’s securities-related matters. He handled Nabors’ reporting duties to the US Securities and Exchange Commission.
He also drafted the company’s proxy statements, which provide information for shareholders; handled the company’s legal matters related to SANAD, Nabors’ joint venture with Saudi Aramco launched in 2017; and oversaw the Nabors Enterprise Risk Management Committee.
In 2023, Mr Smith was promoted to his current position, Associate General Counsel.
Collaborating with industry
With all of these duties at Nabors, he gets to see a broad perspective of the company’s business offerings, which has been valuable in helping him fulfill his duties as Chairman of the IADC Contracts Committee, a role he took on in 2019. Conversely, the collaborative nature of the committee has helped him in his role at Nabors, as well.
“Companies can come to the committee meeting and share contractual issues they’ve had, and you can relay that information to your own organization and consider if you need to incorporate new provisions into your contracts to mitigate potential risks.”
Mr Smith said he also sees value for the committee through its work filing amicus briefs on behalf of industry stakeholders. Amicus briefs are statements filed by an organization that is not party to an ongoing legal case; they offer information or expertise that has a bearing on the case.
For instance, last year the committee filed an amicus brief in support of ExxonMobil on a case in the Texas Supreme Court addressing the extent to which insurers are entitled to refer to extrinsic contracts in interpreting the scope of coverage under an insurance policy.
Mr Smith also noted the value the committee has for smaller companies that might just have four or five rigs. “They don’t have the resources for big in-house legal departments, or even to hire big law firms to support them in these negotiations with operators. While we can’t give out legal advice to these members, we can provide a general interpretation of what the intent behind the provisions of the contract are, and I think that’s valuable.” DC