Industry looks beyond higher horsepower to amp up frac performance
Gun systems with increased configurability and better casing deformation prediction helping to unlock new efficiencies, while electric frac fleets still face adoption barriers despite ESG benefits
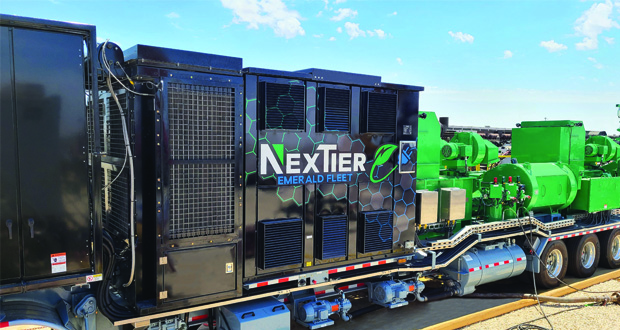
By Stephen Whitfield, Senior Editor
As with other sectors in the oilfield, hydraulic fracturing is all about pushing performance, and companies building new frac fleets and associated equipment must design them with performance in mind. Increased horsepower continues to be a top touted feature by frac service providers – where 2,500- to 3,000-hp trailers were once commonplace, newer systems, such as NexTier Completion Solution’s Emerald electric frac (e-frac) system, can feature up to 6,000 hp on a single trailer. But horsepower is not the only way to help improve performance in frac operations.
“You can only put so much horsepower down a 5 ½-in. casing; you can only get so much pressure. You can’t turn it up to 11 all the time, nor should you,” said Doug Taylor, VP of Digital Operations at NexTier. “Where the differentiators come in is in the reliability of the equipment we’re providing and in helping the operator to make real-time strategic decisions.”
Helping operators gain an edge in decision making means developing tools that can help them improve at the margins, whether it’s through savings in fuel costs, a reduction in emissions or mitigating the dysfunctions that can increase nonproductive time or lead to serious consequences downhole. For the service providers, this could mean improving on systems that are already in the market or creating new workflows to help them spot potential issues.
Whatever steps they are taking, the name of the game is to unlock new efficiencies in order to help operators maximize their frac performance.
“Basically, how are we going to get a tool out there that can help make these frac companies and these operators successful?” said Zach Wade, Senior Operations Manager at GeoDynamics, a technology developer that specializes in completions and abandonment tools. “These guys have a lot of labor going out to these frac sites, a lot of operations, a lot of trucks, a lot of trailers. They’ve got enough costs and logistics to manage. If we can go out there and give them the right tools, they’re making good margins and we’re making good margins.”
Challenges in e-frac adoption
With an increasing focus being placed on the industry’s carbon footprint, e-frac fleets have become a potentially valuable tool. These systems use electrically powered pressure pumps running on modular natural gas generators, instead of the diesel-driven pumps of a conventional frac system. The generators make electricity using CNG, LNG or field gas produced onsite that may otherwise be flared. This can lead to fuel savings and a carbon emissions reduction.
“With dual fuel, you’re always going to have some diesel associated with your operation depending on how you’re fracking the well, depending on how much equipment you have out there, and depending on what the customers require of some of the equipment,” said Ben Dickinson, VP of Strategy and Digital Development at NexTier. “The engine will use whatever natural gas versus diesel combination to operate in the most optimum way. So, there’s always going to be a range of diesel that’s going to be required. On the other hand, electric is fueled by 100% natural gas power-gen.”
While the carbon reduction potential is larger with e-frac fleets, the logistics and cost of building them make their adoption a trickier pill for operators to swallow. For instance, NexTier launched Emerald, its first e-frac offering in 2022, prior to its merger with Patterson-UTI in Q4 2023. However, as of February 2024, only one of NexTier’s active frac fleets is an Emerald fleet. The company expects to be operating around 140,000 electric horsepower by mid-2024. The majority of its fleets running are Tier IV dual-fuel fleets, which use a combination of diesel and natural gas-fueled engines to operate.
“If an operator wants to order a newbuild electric fleet today, it can be 12 to 18 months before it’s delivered because we have to build a package for it. Then on the electric side, it’s not as much a challenge on the equipment as it is a challenge on delivering the power generation. That’s an additional cost compared with a Tier IV spread that has built-in power generation,” Mr Taylor said.
Another hurdle to wider adoption of e-frac fleets is the still unsettled question of who’s paying for the infrastructure that powers an electric fleet – operators or service companies? Service companies like NexTier want the operator to provide the capital for electricity because it is a significant upfront cost. However, the operator wants the frac provider to provide for the power generation because, historically, frac providers also pay for the engines used in diesel and dual-fuel fleets.
For now, third parties may hold the key to alleviating this issue, by providing the infrastructure to power the generators running the e-frac system. Voltagrid, for example, is a turnkey power company that supplies mobile power grids for industrial projects; it is providing mobile power generation units for the Emerald Frac Fleet and leasing it to NexTier over the course of a frac job with Seneca Resources in the Marcellus Shale. Instead of an operator or a frac company spending the money on building the infrastructure themselves and keeping it on hold for potential e-frac projects, they can spend less money to lease from a third-party provider.
“The third-party providers are going to be valuable for everyone. You have these companies popping up where we have the electrical completions equipment, but they can lease us the power generation, or they can lease the power generation to the operator, and that could help both the operator and the service provider,” Mr Taylor said.
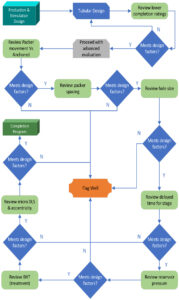
Casing deformation prediction
One of the biggest challenges operators face in hydraulic fracturing is casing deformation. Arshad Waheed, Petroleum Engineering Specialist at Saudi Aramco, noted that casing deformation can happen at any point along the lateral, affecting the well’s production and wellbore accessibility and, in some instances, result in a loss of well control.
In 2021, Saudi Aramco undertook a study to develop and test operational workflows that could help the operator better anticipate instances of casing deformation. Avoiding pipe deformation on a well will save fracturing costs across high-risk areas, help the operator maintain well integrity and safety, and ensure production is not jeopardized.
“When you’re looking at casing deformation, it impacts the well productivity and sometimes the well’s integrity, depending on the type of deformation. If we can look at the workflows we have, that would probably help affect these things positively,” Mr Waheed said. He discussed the study at the 2024 SPE Hydraulic Fracturing Technology Conference in The Woodlands, Texas, on 7 February.
Aramco typically deploys two types of completion strings on its frac jobs: cased-hole cemented completions and open-hole multistage (OH-MSF) completions. For both completion string types, the operator performs the same preliminary stress analysis to determine if the well conditions are favorable for deformed casing. First, it determines whether the bottomhole treating pressures and axial loads expected during hydraulic fracturing will exceed the ratings of the lower completion, followed by a similar evaluation of the pressures in the upper completion.
Mr Waheed said that this methodology was an inadequate means of assessing deformation risk for a number of reasons. First, it ignores other documented causes behind casing deformation – namely, well deviation, well azimuth, dogleg severity, pipe centralization, cement job quality and the type of frac treatment provided. It also does not account for the unique challenges faced with OH-MSF completions, particularly the non-uniformity of the open-hole size in a horizontal well.
The forces applied on a production packer changes as the pressures and temperatures change downhole. These changes make the tubing connected to the packer contract and expand. If the tubing is fixed, or if it reaches the movement limit, any additional axial load could permanently deform the tubing if the load exceeds the safe operational limit. In an OH-MSF completion, since the hole size is not uniform, multiple intermediate packers are run in tandem, and significant variations in applied forces and bending stresses are expected on the pipe. An adequate stress analysis must account for each of the intermediate packers.
“In open-hole completions, we’re running these packers, and the lengths of spacing between those packers may change. The hole size varies all the way through. If you change the hole size, the loads are changing in every section. And you’re dealing with multiple holes, multiple packers, different types of fluids, your displacement is different, a lot of things are different. So, what are we trying to do to design for that? The type of analysis that incorporates this is not done, and the potential for deformation is not reported,” he said.
The study tested two new analysis workflows Aramco developed – one for cemented liners and one for OH-MSF. For the cemented liners, a commercial tubular analysis software was used to a run a model of the well incorporating variables like hole diameters, hole enlargement severity, porosity, formation permeability, hole deviation and azimuth, an ultrasonic cement bond log, dogleg severity and lithology. The software then outputs a liner deformation risk assessment at any given point in the well, providing a color code highlighting this risk.
For OH-MSF completions, the workflow begins with reviews of the lower completion ratings, axial load, planned packer movement, packer spacing, hole size, micro-dogleg severity, anticipated time for each stage of the completion, reservoir pressure and bottomhole temperature. If any one of these parameters falls below the tubular’s design factor – a ratio that measures the maximum quantity of a specific parameter that the tubular can take before breaking – then the well is flagged and the operator and frac company will adjust the completion program accordingly.
Aramco tested the workflows for cemented completions and OH-MSF using historical data from eight horizontal wells, four for each type of completion. For one of those wells modeled with the cemented workflow, the cement bond log helped properly assess cement channeling, which Mr Waheed said gave the operator a better idea of the presence or absence of cement channels than with its traditional workflow. The data from the log would allow the operator to choose perforations in safe areas that avoided intersecting cement channels, minimizing the potential for deformation.
One such project modeled was a monobore completion with a 4 ½-in. tubing and liner with multiple stage fracturing tools and packers in a horizontal well with a production hole size of 5 7/8 in. The upper completion was comprised of 4 ½-in. tubing and a 7-in. compression set casing anchor. The lower completion utilized 10 open-hole mechanical packers deployed on a 4 ½ x 7-in. liner hanger.
The wellbore tubular stress analysis was performed on two stages (stage 4 and 5) using a commercial software as an example of implementing the workflow. Operational conditions during stimulation were modeled based on the frac fluids pumping design assuming the worst-case scenarios for tension, compression, burst and collapse that the completion was likely to see during the stimulation job. The tubing stress analysis model generated from the workflow showed no potential for burst or collapsed casing during stages 4 and 5 of the stimulation operations under ideal conditions.
Aramco has adopted these workflows to analyze the risk for casing deformation on its frac jobs. Mr Waheed said the study illustrated the effectiveness of the workflows in identifying the potential for casing deformation issues before a frac job is completed. He also hopes that publishing the study will encourage engineers to further study the effects of individual variables and downhole tools that affect completion or tubular failure for their wells.
“These new workflows are practical guides for open-hole and cased holes, and we’re identifying the conditions that can lead to pipe deformation, better understanding the things that can help us avoid these cases,” he said.
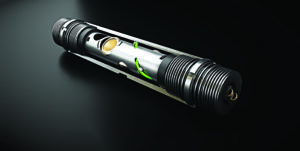
Increasing configurability for different needs
In February, GEODynamics announced the launch of its EPIC Precision and EPIC Flex disposable top-loading gun systems, which are designed to streamline wireline operations.
The guns are customized to fit an operator’s needs. GEODynamics said the switches for the EPIC guns are the first digital switches capable of being configurable to rapid-firing mode, helping operators reduce nonproductive time. The Precision technology offers reusable subs with a configurable and programmable switch and shooting panel, which benefits operators that want a ready-made system.
The Flex technology is suited for operators who want to use various components of the gun system with other components they may already have on hand – the switches and charges are designed to be compatible with open-source software architecture, meaning that they can be programmed with any third-party program.
“What we’re seeing is that companies want to customize their wireline to be whatever they want,” Mr Wade said. “If you want to put Company A’s telemetry in and you want to you use our charges, you can do it. If they want somebody else’s charges in their system and you want us to do telemetry, we want to have that interchangeable capability there. If we’re supporting wireline, we can’t just have one gun system. We have to be able to give them options.”
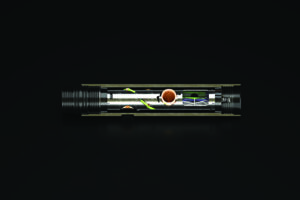
Laboratory testing on the guns was conducted at GEODynamics’ Technology Evaluation Center in Millsap, Texas, in mid-2023, with 100 live shots run on each system. Field trials, done in collaboration with an unnamed operator in the Marcellus Shale in late December 2023 to early January 2024, produced similar results – the Precision and Flex guns each ran 200 live shots successfully. However, Mr Wade said the company faced an issue with trucking the guns out to the field test site.
“We found that we needed to have more equipment on each truck than what we had for the trial,” he said. “We could only put 50 guns on a truck, and the economics of shipping them to regions outside of Texas don’t always work ideally. We had to create a crating system that allows us to put up to 100 guns in one truck, which saves us half the footprint versus the 50 we had.”
The EPIC guns are already being used by operators in the Bakken, and the company is set to begin work with an operator in the Permian Basin in the first half of 2024. Talks are also under way to provide the system for an operator in the Montney Shale this year. DC