Dynamic FITs verify changing integrity of complex wellbores
Frequent dynamic formation integrity tests can quantify wells’ pressure containment capability, ensure better well control
By Don Hannegan and Maurizio Arnone, Weatherford
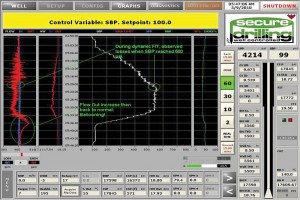
Managed pressure drilling (MPD) methods enabled by drilling with closed-loop circulating fluid systems and PLC-controlled automatic chokes with the ability to precisely measure flow-in and flow-out have established a commendable reputation in several categories of significant importance to the upstream industry as a whole.
Many of those who have applied the technology to date believe MPD is a safer way to drill challenging prospects both onshore and offshore. Incorporating MPD into the well plan has proven to reduce drilling-related nonproductive time (NPT), lower mud costs, achieve well construction objectives with large enough hole sizes for optimized well productivity and increase recoverable reserves by drilling otherwise undrillable prospects.
The focus of MPD lies on wellbore integrity and improving drilling reliability, efficiency and safety. MPD also aids in completing a sound cement job the first time, enhancing well construction and plug and abandonment (P&A) operations.
Understanding the actual pressure integrity of the wellbore is a critical element in the complex wells that we find ourselves operating. Determination of the wellbore integrity requires the operator to conduct a formation integrity test (FIT). Weatherford has developed the concept of dynamic FITs, completed without incurring NPT and without exercising the BOP in the process. The ease in conducting dynamic FITs facilitates more frequent verifications that the wellbore is competent enough to withstand pressures associated with the drilling fluids and the well construction program.
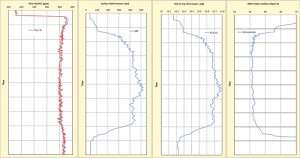
Frequent FITs
There are two industry-recognized methods of testing a wellbore – FIT (Figure 1) and leak-off test (LOT). FITs serve several purposes of wellbore information, including:
• Knowing optimum mud weight and equivalent mud weights for drilling the next section;
• Minimizing risk of loss circulation in drilling trouble zones;
• Deepening the next casing set point, perhaps eliminating a casing string;
• Determining whether planned casing running speeds will destabilize the wellbore;
• Acquiring actual (e.g., not predicted) data inputs for cementing simulating models; and
• Reducing the risk of inducing a fracture during cementing operations.
In order to have a holistic view of the wellbore, FITs should be conducted more frequently than what would be considered the industry norm.
Offset well information, geomechanics data, drilling fluid hydraulics, borehole imaging and formation evaluation data contribute toward plans to achieve a competent wellbore, maintain stability, manage pore pressure and optimize drilling, casing-running and cementing operations.
To reduce formation-related drilling uncertainties, these methodologies are incorporated when planning the drilling program. On complex wells, however, the actual integrity of the wellbore in respect to its ability to withstand the planned fluids, casing and cementing programs changes with each new formation encountered.
Routine underreaming, wellbore strengthening operations and use of loss-circulation materials (LCMs) contribute to the relative unknown. Some cementing programs assume that the weakest component is the last casing shoe; however, this may not be the case. Fracture pressure predictions typically assume shale and tend to be misleading when drilling in sands, not to mention the inevitable margins of errors of such predictions.
HPHT wells inherently present more wellbore integrity uncertainty. These wells, often in deepwater, tend to present rapid departures from plans to very high degrees of overpressure, elevated temperatures and where formation pressures often approach fracture gradient.
Further, once overpressure is geologically established in isolated pressure compartments, reservoir fluids tend to migrate vertically via hydro-fracturing to shallower depths. Operational challenges typically involve narrow, shifting and/or relatively unknown mud weight windows that manifest kick-loss scenarios, risk of stuck pipe, twist-off and sidetracks. Wellbore instability, ballooning phenomena and significant mud losses en route to and within the reservoir section are also common characteristics.
FITs vs LOTs
Many times the industry confuses LOTs with FITs and vice versa. To appreciate the benefits of conducting frequent dynamic FITs while drilling in trouble zones, it is important to understand the difference between the two.
Compared with drilling with an open-to-atmosphere annulus returns system, MPD has been taught as a new way of looking at the hydraulics of drilling. The circulating fluids system may be viewed as if it were a pressure vessel.
For decades, process industries (e.g., chemical plants, petroleum refineries, etc) have avoided open-to-atmosphere systems for safety, energy efficiency, product quality and regulatory compliance. Pressure vessels are periodically tested to rate operating pressure for signs of leaks or permanent deformation. In the drilling industry, our most common methods of testing for pressure containment values are FITs and LOTs.
A FIT is analogous to testing a pressure vessel to its rated operating pressure, which includes a safety factor and where no damage to future pressure containment capability is expected to occur. Conventional FITs require the use of the rig’s mud pumps, closing the BOP and incurring NPT. The operator determines the FIT “test-to” value. If no leak-off occurs, the test provides a degree of assurance the mud in the hole at the time is suitable for the anticipated fracture gradient. This knowledge also aids in optimizing casing-running speeds and planning a cementing program that will not induce a fracture. FITs are considered good drilling practice because of the information that is obtained. However, resistance to conducting FITs is typically associated with the NPT required.
A LOT is analogous to testing a pressure vessel to leak, rupture or permanent deformation. The pressure is raised until the last casing shoe or formation is fractured as indicated by leak-off. In either case, future pressure containment capability may be decreased, requiring less pressure to open the fractures back up again. LOTs deserve careful weighing of risk vs benefit in respect to making the fracture pressure gradient more of a relative unknown than it may already be. However, LOTs provide valuable information to determine the maximum wellhead pressure that could be sustained in case a kick occurs and has to be circulated out.
The confusion between the two tests is in the casualness in the use of the terms and may further reside in the process of conducting a FIT, if leak-off occurs in advance of reaching the test-to pressure. If the integrity test actually revealed the leak-off value, the FIT inadvertently became a LOT and likely recorded as such on the daily rig report.
Benefits of quantifying formation integrity
It is critical to understand the pressure containment capability of the systems in drilling operations. Well control scenarios, mud weight windows, circulating rates, casing running and cementing sequences are pressure related. For assurance, drilling operations can proceed within the limits of the circulating fluids system, quantification of the integrity of the formation and well construction components is imperative.
However, unlike a pressure vessel where testing its integrity periodically is sufficient, the structural integrity of the wellbore is most likely changing with every foot of depth, which enforces the need for more frequent tests, especially in critical zones.
Applying reliability engineering tools is another way of evaluating the benefits of quantifying formation integrity and will answer the following questions: How reliable is the structural integrity of the wellbore to handle the mud in the hole for drilling deeper without incurring losses or risk of a deeper zone pressuring the wellbore and fracturing a shallower one? How reliable will it be to handle planned casing-running and cementing programs? Can I depend on it “failing safe?”
It’s been explained that FITs are relatively benign in respect to risk vs benefit, so why are FITs not conducted more frequently on challenging drilling programs? Cost vs benefit may be the explanation.
Enabling equipment to accurately conduct a FIT
Dynamic FITs are performed with rig pumps, through the bit and while rotating the drill string. This allows for all of the dynamics to be incorporated; ECD, thermal gradient and mud compressibility. Surface backpressure is applied by the MPD system in precise incremental amounts up to the FIT value determined by the operator, eliminating the need to use the BOP. Dynamic FITs also provide valuable data for input to casing running and cementing models, as well as capability for offsite monitoring.
The equipment and methods that enable the practice of the constant bottomhole pressure (CBHP) variation of MPD are required to conduct dynamic FITs as described.
A closed and pressurizable circulating fluids system and the use of a dedicated automated choke manifold with a flow meter are key enablers. A rotating control device positively diverts mud returns to the choke manifold, such as Weatherford’s Microflux control system. This is a fully automated system that measures, analyzes and controls changing wellbore conditions in real time, improving the accuracy of measurement and analysis of flow and pressure data. It uses proprietary algorithms to identify minute downhole influxes and losses on a real-time basis.
The technology measures return flow using a Coriolis flow meter installed in line with the chokes to detect either a fluid gain or fluid loss near real time, enabling gain/loss volumes to be minimized.
It combines closed-loop technology with sophisticated, proprietary data acquisition and computer-controlled equipment to enhance rig safety and drilling efficiency to a level not attainable with conventional open-to-atmosphere mud returns systems.
Without interruptions to drilling progress, the system enables dynamic pore pressure testing, dynamic FITs and dynamic LOTs.
While the dynamic pore pressure test determines the lower limit of the safe drilling window, the dynamic FIT verifies the upper limit of the drilling window. The dynamic FIT reassures the operator that the mud in the hole is suitable for drilling the remaining portion of the hole section, for optimizing casing-running speeds and/or the wellbore has the integrity required for the planned cementing program.
During the well planning phase, the FIT points are normally referenced to offset well data. In exploratory wells, the FIT reference value may be considered more as a theoretical calculated number or a prediction. When a narrow drilling operating margin is expected (difference between pore/collapse pressure and fracture gradient or maximum allowable losses pressure), the effect of pressure and temperature on the drilling fluid becomes a critical variable. The conventional FIT prediction most likely should not be considered the best or safest reference.
While drilling HPHT exploratory or development wells, the transient effect of pressure and temperature on the drilling fluid is a factor that needs to be considered as essential toward a safe and effective drilling program. Although requiring NPT and use of the BOP for a purpose not its primary intent, conventional FITs and LOTs have their respective roles. However, conventional FITs probably should not be totally depended on as reference on challenging offshore wells, particularly HPHT wells with narrow and shifting safe drilling windows.
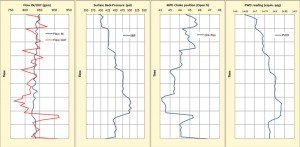
Conducting a dynamic FIT with a closed-loop system
Using the same equipment and CBHP MPD concepts, compressibility and temperature affects on the drilling fluid are inherent factors in a dynamic FIT. Typically, surface pressure is increased in steps of 25 psi (equivalent to 0.02 ppg increases at 6,000-meter TVD) are applied, pausing momentarily after each to ascertain flow-out equals flow-in.
The dynamic FIT procedure was performed in two sections of an exploratory well drilled in a deepwater HPHT environment, circulating through the MPD manifold using the marine riser booster line and the rig’s mud pumps.
The dynamic FIT test (Figure 2) was conducted for the purpose of pressure containment assurance and to determine if the wellbore was able to withstand 15.80-ppg equivalent mud weight (EMW) without incurring losses. Note that as incremental amounts of surface backpressure were applied during the test, flow-out responds in sync with flow-in. The test confirmed within a matter of minutes and without drilling interruption that the planned EMW is within the pressure containment capability of the wellbore.
Figure 3 is a dynamic FIT for the purpose of assuring the pressure containment capability of the wellbore is capable of withstanding 14.83-ppg EMW. Unfortunately, losses were detected before the desired test value was achieved. Although losses were detected, they were identified in enough time to remediate the issue. This real-time data provides drilling decision-makers an opportunity to avoid mud losses, reduce risk of differential sticking and possible twist-off. It may also enhance well control by identifying a zone weaker than predicted or expected. The information may suggest a premature casing set point or use of a liner. And, as mentioned before, the planned cementing program may be tweaked accordingly. In this case, the FIT reference value was reduced from the planned 14.83 to 14.77 ppg EMW.
Conclusion
A well control scenario is, first and foremost, a pressure-related event. FITs should be conducted more frequently than most would consider the industry norm. More frequent verification of the pressure containment capability of the wellbore makes sense for well control and for a litany of other reasons.
Few professionals in today’s chemical, petroleum and industrial process facilities would consider operating their pressure vessels and associated plumbing without first proof testing to be assured they are fit-for-purpose. They are fixed objects specifically designed to operating pressures that incorporate safety factors, and, as such, may be proof tested only periodically for reassurance.
In effect, when the drilling industry conducts a FIT, the purpose is usually to gather proof that the pressure containment capability of the wellbore is capable of handling expected equivalent mud weights and/or casing running surge pressures and/or the planned cementing program.
However, the analogy to the process industries ends when one considers that the integrity of the wellbore is most likely changing, perhaps significantly, with each stand of pipe or formation encountered. However, a downside is the fact that conventional FITs most often entail NPT and require the BOP be used for a purpose that is not its primary role.
When tooled up to practice MPD with a state-of-the-art system on challenging wells, onshore or offshore, dynamic FITs may be conducted with little or no interruption to drilling progress and without having to exercise the BOP.
MPD with closed-loop systems and PLC automated choke manifolds that yield precise and real-time flow measurement information has earned the reputation for early kick-loss detection, improved drilling efficiency and increased recoverable reserves by drilling otherwise undrillable prospects. The authors propose that the fringe benefit of being able to conduct frequent dynamic FITs have potential to be considered to be at least on par with other reasons for practicing the technology. And, on some of the more challenging wells, it may deserve to be a primary reason for practicing the technology in the first place – for safety’s sake.
Microflux is a trademark of Weatherford.