Rigs equipped with walk/skid systems, higher-powered mud pumps and top drives satisfy horizontal-drilling demands
By Joanne Liou, Associate Editor
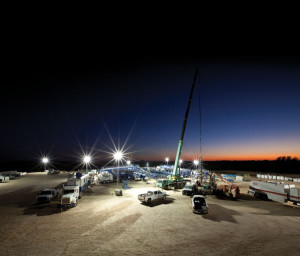
and has since been drilling development wells
in the Eagle Ford (pictured) and Haynesville
and appraisal wells in the Permian.
The drill site has physically evolved with the advent of horizontal drilling and multiwell pads. No longer is a rig confined to drilling a single well before having to rig down, move to another location and rig up again. While this evolution is most prominent in North America, other land markets around the world, including Saudi Arabia and Argentina, are following suit. At the center of the evolution is the rig. Driven by the needs of operators and today’s operations, drilling contractors are stepping up the capabilities of horizontal drilling rigs. Fast moving – walking or skidding – AC rigs with 1,600-hp mud pumps and higher torque top drives are populating the global fleet.
North American onshore rigs are predominately occupied by horizontal, development drilling programs. For Patterson-UTI Drilling, more than 80% of its 200-plus active rigs across the US are drilling horizontal wells. Mike Garvin, Senior VP, Operations Support for the company, said he sees that percentage and total number increasing in the coming year, as E&P companies transition to greater levels of horizontal drilling activity in markets that historically were predominantly drilled with vertical wells, such as the Permian basin. “Additionally, horizontal lateral lengths are getting longer, leading to more complex wells.” That greater complexity combined with the desire for more drilling efficiency has made modern AC rigs the preferred rig class by many E&P companies.
Of the approximately 320 land rigs that Helmerich & Payne (H&P) is operating across North America, South America, the Middle East and Africa, an estimated 80% is directed toward development work. In the UAE, “the rigs we are running are all doing extended-reach horizontals – 10,000-ft measured depth on the horizontals,” said David Millwee, Regional VP – US Land Operations. “In Argentina and Colombia, where we have our AC-technology rigs, the Flex 3 rigs are drilling horizontals ranging from about 4,000 to 8,000 ft depending on the country and location.” Nearly 90% of H&P’s land fleet is drilling horizontal.
Entering US land operations in 2011, BHP Billiton has since been drilling development wells in the Eagle Ford and Haynesville and appraisal wells in the Permian. “Our rigs are specified for drilling horizontal wells and predominately for drilling development wells, too,” Derek Cardno, VP of Drilling and Completions, said. “They’re all AC rigs, and most of them are skiddable. We’ve also turned them into fast movers.”
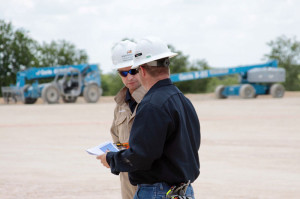
Besides rig mobility, “the two most important components for efficient pad development and drilling of long laterals are the mud pumps and the torque of the top drive,” Jay Minmier, 2014 IADC Chairman and President of Nomac Drilling, said.
In this overview of horizontal-drilling rigs, industry leaders from BHP, H&P, Nabors Drilling, Nomac, Patterson-UTI and Sidewinder Drilling share their insights on rig components and capabilities necessary to meet the demands of onshore horizontal drilling.
Shift to horizontal wells
No stranger to horizontal drilling, Nabors has been drilling horizontal wells in Prudhoe Bay since 1983 and participated in the Austin Chalk trend of the mid-’90s. Nabors has about 300 active land rigs across North America, South America, the Asia Pacific and Middle East, the preponderance of which are drilling horizontal wells. “We are seeing an increasing volume of horizontal drilling internationally, although we have been drilling sophisticated horizontal wells for many years in places like Saudi. A recent example is a record well drilled with one of our rigs, which achieved over 50,000 ft of reservoir contact. The shale reservoirs we are drilling in Argentina are so thick that the initial drilling is vertical, but we

expect over time horizontal drilling will be more prevalent,” Dennis Smith, Director, Corporate Development, said. “It’s not as big a proportion of the total work internationally as it is in the US, but it’s moving that way. I think in another five to 10 years, it will be.”
In North America, roughly 90% of Nabors’ rigs are drilling horizontally, and the industry is supporting the trend. “We’re seeing a big conversion in West Texas and the Permian Basin to horizontal drilling. Customers are switching. Where the majority of the wells they drilled were relatively straight just a year or two ago, now the majority is flipped to where they are going to be horizontal. We see a lot of customers converting drilling plans to horizontal,” Mr Smith said. Not only is the development phase of shales driving the trend but so is the horizontal development of conventional reservoirs, such as the Permian.
The benefit of horizontal drilling is far reaching and not confined to unconventionals or shales. “Horizontal drilling was first commercially applied in the conventional reservoir at Prudhoe Bay. The impetus was to mitigate coning in the reservoir, thereby reducing water and gas intrusion while also increasing well productivity. The economics at the time were a 30% increase in well cost yielded a doubling of production. Many of the wells were drilled in an undulating fashion to facilitate re-perforation over time” Mr Smith explained. With horizontal drilling, “you expose a lot more reservoir to the wellbore, and it’s particularly applicable where you have thinner zones. It’s really the reservoir that dictates it, and shale reservoirs, which require hydraulic fracturing to achieve commercial productivity, lend themselves to horizontal drilling.”
H&P says that it is drilling 8,000- to 10,000-ft laterals in 95% of its operations. However,
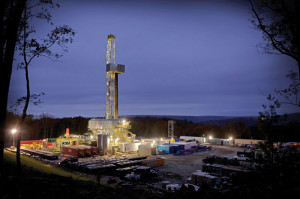
some operators are reaching for 3-mile (15,840-ft) laterals, Mr Millwee noted. H&P has seen wells in Oklahoma and the Bakken push 12,000- to 15,000-ft laterals. In the Eagle Ford area, “we have seen an increase from predominantly 8,000-ft laterals to 12,000-ft laterals, and then in West Texas, we’re seeing the shift from vertical to lateral work with 6,000- to 10,000-ft laterals.”
The shift to horizontal drilling has also changed the way operators pick their rigs. In the US, industry has historically classified rigs by the horsepower of the drawworks, which made sense for drilling vertical wells. Hoisting capacity used to be a primary consideration, but with horizontal drilling, it has become less important. “Today’s wells are often just as long as yesterday’s vertical wells in terms of measured depth, but they are generally shallower in terms of total vertical depth. Hence, hoisting requirements are lessened,” Mr Minmier of Nomac said.
Nomac’s customer base – Chesapeake Energy, EOG Resources, Continental Resources and Noble Energy, for example – is primarily in development drilling mode. Nearly 100% of Nomac’s fleet of 85 land rigs
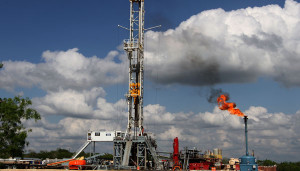
is drilling horizontal wells. “When we talk to operators, they’re most interested in a rig with big mud pumps – 1,600 (hydraulic) hp with 7,500-psi fluid ends – and a higher-torque top drive, rather than drawworks horsepower,” Mr Minmier said. “It is common now to see a rig with a 1,000-hp drawworks, 1,600-hp mud pumps and a higher-torque top drive drilling just as efficiently as a similar rig with 1,500-hp drawworks.”
Pumped for power and pressure
The acceleration of horizontal drilling has led to numerous changes in rig capabilities, such as increased pipe racking capacity and higher hydraulic horsepower, which in turn requires additional power. “Because the measured depth of wells has increased significantly relative to the true vertical depth, you need more capacity to rack pipe so as to avoid having to lay down any drill pipe when tripping out of the hole,” Mr Smith of Nabors said. Hydraulic horsepower translates to bigger pumps, higher volumes and higher pressures necessary to drive the higher torque and RPM capabilities of today’s downhole motors.
Since 2012, Nomac has been methodically shifting to higher horsepower
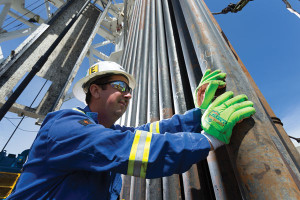
mud pumps. In December 2012, 40% of the company’s rigs were equipped with two 1,600-hp pumps each. By December 2013, it was 52%. Today, 64% of Nomac’s fleet has 1,600 or higher horsepower mud pumps. The contractor also has 16 newbuilds in the works, all of which will be equipped with 1,600-hp pumps. Plans to upgrade other rigs that currently have lesser horsepower pumps are also under way. “By the end of next year, I expect 80% of our fleet to have 1,600-hp pumps,” Mr Minmier added. “That’s arguably the most important factor in determining how long and how efficiently a horizontal section can be drilled.”
With the greater well complexity and longer horizontal laterals, more mud pump pressure is needed to efficiently drill the wells. Accordingly, circulating systems are being upgraded to generate more hydraulic pressure. “We’re providing rigs now with 7,500-psi mud systems, when traditionally it had been limited to 3,500 or 5,000 psi,” Mr Garvin of Patterson-UTI explained. This allows for more hydraulic horsepower to drill extended-reach horizontals quicker.
For H&P, Mr Millwee estimates that about 75% of the newbuilds entering the land market are equipped with 5,000-psi systems. “In most areas, we drill the production section between 4,200 psi to 5,000 psi depending on
the well design and type of BHA used,” Mr Millwee said, “but as we’ve seen the shifts to longer laterals and larger hole sections, we have had operators start to demand 7,500-psi systems. Recently, we’ve had operators drill production sections between 6,000 psi and 6,500 psi.”
Sidewinder Drilling, which has 42 land rigs in the US, is constructing two newbuilds – one to be delivered in January and the second in March 2015. Both are likely to operate in Texas and will be equipped with 7,500-psi mud pumps. “We selected the Weatherford 7,500-psi mud pumps with permanent magnet motors as we believe they will be more reliable, more powerful and lighter weight than conventional mud pumps,” Jon Cole, Chairman & CEO of Sidewinder said. Permanent magnet motors are smaller and lighter than conventional AC motors. “They can run for longer periods at maximum output than conventional motors.”
Nabors Drilling has also observed more requests for 7,500-psi pumps, which are being retrofitted onto older rigs. “The long-standing standard has been a capability of 5,000 psi,” Mr Smith explained. “To go to that higher pressure, you need to change out the fluid ends and high-pressure piping.” The higher psi allows operators to take advantage of new efficiencies in the drill bits, the high-torque motors and the bigger, faster drilling motors. “It all benefits rate of penetration and the ability to clean the hole efficiently.”
Through 2015, Nabors will add 60 rigs to its fleet, all of which will have the option for 7,500-psi pumps. In North America, about 20% of Nabors’ fleet of 300 rigs is outfitted with 7,500-psi pumps. “We are now installing the higher-pressure piping into all of our new and upgraded rigs so that they can be readily retrofitted,” Mr Smith said.
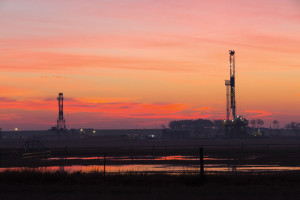
In the Haynesville, BHP Billiton has specified mud pumps to 7,500 psi. “That’s helped us a lot because they’re higher mud weight, longer-reach wells (reaching 18,000 to 19,000 ft) with a small hole size,” Mr Cardno stated. BHP is using 4-in. drill pipe in the reservoir section in the Haynesville, while using either 4 ½ or 5 in. in the lateral section in other plays. “Because we’re TDing wells in 6 ¼-in. hole, that’s the optimum drill pipe size, and the 7,500-psi capability has helped our performance in Haynesville by allowing full flow rate to total depth.”
Spinning farther out
Hydraulic horsepower is to mud pumps as torque is to top drives. However, while the top drive plays a critical role in horizontal drilling performance, it also is a key point for failure. “The top drive is by far our leading cause of downtime,” Mr Cole of Sidewinder stressed. He urged manufacturers to improve quality control and equipment uptime, as well as ensure the availability of spare parts.
Sidewinder has 14 AC rigs, including the two under construction, 10 SCR rigs, 12 mechanical rigs and eight older mechanical rigs that were built

prior to 2000. The older mechanical rigs will undergo selective upgrades to improve horizontal drilling performance depending on the field.
“We have to have a top drive to drill a horizontal well,” Mr Cole stated. “We’re upgrading to higher torque electric top drives on some of our rigs in Appalachia, and we will use the displaced hydraulic top drives on our older mechanical fleet.”
The wells that Sidewinder is drilling in Appalachia, particularly in the Utica, have a longer horizontal section than what they’re drilling in the Marcellus, where they generally run 7,000 to 12,000 ft. “The hydraulic top drives that we had before lack the torque to really effectively execute the programs in the Utica,” Mr Cole stated. “On our 1,500-hp AC rigs, we prefer 50,000-ft-lb continuous torque. On the new mechanical rigs, we’re upgrading from hydraulic 20,000 ft-lb units to AC-electric powered top drives with up to 30,000 ft-lb of torque.” While high-torque top drives have been in use offshore, a typical 1,500-hp land rig uses a 30,000 ft-lb torque top drive. “Demand is increasing for higher torque capacity top drives,” he added.
In the Haynesville, BHP drills intermediate sections with hard, 40,000-psi compressive strength rock. “That needs more torque capability in the top drive,” Mr Cardno explained, which the operator is able to achieve with Nabors’ PACE-X rigs. The operator began deploying the PACE-X rigs in 2013; the rig features a 500-ton Canrig AC top drive with

51,400 ft-lb of continuous torque.
Operator demands for higher-torque top drives are leading to a shift away from hydraulic top drives in favor of AC-electric units. Approximately 78% of Nomac’s rigs have AC top drives. Similar to the mud pump trend, Mr Minmier foresees a continued shift in Nomac’s fleet to reach 90% by the end of next year, as all of Nomac’s 16 newbuilds will include AC top drives and others will be upgraded.
“We’ve been going through a significant upgrade process for the last two years, adding bigger mud pumps, adding AC top drives, adding skidding and walking systems, adding hydraulic catwalks, Iron Roughnecks – all the features that operators are requesting. Eventually, the fleet will be all AC top drives, all 1,600-hp mud pumps, all skidding and walking. It’s just a matter of time,” Mr Minmier said.
Moving structures
For land rigs, there are two facets to mobility: the ability to move from location to location and the ability to move from well to well on the same location. The latter has taken on greater significance due to pad drilling, although the former remains key to the efficiency of the overall drilling operation. “A decade or so ago, rigs were being designed and marketed as

being fast moving, meaning they can quickly move from one location to another. In that context, it was how fast can you rig-down, move to a new location and rig back up,” Mr Minmier explained. “With the prevalence of pad drilling, it’s becoming more critical how efficiently a rig can move from well to well on the same pad. It’s not uncommon to see land rigs today doing only two or three location rig moves in a year, and they used to do 15.”
Today, 59% of Nomac’s rigs are capable of skidding/walking. Over the next 18 months, that percentage will increase to 80-90% through newbuilds and upgrades. Typically, the rigs can skid/walk from one well to another in six to 12 hours. “You don’t rig-down. You don’t lay the drill pipe down out of the mast,” Mr Minmier explained. “Compared to a location move, you’re talking hours rather than days.”
Approximately 50% of H&P’s fleet has hydraulic skid systems; upgrades on other rigs can be done upon operator request. In West Texas, where H&P currently has approximately 90 rigs operating, some operators are still in delineation mode, Mr Millwee explained. “They want to figure out where the optimal locations for their reservoirs are located. Then, based on those
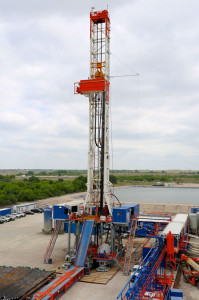
locations, develop a long-term plan for multiple wells on a pad. When they go into production mode, we install skid systems. As the operators continue to better define their fields, we’ll upgrade the rigs for the efficiencies to do the pads.” The space between each well predominantly ranges from 25 to 50 ft, he noted.
In the Eagle Ford, Bakken and Marcellus, H&P is now primarily drilling multiwell pads. “I see West Texas becoming more and more of a multiwell pad area, as they define the areas and go into development,” Mr Millwee said. “In the Mid-Continent area, specifically in the Woodford, we’re seeing more of a push toward pad wells again. We’ve had some pad wells and some single wells there, but we see that one shifting to almost an all-pad environment.”
The significance in pad drilling systems is prominent in terms of reducing nonproductive time. “It’s a lot of these non-drilling activities where the opportunities (to improve efficiency) lie. Being able to move a rig quickly is a huge efficiency, where it traditionally takes three or four days to move a rig from pad to pad, we can literally walk to the next well on a pad in 45 minutes,” Mr Garvin of Patterson-UTI said.
Since the early ’70s, Nabors has deployed skidding/walking systems at Prudhoe Bay and in desert applications in the Middle East, including Saudi Arabia. The technology has evolved from lift-and-roll to stomper systems since early 2000s. Approximately 75% of Nabors’ US fleet – including approximately 150 AC rigs – have walking systems; outside the US, about 33% of its rigs are equipped. The configuration of the newest AC rigs with walking systems provides more flexibility over a skidding system. “The walking systems have a little more

advantage when you have parallel rows or the wells are not in a straight line.” While skids are long beams with hydraulic cylinders that pull the rig along, walking systems have four feet that jack down to raise the rig and then extend longitudinally to move the rig a few feet then reset the process. “Stompers can rotate to move any direction on the compass, whereas skids are in a straight line. There is a debate among contractors as to which is better,” he added.
The new generation of mast and substructures allows drilling contractors to rearrange its rigs to reduce the number the loads and connections, making the rigs move a lot more efficiently between locations. “It’s still important to move rapidly between pads and with smaller-sized loads requiring fewer permits,” Mr Smith said. “In 2005, when we started building a lot of new rigs, the use of AC drives and digital controls facilitated repackaging the rig into fewer loads because the equipment’s lighter and has fewer complex connections.”
Conclusions
Automation is on the horizon for land drilling. While automation has made more headway offshore, onshore drilling contractors also realize there are opportunities for automation to improve

operations and increase efficiencies. “One aspect of automation is automating the drilling of the well downhole,” Mr Garvin said. “Electronic drilling systems on the rig offer very precise control over the hoisting, rotary and circulating systems on the rig.” This precision allows the rig to maintain an optimal weight on the bit to maximize drilling efficiency. Additionally, precise control of the rig’s systems allows for the use of newer, more advanced downhole drilling tools to further increase drilling efficiency.
In the short term, and perhaps long term as well, Mr Millwee of H&P believes operators will maintain laterals in the 10,000- to 15,000-ft range to maintain the economics of the operation. “A lot of (the economics) is going to be dictated by completions technology in the frac,” he said. From the operator’s perspective, they must consider if the extra 5,000 ft up to the 15,000-ft lateral is providing more value. “Can they push it even farther and continue to do the frac in such a way where there’s a value proposition to push them longer and longer?”
Mr Millwee continued: “I don’t think the rig will be the bottleneck at that point. I think the bottleneck may be the overall well design, architecture and completions and whether they are able to get the rate of production they want out of that part of the reservoir.”
While today’s horizontal drilling rig is capable of meeting operator demands, Mr Cardno of BHP believes there are opportunities to further optimize the drilling rig and operation. “We do things that take hours that if we really got focused on them, we could potentially do it in minutes,” he stated. Alluding to Formula 1 race cars, he described how crews have “gone from changing tires from 15 seconds to doing it in 2 or 3 seconds. They probably thought they were doing it really fast when they were doing it in 15-20 seconds.”
“We’re training our engineers and field crews in lean techniques and how to identify ways to take time out of our business,” he continued. “It’s not by doing things recklessly. It’s by having a really good plan, the right tools, the right people, crews being motivated to execute that plan and then do it even better the next time. The new generation of rigs have good equipment; we need to focus on running them well – safely and productively.”
Good post Joanne, thanks. I’ve shared it on Oilpro.
Drilling & Rig operational efficiencies will certainly continue to evolve, both onshore and offshore, in a number of areas.
All the best,
Eric R.
Great article. I can definitely see your point on horizontal drilling. Technology advancements have certainly made the process more efficient, but there is still a lot of room for improvement.