Drilling & Completion Tech Digest
MPD system enhances top-hole drilling, reduces footprint for two Petrobras wells
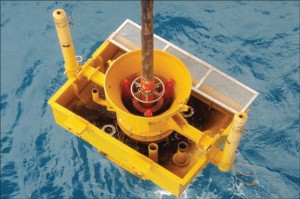
AGR has completed its first Brazilian operations using the EC-Drill technology, which is based on the riserless mud recovery system that has been modified for use on Petrobras’ jackup wells.
AGR’s managed pressure drilling system was used on two Petrobras wells in Brazil’s Rio Grande do Norte region. EC-Drill made it possible to adjust the drilling fluid level in the conductor, allowing accurate manipulation of bottomhole pressure for more effective drilling.
The system improved drilling of the top-hole sections in two areas – in minimizing the environmental footprint by returning all mud and cuttings to the rig without discharge to the sea, and in manipulation of bottomhole pressure to compensate for equivalent circulating density.
The EC-Drill system provides the potential for faster kick/loss detection, as well as savings in rig time and costs on deepwater wells.
Acid system prevents well abandonment in Nigeria
Baker Hughes’ Pressure Pumping group recently applied an acid system to a well in Nigeria, forcing release of the completion assembly and saving the well from abandonment.
The operator was running the 4 1/2-in. lower completion system, made up of a packer-retrieving tool and lengths of blank pipes, screens and swellable packers, when the pipe used to deploy the assembly became stuck about 90 ft (27 meters) before the actual well depth of 14,254 ft (4,345 meters). In an attempt to pull free, the setting tool backed off and came out of the hole without any of the completion components.
An acid system using non-emulsifiers, surfactants, mutual solvents, mild acid and corrosion inhibitors was placed into the well. A 24-bbl acid system was allowed to soak for 45 min with the string in tension and was later displaced with 193 bbl of pseudo oil-based mud.
“On the first pull after the system treatment reaction, all the completion accessories came out freely to the surface,” Abidemi Bankole, Pressure Pumping district engineer for Baker Hughes, said. “This successful treatment saved the well from being abandoned and saved the client the expenses of having to sidetrack to re-drill.”
Rigless ESP system installed in Middle East
Artificial Lift Co has installed the first Rigless Electrical Submersible Pump (ESP) string in a Saudi Aramco field in the Middle East.
The installation comprised a 134-hp Rigless ESP system with a 6,000 bbl/day pump. The system includes Artificial Lift’s Permanent Magnet Motors and Wet Connect system. The unit was installed at a depth of 6,119 ft and included the installation of a downhole ESP gauge, packer and subsurface safety valve assemblies.
Rigless ESP technology provides an opportunity to retrieve the ESP string without a rig, realizing benefits through cost savings on rig utilization and electricity expenditures, decreased downtime and less oil deferment.
The Middle East installation follows the installation of the ESP system on three wells in Alaska.
Cyclone Drilling receives 1,000th Canrig top drive
Canrig Drilling Technology recently celebrated the shipment of the company’s 1,000th top drive at its manufacturing facility in Magnolia, Texas. Cyclone Drilling received the milestone top drive.
Cyclone has purchased 22 top drives to date and sees a potential demand for four more by the start of 2013.
Halliburton, PETRONAS join forces in shale E&P
Halliburton and PETRONAS Carigali signed an agreement for the evaluation and development of global shale resources in February. Halliburton will work with PETRONAS Carigali to set up a Shale Technical Centre of Excellence in Kuala Lumpur.
The collaboration will enable PETRONAS to shorten its in-house capability development by leveraging Halliburton’s technology and experience in the North America shale industry.
Hybrid bit cuts 86 hours from drilling time in Colombian well
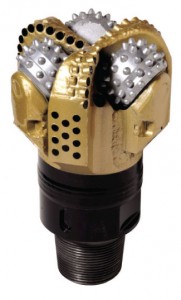
The first use of the Hughes Christensen Kymera hybrid bit technology in Colombia helped an operator save approximately 86 hrs and $250,000. The motorized 8 1/2-in. Kymera bit drilled through 460 ft (140 meters) of hard conglomerate rock and 1,232 ft (375 meters) of interbedded claystones, shale, siltstone and sandstone, as well as traces of pyrite and marl. The interval drilled was 1,667 ft (508 meters) at 33.51 ft/hr (10 meters/hr), according to Joel Baretto, sales manager for Baker Hughes Drill Bit Systems, Colombia/Andean geomarket.
The hybrid bit is based on PDC bit designs with rolling cutters on the periphery of the bit. It can effectively and aggressively drill shale and other formations with problematic plastic, or malleable, characteristics two to four times faster than a roller cone bit.
50th Super Single rig to go to Academy Drilling in Permian Basin
MD Cowan’s highly mobile, smaller-footprint Super Single Drilling Rig has crossed the 50th-unit mark.
Academy Drilling purchased the milestone rig for operations in the Permian Basin. The rig is scheduled to be delivered in March 2012.
The Super Single rig design was introduced in 2005, and recent advances include larger-diameter drill line and sheaves, internally cooled drawworks, upgraded hydraulic system and increased mud pump horsepower.
The Super Single rig can be moved between wells in less than 18 hours, without cranes. It features mechanized pipe handling, operates with a smaller crew and reduces hazard exposure.
StabFrame completes pile installation operation
The first offshore pile installation operation with the StabFrame, a subsea pile-stabilizing template, has been completed in the OGX Waimea field in Brazil’s Campos Basin.
Jointly developed by Large Diameter Drilling and MENCK, the StabFrame stabilizes piles in all depths required for underwater pile driving. Its hydraulic release mechanism allows the pile to be driven further into the seabed before opening the frame and can be adjusted to unpredictable and challenging seabed conditions.
Ulterra bit sets record in Granite Wash play
A new 12 1/4-in. U616M, six-blade matrix PDC bit with 16-mm cutters recently set a Roger Mills County footage record in western Oklahoma. The Ulterra bit drilled 7,065 ft (2,153 meters) from surface casing down to a depth of 8,115 ft (2,473 meters), saving the operator an estimated $44,500 vs the closest offset and $88,500 vs the average of five offset wells.
This generation U616M is the result of extensive bit design and cutter testing in the Granite Wash play. Ryan Wedel, Ulterra applications engineering supervisor, notes that the bit has significant durability in transitional drilling. “This allows the bit to maintain a high rate of penetration throughout the interval in a variety of interbedded formations,” he said.
The U616M has set multiple footage records in the Granite Wash play.
Linear gel fluid system meets Canada’s water conservation requirements to hydraulically fracture shallow-gas wells
A Baker Hughes fit-for-purpose linear gel fluid system enabled a Canadian operator to hydraulically fracture two shallow gas wells while complying with a government directive concerning water conservation.
Late last year, Baker Hughes fractured two vertical wells in Central Alberta, Canada. The wells targeted the Ardley and Edmonton Sands gas formations between 590 ft (180 meters) and 968 ft (295 meters) total vertical depth.
The groundwater base at these locations is approximately 984 ft (300 meters) below ground level. Because these zones are above the potable water table, Baker Hughes needed to comply with the Alberta Base Ground Water Protection regulations outlined by the Energy Resources Conservation Board’s Directive 27.
Directive 27 states that only acceptable fracturing fluids are permitted to reduce the risk of contamination of the groundwater. Fracturing a shallow gas well within a 656-ft (200-meter) lateral from a water well also is prohibited under the same directive.
The company stimulated each of the eight zones (four per well) with five tons of 20/40 sand pumped with a fit-for-purpose linear gel fluid system. The system was energized with carbon dioxide to assist in the treatment of flowback water and to reduce the volume of fresh water required. The team emulsified the system using 75% CO2.
“Records suggest that using CO2 emulsions provide better production results than nitrogen foams when stimulating these formations,” Stephanie Cartwright, alliance specialist in fracturing for Baker Hughes in Canada, said.
The company used about 4,994 cu ft (140 cu meters) less fresh water in the stimulation treatments by emulsifying the linear gel system.