Drilling & Completion Tech Digest
Installation of monodiameter system demonstrates advancement in expandable technology
Enventure Global Technology recently announced the first successful commercial installation of the company’s 12 1/4-in. SameDrift system. The system was installed for an operator in the Middle East.
SameDrift is a drilling liner with an industry-standard drift diameter that matches the previous casing string run in a well so that it can be easily incorporated into the well’s standard casing design. It builds on the capabilities of Enventure’s ESET product line to rotate and reciprocate the liner to help work it to setting depth and to improve cement job quality.
The SameDrift Openhole Liner system ties back to casing without the loss of internal diameter, and the SameDrift Openhole Clad system isolates a trouble zone in the well without tying back into existing casing and provides the same drift below the previous casing.
After the installation of the 12 1/4-in. drift open-hole clad beneath 13 3/8-in. casing, the operator drilled the 12 1/4-in. directional BHA to TD, and completed several round trips through the clad before setting and cementing the 9 5/8-in. casing.
Reaming tool helps challenging wells reach target depth
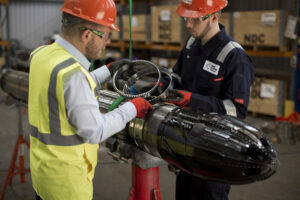
Deep Casing Tools (DCT) recently ran three of its TurboRunner tools with Shell Sarawak despite challenging conditions heightened by COVID-19.
The scope of work, which was awarded to DCT in 2018 and executed in conjunction with a regional partner, EFTECH, required horizontal well completions in six new wells to ensure target depth (TD) could be reached. The work was carried out on Velesto Drilling’s Naga 7 jackup, located offshore Miri, Sarawak.
Despite challenging conditions, including tight spots in all six wells, the runs were completed successfully by deploying DCT’s turbine-powered completions tool, TurboRunner.
It uses high-speed reaming to reduce potential equipment damage, create less downtime, eliminate wiper trips and open-hole exposure and enable cost-effective drill through and drill ahead.
Shell, Equinor combine digital forces to optimize inventory
Shell and Equinor have agreed to collaborate on developing the next generation of the Shell Inventory Optimizer, leveraging advanced analytics on historical data to optimize operational spare part inventory levels.
This is the first project under a Digital Collaboration Agreement signed by the two companies in 2017. The goal is for energy companies to have better control over available equipment and to optimize stock levels.
Since first deployment in 2017, the Optimizer tool has been used across Shell’s upstream, manufacturing and integrated gas assets globally, generating millions of dollars in value through optimized stock levels.
Microsoft will support Shell and Equinor with co-development of the tool, which runs on Microsoft Azure.
Predictive technologies expected to help adnoc save 20% on maintenance
The Abu Dhabi National Oil Company (ADNOC) has completed the first phase of a large-scale predictive maintenance project to maximize asset efficiency and integrity across upstream and downstream operations.
Utilizing artificial intelligence (AI) technologies, such as machine learning and digital twins, ADNOC’s predictive maintenance platform helps predict equipment stoppages, reduce unplanned equipment maintenance and downtime, and increase reliability and safety. ADNOC expects the system as a whole will deliver up to 20% savings in maintenance costs.
“We are pleased to have achieved this important project milestone, particularly given the ambitious scale of ADNOC’s predictive maintenance project,” said Abdulmunim Saif Al Kindy, Executive Director, People, Technology & Corporate Support Directorate at ADNOC. “We are already seeing significant operational benefits and cost savings, and we intend to continue to embrace the power of digitalization and AI as we further enhance performance and drive value across our business.”
ADNOC’s predictive maintenance project is part of the company’s digital acceleration program, which focuses on embedding advanced digital technologies across the company’s operations.
The project, which was announced in November 2019, is being implemented over four phases. The first phase covers the modeling and monitoring of 160 major turbines, motors, centrifugal pumps and compressors across six ADNOC companies.
All four phases of the project are expected to be completed by 2022. ADNOC expects it will enable the central monitoring of up to 2,500 critical machines across all ADNOC companies.