Dalma Energy adopts new work management system on Omani rigs to address ‘last mile’ challenge
Program to ensure procedures are correct, understandable and properly delivered at the rig site has resulted in 82% safety improvement on 15 rigs
By Cason Swindle, Context Associates; Edi Gittenberger, Rider International
Internet, phone and TV companies have what’s called a “last mile” problem: These companies spend billions of dollars in satellites, cables, towers and other technology, but until their service goes the “last mile” and is accessible by their customers, it creates no value for the company or their customers. All the infrastructure in the world doesn’t matter until the companies go that final distance to their customer’s homes and offices.
Drilling contractors and service companies have a similar “last mile” problem: They spend an enormous amount of time and resources developing policies, procedures, programs, systems and processes to improve safety and productivity. However, if these efforts don’t become operational at the worksite, they fail to create any benefit for the company. Even worse, they leave in place the risks that were supposed to be addressed, giving them a false sense of security.
Dalma Energy set out to address this “last mile” challenge. By doing so, it addressed several issues in safety and productivity.
Project Genesis
When Dr Fredric Young, CEO of Dalma Energy, visited one of the company’s rigs four years ago, he saw something surprising: a laminated piece of paper on a winch describing a 26-step operating procedure, but only two steps of that procedure were relevant to the winch operator. Rig management simply expected that the winch operator would be able to identify the two relevant actions from the 26 listed and operate the winch properly without further support.
If this was the case with the winch procedure, Dr Young wondered, how many other procedures were unclear and not executed as expected, and did the rig crews even know that there were issues with the procedures? To address this challenge, he created an initiative that would make it clear for Dalma’s crews which correct procedures they should use for each operation on the rig. The initiative also would make sure the crews followed those procedures.
The following results were anticipated from the initiative:
• Improvement of rig safety statistics, specifically a reduction or elimination of injuries to crew members;
• Decrease in rig nonproductive time (NPT); and
• Optimization of procedural management and discipline processes.
Development, implementation
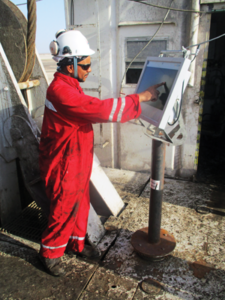
For ambitious projects like this, design challenges must be explored from the beginning. The first challenge was that each rig came with more than 7 yards of paper procedure books, all kept in the administrative office. It was clear that expecting people to memorize books full of procedures was not a workable solution and that paper-only access to those procedures was unmanageable. Further, Dalma’s workforce largely consists of local Omanis who are new to the drilling industry and have limited drilling experience. Relying on their existing expertise to make the right decision was a recipe for increased risk, incidents and lost productivity.
The development of the project was split into two focus areas: First, there would need to be a review of all procedural manuals to make sure the content was correct, consistent and easy to understand. Second, an IT solution would be needed to deliver this content to the workforce. The delivery method must ensure the relevant information for each procedure would be available where the work was to be done and that the correct procedures would be followed.
Well Engineering Partners (WEP) from The Netherlands was brought in to optimize the content of the processes and documentation provided by Dalma. The Simplified Technical English standard (ASD-STE100), developed for the airline industry but expanded to be relevant for drilling processes, was used to rewrite all processes. A third party was hired to develop the IT solution to deliver the procedures and processes to the worksite and track performance.
Once the project was developed and ready for a proof-of-concept implementation, Rider International combined the content and the IT platform into a single organization and is commercializing the developed IT platform and process for procedural management and discipline.
Rider has worked with Dalma for the past nine months on implementing the Rider system on 15 of Dalma’s rigs in Oman. The implementation team has been training rig crew members, installing hardware and software, and providing onsite support. While rig workers and leaders were hesitant at first, with support and hands-on coaching, they are now comfortably using the system to plan and execute rig operations. Stabilization and utilization of the new platform is ongoing and will continue until the implementation is completed in Phase 2 of the project.
Program results to date
Positive results are emerging within a few months of implementing the initiative. Safety performance has improved 82% against the 12-month average to date, and NPT has been reduced by an average of 22.5 hours on rigs where the initiative is in place, versus an NPT increase of 7.5 hours on rigs in the fleet where the program is not yet operational.
Dalma has also engaged in discussions around procedures and standardized ways of working between rigs, allowing for lessons learned to be put into operations throughout the fleet. Dr Young visited with field crews recently and learned that, for the first time, crews were actively participating in making procedures better by giving real-time feedback to the content programming team. As many as 600 comments from crews were received in less than four months; all comments were immediately included and sent to all rigs and all users of the Rider system. In recent discussions with office-based superintendents, Dr Young learned that his teams are now following crew actions on their Rider office screens in real time, which makes them much better prepared to provide assistance when needed.
Comments on the Rider system from rig workers have included:
• It helped remind the night toolpusher to check the drill pipe wiper during an operation, which he appreciated;
• The toolpusher appreciated the system after reviewing preparatory sub procedures for laying down tubulars and RIH completion. In his view, if the system is on the rig floor, there’s no need to give separate instructions to the driller and assistant driller;
• The night toolpusher said the six-day look-ahead in the system was helpful for planning, especially in operations where wells were being drilled in 12 days;
• Supervisors appreciated the toolbox talk task function, where they can show pictures of the HAZIDs, safety alerts and hazards to the crew;
• Mud engineers appreciated the efforts taken in the preparing sub procedures, which are focused on safe handling of chemicals;
• Toolpushers found the preparation tasks helpful to plan efficiently, helping to avoid NPT related to equipment preparation; and
• The companyman and well engineer appreciated the tuition module, crew experience tracker, crew change management, timeline view and planning module. They also pointed out opportunities to have Rider linked to the operator’s instructions, personnel, system, etc.
Two specific results from implementation have already significantly impacted Dalma’s operations: operationalization of its bow-tie process and Omanization of its workforce.
operationalization of the bow tie
The use of the Rider platform for operationalization of Dalma’s bow-tie process allowed a fundamental rethink of the approach to the control of work activities and hazard management. With minor adjustments to the company’s existing methodology, plus the introduction of supporting software, Dalma was able to move risk and hazard studies from the office to the drill floor. To achieve this, Rider created feedback loops within the bow-tie process that allowed hazard and barrier information to be used to control work activity and develop staff competence.
The key to success was allowing the planning and execution of activities to be linked to the continual development of competencies, while also supporting team leadership. By integrating the bow-tie analysis with a new learning and development model, the system was capable of supporting, monitoring and continually improving crew competence, increasing their confidence that they won’t miss a critical step, and increasing management’s confidence that safety barriers will be in place.
Omanization of the workforce
Oman has set ambitious targets to source and train more local talent for the oil and gas industry. This long-term government nationalization program has been in operation since 1988 and has played an important part in the gradual replacement of expatriates with suitably trained nationals in the industry. While the average for operators in the oil and gas sector is around 70% Omanization, Dalma has achieved and maintained a 92% level of Omanization within its operational workforce.
Rider’s platform provided Dalma with improved support for work activities, linking individuals to the tasks that need to be completed and supporting teamwork through the provision of guidance and information at their fingertips. By mapping competencies against the planned work activities, the individuals get the support they need to ensure the work is completed safely, on time and to the required standard.
Rider also mapped work activities against qualifications, simplifying the onboarding of new recruits, decreasing the time required to make them competent, and supporting the development of the existing rig crews.
Lessons Learned
Many lessons were learned along that way that may be useful to others the industry who are contemplating this type of project, said Craig Crowther, Oman Operations Manager for Rider International. They include:
• Always keep communication channels open and live, rather than working alone to come up with a utopian solution. Some of the initial team members involved didn’t want to go to Operations until things were perfect, and it resulted in Operations feeling left out early on in the development process.
• The cultural and organizational impact of changing to the “new” way of working was highly underestimated by the original team. Be mindful of including change management practices in the program design, development and implementation to smooth out the organizational impact of a change of this size.
• Recognize the critical value of and cultivate direct and explicit support from company senior leadership. Many in the organization will look to leadership to support and guide them in working on and accepting new ways of operating.
• Procedure use in the field causes a feedback loop to the office with procedure improvements requests. This a great result, but the organization was not adequately staffed or prepared to handle all the feedback. As the program progresses, the rate of feedback received will slow down. Ensure the organization is properly staffed to address issues and feedback as they arise.
• Even though a lot of performance data has been generated, that doesn’t immediately translate into actionable intelligence. An organization preparing to develop and implement this type of program needs to build a process for analyzing data and making decisions based on it to optimize their operations.
Conclusion
The “last mile” challenge for drilling contractors is real and has a significant impact on operational success. Addressing the challenge requires new approaches that build operational consistency and reliability in procedural management and discipline, but with the tools and services now available in the marketplace, that challenge has become easier to address.
The safety and productivity results to be gained are measurable and significant and, thus, make this kind of project worth serious consideration to any drilling contractor or services provider looking to improve their performance in this highly competitive marketplace. DC
This article is based on a presentation at the 2017 IADC Drilling HSE&T Europe Conference, 27-28 September, Amsterdam.