Custom Nabors rig built for coiled-tubing MPD enables North Slope redevelopment project
By Clyde Treybig, Drew Byers and Bob Mize, Nabors Alaska; Lamar Gantt; ConocoPhillips

In 2003, ConocoPhillips Alaska initiated the Kuparuk Redevelopment Study on the North Slope to optimize patterns in the Kuparuk water flood. More than 130 potential development opportunities for coiled-tubing drilling (CTD) were identified in the field as a result of the study.
One key element of the redevelopment plan was to use CTD technology to deliver lower-cost and higher-value development operations. CTD sidetracking operations involve the use of a continuous string of tubing that is spooled off a reel into an existing wellbore to convey drilling tools and drill bits to the reservoir. One advantage is that drilling operations can be conducted through the existing well completion.
These operations have been performed on Kuparuk since 1998. However, they were only marginally successful until 2004, when technology that included a new generation of downhole directional-drilling tools was developed to enable CTD to deliver more economic sidetracks.
The program delivered promising results from 2004 to 2006, yet the redevelopment effort was hampered by limited coiled-tubing rig availability. The number of opportunities for CTD drilling justified a dedicated CTD rig custom-built for the Kuparuk field.
In early 2007, ConocoPhillips collaborated with Nabors Alaska Drilling to design and construct a CTD rig that could address the requirements of the proposed Kuparuk program and accommodate the challenges of the Arctic environment.
The result of this collaboration was Nabors rig CDR2-AC, an Arctic coiled-tubing drilling rig capable of drilling either conventionally or with coiled tubing, and with a top-drive and mast configuration. The rig was designed and built specifically to optimize CTD managed pressure drilling (MPD) operations in the Kuparuk Field. MPD provides more precise control of wellbore pressure and therefore improved safety, decreased costs and increased wellbore lengths.
The rig design was developed by Nabors Canada as an Arctic package that could better serve drilling conditions on the North Slope. The Arctic design allows all equipment, including the entire coiled-tubing string, to maintain proper warmth and eliminate freeze-up, and of course, protect all personnel from the harsh environment.
This is the first time in Alaska that a rig has been designed and built from the ground up, specifically for CTD operations. The design enhancements that have been included are targeted to provide a safer, more efficient drilling machine and will enable CTD to deliver lower-cost, higher-value results.
THE TECHNOLOGY
Rig CDR2-AC offers a twist on conventional CTD in the way the rig is powered. Nabors discontinued the use of hydraulic power in favor of a proprietary AC electric drive system with a complete AC power distribution and control system. It has a variable frequency drive unit that provides continuous, variable AC power to the drilling and support machinery. The system is powered by three motor/generator sets, as well as a utility package that allows the rig to operate on 13.8kV electrical power when available.
The rig is also equipped with an injector that has 100,000 lbs of pull capacity or 35,000 lbs of snubbing capacity. The injector travels on the main structural rails of the rig floor using an independent handling system for the deployment of drilling tools and for offline maintenance and coil-cutting operations. The injector-handling system offers 10 ft of vertical lift for mounting to the lubricator while maintaining the necessary coiled-tubing tension back to the reel.
The rig contains a coiled-tubing reel drive system for a reel of 180 in. outside diameter and 96 in. overall width. It uses the Foremost plug-and-play design, allowing the shipping reel to be the working reel. The rig substructure complex contains two complete pressure deployment lubricators capable of inserting 66 ft of BHA components. Other equipment include a Pacific Rim Commander 350, 400-hp, 150-ton drawworks and a 150-ton Foremost Model F-150T AC top drive that utilizes a fixed torque guide in the mast.
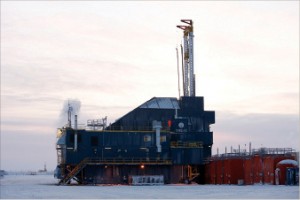
The pipe shed includes an 8,000-lb capacity pipe-handler system that can handle tubulars with a 20-in. maximum diameter and 45-ft maximum length. The pipe shed also contains a work space for the maintenance and storage of the bottomhole assembly. Special tooling and work benches allow for improved handling and maintenance of BHA tools, with reduced exposure to injury for rig crews.
The mud complex contains approximately 600 bbl of active mud capacity and 900 bbl of storage mud capacity. Fluid pumping is handled by two triplex mud pumps, along with a BOP test pump that can divert 10,000 psi service downhole if needed. A mud pallet lift system accommodates outdoor placement of the mud pallet while providing lifting capabilities inside the mud pit area to safely and efficiently transfer mud sacks to the hopper.
Housed within the rig on top of the mud pit complex and adjacent to the rig floor is the training/conference room, which provides a convenient location for safety meetings, breaks and change-outs. Offices were built for company representatives, toolpushers/drillers and service providers. This arrangement enhanced communications and enabled rig personnel to function as a coordinated “rig team.”
A NEW LEVEL OF CONTROL
The rig also gives the operator the ability to monitor and manage all major equipment, including drawworks, top drive, injector, coiled-tubing reel drive, managed pressure choke, mud pumps and mud pits for independent and activity-based operations.
The control system includes a joystick for operating the push and pull of the injector and the hoisting and lowering of the block. Operational controls and parameters, such as hook load, block height, speed and ROP, as well as status and alarms, are accessed via touch screens connected to the drilling control network.
Features that help the driller optimize efficiency and safety include coiled-tubing tension set points (minimum and maximum), coiled-tubing stress analysis, pipe life management, managed pressure choke control, pump control, block position limits, block speed limits, driller’s set points, over pull/snubbing limits, drilling/tripping process screens and pit volume, flow and valve control. Remote cameras are strategically located to provide continuous monitoring of key areas.
The electronic drilling control algorithms help drillers significantly reduce costs and improve safety. Up to four parameters can be monitored or maintained simultaneously: WOB, ROP, drilling torque and Delta-P (differential downhole motor pressure). These features, when coupled with MPD, provide a consistent steady state at the bit, resulting in longer bit life, optimum bit performance and enhanced wellbore stability. Directional drilling control is also improved.
LIGHTENING UP
The operating conditions, environmental stipulations and regulations in the Arctic also played a part in the design of the CDR2-AC. To minimize pad size, drilling pads on the North Slope are designed on a well row that can only be accessed from one side of the well. Consequently, rigs are cantilevered.
In addition, Nabors wanted to reduce impact on the North Slope road system. Though roads stay frozen for much of the year even in summer months, an excessively heavy rig can break through the road surface. Nabors targeted a goal of a maximum 1.2 million lbs for each of the two modules, knowing it also had to be designed to work efficiently. Advanced design and lighter materials helped keep the weight down.
Nabors achieved its design goals, constructed and delivered CDR2-AC to the North Slope, and spudded the first well within 20 months of contract approval. The rig, which began drilling in May 2009, now has operated for one summer season without incident.
AIRLINE CHECKLIST
When it came time to train employees to operate the new rig, Nabors Canada employees spent three months in Alaska providing crews with hands-on training. During the construction phase, new rig operating procedures were developed because of the complexity of the operations, compared with those on a rotary drilling rig.
Once in operation, the new procedures were augmented with checklists that are essentially flow charts of each operation on the rig. The charts walk the crew through all tasks on the rig step-by-step in real time, as opposed to simply giving a list of manual-style instructions. The method is akin to the checklist a pilot must go through when preparing to fly a plane. It ensures the crew is completing every task and forces confirmation that each step has been completed before the crew moves on to the next step. This approach has led to the efficient and safe operation that is required in MPD operations.
The rig leadership, crew and Anchorage-based team members have adopted “A New Era of Operational Excellence” as their motto to create a safer, cleaner and more efficient drilling rig and operation. The CTD teams have been committed to this operation, resulting in a successful start-up.
Sirs,
Improved Energy Efficiency can be attained on your gen sets with our “Auto Tune” power factor correction unit resulting in 20-25% savings in diesel fuel costs,increased monthly savings on fuel costs,improve the amperage out put on your gen set and deliver a fast ROI/ 5-15 months on average. We have warranties and a guarantee that cannot be matched. Denali Power Systems ia all about customer savings and customer support. You can reach me at 253-508-2098 (cell) or contact Jim Rau at corporate headquarters 218-568-6500 for more information on how we can improve your bottom line quickly and efficiently!
Terry Eklund
253-508-2098 cell
Denali Power Systems
http://www.denalipower.com