Crews take greater ownership of safety as Noble focuses on learning from successful work
Multiple safety concepts are brought together aiming to leverage personal experiences of frontline rig crews to build a safer workplace
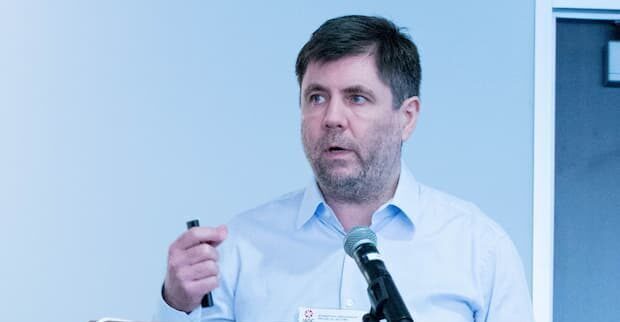
By Stephen Whitfield, Senior Editor
When incidents happen at the rig site, companies typically investigate for causes, and their findings help drive continuous improvement in safety. However, this approach of investigation and corrective action remains a reactive one, as it only kicks into gear only after something has gone wrong.
Thomas Koester, Human Factors Specialist at Noble Drilling, argued that companies should not wait for an incident to occur in order to learn lessons, improve safety and prevent future incidents. Every day, workers perform their regular duties and encounter challenges that they overcome without incident, and the insights workers gain from these experiences can be valuable in building a strong safety culture.
“Traditionally when we’re talking about learning about safety, we’ve focused on the failures that occur – the incidents, the investigation and analysis. But how can we learn from the rest of what’s going on, all the successful, everyday practices that are happening?” he asked. Mr Koester spoke at the 2024 IADC HSE&T Conference in Houston on 6 February.
Over the past two years, Noble Drilling has sought to redefine its approach to safety, both through the adoption of new concepts to guide its safety protocol and the Learning from Normal Work program. The aim is to create a “bottom-up” approach to safety by empowering rig personnel to have a greater influence on the actions the company takes to enhance safety onsite.

New approach to safety
The background for Noble’s adoption of Learning from Normal Work came from its embrace of three separate concepts, Mr Koester said: Safety-II, Safety Differently and Safety as a Capacity. Safety-II is an approach to safety management that assumes that everyday performance variability provides the adaptations needed to respond to varying conditions people see in the field, and this is the main reason why people can avoid safety hazards. Essentially, it is an approach that assumes people learn not only from failures but also from successes in preventing failures and from observations about their environment in order to develop situational awareness.
The concept of Safety Differently involves a rethinking of how organizations approach safety. Traditional safety thinking generally considers workers as the cause of poor safety performance – they make mistakes, violate rules and cause incidents. Because of this, organizations intervene and try to influence workers’ behaviors, developing strict guidelines that tell them what to do; their success is measured through the absence of negative events.
Under Safety Differently, workers are not a problem to control; rather, they are the solution to problems. Organizations should learn how workers create success and harness their skills and competencies to build a safer workplace. This means collaborating with frontline staff and providing them with the tools and the proper environment for them to do their jobs safely. This concept requires organizations to measure safety as the presence of positive capacities instead of the absence of incidents – preventing incidents means enhancing the capacities that make things go right.
Rather than intervening in the behavior of workers on the rig, safety protocol should aim to improve the conditions under which they work: “People go to work with the best intentions. They don’t go to work with the intention of generating an incident, but they are flexible and capable of compensating for inadequacies, weaknesses and flaws if they see them in a system,” Mr Koester said. “We should design the system to fit with the people, not the other way around.”
The flip side of Safety Differently is the Safety as a Capacity concept. While Safety Differently focuses on enabling things to go right, Safety as a Capacity requires organizations to incorporate mechanisms that allow their workers to fail safely when an error is made at the worksite. Mr Koester used a car crash to illustrate this concept: “Cars have been designed with a capacity to protect the people inside, acknowledging that road accidents will happen, but they protect what is most valuable – which is the driver and passengers.”
Learning From Normal Work
Those concepts each inspired Noble to introduce an external program, Learning from Normal Work, onto its rigs in 2022. It starts with identifying positive examples of safety on a given job, then reflecting on those examples through team meetings and recording any lessons learned. Then, if necessary, a mechanism can be designed from those lessons that can be applied to all of its personnel.
One such example Mr Koester noted was when personnel on one of Noble’s rigs practiced “active waiting” outside of the red zone. In instances when crew members were not working inside of the red zone, yet were still standing nearby, they maintained eye contact with the driller’s cabin and observed equipment movement to make sure they were not standing in harm’s way. This behavior was noted by a supervisor, and it became a topic of discussion for a learning team, which is a facilitated meeting with a group of workers to discuss how work is conducted.
“This is not something that is in formal procedures. This was just grown organically out of their everyday practice. They were updating their situational awareness constantly, so this way of spending the waiting time on something that was productive was a positive example. When they were confronted with it, it was a sort of moment of knowledge for them. They weren’t really aware of what they did, but when they had that process explained to them, they could see that this was something they had developed,” he said.
Learning team meetings allow personnel to discuss the constraints that make work difficult, as well as the positive work that the personnel is able to do. Unlike incident investigations, which typically start from an event and move backward, the learning team focuses on proactive learning, looking for lessons whether an event has occurred. In this example, the learning team discussed why “active waiting” is a good idea and how it contributes to overall safety.
The learning team concept was designed to provide a “bottom-up” approach to safety culture, Mr Koester said. Examples come from the behaviors spotted on the rig, and personnel are encouraged to detail their experiences and explore how their behaviors can help in the creation of new protocols. “We want this learning to be facilitated by the leaders onboard. Even though the supervisors and facilitators are still running these meetings, the content is being delivered by the personnel. It becomes highly interactive, based on their ideas, their input, their strategies, and then we can start a conversation.”
From there, the team creates a learning card that records the behavior noted and any potential lessons learned. In the instance with the red zone behavior, the learning team explained the “active waiting” that the rig personnel performed, and noted actions rig crews can take when they are in similar situations – paying attention to equipment, keeping eye contact with the driller’s cabin, and so forth. These cards can also help to facilitate discussions among other learning teams on different rigs, as well as provide blueprints for building a safer culture, Mr Koester said.
“When someone sees an example like this, they might remember a similar situation where they have some experience and find something they can bring to the table. Then we may start another learning team session, and then we see another example in another card with exactly the same principle.” Noble already has 163 learning cards in its database, which will continue to expand.
Making crews feel heard
The Learning from Normal Work program has already had a positive impact on Noble’s rig site safety culture, he added. For one, the program is stimulating the psychological safety of the rig crews. By allowing rig crews to interact with their supervisors during learning team sessions and discuss their own experiences, crews know they will be heard and are more comfortable speaking up on issues they notice. This effectively starts a chain reaction: The more comfortable personnel feel in discussing potential safety hazards they’re observing, the more hazards get noticed; as personnel see their observations lead to action, the more likely they are to continue speaking up.
“The workers onboard are constantly building safety,” Mr Koester said. “They’re constantly building capacity into the system and making it stronger and safer. This is something that can be done on a very basic level.” DC