MPD poised for growth in Australasia deepwater
By Shaun Toralde and Chad Wuest, Weatherford
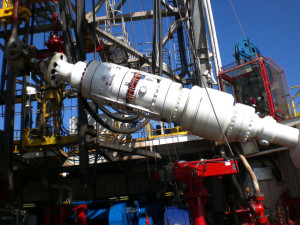
The pace and success of Australasia’s deepwater exploration and development depends on achieving high standards of safety and environmental stewardship while addressing operational and efficiency challenges. The solution will come in part from lessons learned globally and locally with managed pressure drilling (MPD) systems and methodologies.
Global success with MPD systems, along with pioneering deepwater MPD efforts in Indonesia and onshore success in Australia, New Zealand and Papua New Guinea (PNG), provide a firm base of experience and technology for this next step in regional drilling practices. The volume of work under way in the region and the capabilities of MPD systems and methods to enhance these operations suggest the technology is poised to have a significant impact on deepwater drilling in the area.
MPD deepwater technology
MPD systems have had remarkable success enabling safe and efficient operations in a range of land and offshore applications. Within a closed-loop system, MPD methodologies provide a means of listening to the wellbore and quickly adjusting to micro-oscillations in downhole pressure. This measurement and control of wellbore pressure has been a solution to many difficult well problems, particularly in deepwater.
Within an MPD system, a small set of equipment makes up a scalable kit. The system begins with the inherent safety benefits of installing a rotating control device (RCD), which diverts fluids and gas away from the rig floor. Precise pressure monitoring and fingerprinting improves wellbore visibility that informs manual controls for early kick detection. A full MPD Microflux control system provides wellbore visibility plus pressure control via an automated, specially instrumented choke manifold.
The extension of MPD to deepwater applications aboard dynamically positioned rigs occurred with Weatherford’s development of a subsea RCD that is integral to the marine riser system. The Model 7875 below-tension-ring (BTR) RCD extends MPD methodologies to deepwater drilling.
Implementing MPD aboard a drillship or semisubmersible extends new layers of well control barriers through capabilities such as early identification and mitigation of gas influxes. Specific to deepwater operations, it also provides a solution to riser gas. By preventing it at the source, MPD stops gas from coming out of solution in the riser where it is above the seafloor BOP stack.
The first applications of BTR RCD technology occurred aboard a drillship targeting carbonate prospects in Indonesia. Using pressurized mud cap drilling (PMCD) methodologies to drill in total loss circulation conditions has allowed operations to reach zones that were impossible to drill conventionally.
Australasia MPD
MPD systems have been used onshore in Australia, New Zealand and PNG for nearly a decade. Some of the earliest applications have been in PNG’s prolific fractured carbonate reservoirs and fields in the lowland areas of the country. Most MPD applications involve PMCD to deal with total losses encountered in the area’s reefal structures.
MPD has also been used onshore Australia. RCD installations have been used, individually or in conjunction with choke systems, to divert and control flow for improved safety and drilling efficiency in coal seam gas operations. Further, constant bottom hole pressure (CBHP) methods have been deployed in geothermal projects.
In New Zealand, MPD has been adopted in the Taranaki Basin to reduce fluid losses and address well control issues common in depleted fields.
In one such application, two vertical infill wells exhibited a common problem with expensive losses of the synthetic mud system to the underpressured formation. CBHP methods were implemented to stop the losses and improve control of the well. Weatherford Secure Drilling Services employed the Microflux control system and automated MPD choke manifold to reduce mud weight to stop the losses. Instead of modifying mud weight, which takes a while to change, MPD instantly reduced wellbore pressure by manipulating the amount of surface backpressure being exerted.
With better monitoring and control, less mud weight was required to safely maintain well control. The lower mud weight greatly reduced losses to the depleted formation, saving a significant volume of synthetic mud while reducing risk and rig time.
Deepwater applications
The drivers for deepwater MPD have typically been based on providing a means of drilling difficult wells or improving the economics of the drilling operation. They include optimizing the drilling process and enabling the use of MPD variants – CBHP when narrow mud weight windows and wellbore ballooning are expected, or PMCD when severe circulation losses are anticipated.
More recently, however, MPD is helping address post-Macondo concerns by providing a flexible system to supplement the safety and efficiency of deepwater operations. Those capabilities include early kick/loss detection and helping to establish optimal casing points.
The equipment setup for offshore MPD applications with surface BOP stacks involves installing the RCD directly on top of the annular BOP. For operations involving subsea stacks and a moored drilling rig, the RCD is normally deployed on top of the riser’s collapsed slip joint and above the tension ring.
On a dynamically positioned rig, the RCD is positioned below the tension ring and integrated with the rig’s riser system. The RCD is installed in the riser below the waterline and above the termination joint for the subsea choke and kill lines.
Because it is installed below the tension ring, the RCD requires a tension rating of 3 million lb. In the BTR setup, the MPD system has a higher pressure rating as it is no longer limited by the pressure rating of the collapsed slip joint used in previous systems installed above the tension ring. The BTR RCD also preserves the rig’s heave compensation system because the slip joint is no longer collapsed.
The location of the RCD allows for better rig rotation capabilities by keeping MPD hoses away from tension lines. Installation of the MPD system is also safer because the entire assembly fits through the rig floor, which minimizes the time that personnel are required in the moonpool area.
Indonesia performance
In the Indonesian deepwater drilling program, limited pre-drill information and the potential for severe kick-loss conditions led to the selection of MPD to monitor and manage wellbore pressures. In eight rank wildcats drilled to date, the system has successfully provided effective kick detection and mitigation and managed wellbore pressures during drilling, making connections, tripping, and even during cementing and perforating operations.
MPD has also eliminated the occurrence of riser gas by identifying and controlling influxes deep in the well. A gas influx entrained at depth in an oil-based mud typically breaks out of solution at a depth of 2,000-3,000 ft (600-900 m) below the rotary table. Because this point is above the subsea BOP, which is typically 5,000-6,000 ft (1,300-1,800 m) below the rotary table in deepwater, gas breakout is above the BOP and beyond conventional containment.
The MPD system detects the gas influx downhole when it is small and controls it while circulating it out of the hole. In the Indonesian deepwater MPD wells, there has been no incidence of formation gas breaking out of solution in the riser.
The ability to transition between CBHP and PMCD methods has also provided versatility. Use of advanced flow monitoring methods enables early kick/loss detection and mitigation. When severe fluid losses occur deeper in the well, the MPD mode is transitioned to PMCD, which enables drilling with no returns to reach the planned target depth.
Deepwater Australia
Australia’s western market is the country’s largest producing region and is expected to remain so over the next four decades. According to Australia’s Bureau of Resources and Energy Economics, gas production, including LNG, is projected to nearly triple (equal to a growth of 2.9% a year), to reach 8,595 petajoules in 2049-50.
The range of water depths, especially in the northwest, requires a variety of rig types. MPD configurations can be adapted to these rigs with above- and below-the-tension-ring equipment systems.
The specification of MPD-capable rigs in Australian deepwater will be centered on personnel safety and environment protection. In particular, its implementation will be based on early kick detection, riser gas handling and environmental containment. Basic RCD installations will be the minimum safety application, with MPD deployed on critical wells. Many operators anticipating the need for MPD operations are specifying rigs equipped to support full MPD deployment. The expectation is that the full system will provide operational efficiencies that will justify it economically, as well as provide new options for drilling difficult wells.

Deepwater New Zealand and PNG
New Zealand activity and interest is growing. As in Australia, MPD systems and methods are expected to be driven by safety and environmental concerns as much as operational capabilities and efficiency.
There are 18 identified basins within the country’s territorial jurisdiction. The area is large, covering about 5.7 million sq km of land and seabed, and much of it has not been explored. Basins with oil and gas may make up as much as 20% of the country, according to a 2012 draft report by New Zealand-based Concept Consulting Group. The report notes that the combination of increased acquisition and provision of seismic data by the government since the mid-2000s improved deepwater drilling and production technology, and higher oil prices are expected to increase exploration effort outside the immediate Taranaki basin and increase the likelihood of a major find.
Exploration and development of the Taranaki, Pegasus, Great South, Canterbury, Northland and Raukumara basins, as in Australia, will require a range of rig types and MPD configurations. Newbuild, dynamically positioned rigs will probably install the slim BTR type of RCD and use customized components for the rest of the MPD riser package due to riser internal diameter restrictions and to facilitate easier integration with conventional rig systems. The specialized installations typically require advanced planning and lead times. Moored floating rigs may be more quickly equipped with BTR or riser-cap types of RCD.
Australasia outlook
The track record and scalability of MPD combined with the demands of exploration and development in the Australasian region set the foundation for a major advance in drilling safety and efficiency. MPD success around the world, such as in Indonesia, and in land applications in Australia, New Zealand and PNG, provides the experience and specialized equipment and methodologies to facilitate fast adoption in the region’s deepwater provinces. These factors will drive the specification of MPD-ready rigs, both newbuild and retrofits, and broader application of MPD in general.
The scalability of MPD provides the ability to incrementally apply the technology, which will ease its adoption process and lead to more rapid acceptance and use of the full set of MPD capabilities. With a growing number of global operators using MPD and specifying MPD-ready rigs, the use of the technology in Australia and emerging deepwater markets is set for rapid expansion, either as a proactive installation to maximize operational safety and efficiencies or a reactive installation in response to an event that MPD could have easily prevented if it had been installed.