AWS: Cloud computing provides platform to integrate robotics with digital twins
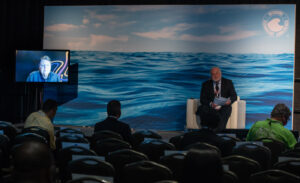
By Stephen Whitfield, Associate Editor
The oil and gas industry has embraced the digital transformation as a way to reshape its operations, fueling a technological landscape that could help companies realize greater efficiencies and cost savings. Amid this evolution, cloud computing platforms have emerged as an optimal means for companies to maximize their productivity, allowing them to integrate machine learning and artificial intelligence systems in one spot.
Edge-to-cloud technologies, such as high-performance computing systems, autonomous systems and robotics, are the mechanisms that can help companies make the most out of the cloud, according to Bill Vass, Vice President of Engineering at Amazon Web Services (AWS).
“We’re seeing a lot of transformations across the energy sector right now,” Mr Vass said at the 2021 Offshore Technology Conference on 17 August. “A lot of companies are moving to the cloud to take advantage of high-performance computing for optimizing their exploration, and you’re seeing this kind of merging between the geospatial and the virtual world in digital twins, bringing IoT data, machine learning and, even in some cases, quantum computing together.”
In his presentation, Mr Vass outlined the work AWS has done to help the oil and gas industry better utilize digital systems, focusing particularly on his company’s cloud platform and its work with Woodside Energy on digital twins and robotics. Woodside Energy utilizes AWS robotic systems integrated within digital twins of its 7 LNG facilities in Australia to increase efficiencies and improve safety monitoring at each facility.
The digital twins utilize a combination of data from more than 250,000 sensors installed at each facility, as well as LiDAR data collected from drones and robotic vehicles. The data is overlaid onto a 3D model of the plant using CAD/CAM (computer-aided design/manufacturing) applications, and machine learning algorithms help process data from each facility in real time. Woodside can overlay the visualization of the sensor data generated from the CAD/CAM systems with real-time video from on-site cameras. Should a robot detect an anomaly onsite, personnel located offsite can instruct the robots to take the appropriate remedial steps. For instance, an operator can send a robot to loosen the valves needed to release excess steam from a compressor.
The digital twins have helped Woodside save an estimated $6 million per month in operational costs for each LNG plant, primarily because robots can address problems in hazardous locations onsite more quickly than humans. Additional costs have been eliminated by not having to send offsite personnel to perform safety inspections, as inspectors can use the robots as their eyes and ears on the ground while working from a remote center.
“Because of the machine learning and the ability to do these 3D walkthroughs, they can perform safety checks virtually rather than sending someone to stand outside in the heat of Australia,” Mr Voss said. “The robots navigate in this environment because of this 3D model, and you can see them flying through and doing their inspection. You’re sending robots into places where you don’t really want to send people, and the people can just tell them where to go. You don’t need to steer them at all. Because the robot has a 3D model of the plant built in, you’re basically writing the code of what you want the robot to do.”
Beyond the digital twins, Woodside and AWS are working to further expand the use of automated robotic systems in its operations. In March, Woodside announced that it has begun using the AWS Robomaker with its Sagemaker platform to process to train, tune and deploy machine learning algorithms for robotics manipulation. RoboMaker is a cloud-based system that allows users to integrate video stream, image and video analysis, speech generation, and logging and monitoring software extensions within a single application, while Sagemaker is a web-based system that allows users to develop and deploy machine learning models for robots.
The goal with incorporating RoboMaker with SageMaker is essentially to allow robots to perform repetitive manual tasks previously done by humans at their facilities, such as manual pump shutdown procedures that involve turning multiple valves in sequence. The Sagemaker system will utilize camera views with machine learning models to serve as a quick training solution for robots on its facilities, allowing them to deploy more robots at scale in a shorter time frame than it had previously.