Automation-enabled fuel efficiency leads onshore drilling ESG
Intelligent monitoring software combined with energy storage, alternative fuel options demonstrate high potential for cutting emissions
By Stephen Whitfield, Associate Editor
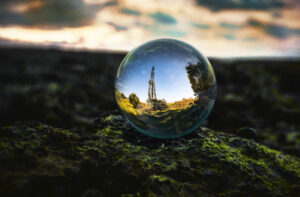
As the land drilling sector comes under increasing pressure from investors and the general public to demonstrate better ESG performance, operators and drilling contractors are stepping up in a multitude of ways. “We’re setting goals to show that we’re serious about reducing our emissions,” said Garrett Jackson, Vice President of ESG and EHS at Devon Energy. “It’s something that’s going to require a lot of effort and a bit of investment to reach some of these reduction levels, but it’s something we’re committed to doing.”
Devon, like many other large operators, has announced a goal to achieve net-zero greenhouse gas (GHG) emissions for Scopes 1 and 2 by 2050. Scope 1 emissions are direct emissions that occur from sources directly owned by the company, while Scope 2 covers indirect emissions from the purchased sources. To achieve these goals, operators have increasingly looked to their drilling contractors for innovations when it comes to reducing rig-related emissions.
Among the key technologies that companies are looking to are energy storage systems, such as battery power, or dual-fuel and natural gas engines. These technologies are enabling so-called “hybrid” rigs that help companies reduce their reliance on high-emission diesel generators.
“There is no magic bean, and we’re only one piece of that puzzle,” said Todd Benson, Chief Innovation Officer at Helmerich & Payne (H&P). “We’re looking at technologies that can allow us to enable the maximum efficiency of extracting the hydrocarbon. It’s about getting the industry to recognize how it can optimize execution and emissions for the services they need.”
Deeper levels of collaboration between operator and contractor will certainly play a critical role in this journey, not only in terms of developing and deploying technical innovations but also in terms of measuring and reporting emissions data. The lack of industrywide standards remains a challenge as it creates uncertainty on both sides: What counts as Scope 1 and what counts as Scope 2 when the drilling rig is contracted to drill a well for an operator?
“We’re not yet reporting on numbers for where we are today or where we hope to be because we’re still trying to understand who really should report on some of these numbers,” said Katy Holst, Vice President of Technology at Patterson-UTI. “We need to establish clear standards of who needs to report on emissions before we can consider publicly announcing figures and targets.”
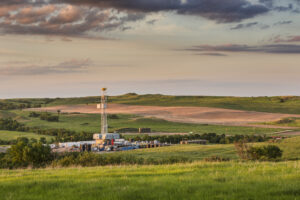
Maximizing engine efficiency
H&P has collaborated with its operator clients on several alternative and mixed fuel options to reduce diesel fuel usage by using natural gas, high-line power and dual fuel. The company currently has 34 active rigs with dual-fuel capabilities and seven rigs operating on high-line power. Dual-fuel engines have enabled H&P to reduce diesel utilization by up to 30%, and it estimates that the GHG emissions impact is 70% lower for its high-line power systems compared with a conventional diesel engine.
In recent years, the company’s strategic ESG focus has not only been on reducing NOx and particle emissions, which can be achieved by reducing the use of diesel, but also on reducing greenhouse gases, which can be a challenge even when using natural gas and dual-fuel systems. Methane slip – the methane released as unburned gas from a natural gas engine – is one example.
“The biggest thing when you’re using natural gas engines is that you have a dynamic energy load that’s constantly changing,” Mr Benson said. “It is challenging to hit the efficiencies needed to avoid methane slip. So a natural gas system is fine if you’re only worried about NOx and particle emissions, but if you’re focused on CO2-equivalent greenhouse gases, natural gas has to be done in a very creative way in order to get those efficiencies without that methane slip.”
To reduce both its CO2 and NOx emissions, H&P has focused on maximizing engine efficiency, regardless of what fuel type is used. The company has been developing and testing its new Engine Management technology, an automated software application that monitors the power coming from various generators, across its rig fleet. Although H&P has actively worked with its clients for years to manually reduce unnecessary engine use, the new software can calculate the most efficient number of generators needed for a given operation, then automatically react to the loads drawn out of generator sets by turning on or shutting down generators as needed. No manual intervention is necessary.
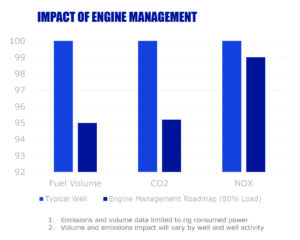
Over the past three years, the company’s concerted efforts to reduce emissions and fuel consumption, combined with efficiency improvements from technology and operational performance, have led to an 11% reduction in CO2 emissions per km drilled, from 66.2 tonnes to 58.9 tonnes. This year, H&P aims to reduce its excess rig engine runtime by 10%.
The company is now working to incorporate predictive energy planning capabilities into its Energy Management system. This would enable the system to anticipate the amount of power needed to be supplied by generators or storage at any given time and how much power it needs to distribute to each circuit within a rig’s power grid. The goal is to ensure an even flow of power within the grid, a process known as load balancing. Load balancing reduces the probability of unexpected energy peaks, which often require extra generator power to cover the excess power needed to meet unexpected demand. Mr Benson said H&P is in early-stage development of these predictive capabilities and hopes to initiate testing in the near future.
Further, the company is also working with battery system suppliers to determine the viability of kinetic energy recovery systems on a land rig. There have already been some successful field trials. Commonly used in Formula 1 auto racing, such systems utilize a device to absorb the kinetic energy generated from the rig’s electronic braking system during a tripping operation. That kinetic energy is then stored in a battery system, converted into electricity and fed back into the rig’s power supply during peak demand.
“We’re trying to figure out what the true benefit of a battery system is now,” Mr Benson said. “Can we use regenerative power? When we’re tripping, when we’re letting the pipe down in the hole, the electronic braking system becomes a legitimate way of charging the battery. We’re capturing excess power that would otherwise become heat and go into resistor banks.”
Prioritizing dual-fuel and high-line power
Reducing diesel use has long been a focus area for Devon, as the operator already prioritizes drilling rigs that either can connect to high-line power or have dual-fuel motors suitable for compressed natural gas, liquefied natural gas or field gas. As of 2019, nearly 60% of the company’s wells were drilled by rigs running either dual-fuel or high-line. The company estimates savings of 2.5 million gal of diesel equivalent from 2018 levels, resulting in 19,000 fewer tonnes of CO2. Total direct GHG emissions also plummeted from 5.65 million tonnes of CO2 equivalent in 2018 to 2.61 million tonnes in 2019. The company will release 2020 emissions statistics at the end of this year.
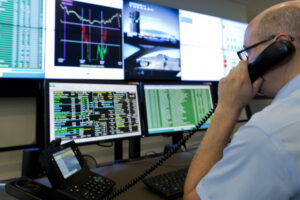
“You need to have a multi-pronged approach as you’re trying to improve fuel efficiency on site,” Mr Jackson said. “There’s not one single solution that’s going to reduce our emissions.”
The company is also in the early stages of trialing various energy storage devices that it can install on the rig, such as battery systems that could serve as a backup, allowing drilling operations to be run in peak hours without having to put additional generators online. Mr Jackson said cost considerations may prove the biggest hurdle to adapting energy storage at scale in its land operations, however. “Energy storage is still an emerging technology on land, and as with any emerging technology, an important piece of making things sustainable is that it has to be cost effective. We’re not trying to do this so that it looks good on paper. We need it to work over the long haul,” he said.
Beyond Scopes 1 and 2 GHG emissions, the company’s new environmental performance goals announced in June also target methane emissions specifically. By 2030, it aims to reduce methane emissions intensity by 65% compared with a 2019 baseline and to eliminate routine flaring. To drive these changes, Devon began transitioning from gas-driven pneumatic pumps and controllers to ones that are air-driven in 2019. This removes one of the largest sources of methane emissions at the wellsite. The company has also invested more than $1 million in optical gas imaging cameras as part of its leak detection and repair (LDAR) program. The cameras enable more efficient and frequent examinations of equipment for methane leaks as part of the company’s LDAR surveys.
In 2019, the company performed LDAR surveys at 1,491 facilities, 864 more than were required by state and federal regulations. These efforts not only led to a significant drop in methane emissions – from 1.22 million tonnes of CO2 equivalent in 2018 to 0.73 million tonnes in 2019 – but they also generated additional data that has allowed Devon to identify the equipment most likely to develop leaks, thereby refining its maintenance programs.
To further curb methane emissions, Devon recently developed a cloud-computing software application where users can capture, enter, track and document LDAR survey findings. The app automatically syncs with Devon’s enterprise data system, and users can schedule repairs, create work orders and document successful repairs.
Understanding load requirements
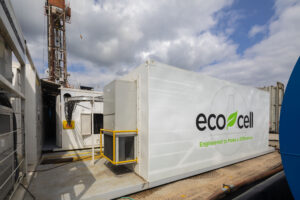
Reducing fuel consumption through automation-enabled technologies is the primary focus of Patterson-UTI’s emissions reduction efforts. The drilling contractor has developed GenAssist, a rig control system that allows for automatic shutdown of engines when they have been running at low load levels for extended periods of time. The system also automatically starts up additional engines when the rig power demand surpasses a programmed load threshold for the number of generators online. GenAssist is currently running on a number of Patterson-UTI’s rigs, and the company is actively discussing deployment on additional rigs with multiple operators.
Another key ESG-enhancing innovation in the company’s arsenal is its EcoCell technology, launched last year. It allows energy to be stored in lithium batteries when power demand from the rig is lower than the rig’s generator capacity, then provides supplemental power back to the rig during peak usage. The system stores over 500 kWh of energy and can produce 1.5 times more power than a generator set at full load.
The system was developed based on Patterson-UTI’s experience – gained from drilling thousands of unconventional wells – of what power requirements would be needed to utilize a stored energy source to maximize emissions savings in typical drilling operations. One example is designing the system so that a tripping operation can be completed with just one engine online, instead of two or three; the battery system supplies the supplemental energy needed in hoisting and then charges during connections.
“When we’re designing a system like EcoCell, we need to understand what the load profile looks like and what extra storage we need in the batteries,” Ms Holst said. “With drilling, we want to be aggressive in cycling those batteries, either charging or discharging based on the number of engines running online and the rig power demand.”
So far, Patterson-UTI has installed units on rigs in West Texas and the northeastern US. “It’s important to test in different regions,” Ms Holst said. “The well programs may vary significantly between areas. The number of pumps on the rig, the length and duration of the drilling program, operating at different elevations and ambient temperatures – all of these variables need to be considered to fine-tune the system.” The company said current plans are to manufacture and install two units per month into 2022.
Simultaneously, the company will continue to refine models within its PTEN+ edge computing platform that can calculate fuel consumption and emissions in real time. Along with calculating actual emissions and fuel consumption rates, the programs model what the rates would be if more optimized engine management were employed, or if automation technology such as GenAssist or EcoCell was installed on the rig. This allows personnel to know how much they could save if they were to turn engines off when not needed, or if they were to invest in deploying more advanced technologies at the rig location. DC