Aramco’s Assaadan: Personnel development among most critical issues for Middle East
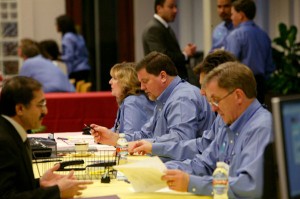
Saudi Aramco may have to double or even triple the workforce on its rigs in the coming years in order to meet the world’s increasing demand for energy, and that’s going to be a tough undertaking, Ibraheem Assaadan, Saudi Aramco general manager drilling & workover, noted during the keynote presentation at the 2011 IADC Critical Issues Middle East Conference & Exhibition on 11 May in Dubai.
“First of all, we have to work harder at replacing the aging field personnel. … And we have limited time. We don’t have all the time we need to do it and do it right; therefore we need to have a strategy – a working strategy, a proven strategy – to transfer the knowledge,” Mr Assaadan said.
Saudi Aramco has been using its Upstream Professional Development Center in Dhahran to take fresh university graduates through an intensive multi-year program that involves classroom lessons and field practice. Mr Assaadan believes his company is much better-positioned than many others in the industry because they’ve had this development program in place for years; however, getting qualified personnel in the sufficient numbers remains difficult.
Safety performance is also challenged due to the limited academic venues that provide an HSE educational foundation, he said. “We are looking for people to be degreed in HSE, and the options are very limited from what we see in terms of universities. … Something has to be done about that.”
Mr Assaadan believes that the position of HSE officers must be high-graded in terms of abilities and qualifications. “The best way to do it is to have people with passion. It’s not just people who are doing it for a living. We need to have people with passion and experience,” he said. “The best way we see is to take people with hands-on field experience – part of the crew, maybe assistant driller or driller – and give him the foundation for an associate degree … so that you get the best of field experience as well as the academic foundation.”
Further, he believes that training can’t be limited to newer and younger workers. “As our current workforce is aging, they’re not the most technology-savvy and we have to do something about this. The fact that he still has five years to go, plus or minus, is not a good enough reason not to invest in him in terms of technology,” he said. This will become especially important as technologies become ever more advanced on drilling rigs. Mr Assaadan advocated the further use of automation to improve drilling and safety performance, as well as to mitigate the effects of personnel shortages. “I think we need to take automation to the next level,” he said.
He also cautioned drilling contractors on the aging of the worldwide fleet, saying that requirements for automation and other technologies will force the retirement of older units in coming years. “It depends on the timing, but we might find ourselves in situations where the demand is much higher than the supply, and that will probably cause some unwanted disruptions to our operations.”