2011 SPE/IADC Drilling Conference: Conference theme is ‘Being the best – growing our business’
Plenary sessions to highlight challenges in achieving outstanding performance in a tough business environment
By Diane Langley, editorial coordinator
How can an organization and each industry worker achieve outstanding business performance today? Sustaining performance and the economic bottom line can be the greatest challenge in today’s tough, unpredictable and volatile business environment.
This year’s SPE/IADC Drilling Conference will bring together leading industry thinkers, engineers and executives to address this time of challenge and share knowledge on the latest technologies. The program includes three plenary sessions addressing the critical issues of the day.
On 1 March, moderator Jan Brakel, manager wells R&D for Shell International E&P, will lead “Plenary Session I: Sustainable Competitive Advantage in an Era of Fast Followers – How Is this Possible?” Representatives from Schlumberger, Maersk Drilling, National Oilwell Varco and Total will offer their perspectives.
On 2 March, moderator Paul Sankey, lead analyst – US integrated oil for Deutsche Bank Securities, will lead the discussion on “The Challenge of New Frontiers — What Frontiers, What Challenges?” Panelists are from Shell International E&P, Sonangol E&P, BG Group, Weatherford International and Pride International.
On 3 March, David Reid, global account VP/E&P business and technology for National Oilwell Varco, will moderate the session “Performance – How to Get Better at Getting Better?” that explores the acceleration of performance improvement. The panel includes representatives from Statoil, Noble Corp, Baker Hughes and Apache.
Technical Session 1: Bits and Coring
SPE/IADC 140133
Surface Hole Casing While Drilling (CwD); A Review of 5 Years Experience in Gabon, West Africa, B. Askew, A. Phillips and J.H. Wingate, Baker Hughes
This paper will document the experiences of surface-hole casing while drilling in onshore Gabon over a five-year period. Modifications and improvements to the CwD shoe will also be discussed. Over a five-year period from 2005, a total of 53 wells in Gabon have been drilled using CwD technology. Modifications to the CwD bit are required to drill further and faster into the underlying carbonate formations. These changes include diamond volume management, changes to bit profile to improve point loading, change of cutter type to improve durability and impact resistance.
SPE/IADC 140070
Maximizing Core Recovery in Lower Tertiary through Drilling Optimization Service and Intelligent Core Bit Design, P. Guarisco, J.Meyer, Petrobras; R. Mathur, I.Thomson, J. Robichaux, C. Young, E. Luna, Baker Hughes
This paper will focus on the longest 12-in. coring application in a deepwater Gulf of Mexico Lower Tertiary well. A total of 360 ft of Lower Tertiary sand was cored and recovered in a single run. The section was drilled using a constant rheology drilling fluid, and hydraulics simulations were performed to guarantee ECD management and optimize hole cleaning. Geomechanical modeling included fracture characterization to select the proper particle size distribution for bridging and wellbore strengthening formulations.
The planning and collaboration in a multidisciplinary team was the key for the accomplishment of this record run. The record run eliminated two extra coring runs accounting for significant reduction in operational cost.
SPE/IADC 140353
Cutting Carbonates – New Technology Delivers Step Changes in Bit Performance, R.W. Weeden, S. Williams, F. Lugo, P. Gaduan, NOV
Historically, Omani carbonate formations were drilled with rolling cutter technology. However, after decades of development, rolling cutter bit designs could not provide the durability and efficiency required by operators. The reliability and durability of diamond impregnated bits have offered the industry a good option to reduce the number of trips required to drill a carbonate interval when tripping costs outweigh the operational costs of low penetration rates. While there are still improvements to be made with this technology, the next step change in performance will come from a bit that has the longevity of diamond impregnated bits and the efficiency of PDC bits.
This paper details a project aimed at delivering the next generation of drill bit technology for carbonate formations.
SPE/IADC 140317
Extension of Gauge Length to Reduce Vibrations and Improve Drilling Performance, G.F. Smyth, A.M. Evans, J.Babb, N. Bolivar, Hibernia
During extended-reach drilling operations at the Hibernia Platform, operated by Hibernia Management and Development Co and led by ExxonMobil Canada, bit gauge length and profile have been systematically varied to improve drilling performance while using a standard bottomhole assembly (BHA) and bit design.
This paper presents the results of progressing from a 4-in. non-tapered gauge bit to a 5-, 6-, and 7-in. partially tapered gauge from 2005 to 2009. Mechanical specific energy, vibration and directional response data are presented for each incremental change in gauge length over a group of seven wells. Results indicated the tapered profile and increased gauge length provided comparable directional response with significantly improved drilling performance.
Technical Session 2: Deepwater 1
SPE/IADC 140113
Kick Tolerance Misconceptions and Consequences to Well Design, H.Santos, E. Catak, S. Valluri, Safekick
During development of a new well control system, kick tolerance misconceptions were identified and will be presented. Among those are the effect of friction losses and BHA geometry in the final calculation of the maximum allowable kick volume. The paper will also highlight the positive effects of using an automated well control system compared with the traditional one where the choke is manually controlled. In some cases, kick tolerance (in volume of allowable kick in the well) can more than double.
SPE/IADC 140326
Effective Vibration Modeling for Improving the Quality of Sonic Measurements, C. Chatar, M.P. Blyth, Schlumberger
For oil and gas operators, understanding rock properties in real time has become a critical success factor for reaching deep reservoirs. The detrimental physical effects of shock and vibration on drillstring and BHA components are well known, but measurements of acoustic signals are also sensitive to excessive sources of downhole noise. It is critical to the quality of the sonic log to minimize vibrations while drilling. Background information on acoustic measurements is presented, along with an overview of current BHA vibration-modeling techniques. Data are reviewed from projects with poor-quality sonic data due to lack of vibration modeling and projects where vibration modeling resulted in superior measurements. BHA planning to minimize vibrations and to optimize acoustic measurements is presented.
SPE/IADC 139410
A Historical Review of Drillpipe Capabilities and the Triggers for Change, T.M. Redlinger, J. McCormick, Weatherford
This paper reviews the evolution of drill pipe capabilities and compare the historical expectations of the well designs. It reviews the triggers that created the need for adoption of new grades and connection standards. The paper discusses the pending new drill pipe technologies and their effect on capacity improvements.
SPE/IADC 140144
Dynamic Aspects Governing Cement Plug Placement in Deepwater Wells, P.E. Aranha, C.R. Miranda, J. Magalhaes, G. Campos and A.L. Martins, Petrobras; A. Braghini, M.F. Naccache, PUC-Rio
This article presents a parametric study in the role of rheological properties of fluids (drilling fluid, spacers and cement slurries), string rotation, flowrates (including free-fall effects) in the displacement quality of cement plugs. Analyses are based on three simulation tools. Conventional cement pumping software defines flowrate profiles at annulus entrance, accounting for free-fall effects. CFD and an in-house developed software based on the lubrication theory define interface propagation and contamination levels.
Technical Session 3: Tubular 1
SPE/IADC 139785
Fatigue-Based Tubular Connection Performance for a CSS Application, S-Y Hsu, K.H. Searles, ExxonMobil; A. Aylor, Imperial Oil Resources
In this paper, a multiscale geomechanics modeling methodology is presented to predict the onset of casing and connection failures due to CSS-induced ultra-low cycle fatigue (ULCF). The modeling methodology consists of a global model of single or multiple pads, a next level submodel of near-well formation and cement, and a final submodel of casing and connection. To predict the ULCF life, an algorithm based on the concept of cyclic void growth is incorporated into the final submodel. It provides the capability to predict the number of steam cycles to failure using the concepts of demand (load) and capacity (resistance).
Sensitivity studies were conducted on connection offset to slip plane and suggested that fatigue life could be extended by placing the connection away from slip planes. Parametric studies were also conducted to characterize the impact of threaded connection design on fatigue life.
SPE/IADC 140262
Application of a New Method for Predicting Down Hole Loading of Tubulars During Expansion, M.E. Evans, J.R. Setterberg, Weatherford
This paper describes the loads experienced by solid expandable tubulars during downhole expansion. These loads are compared to the loads experienced by tubulars when expanded using current laboratory techniques. The paper demonstrates that the current practices for expanding test samples do not include all of the loads that can be experienced in situ. The loads that are excluded in making expanded thread connection test samples may have significant impact on the performance of the threaded connections. Newly developed testing methods and equipment that have been used to replicate the actual downhole loads that are generated when casing is expanded are described and data generated from the testing of samples made with the new equipment presented.
SPE/IADC 139762
Intergranular Cracking of Oil Field Tubular Components Resulting from the Tempering Process, S.Koneti, S.R. Gokhale, T. Wadsworth, T.H. Hill Associates
Oil country tubular components often fail through brittle intergranular cracking when exposed to environmental conditions that contain aqueous H2S. Such failures promulgate the notion that detection of intergranular cracking morphology on fracture surfaces is a confirmation of failure through sulfide stress cracking or hydrogen embrittlement, even when no evidence of a source of nascent hydrogen exists. Study of intergranular cracking related failures has shown that such failures can occur not only when the component is exposed to H2S but can also be caused by temper embrittlement due to improper heat treatment.
This paper presents case studies and lessons learned from analysis of such failures and presents the metallurgical and analytical techniques that need to be utilized to identify the temper embrittlement mechanism.

SPE/IADC 139826
Breakout Torque: Hypothesis, Investigation and Evaluation, J.N. Brock, A. Muradov, S.S. Youngson and C. Brooks, National Oilwell Varco; M.L. Payne, BP
The continuing development of high-torque rotary-shouldered connections (RSC) has represented an enabling technology for the industry and permitted the continued advancement of drilling deeper, higher departure and more cost-effective wells. Occurrences of high-breakout torque have been reported with API RSCs and with proprietary high-torque RSCs from different manufacturers.
This paper presents an analysis and evaluation of the causes of high breakout torque with rotary-shouldered drill stem connections. Results of torque analysis, ambient stress measurements, finite element analysis, and visual evaluation of connections are presented. The impact of rig running procedures and handling equipment is considered and evaluated.
Technical Session 4: Completion Technology and Field Development
SPE/IADC 140228
Case History: Lessons Learned From Retrieval of Coiled Tubing Stuck by Massive Hydrate Plug When Well Testing in an Ultra Deep Water Gas Well in Mexico, V.V. Arrieta, A.O. Torralba, P.C. Hernandez, E.R.R. Garcia, Pemex; C.T. Maia, M. Guajardo, Halliburton
This paper presents a case history in which water production in a gas well was greater than anticipated during the clean-up period. A massive hydrate plug was formed while coiled tubing was being pulled out of hole, and the coiled tubing became stuck. The steps taken to free the coiled tubing are discussed.

SPE/IADC 140274
Merging Multilateral & Casing Exit Technologies to Increase Wellbore Junction Reliability by Reducing Rig & Openhole Exposure Times, C.Guidry, C. Pleasants and J. Sheehan, Baker Hughes
This paper reveals the challenges and benefits of merging casing exit, sealbore diverter (SBD), and multilateral (ML) casing junction technologies into one system that reduces both rig and open-hole exposure times, thereby improving reliability, reducing risk and providing a more cost-effective solution to meet the client’s need.
Typically, an ML junction well is accomplished by completing a casing exit with a conventional whipstock (WS) and milling bottomhole assembly, drilling the open hole, removing the WS, installing the SBD, and then integrating the ML casing junction to the SBD at the casing exit window.
A new system combines the attributes of the WS and SBD into one downhole assembly, which allows the WS to be retrieved while leaving the SBD anchored and properly oriented in the wellbore. This removes lateral and rotational orientation concerns, while also eliminating one trip downhole. A new geometry milling BHA was also employed to maximize window length to improve ingress and egress of the steerable drilling BHA.
SPE/IADC 140304
A Cost Effective Alternative Method of Deploying Perforating Devices in High Angle Wells, R. Hord, Quicksilver Resources; T. Scott, F. Weeks, M. Budde, Weatherford
This paper describes the development of a new innovative deployment method for perforating devices in horizontal wells without the use of coiled tubing, jointed tubing, drill pipe and/or tractors. The new method involves a simple cement wiper plug system with a HPHT rupture disc located in the top plug. Once the cement is pumped into the well, a retarded water mixer is pumped behind the top plug. This water is located in a pre-calculated area behind the plug. This mixture is designed to wash the cement out of the float shoe and not harden. When the top plug is bumped and latched in, the casing may be tested and the rupture disk burst.
Later, a fluid pumping unit is mobilized to the wellsite with the wireline perforating unit to complete the well. At this time, the formation fractures are initiated into the area near the shoe, allowing fluid to be pumped into the formation. The frac truck pumps the perforating device down the wellbore. Perforating takes place and the perforating device is retrieved via wire line. Immediately upon retrieval of the perforating guns, the frac unit procedure is initiated.
This method is supported by 400-plus successful case histories.
SPE/IADC 140010
Passive Inflow Control Devices and Swellable Packers Control Water Production in Fractured Carbonate Reservoir: A Comparison with Slotted Liner Completions, K.S. Youl, H. Harkomoyo, W. Suhana, Kodeco; R. Regulacion, T. Jorgensen, Halliburton.
This paper discusses first usage of a new tube-type ICD combined with swellable packers to control water in fractured carbonate reservoirs in Asia. Traditionally, horizontal wells in the Poleng field in East Java were completed with slotted liners and struggled with early water breakthrough and high water-cut production. Since highly productive fractures are thought to be the main conduit for water, and slotted liners do not provide control for fluid inflow to the wellbore, the high water cut has challenged offshore production significantly.
To combat these challenges, a new completion strategy using ICDs and swellable packers for both delaying and minimizing water breakthrough was suggested for the Poleng Field. The ICD/swellable packer technology has shown that it can control inflow of unwanted water in a fractured carbonate reservoir. Field properties and how the challenges for drilling and completing the wells were addressed are presented.
SPE/IADC 139628
Challenging Multilateral and Completion Design for a Deepwater Well in Italy: Decision Support Through Risk Analysis, C. Repetto, C. Sanasi, S. Di Vincenzo, C. Cordeddu, G. Ricci Maccarini and M. Tufo, Eni; J. Michelez, N. Rossi, Altran Consultancy
A challenging subsea well is planned to be drilled and completed in a deep offshore field in the Adriatic Sea. This project includes all the challenges and criticalities related to deepwater wells, sour environment, gas lift wells, multilateral and intelligent wells. The objective of the study was to provide decision support for the selection of the most suitable multilateral and completion design addressing, through a probabilistic approach, all the uncertainties regarding reservoir characteristics, well design and productivity in terms of duration and cost.
A multidisciplinary working team has been created to assess all the aspects of the project with its opportunities and criticalities. Different scenarios have been compared with regards to the available technologies for multilateral and intelligent completions. The first step of the analysis was the identification of the uncertainties related to technical, organizational or environmental issues, successively reported in a probabilistic time and cost model. A dedicated fault tree approach was deemed useful to focus on the combination of events leading to a potential branch loss and to calculate the associated probability. Uncertainties were then combined with production profiles into a technical unit cost
Technical Session 5: Drilling Automation
SPE/IADC 139849
Real-Time Optimization Of Drilling Parameters By Autonomous Empirical Methods, W.L. Koederitz, W.E. Johnson, National Oilwell Varco
Several methods exist for determining the optimum selection of drilling parameters when drilling is under way, including the use of drill-off tests, downhole measurements, previous experience, engineering judgment and modeling. Use of these methods often requires significant resources and the results can be specific to the situation being optimized. The goal of this research was to develop optimization methods that can be effective without any a priori knowledge of the drilling environment. Further, it was specified that these methods must be implementable as an autonomous system that can run without human intervention.
The results of developing and field testing these techniques are presented in the paper, A new tool for drilling automation has been developed which is effective for real-time drilling performance improvement. Further, it is expected to serve as a base platform for more sophisticated approaches to drilling optimization.

SPE/IADC 140231
FMECA and Commissioning – Guidelines to Effectively Deliver Technology and Systems for Successful Drilling Automation, J. De Wardt, De Wardt & Co; T. Moore, SwRI; A. Mackenzie, National Oilwell Varco
Failure Mode and Effects Criticality Analysis (FMECA) is a powerful tool used in high-risk businesses to deliver reliability. Well-known methodologies applied in aerospace, nuclear and dynamic positioning systems can be translated to drilling. Commissioning is the transition process between construction and operation used in process plants from onshore chemicals to offshore production.
The drilling business has applied these tools to a limited extent. FMECA is typically applied to a single component and not the entire rig or system. Commissioning tends to be done at the major component level rather than as an integrated facility. As the integration of systems in the drilling process grows, these tools become very pertinent to success and reducing risk. They are the foundation of reliability success for automated drilling systems. These two tools, properly and efficiently applied will bring immense value to the industry in terms of reliability.

SPE/IADC 139403
Continuous Motion Rig, a Detailed Study of a 750-ton Capacity, 3,600 m/hr Trip Speed Rig, M. Grinrod, H. Krohn, West Drilling Products
The basic principles for a continuous motion rig have been presented earlier (IADC/SPE 128253).The concept allows jointed pipe to be run or pulled in a continuous manner. Several benefits besides significant improvement in tripping speed can be listed. This new rig concept can be used on every rig on- or offshore where well costs, well safety and efficiency is an issue.
The concept based on a 750-ton system has been studied in a Joint Industry Project (JIP). This paper discusses aspects of the Continuous Motion Rig based on findings in the JIP. This paper discusses details related to equipment and control system for full automation and rig layout.
SPE/IADC 139897
Increased Rate of Penetration Through Automation. J. Dunlop, R. Isangulov, W.D. Aldred, H. Arismendi Sanchez, J.L. Sanchez Flores, J. Alarcon Herdoiza, J. Belaskie, J. Luppens, Schlumberger
The implementation of automation in drilling lags behind other industries. One reason for this is the variability of drilling operations and uncertainty in knowing what is being drilled at any given time. A closed-loop system continually monitors drilling parameters and drilling performance in real time and constantly adjusts WOB and RPM maximizes instantaneous ROP. The system has been tested on more than 20 drilling operations around the world in advise and control mode. Field tests show an improvement in ROP typically greater than 10% versus nonautomated operations.

SPE/IADC 140114
Interoperability: An Enabler for Drilling Automation and a Driver for Innovation, A. Sadlier, M.Laing, Baker Hughes
This paper examines several industry segments to recognize how standardization at the level of interconnectivity has affected both their interoperability and innovation. Business models that promote and reward innovation will ultimately drive solutions for automation. But interoperability will drive more than just automation; it is the key to shattering the myth around service complexity. Protecting IP requires encapsulation of process and control logic and the adoption of appropriate interface standards. Standards enable the prospect of greater interoperability, reduce system complexity through modular packaging, and drive innovation.
SPE/IADC 140255
Development of an automated system for the Rapid Detection of Drilling Anomalies Using Standpipe and Discharge Pressure, D. Reitsma, At Balance
The requirement for the early detection and the control of kicks, losses and other anomalous conditions while drilling are becoming increasingly important as the industry drills in more challenging environments both onshore and offshore due to greater challenges with respect to equipment stresses and pressure regimes. This paper presents the design and testing of a high fidelity and high certainty system for the early identification of anomalous conditions while drilling such as kicks, losses, washouts, drill string plugging and hole bridging without the need for traditional delta flow equipment and interpretation methods. An explanation of how the system minimizes false alarms and how visual and audible methods inform the operator of the different anomalies as they are detected are included.
Technical Session 6a: HSE
SPE/IADC 139161
Psychological Effect on HSE Behaviour – New Initiative from a Drilling Team, M. Al-Mehailani, K. Al-Hindi, A. Gohain, S. Muqeem, S. Akhtar and A.S. Al-Rakdan, Kuwait Oil Company
In spite of consistent campaigns for HSE compliance, crew members are often caught in unsafe acts. To minimize such unsafe acts, a drilling and workover team had conceptualized a new approach and implemented it for the first time. The program is basically an approach for improving safety performance through psychology. The program, having yeilded amazing results, calls for a safety violator to wear a jacket with a slogan that says “Caught in Unsafe Act.” This safety program is like a game: any person caught in an unsafe act has to keep wearing that jacket as a penalty for the violation until another person is caught performing some unsafe act. It labels the person as a violator and presents the violator as a man who needs to be watched. This tends to stir up more HSE awareness, and develop a better HSE attitude and culture.
SPE/IADC 138960
Reducing Safety Incidents by Lifting Single Joints of Drill Pipe with a New Design of Elevator, A. Law, J. Turnbull, BP; T. Redlinger, M. Frilot, G. Brady, Weatherford.
The traditional methods, equipment and safety measures currently in use have failed to eliminate incidents, injuries and near misses which occur while picking up single joints of drill pipe. Operations in the North Sea and elsewhere have recorded a significant number of serious incidents with the “variable” type of single joint elevators that are commonly used which have resulted in dropped objects, lost time incidents with attendant injuries and near misses. A recent joint effort between a major oil company and a service company has led to the development of tools and methods that incorporate several key features and provide a means to enhance safety and operational efficiency while lifting single joints of drill pipe. The authors discuss the problem as it existed, review the new methods and handling tools which evolved and provide current data on their implementation.
SPE/IADC 139845
Can Safety Improvement Increase Drilling Efficiency? D. Pavel, S.Boutalbi and B. Grayson, Weatherford
The number one operational safety risk during the drilling and completion of a well is the risk of a kick and the danger that this can place on people, assets and environment. The second is the potential misdiagnosis of a kick or the ability to identify, quickly and efficiently, downhole anomalies. There are numerous key elements that exist in the industry today that can have great affects on mitigating these risks and creating a substantially safer drilling and completion operation and environment. These elements are field proven for 40 plus years, are readily available from numerous vendors and are economical. Surprisingly, these elements are not used on the most critical, risk-laden and expensive wells being drilled.
This paper describes how a few of these basic elements would greatly enhance the operational safety and efficiency. A closed mud-returns system allows one to identify kicks quickly and accurately, thereby minimizing risk, without sacrificing other operational elements.
Technical Session 6b: Case Studies
SPE/IADC 140331
Case History of Innovative Plug-and-Abandonment Equipment and Processes for Enhanced Safety and Significant Cost Savings, D. Olstad, J. McCormick, Weatherford
This paper examines the combination of aggressive engineering and competent staffing of newly developed Pulling and Jacking Units (P&JUs) to solve P&A problems in a safe and efficient manner on four offshore P&A projects. The P&JUs examined have operated offshore on Interventions and P&A operations to address hurricane-damaged platforms and have been utilized to address aging wells in the GoM. The P&JU are designed for rapid mobilization and provide a strong foundation to conduct multiple project tasks.
SPE/IADC 140260
The Successful Evolution of An LWD Rotary Steerable System For Air Drilling, C. Hartley, D. Weisbeck, S. Robert, M.Smith, Weatherford
This paper presents the evolution of a third generation point-the-bit rotary steerable system (RSS) and its successful application for air drilling of directional wells and lateral intervals. The authors show how the challenges of rotating jointed pipe and electronic components through high doglegs were tackled. Results of successful deployments on over 20 bit runs are demonstrated, along with a step-change in delivered tool reliability.
SPE/IADC 140305
An Aggressive Approach to Reducing Failure-Driven Non-Productive Time in Onshore Drilling Operations: Expanding the Quality Program, J. Everage, S. Altizer, J. Veloz, T.H. Hill Associates; F. Kellow, Devon Energy
In determining the necessity of drill string quality assurance initiatives, an operator must answer two primary questions: 1) What is the probability of failure and 2) What would be the impact, financial or otherwise, of a failure event?
Typically, balancing answers to these questions with the expense of additional quality management measures has presented a challenge to onshore operators. However, the switch to drilling 100% horizontal wells in recent years has served to make it economical to implement a robust quality program.
An operator drilling in the Barnett Shale region implemented an aggressive quality management plan to reduce risks/expenses resulting from dril string failures. The operator first established a baseline for non-productive time due to drillpipe and HWDP failures, and then tracked the changes in NPT over a two-year period as the quality program was developed and implemented.
Technical Session 7: Wellbore Stability and Hydraulics
SPE/IADC 140298
Automated Real-time Drilling Hydraulics Monitoring, P. Zoellner, G. Thonhauser, TDE; M. Lueftenegger, H.F. Spoerker, OMV
One essential element of real-time drilling monitoring is wellbore hydraulics reflected by fluid flow and pressure response. Issues related to pipe wash-outs, cuttings accumulations and well control create a significant source of drilling-related problems and consequent lost time. In addition to lost time incidents, the optimum processes to clean and condition the hole in relation to hydraulics are a significant potential in avoiding hidden lost time. This paper outlines a concept and several case studies to monitor drilling hydraulics by analyzing flow in relation to pump pressure and other relevant sensor channels.
SPE/IADC 140145
Well Construction Hydraulics in Challenging Environments, A.L. Martins, A.F.L. Aragao, P.E. Aranha, M.G. Folsta and A.T.A. Waldmann, Petrobras
Hydraulics play a major role in well construction, especially in narrow operational window scenarios, where the difference between pore and fracture pressures approaches zero. Besides, special geometry wells are becoming attractive alternatives to enhance production. Efficient drilled cuttings transport, minimizing contamination in fluid substitution operations and gravel packing are critical operations to be performed. This presentation focuses on the application of latest design, chemicals, software and equipment technology for drilling and completing in challenging scenarios.

SPE/IADC 140261
Liner Drilling Technology as a Mitigation to Wellbore Ballooning – A Successful Study in the Gulf of Mexico Shelf, S.M. Rosenberg and D.M. Gala, Weatherford
This paper demonstrates the benefit of liner drilling technology to successfully drill the operator’s 7-in. liner in place. This technology provided an effective solution to lost circulation and wellbore ballooning in the Gulf of Mexico shelf. Conventional drilling techniques proved problematic causing the well to exhibit severe lost circulation. Liner drilling technology was identified as the most appropriate technique for setting the liner at planned depth. Ultimately, the correct application of liner drilling technology on this well allowed the operator to reach the intended drilling depth and completion objective.
SPE/IADC 140028
Understanding XLOTs, A. Heger and H.F. Spoerker, OMV
The purpose of this paper is the attempt to understand and prove the shape of the commonly known XLOT curve as well as to offer new theories about fracture initiation at the wellbore wall, SH,max determination from XLOTs and the change of the pressure/volume curve by repeated cycles. The most difficult area seems to be between the leak-off-pressure and the formation breakdown pressure. The paper discusses the basic theory behind the leak-off test procedure commonly applied on worldwide drilling operations, its limitations and possible shortfalls as well as recommendations for the correct execution of the test according to good oil field practice.
Technical Session 8: Hole Positioning
SPE/IADC 140183
A Comparison of Collision Avoidance Calculations, S. Okewunmi, Chevron; A. Brooks, PathFinder
This paper will describe procedures commonly used in the industry for avoiding unwanted wellbore collisions. Exercises have been conducted to compare uncertainty envelopes and estimates of collision probability, calculated by different service companies using different software packages. The exercises showed substantial variation among the results obtained, given the same input data. These results highlight the need for detailed specification of the problem, oversight of the process by suitably qualified personnel and for clear annotation of all results to indicate the methods employed and assumptions made.
SPE/IADC 140192
Improving the Quality of Ellipse of Uncertainty Calculations in Gyro Surveys to Reduce the Risk of Hazardous Events like Blow Outs or Missing Potential Production through Incorrect Well Bore Placement, R. Ekseth, J.L. Weston, A.G. Ledroz, B. Smart, A. Ekseth, Gyrodata
Wellbore position uncertainty estimation (error modeling) is a key element in safe and economical drilling. The quality of the error modeling (ERM) has improved a lot over the last 10 – 15 years through the publication of SPE papers. These papers together form a good framework with one exception – they do not provide a publicly documented methodology for the calculation of the uncertainty inputs for gyroscopic survey tools. Magnetic survey instrumentation ERM inputs have been derived and reviewed externally. However, it has been left to the gyro-service providers to supply gyro model inputs, mainly without any third-party review, audit process or clear methodology. This represents a potential safety hazard where overstated performance may be presented. This paper is an attempt to define a process for the derivation of a brand new set of uncertainty estimates for existing gyroscopic tools based on real downhole survey data.
SPE/IADC 140073
Advanced Reservoir Navigation System and Drilling Technology Maximizes Productivity and Drilling Performance in the Granite Wash – US Midcontinent, S. Janwadkar, M. Thomas, S. Privott, Baker Hughes; R. Tehan, L. Carlson, W. Spear and A. Setiadarma, Linn Energy
Efficient extraction of hydrocarbons from the Granite Wash play poses drilling and geological challenges. The Granite Wash deposit varies throughout the field. Due to the geological complexity, this field requires precise placement and navigation of the wellbore real-time. To overcome these challenges, LWD technology paired with real-time reservoir navigation services were utilized.
This strategy has been implemented to drill several wells with excellent results. Advanced LWD technologies have allowed for precise placement of the wellbore and significantly improved drilling performance.
SPE/IADC 139122
Wellbore Positioning Practices and Challenges in Africa, G.Skinner, Baker Hughes
Understanding the subsurface geometric position of a wellpath is critical, as this data is relied upon by different functional groups throughout the entire life of the field. This paper will highlight challenges that exist in while-drilling wellbore surveying techniques and collision management, with focus on their application in Africa.
A factor encountered in onshore drilling in Africa is survey cost as a percentage of drilling budget. This is especially common in vertical hole sections where inclination-only single-shot surveying is standard practice. The paper explains the benefits of more thorough directional surveying.
Technical Session 9: Tubular 2
SPE/IADC 140159
Analysis of Tubular Failures in Riserless Environment, R. Samuel and R. Adari, Halliburton; J. Gradishar, Shell; A. Willie, Iyoho/Shell
Riserless drilling poses numerous operational challenges. A new modeling approach is proposed to calculate appropriate hook-load values, torque and drag. This method can model situations in which the drill string/casing string is in open water or in open hole under different operating conditions. Both soft- and stiff-string models are used in the tension-force estimation, as well as the wellhead side-loading calculations. Hook-load calculations and buckling limitations for the scenarios in which casing and inner strings are run with drilling mud inside the inner string, seawater in the outer string, and pad mud in the hole below the mudline, are presented. This study compares simulated predictions with actual well data from wells from Angola and the North Sea.
SPE/IADC 139824
Lateral Buckling – The Key to Lockup, R.F. Mitchell, Halliburton; T. Weltzin, Statoil
Buckling tests were performed in the Ulrigg U2, a 2,020-m research well, with a buildup and 60B0 tangent geometry. These tests represent a major advance in the understanding of drill string buckling. This paper presents the calculated drill string positions for two loading tests performed in vertical and inclined sections of the Ulrigg U2 test well.
SPE/IADC 139944
On Interaction Buckling in Platform Conductors, A.J. Adams, Nexen Petroleum
For almost 30 years, the design of platform and jack-up conductors has been based on Baur and Stahls’ famous hypothesis that internal string loads do not contribute to buckling (Baur and Stahl 1980, OTC 3902/SPE 12466). It is a vital result, allowing significant weight and cost savings. However, no derivation was ever given, and the result has remained a folk theorem – widely used, but never proved. The industry has therefore been at risk should the result prove to be a severe approximation, or to have unduly restrictive assumptions and/or limitations. This paper provides a rigorous proof of the Baur and Stahl hypothesis.
SPE/IADC 139939
Collapse Prediction Methodology for the Solid Expandable Tubulars, J. Agata, E. Tsuru, M. Sawamura, H. Asahi and H. Tsugihara, Nippon Steel
This paper summarizes an experimental and numerical study aimed at understanding the collapse resistance of expandable tubular (EX-T) before and after expansion, and the construction of the prediction method for post-expanded collapse. Post-expanded collapse resistance is an important property for EX-T, and high-collapse EX-T is necessary for the realization of expandable tubular monobore. This reliable prediction technique can be useful for casing design using EX-T. However, widely used collapse formulas are not applicable to post-expanded pipe.
Technical Session 10: Rigs, Equipment and Smart Technology
SPE/IADC 140365
Low Force Shear Rams: The Future is More, F. Springett, E. Ensley and D. Yenzer, National Oilwell Varco; S. Weaver, Noble Drilling
With the increased usage of stronger and tougher tubulars in today’s well construction, the ability to shear in the BOP without turning to larger operators is an economic necessity. This paper will discuss the mechanics of shear and how it applies to V-Shear technology of yesterday to current low force shear of today and tomorrow.
SPE/IADC 140086
Thermally Compensated Leak Detection Results in Significant Blowout Preventer (BOP) Testing Efficiencies, C.M. Franklin, R. Cully, IPT Global; T. Sargent, Noble Energy; C. Brown, Hamilton Engineering; G.W. Owen, Devon Energy; S. Griffith, Shell; J. Osmond, Hess
An industry consortium of operators, and service providers, was established for advancing the art of leak detection; with the initial development focused on testing blowout preventer equipment in deepwater. Upon completing the pilot program on five deepwater rigs, the results exceeded original expectations. The software is intuitive, simple and now proven to be rig friendly.

SPE/IADC 139493
Emergency Severance of Casing for Deepwater Operations, a Design Build and Test Program of Novel Technologies, N. Richmond, N.J.S. Bamford and A.S. Bamford, Geoprober Drilling
In deepwater, emergency disconnection while running casing is the action of last resort. An Annular Cutting Tool (ACT) has been developed that can be implemented inside an API housing, spool piece or an extension to a BOP ram body. The ACT has been designed to work with conventional drill pipe blind rams. The cutting mechanism is swarth free and produces a good quality cut for later re-entry to the well. The paper describes the selection and testing of bearing and seals and how the drive and control system was optimized to cut and seal the casing in less than 45 sec required by API RP 53.
SPE/IADC 139888
Condition Based Maintenance: A New Early Leak Detection System for Mud Pumps, A. Kyllingstad and P.J. Nessjoen, National Oilwell Varco
This paper presents a new, patent applied method for early detection and localization of valve leaks in piston pumps. The paper includes field test results showing how the vibration patterns change as a valve leak evolves. The presented system represents a significant improvement compared with current practice where pump leaks are detected manually, normally at late stage when the discharge pressure shows large pulsations.
SPE/IADC 139922
The Next Generation Top Drive and the Lessons Learned from the TDS-1250, G.A. Pickett, J.C. Saski and R. Luher, National Oilwell Varco
With all the emphasis today on the economics of improving well costs and that all the “easy oil” is gone, the industry is faced with finding a way to provide marketable technology to drill more challenging wells even cheaper. The top drive stands out as one of the few pieces of equipment in the critical path. Top drive failures account for a large portion of downtime, thereby increasing costs to drill a well, and the top drive is in essence the drill needed to reach reservoirs that are farther and deeper than once thought possible. Two case studies are presented.
SPE/IADC 140266
Deepwater DP Drilling Rigs on Shallow Water Wells, Can it Work? R. Kadiyala and A. Whooley, MCS Kenny
The steady influx of newbuild rigs into the Gulf of Mexico has flooded the market with 10,000-ft plus rated rigs, forcing smaller rigs to forage elsewhere. This influx is clearly driven by the industries move to deeper and deeper waters. The effect of these changing priorities has led to a shortfall in rigs specifically tailored to shallow-medium water depths. This paper discusses the challenges associated with operating deepwater rigs on shallow water wells.
Technical Session 11: Performance Drilling – Drilling Optimization and Efficiency
SPE/IADC 139841
A Systematic Approach to Performance Drilling in Hard Rock Environments, M. Dykstra, B. Schneider, J. Mota, Shell
In the Haynesville shale, hard rock drilling is one of the challenges in each well. Early attempts to drill through formations required as many as eight bit-runs and 23 drilling days. Significant step-change improvements have resulted in repeatedly drilling this interval with one bit in six days, which equates to a savings of 1 million USD per well. This achievement by the Well Delivery Team is a result of careful bit selection using advanced modeling techniques, conducting bit hydraulic optimization, selecting optimal mud motors, defining a roadmap of drilling parameters versus lithology, training for the drill crews and using mechanical specific energy to define end-of-life for each bit.
SPE/IADC 140333
How to Accelerate Drilling Learning Curves, E. Van Oort, J. Griffith, B. Schneider, Shell
Shell Upstream Americas is employing a highly effective performance improvement group to help drive performance optimization and the delivery of top quartile performance on its wells in the Americas and beyond. Central to this group is a dedicated team of optimization engineers, the innovative use of real-time optimization centers and value-adding root-cause failure investigations. This paper highlights the modus operandi of these optimization engineers, the techniques and tools they employ, and the remarkable results they have been achieving.
SPE/IADC 139848
Integrated Drilling Optimization and Downhole Drilling Dynamics Enables PDC Bits to Drill in the Colorado Region of the San Juan Unconventional Gas Basin, T. Pink, L. Harrell, D. Perez, J. Carrico, P. Mackinnon, NOV
This paper discusses how an optimization process was integrated with a multiplacement downhole drilling dynamics sub to discover what was limiting the performance of fixed cutter bits in the San Juan basin. This paper discusses how an optimization process was integrated with downhole drilling dynamics analysis.
SPE/IADC 140172
Anatomy of the “Best In Class Well”; How Operators Have Organized the Benchmarking of Their Well Construction and Abandonment Performance, P. Rushmore, Rushmore Reviews
Twelve operators came together in 1989 to rationalize the sharing of drilling performance offset data. This has grown into a global program with data provided by over 180 operating companies in over 80 countries and which now covers the completions and well abandonment phases. This paper describes the data, process, analysis tools, benefits and limitations of global well construction benchmarking.
SPE/IADC 140332
Understanding and Managing Bottom Hole Circulating Temperature Behavior in Horizontal HT wells – A Case Study Based on Haynesville Horizontal Wells, K. Trichel, J. Fabian, Baker Hughes
This paper discusses a Haynesville horizontal well case study where temperature simulations were compared and calibrated to actual downhole temperature measurements taken while drilling. After calibration of the model was established, a series of simulations were conducted to investigate the sensitivity of bottomhole circulating temperature to choices of drilling systems, fluids systems, mud cooling systems and well design. This paper will detail the effects on bottomhole circulating temperature and will present optimization guidelines and planning considerations for managing circulating temperatures.
SPE/IADC 140391
Managing New Technology Introduction to Provide Maximum Benefit, A. Hatch, N. Shepherd, P. Diepeveen, E.ON Ruhrgas; G. Affleck, Weatherford
By utilizing multiple strands of new technology in a controlled, managed fashion, Eon Ruhrgas delivered rate of penetration increases of 200% and at the same time increased net to gross by nearly 100% on a recent North Sea development project. The delivery of these new technologies will be reviewed along with the culture of learning and constant improvement fostered by the operator. A case study from the Babbage field will outline in detail the observed improvements in performance.
Technical Session 12: Downhole Tools
SPE/IADC 139830
Axial Excitation as a Means of Stick Slip Mitigation – Small Scale Rig Testing and Full Scale Field Testing, I. Forster, NOV
This paper describes the work carried out at NOV Downhole on an in house designed and built, small scale, vibration test rig which was developed with the purpose of replicating stick slip and studying various stick slip mitigation methods. Full scale field operations where an Axial Excitation Tool technology has been applied have resulted in significant overall improvements in stick slip. With reference to offset data, the paper presents actual field data.
SPE/IADC 140277
New Technologies to Enhance Performance of Section Milling Operations that Reduces Rig Time for P&A Campaign in Norway, E. Scanlon, ConocoPhillips; G. Garfield and S. Brobak, Baker Hughes
In 2008, ConocoPhillips completed the P&A of two of eight water injection wells at the 2/4 W Platform in the Norwegian sector of the North Sea. The average performance was 65 days per well. In mid-2009 ConocoPhillips resumed operations to P&A the remaining six wells. The scope to P&A the remaining six wells was increased to include a second barrier across the Miocene which called for more section milling than the first campaign. ConocoPhillips management challenged the rig team to significantly improve performance on the second campaign. Performance on the final six wells improved dramatically to an average of 46 days.
SPE/IADC 138001
High Performance Wellbore Departure and Drilling System for Accessing New Target, C. Dewey, S. Swadi, S. Alsup and P. Desai, Smith Services
Conventional wellbore departure systems require multiple trips to achieve a specific objective. The industry requires an economical solution to accomplish the objectives in a single-run with good downhole dynamics control and BHA drillability. The re-entry system should be capable of milling a window large enough for obstruction-free BHA entry/new liners. After exiting, the system should drill a full-gauge lateral borehole to the target with good directional control and minimal vibration.
To solve the challenge, new systems technology was developed/tested in three phases. The paper presents field-data from phase one/two and results of ongoing full-scale yard tests with key observations/conclusions.
SPE/IADC 139953
Remote Communication Techniques from Surface to Downhole Tools, P. Joseph, L.E. Mendez and D. Dolyniuk, Baker Hughes
This paper will present new remote communication techniques from the surface to the downhole tools. Primary focus while developing this technique was toward downhole completion tools like packers, anchors and flow control devices. Two methods of communication are discussed. The first method described is communication to the tool using flow-induced signal patterns. The second method is using signal patterns generated by an acoustic source at the surface.
SPE/IADC 139870
Operator’s Recommendations for a Uniform Dull Grading System for Fixed Cutter Hole Enlargement Tools, L. Ulvedal, Statoil, J.D. Enterline, D. Scott, S. Radford, J. Clinkscales, L. Shale and M. Croxton, Baker Hughes
An IADC standard system was defined and implemented in 1991 to accurately permit the dull grading of fixed cutter bits. Now as hole enlargement is one of the fastest growing sectors of today’s drilling industry there is a greater need for an accurate and uniform dull grading system for fixed cutter hole enlargement tools. Through collaboration between an operator and a bit manufacturer, this new dull grading protocol is being proposed to better characterize hole enlargement tool dull conditions. The characterization method will be described.
SPE/IADC 139769
Coating Optimized for Abrasion and Fatigue Resistance for Use in Extreme Well Geometries, J.E. McCormick, J. Le and C. Evans, Weatherford
A new HVOF applied tungsten carbide coating has been developed for use on performance drilling tools for these challenging applications. Extensive testing shows excellent resistance to both wear and cumulative fatigue stress. By combining ductility that resists fatigue stress and crack development with the abrasion resistance of tungsten carbide, a coating is now available for rotating drilling tools in extreme well geometries. Field trials and testing with less ductile versions of tungsten carbide coatings revealed cracks within the coating. A ductile coating is a practical necessity.
Technical Session 13: Deepwater 2
SPE/IADC 139708
Wellbore Stability Modeling and Real-Time Surveillance for Deepwater Drilling to Weak Bedding Planes and Depleted Reservoirs, J. Lang, S. Li, Halliburton; J. Zhang, Shell
Wellbore instability is a main cause of losses in boreholes and represents a serious challenge in the drilling industry. When a well is drilled at shallow angles to thinly bedded shales, it is often highly unstable. Rock failure can occur. These are some of the cases we encountered in surveying offset wells in deepwater Gulf of Mexico depleted reservoirs for a new predrill study. The key solutions are to not only improve wellbore stability modeling associated with bedding planes, rock anisotropy and pressure depletion, but to additionally take into account their impact on horizontal stresses. In the proposed model these factors were considered. Fracture gradient calculations were also implemented to consider rock anisotropy and the depletion. Lab test data of rock strengths with differing loading directions were collected and analyzed. New correlations were developed.
SPE/IADC 140281
A New Player Entry to the Deepwater Market; T. Ouwerkerk, Maersk Drilling
The paper gives an introduction to the motivation and perspectives behind the decision of Maersk Drilling (MD) entering the deepwater market. It illustrates how MD intends to position itself among competitors and how rigs have been equipped to achieve this. It goes into detail about what philosophy MD is following. To communicate this the presentation will introduce the equipment installed on the new built semisubmersibles and the safety and efficiency targeted with this equipment
SPE/IADC 139511
Drill Pipe Cutting at Ultra High Pressure – A Proven Capability for Stuck Pipe Hazards, J. Segura, Weatherford
From conceptual development to laboratory data this paper will describe the need, development, testing and results of ultra high pressure jet cutters and severing tools for use in environments up to 30 kpsi for today ‘s deepwater, ultra deep well market. The first of its kind test vessel allows for actual separation of drill string components at bottomhole pressures with zero tension applied.
SPE/IADC 139929
First Application of Heat-Activated, Rigid Rapid-Fluid System in Deepwater Environment in Mexico Helps to Cure Severe Loss of Circulation: A Case History, J. Castro, L. Solis and J. Urdaneta, Halliburton; V. Arreola, Pemex
This paper focuses on how a severe loss of circulation was treated using a heat-activated, rigid rapid-fluid treatment, restoring full circulation and successfully increasing the window gradient in the first attempt in a deepwater wildcat well in the northern Gulf of Mexico. An engineered solution was proposed for the placement and calculations. It was verified through laboratory tests and in the field. The paper discusses the results of the application and how it was applied in the next drill stage.
Technical Session 14: Drilling Fluids
SPE/IADC 139817
One Sack Rapid Mix and Pump Solution to Severe Lost Circulation, D.K. Clapper, J.J. Szabo, S. Spence, M. Otto, B. Creelman, T.G. Lewis Jr and G. McGuffey, Baker Hughes
A fiber pill formulation has been developed to address common operational concerns that exist with current lost circulation pill procedures. Laboratory testing has demonstrated the ability of the fiber pill slurries to rapidly dewater/deoil and form a sealing plug on ceramic filter discs. Testing also indicates that the fiber product formulated as a weighted pill with barite will form a plug with measurable compressive strength. A few field application is discussed in detail
SPE/IADC 139623
Drilling Fluid Design Enlarges the Hydraulic Operating Windows of Managed Pressure Drilling Operations, D. Oakley and L. Conn, M-I SWACO
With the increasing use of Managed Pressure Drilling (MPD) to mechanically control bottomhole pressures for drilling narrow mud weight windows, little consideration has been given until recently to integrating drilling fluid design and MPD operations for a specific application. This paper describes how the development of low rheology drilling fluids are able to reduce downhole frictional pressures by at least 0.5 lb/gal equivalent density using novel weighting agents that do not sag or settle in a wellbore, yet still provide the necessary drilling fluid density for stable wellbore conditions.
SPE/IADC 139932
Drilling Highly Depleted Formations with Engineered Particle Non-Aqueous Fluids (EP-NAF): South China Sea, M.R. Niznik, A. Lawrence, S.C. Zeilinger, ExxonMobil
A new fluid system (EP-NAF) has been utilized in the Malay Basin of the South China Sea to drill through highly depleted sands (3.7 ppg) with a non-aqueous fluid at elevated densities. The fluid contains sized particles to both bridge and prop open fractures as they occur during actual drilling operations. Formation integrity is gained immediately and does not require additional critical path rig time.
SPE/IADC 140324
The Continuous Measurement and Recording of Drilling Fluid Density & Viscosity, A. Miller, Maersk Oil, R.C. Minton, Mosarric Services; R. Colquhoun, Mud Automatics; M. Ketchion, Baker Hughes, INTEQ
This paper presents the field results of the use of a novel instrumentation package that continuously monitors these properties, exports the data to the logging database and permits trend analysis and the wider promulgation of the information, mitigating the limitations of the current approach. The package design eliminates the requirement for manual sampling. Data will be presented from an HP/HT drilling operation in the UK sector of the North Sea. These measurements will be compared with manual readings and viscosity signatures/trends will be identified and correlated with known events.
Technical Session 15: Cementing and Zonal Isolation
SPE/IADC 139909
Remotely Operated Top Drive Casing Running System Combined with New Cement Head Enables Major Oil Company to Improve Zonal Isolation and Cement Bonding with Enhanced Safety and Efficiency in Caspian Sea, T. Cummins, E. Abrahamsen and I. Killoh, Weatherford
Conventional methods for landing and cementing casing strings in a surface wellhead resulted 140318n zonal communication, mud/cement losses and poor cement bonding. Rig up/down of conventional casing running and cementing equipment required extensive manual handling and man-riding operations on the critical path, with times of 1 hr being common. During this time circulation was not possible, leaving well fluids static and turning them to a gelled state before cementing operations had begun. This gelling led to channeling of fluids, mud/cement losses and poor cement placement. To address these problems, a remotely operated top-drive casing running tool combined with a new, remotely operated cement head were deployed.
SPE/IADC 140242
Predicting Salt Leaching During Drilling and Cementing Operations, M.G. Folsta, A.L. Martins, R.F.T. Lomba, W.F. Cardoso Jr, C.A. Simao and I.A. Sidi, Petrobras; C.E. Dannenhauer, ESSS
This work details a salt solubilization study to be used both for drilling and cementing operations in salt zones. The software developed aims to estimate the amount of salt incorporated by the drilling fluid or the cement slurry during the fluids flow in contact with the salt formation.

SPE/IADC 138852
Novel Solution to Cement Strength Retrogression, S.A. Gibson, BJ Services
With the North Sea being a mature drilling arena, ever more complicated wellbores are required to access remaining deposits and these must be achieved with increasing cost effectiveness for operators. The method of silica addition to cement slurries as a liquid presented here offers direct and indirect financial benefits and direct reduction in personnel exposure to dust. Since starting to market this product, the use of a liquid strength retrogression prevention additive has steadily been gaining acceptance throughout the industry
SPE/IADC 139766
Casing Burst Stresses in Particulate-filled Annuli: Where’s the Cement? I.A. Kalil and A.R. McSpadden, Altus Well Experts
This paper describes the backup support of cemented casing based on analytical analysis and provides a means to determine the increase in burst resistance due to cement. Prior work used cement properties to classify cement as “ductile” or “brittle”. In all but one case in these studies, the cement sheath was a solid matrix that bonded to the casing string, the formation or both. Comparisons are provided for casing burst resistance assuming various backup profiles.
Technical Session 16: Directional Drilling
SPE/IADC 140265
Extended Reach Drilling – Offshore California, Extending Capabilities and Improving Performance, N.R. Armstrong and A.M. Evans, ExxonMobil
SA-16 El Capitan is the latest extended reach drilling (ERD) well to be drilled from the Heritage Platform into the Sacate Field. The application of learnings from previous wells enabled El Capitan to be drilled to 37,165 ft MD (6,938 ft TVD) and 33,682 ft horizontal displacement. The most challenging phases of the well are described in this paper, concentrating on the main engineering areas of focus during planning and execution.
SPE/IADC 140318
Hibernia Well Overcomes Challenges to Further Extend Worldwide Extended Reach Drilling (ERD) Envelope, M. Woodfine, N. Bolivar and S. Trend, Hibernia; S. Ottesen, ExxonMobil
In 2007, Hibernia Management and Development Company (HMDC) began drilling operations on B-16 57 (OPA2). The plan involved drilling an oil producer to 32,000-ft measured depth (MD) and to a total vertical depth (TVD) and horizontal departure that would put the well outside the worldwide ERD envelope. The well was plugged and abandoned at ~20,000 ft in the 12B-in. hole section as a result of several factors including complex geology and wellbore instability. The planning of the redrill began almost immediately. The final trajectory was able to minimize risk associated with encountering unstable zones and complex lithology. Successfully drilling this well required an engineered approach to operations as well as incorporating an ultra thin fluid system in the deeper hole section.
SPE/IADC 139925
Controlling Well Path Trajectory with Rate of Penetration Modulation, S.R. Farley, C.A. Maranuk, B.J. Hronek and C. Jasper, Weatherford
A new system of wellbore directional control has been developed which uses continuous string rotation above a positive displacement motor and bent sub. The goal of this system is to eliminate all oriented drilling in applications up to 4 degrees by 100 ft by employing a low risk, low cost method that maximizes rate of penetration and hole cleaning. At the GTI test facility in Oklahoma, drilling tests yielded successful well trajectory manipulation, delivering up to 3 degrees by 100 ft of controlled directional performance in both 6-in. and 8½-in. hole diameters.
SPE/IADC 140245
Turbodrill BHA Solves Build Section Challenges, Anadarko Basin, C. Staley, G. Bruton, Chesapeake Energy; M. Natanael, J. Kelley and R. Milne, Neyrfor/Schlumberger
The operator wanted to reduce the number of bits/runs drilling the difficult build and lateral sections in its Colony Granite Wash play in Washita County, Oklahoma. The formation contains multiple reservoirs within complex sequences of sandstone, siltstone and shale interbedded with granite/limestone wash. A turbodrill paired with a diamond impregnated bit is normally a viable system to tackle the challenge. However, the turbodrill/impreg BHA was historically incapable of achieving target inclination build rates when initiating the beginning of the curved section.
The engineering team evaluated run data and performed mathematical-based predictive analysis. The study indicated that using a bent housing turbodrill with two bends and an impregnated bit with shorter gauge could yield up to 65% higher build-up rate. The new turbodrill/impreg BHA was run and has set numerous new field performance records.
SPE/IADC 139773
Overcoming Challenges for Drilling High-Dogleg Seferity Curves, S. Janwadkar, O. Hummes, A. Peter, M. Freeman and S. Privott, Baker Hughes; D. Greene, SM Energy; C. Loesel, Forest Oil
Wells in US Shale-gas plays require a DLS of 10-14 deg per 100 ft. Achieving high DLS with steerable motors presents numerous drilling challenges. These challenges led to the development and ultimately the successful testing of a new high-dogleg RSS. The new system drilled all sections, including high-DLS curves, tangents and laterals with one BHA. The system can perform open-hole sidetracks and drill high-DLS curves and laterals with a precise directional control and well placement. The authors discuss the design, simulation criteria and results in different environments
SPE/IADC 140024
Achievements and Lessons Learned from a 4-Year Experience of Extended Reach Drilling in Offshore Dagang Oilfield, Bohai Basin, China, R. Cheng, H. Wang, L. Zou, M. Zhou, D. Sha, C. Liu, CNPC
The long-term continuous exploitation makes it increasingly difficult to maintain sustainable hydrocarbon production onshore in Dagang Oilfield. The shelf sea area of Bohai Basin with an average water depth of about 2.5 m is identified as the main take-over battlefield, which needs to be developed by extended reach drilling (ERD) due to the lower loading capability of subsea thick silt and the inaccessibility of drilling rigs onshore or offshore. Favorable achievements have been obtained during the 4-year ERD play. Four extended-reach horizontal wells with the horizontal displacements larger than 4,000 m have been successfully completed.
Technical Session 17: Managed Pressure and Underbalanced Drilling
SPE/IADC 140267
Integrated Downhole Isolation Valve and Managed Pressure Drilling to Facilitate Development of Sour Fractured-Limestone Gas Reservoir in East Java, Indonesia, G.R. Darmawan, N.B. Sangka, S.D. Susilo, Pertamina; S. Nas, J.S.S. Toralde and A.E. Prasetia, Weatherford
Drilling operations for the development of a sour gas reservoir in the Kujung fractured-limestone formation in East Java, Indonesia are prone to kick-loss cycles. Well control incidents have been experienced on two previous wells drilled in the area. Most of the drilling budget was spent on cement and lost circulation materials to mitigate circulation losses and the resulting kicks. The skin factors of the said wells are therefore understandably high.
In planning subsequent wells, underbalanced drilling was ruled out due to the sour nature of the reservoir, and managed pressure drilling (MPD) was selected. To further ensure the minimization if not elimination of the release of sour reservoir fluids at surface, MPD methods were integrated with the utilization of a downhole isolation valve (DIV). The details of the DIV + MPD system are presented.
SPE/IADC 140289
ECD Management and Pore Pressure Determination with MPD Improves Efficiency in GOM Well, P.D. Fredericks and L. Smith, At Balance; K.J. Moreau, KJM Energy Services
In early 2010 Stone Energy restarted development of the Amberjack field in the Gulf of Mexico. Controlling the equivalent circulating density (ECD) in the narrow window between wellbore stability (14.9ppg) and fracture gradient (15.2ppg) was going to be just as critical now as it was in the past.
Stone determined that they could avoid drilling problems with automated managed pressure drilling (MPD) technology which was unavailable in 2001. Using MPD, Stone managed the BHP in windows ranging from C B10.16 ppg while drilling, C B10.12 ppg while tripping, and C B10.05 ppg while rolling over the mud from 14.8 to 15 ppg. Controlling the BHP and ECD with automated MPD allowed Stone to reach planned total depth in less time and avoid the wellbore instability and well control events.
SPE/IADC 140297
Mist Drilling in Low Pressure, Highly Fractured Carbonates Enhances Image Log Quality and Fracture Discernment. N.M. Nor, M. Balzarini, M. Siddiqui, Shell
Underbalanced drilling is an effective technique to reduce severe losses typically encountered while drilling through vuggy and fractured carbonates. This paper discusses the successful application of mist (N2 and water) for the first time in the Grosmont lease area. The successful experience with mist drilling in these fractured carbonate rocks paves the way for better fracture discernment and reservoir characterization.
SPE/IADC 139683
New Technology, Which Enables Closed-looped Drilling (MPD) from Mobile Offshore Drilling Units (MODU), J.A. Andresen, T. Askeland, Siem WIS
Siem WIS has developed a new seal solution that will be installed inside a riser below the slip joint; this will enable managed pressure drilling from MODU utilizing standard equipment. The new technology will give the operator status of the seals and gives time to evaluate before entering into a well control situation. The presentation will describe the sealing system; qualification and experience (case history) utilizing the Siem WIS closed-loop systems.
SPE/IADC 139842
Drilling Performance Improvement in the Haynesville Shale Play, J. Mota, B. Schneider and J. Billa, Shell E&P; M. Weissman, Drilling Consultant
This paper reviews the key factors that enabled a significant performance improvement in an ongoing drilling campaign in the Haynesville, North Louisiana. The operator has delivered a 60% reduction in drilling times, and a 50% reduction in well cost in less than two years. The performance improvement has been achieved by defining the key performance limiters enabling the pursuit of key technologies and process improvements.
Technical Session 18: Dynamics and Stick Slip
SPE/IADC 139956
Field Experience with an Active Stick-Slip Prevention System, P.J. Nessjoen, A. Kyllingstad, P. D’Ambrosio, I.S. Fonseca, A. Garcia, National Oilwell Varco; B. Levy, Shell
This paper is a field evaluation of an active stick-slip prevention system. Observations and experiences from developer, contractor and operator are shared. The evaluated system is active with smart control of the top drive, meaning that the top drive speed is varied in a way that dampens stick-slip oscillations. It is software based, requires no extra instrumentation and can be implemented on virtually any types and brands of top drives.
SPE/IADC 140044
Results of the July 15, 2010, IADC Stick-Slip Mitigation Workshop, K.A. Womer, KWTS; D.R. Torkay, G. Villanueva, Seawell Americas; T. Geehan, M-I Swaco; J. Brakel, Shell; D. Pirovolou, Schlumberger; D. Reid, National Oilwell Varco; M. Killalea, IADC
This paper presents the results from a workshop on stick-slip mitigation held in Houston on July 15, 2010. This workshop, sponsored by the IADC ART Future Technology Subcommittee, brought technology leaders and engineers together to discuss issues related to stick-slip mitigation. Its goal was to educate the industry regarding existing technologies available to address this issue as well as identify the need for possible future technologies. The paper describes the unique structure of the workshop.
SPE/IADC 140347
Testing the Combination of High Frequency Surface and Downhole Drilling Mechanics and Dynamics Data Under a Variety of Drilling Conditions, B. Lesso, M. Ignova, F. Zeineddine, Schlumberger; J.M. Burks, B. Welch, NOV
NOV developed an instrumented surface sub that replaces the saver sub at the bottom of the top drive on a rig ‘s travelling assembly. It measures in real-time tension/compression, torque, RPM, surface pump pressure among others at the top of the drill string. These measurements, made at 400 Hz, are not dampened by the drill line and sheaves. Schlumberger developed a drilling mechanics sub that measures tension, torque, RPM, internal and annular pressure between 200 and 2000 Hz.
A test was conducted at Schlumberger ‘s directional drilling test facility near Cameron Texas. Four different BHACs were run to evaluate downhole behavior for milled tooth and PDC bits and directional drilling in surface rotary mode as well as with steerable motors. This paper presents some of the wide range of findings.
SPE/IADC 139996
Development of an Innovative Model-Based Stick-Slip Control System, J. Rudat, University of Hanover, D. Dashevskiy, Baker Hughes
This paper presents an innovative model-based stick-slip control system. It is based on a model of the drilling process which predicts the intensity of downhole vibration with respect to drilling parameters. To overcome the limited bandwidth of the typically used mud-pulse telemetry systems, models are identified downhole in the dynamics measurement tool. The paper presents field tests performed to evaluate the stick-slip control system and investigation of how model parameters can be identified from measurements and how well the identified models represent the drilling process.
SPE/IADC 139893
Underreamer Dynamics, B. Meyer-heye and H. Reckmann, Baker Hughes; G.P. Ostermeyer, Technische U. Braunschweig
Dynamic cutting force models for bits and reamers have been developed according to the results of a cutting force analysis. These models contain weight, torque, and residual side force. They were implemented into a highly sophisticated drill string model using a finite element analysis. Dynamics simulations in time domain of complete drills trings with regard to the cutting forces at bit and reamer are shown. Interactions of pilot bit and reamer coupled by the BHA are investigated using this model.
SPE/IADC 140011
Analytical and Experimental Backward Whirl Simulations for Rotary Steerable Bottomhole Assemblies, D.R.H. Stroud, L.A. Lines and D.J. Minett-Smith, Weatherford
A unique analytical model has been developed to predict BHA dynamic behavior, gaining better understanding of dominant factors that cause backward whirl. A full-scale test rig has been constructed that is capable of initiating and sustaining full rolling contact backward whirl, repeatably, reliably and safely. Excellent correlation between analytical simulations and full-scale experimental results has been achieved.
Session 1 e-posters:
SPE/IADC 140069
Exploration of the Interaction Between Drill Bit Gauge Profile And Point-the-Bit Rotary Steerable Systems, L.A. Lines, M. Larronde, D. Stroud, Weatherford.
This paper investigates bit passive gauge profiles for point-the-bit rotary steerable systems (RSS). Results of theoretical analyses, laboratory testing and field studies are presented, showing a step-change improvement in drilling performance and efficiency. A methodology has been developed for exploiting lateral stability afforded by extended passive gauge, without limiting steerability or creating stick-slip or high torque.
SPE/IADC 139829
Casing Design with Flowing Fluids, R. Mitchell, Halliburton
Most of the casing design load calculations that have been published are based on static fluid pressures. In this paper, the general equations for the balance of fluid momentum are combined with the equilibrium equation for the pipe. The effective force then emerges as a natural combination of pipe force and fluid force terms. Numerical examples are caluated to illustrate the new concepts.
SPE/IADC 140181
Case Histories of Recent Field Results for Advancement in Milling of Cemented Tubulars, M.A. Haq, J. Fisher, T.F. Bailey, Weatherford
Milling success depends on technologically advanced mill design and efficient job execution. This paper describes case histories of a new 2-pod mill designed for milling cemented tubulars. Field results have shown better performance in terms of higher rate of penetration (ROP) and longer service when compared to conventional mills.
Session 2 e-posters:

SPE/IADC 140224
Documentation of Risk and Cost-Reducing Potential by Utilizing an Automatic Supervision and Decision Support System During Drilling a Challenging HPHT Well, R. Rommetveit, S. Odegard, C. Nordstrand, eDrilling Solutions; K. Bjorkevoll, SINTEF; M. Fjeldheim, Total
A very challenging HPHT well has been drilled while running an advanced decision support and ECD management system. The system has been running in parallel with the operation, and used all available real-time drilling data in combination with real-time modelling to monitor and optimize the drilling process. This information was also used to visualize the wellbore in 3D in real time. Automatic forward-looking of ECD was also part of the active system. It was implemented in Total E&P Norge TASC (Total Activities Support and Collaboration) Center in Norway. The system was piloted by Total, and was, therefore, not fully integrated in Total’s work and decision process.
Experiences from use of the system clearly show that the forward-looking capability gave early warning of a near-future kick situation and the diagnosis functionality gave first an early warning of an upcoming kick and then a firm diagnosis. A loss situation was warned against and eventually diagnosed by the system. Potentially at least 10 rig days, large amounts of drilling mud and a squeeze cement job could have been avoided by fully utilizing the system.
SPE/IADC 139943
Automation of the Drilling Fluid Mixing Process, Field Experiences and Development from North Sea Operations, O. Kvame, Seawell; B. Blom-jensen, Y. Bastesen, J. Sandvik, National Oilwell Varco
This paper summarizes experiences and developments from several years of operating at different levels of automation to bulk transfer and the drilling fluid mixing process with a focus on rigs operating in the North Sea. This paper will address systems from semi-automated sack cutting units to fully automated drilling fluid process systems.
Session 3 e-posters:
SPE/IADC 139954
Exploration Drilling Campaigns – Optimized Drilling Performance Using Drilling Cconsortium Management, B.T. Ribesen, Det Norske Oljeselskap; K. Horvei, Halliburton; T. Magnussen, AGR; A. Saasen, Det Norske Oljeselskap/Univerity of Stavanger; T. Veiberg, AGR
This paper describes in detail, based on a three-year field experience, how an operator, a well management company and an integrated service provider efficiently run a drilling campaign. During this campaign five different operators have used this management system to efficiently drill exploration wells. As is shown, this combination of companies using a rig continuously throughout the campaign has produced several of the best exploration well drilling operations on the Norwegian continental shelf.
SPE/IADC 139408
Approaching the Technical Limit: Mature Basin Benefits from Influx of Advanced Drilling Rigs/Tool Technology, H. Marquez, M. Crovetto, Smith Services
An operator working a mature field in southern Argentina wanted to utilize the latest drilling technologies to establish a new field benchmark. The basin has been producing hydrocarbons for about 100 years and most operators active in the area were reluctant to apply high-end technology to develop what is to be marginal reserves.
In spite of the economic risk, a plan was initiated in Q1 2009 to deploy new automated flexible drilling rigs in conjunction with high-performance downhole tools designed to efficiently utilize the rigs’ increased hydraulic horsepower capabilities. Due to hole deviation problems, a reliable yet cost-effective vertical drilling system was employed. The new tools have been run on several wells in El Huemul field with outstanding results.

SPE/IADC 140051
Challenges of Drilling in The Chilean Altiplano. M.C. Holdeman, G.A. Pidcock, W.M. Levy and H. Figueroa, Estrella Servicios Petroleros; R. De Angelis, Geoestrella; R. Lyon, Geotec Boyles Bros.
Effects of altitude, geography and climate must be taken into account in the overall planning of a Chilean drilling operation. The effects on personnel can vary and are somewhat unpredictable. There are specific tests that must be performed before working at high elevation that can detect potential problems and there are mitigation methods that can be applied on site that can help personnel increase performance.
Equipment is also affected by the high elevation and the climate. The lack of oxygen at elevations over 4,000 m results in a loss of power for internal combustion engines of more than 40%. This is exacerbated by the limited experience operating large drilling equipment at high altitudes. Overcoming these challenges can only be achieved through careful planning and by selecting specific technologies to mitigate the effects of the environment.
SPE/IADC 138922
Rigorous Identification of Unplanned and Invisible Lost Time for Value Added Propositions Aimed at Performance Enhancement, H. Spoerker, OMV; G. Thonhauser and E.E. Maidla, TDE
During the SPE ATW on automation, it was identified that one of the major opportunities in the drilling and completions industry is the identification of non-planned events. The key point was to share risk and reward by using an unbiased system that is able to accurately measure, in an automated form, most of the routine drilling and completions operations that will be compared against pre-agreed benchmarks to establish if the goals and objectives are being achieved.
This paper explains how automatic operations detection are carried out to address the proposed challenges and the necessary reporting and user interaction needed. The theory and one case history are presented.
Session 4 e-posters:
SPE/IADC 140205
Quality Assurance of Wellbore Stability Analyses, B.S. Aadnoy, University of Stavanger
The paper will first present examples of inadequate wellbore stability analysis and typical error sources. Then several field cases will be derived in detail showing the correct models for 3-D analysis, including assessment of in-situ stresses and their directions, definition of stress state, define bounds on in-situ stresses, penetrating and non-penetrating situations, elastoplastic well barrier, effects of temperature and depletion and how to calibrate the models with fracture and breakout data.
SPE/IADC 140327
Hydrocarbon Reservoirs Where Proactive Geosteering Is Most Likely to Succeed, D. Seifert, Saudi Aramco; R.E. Chemali, M.S. Bittar, Halliburton G. Althoff, A. Lotfy, Halliburton
Proactive geosteering is the fastest-growing form of geosteering. It enables reservoir exits to be anticipated before they occur and well paths to be altered to navigate within the best portion of the reservoir. This paper demonstrates that proactive geosteering is most likely to succeed when drilling in a high-resistivity reservoir surrounded by low-resistivity formations. These observations are substantiated and quantified with models and actual case histories.
SPE/IADC 140045
Real Time Pore Pressure Prediction Using LWD and Borehole Seismic Data Assists In Mitigating Risk on an Appraisal Well Offshore Malaysia, A. Ahmed, L. Anis, S. Fey, R. Hussain and H. Rahim, Schlumberger; T.B. Hua, A. Mohaideen, Petronas
A successful methodology was employed drilling an appraisal well offshore Malaysia. To drill to TD safely, casing point selection and mud weight management were critical during the drilling phase. Type 1 and Type 2 overpressure mechanisms were expected. Traditionally LWD measurements like resistivity and sonic are employed but with the advent of seismic while drilling, an extra acoustic measurement is introduced to increase the confidence in pore pressure prediction workflow.
The challenge was to manage the mud weight in the 8½-in. hole section, where a second pressure ramp was expected but uncertainties were higher both for magnitude and depth at which it would occur. By employing the real-time pore pressure prediction workflow, Petronas was able to safely and successfully drill to TD without losing the well.
SPE/IADC 139910
Rebuilding a Tool Joint: Best Practices to Avoid Failure, G. Pettit and S.R. Gokhale, T.H. Hill Associates
Weld repair of tool joints has become common practice in the industry as a method to increase the outside diameter of the joint. In rebuilding, soft metal is welded to the tool joint surface which allows it to meet Premium Class dimensional requirements. While expedient and generally accepted, welding on the outer surface of a tool joint should be avoided. The welding process re-heat treats the steel in an uncontrolled manner, which increases the likelihood of failure. This paper presents the results from two failure analyses in different geographic regions. This paper provides the lessons learned from these failure analyses, including field data and the metallurgical results.
Session 5 e-posters:
SPE/IADC 140211
Which Drill Pipe is the Less Resistant to Buckling: Steel, Aluminum or Titanium Drill Pipe? S. Bensmina, S. Menand and H. Sellami, Mines ParisTech
Drilling equipment manufacturers and contractors have to meet higher requirements to manufacture and operate top-quality tubular in these severe environments. However, with the increasing complexity of drilled wells, steel may become a limiting drill pipe material. A non-steel alternative material may exist such as aluminum, titanium or composite materials.
The use of these new materials in extreme drilling environments raises many questions relative to their resistance in terms of fatigue, static and dynamic load, corrosion and buckling. A new numerical buckling model, taking into account doglegs, friction, rotation and tool joint effects, has been validated with lab and field experiments with non-steel material. Available steel, aluminum and titanium drill pipes have been modeled and classified according to buckling resistance.
SPE/IADC 140357
Natural Gas As a Fuel In Drilling Operations – Analysis, Testing and Implementation, D.G. Hill, J. Johnson, J.W. Bell and N. Mayer, EnCana; H. Giberson; R.P. Hessler and W. Matthews, Ensign United States Drilling
The application of dedicated natural gas engines to power drilling rigs is a new and environmentally responsible approach to operations. The use of dedicated gas engines on drilling rigs provides the following advantages: reduced emissions, reduced cost, improved maintenance characteristics and provides a model for the industrial application of natural gas as an engine fuel to support energy security. This paper describes the process used to evaluate, test and implement dedicated natural gas drilling systems in drilling operations in Wyoming (Jonah) and Louisiana (Haynesville).
Session 6 e-posters:
SPE/IADC 140320
Delivering Performance in Shale Gas Plays: Innovative Technology Solutions, F. Baez, S.P. Barton, NOV
The paper focuses on technology development for improving drilling performance in natural shale gas plays. A combination of technologies can be used to dramatically increase performance in challenging sections by limiting resistive torque, maximizing bit hydraulics and improving weight transfer. In each example, a separate engineered solution is introduced. Case studies are documented where solutions have proven extremely successful in gas shale plays.
SPE/IADC 139926
Fluid Hammer Drives Down Well Costs, R. Staysko, B. Francis, Suncor Energy, B. Cote, BBJ Tools
An innovative proven new tool, the fluid hammer, provides axial percussive force and effective weight transfer to the bit which increases the rate of penetration (ROP) from 30-50% with no impact to bit life. Suncor Energy Inc, together with BBJ Tools in Alberta, Canada have developed and applied the fluid hammer in wellbores with excellent results. The study compares geological formations, compressive rock strength, mud weight and BHA parameters such as weight on bit, rpm, hole drag and ROP.
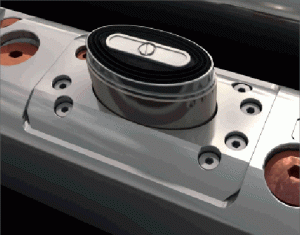
SPE/IADC 140337
New Sampling and Testing-While-Drilling Technology – A Safe, Cost-Effective Alternative, M.A. Proett, S. Eyuboglu, J. Wilson, T. Solbakk, Halliburton
Newly introduced formation sampling-while-drilling (FSWD) technology can significantly reduce costs because the testing and sampling can be performed during the drilling process. This paper demonstrates an economic model using field examples to evaluate the cost benefit between using WFTP and FSWD fluid sampling operations performed in deepwater fields.
SPE/IADC 140249
Acquiring Formation Pressure Measurements In Challenging Borehole Conditions, M. Piber, RAG, S.C. Ash, J. Hemsing, R.S. Kuchinski, Weatherford
The Compact Formation Tester (MFT), of diameter approximately 2.4 in., was deployed in memory mode and conveyed to test depth. Extensive operational planning and pre-job modelling was completed to allow optimum data acquisition while minimizing operation time. All tool data were stored in onboard memory for retrieval after the formation tester returned to surface. Twenty two pressure stations were attempted in two wells to a depth of 2,250 m under borehole conditions where information is usually not attainable. Several examples are presented to demonstrate this new technique was successful.
Session 7 e-posters:
SPE/IADC 140117
Cutting the Cost of HP/HT Clean-Ups – Novel High Density Clean-Up Package Enables Brine Reclamation and Reduces Costs, M.H. Richmond, A. Hutton and M. Davidson, Baker Hughes; B. Frost, S. Leon, S. Howard, Cabot Specialty Fluids; M. Jaspars, University of Aberdeen
A requirement for high-density, solids-free clean-up fluids drove the investigation into the use of cesium formate (CsCOOH) as the base brine. The use of CsCOOH brings unique challenges to the clean up, most notably, the cost implications. The high price of CsCOOH brine means any losses could severely impact upon the cost of the clean-up operation. Furthermore, any brine used in clean-up pills that could not be recovered for re-use would have to be considered as lost. It was, therefore, imperative to return the brine to its original condition thereby avoiding the need to dispose of a very expensive commodity. This paper looks at the laboratory testing surrounding the development of a high density clean-up fluid (HDCUF) and the ability to remove the contamination from the brine.
SPE/IADC 139534
Preliminary Test Results of Nano-based Drilling Fluids for Oil and Gas Field Application, M. Amanullah, M.K. AlArfaj and Z.A. Al-Abdullatif, Saudi Aramco
A nano-based drilling fluid was developed using a blend of nanos and nanostabilizer to study the rheological and filtration properties and evaluate its suitability for oil and gas well drilling. Initial mud formulation indicates that development of a functionally viable, physically stable and homogeneous and also long lasting nano-based drilling mud is difficult using water or salt water as the fluid phase. However, use of a suitable viscosifier at a right concentration and adoption of a special preparation method lead to the formulation of a nano-based drilling mud with desirable rheological and filtration properties. Initial test results indicate that the newly developed nano-based drilling mud produces suitable high and low end rheological properties.

SPE/IADC 140241
Application of Tandem Rotary Steerable-Positive Displacement Motor Bottomhole Assembly in Drilling Horizontal Wells: Case Study of Three East Siberia Wells, Z.M. Okafor, A.J. Buchan, D. Diyanov, S.A. Rawlins, Schlumberger; G. Zhadan, Y. Nikitenko, Vankorneft
The Vankor field in East Siberia is predominantly developed using horizontal wells drilled into the Yakolev and Nizhnekhet reservoirs. Traditionally, the wells have been drilled with steerable PDMs, in 2008 RSS tools were introduced along with LWD technology and this provided significant performance improvements in the 8-in and 6-in. sections. To further improve on drilling performance an engineering study was conducted in 2009 to assess further opportunities for increasing the annual cumulative meters drilled on the project. New BHA designs delivered better drilling performance outperforming conventional power drilling with over 350% improvement in ROP and 12 days saved per well section. The drilling cost savings realized from applying this new technique is in excess of $500,000 per well.
Session 8 e-posters:
SPE/IADC 139855
The First Successful Short Radius Re-Entry Well in Deep Gas Drilling in Saudi Arabia. J.K. Verma and S. Ganda, Schlumberger; S.A. Khamees and H.D. Okwa, Saudi Aramco
This paper discusses the planning and execution of the first successful short radius sidetrack in the deep gas drilling in Saudi Arabia. ANDR-XYZ was sidetracked from vertical at 12,242 ft and built inclination to 90B0 with maximum dogleg severity recorded as 39B0/100 ft. The short radius sidetrack was chosen among three other options. The only technical and economic approach to re-enter the well was to sidetrack in the 7-in. liner. The successful delivery of this well resulted in saving of 45 rig days compared to the other options.
SPE/IADC 140375
Enabling Technology Optimizes Dynamic Mud Weight Management and Reduces Well Costs Associated In Drilling Operation, T. Barbato, Louisiana State University; A.S. Cenberlitas, D.M. Gala, Weatherford
The advent of the new technology, Micro-Flux Control (MFC) System, has enabled a new safer process and practice in defining uncertain downhole limitations from wildcat to mature fields. In this paper, description and features of the MFC system and case studies with real field data are presented. This paper includes actual field cases from recent wells drilled in United States, North Sea, North Africa and Asia Pacific.
SPE/IADC 139989
Conventionally Undrillable Open Fractured Reservoir Drilled Using Managed Pressure Drilling Technology, I. Hammoudi, K. Kartobi, Sonatrach; H. Qutob, M. Arnone, F. Torrez, N. Barakat, Weatherford
The Nezla Field is located in the Triassic Basin in Algeria. This field represents many challenges for conventional drilling due to the complexity of the geological structures, one of these is the Quartzites de Hamra formation, a gas reservoir sandstone highly tectonically fractured. The drilling history of this formation reports events of total fluid losses leading to gas kicks due to the loss of hydrostatic head in the annulus. This paper describes MPD application and presents the successful application of the technique to enhance Nezla field exploitation.
SPE/IADC 139839
Mitigating Stick-Slip in Deep Drilling Based on Optimization of PDC Bit Design, G. Pelfrene and H. Sellami, PL. Gerbaud, Mines ParisTech
Deep-hole drill string vibrations are an important cause of premature failure of drill string components and drilling inefficiency. PDC bits are more susceptible to the stick-slip phenomenon characterized by intense RPM fluctuations of the drill bit. Based on full scale laboratory drilling tests and numerical simulations, this paper aims at understanding the dynamic behavior of the bit/rock interaction and assessing how stick-slip depends on bit design.
i am thair waseem from pakistan i want to regested my school with IADC PLS REPY
reg gard
rig tec drilling schiil