Completions, MPD, automation await industry standardization
Critical issues in drilling & completions with Hege Kverneland, corporate VP, chief technology officer, National Oilwell Varco
By Diane Langley, editorial coordinator

What are some of the key drilling and completions challenges facing the industry today?
Some of our customers and oil companies have told us that the drilling aspect of operations is a good, integrated process and is relatively standardized. But when it comes to completion, there are many different activities and concerns taking place. I can point to comments received from customers that say the new drilling rigs focused too much on drilling and too little on completions and the logistics around this operation. Operators would like for us to look at more standardization in the completions segment. The industry needs to work closer together to solve this problem and identify areas where standardization is applicable.
The industry is talking a lot about managed pressure drilling (MPD). More challenging wells are being drilled under higher pressure and with smaller differences between fracture and pore pressures. A more standardized system for MPD would help to get cost out of the equation. We are being asked to standardize more – everything from MPD to automating the drilling process to automating the completion process. This is the biggest challenge.
How is NOV responding to these challenges?
We are always looking into the possibility of improving the drilling and completion process and how this can be done smarter and cheaper. NOV is looking to connect what’s happening downhole to what’s happening on the rig by closing the loop, so to speak. The goal is to control the topside equipment and pipe-handling equipment according to well conditions.
Another focus is to reduce downtime of the equipment, for example, by utilizing redundancy in the design of the equipment. Another option is implement condition monitoring systems for the machinery in order to better plan for maintenance. Today, the completion operation requires that extra equipment be brought to the rig, and this adds a logistics aspect to the scenario. While we are looking at reducing the cost of the completion side, we will continue to work on reducing drilling costs as well. We are faced with another challenge in that we, as an industry, need to sit down and say where we can be more efficient, where we can be more open and work together – somehow change the business model.
What mechanical components and technologies have been proven to meet these challenges?

We are really focusing on how to better deal with information gathered from downhole. Real-time downhole measurements to the rig, instead of mud pulsations, effectively increase the amount of data available on the rig while making it easier to control the surface equipment and formulate the right decisions.
IntelliServ has been developed to provide high-speed, high-volume, high-definition, bi-directional broadband data transmission to measure, evaluate, monitor and actuate in real time. More instrumentation/sensors downhole need to be “IntelliServ-ready” and available for customers to get increased value from the service. IntelliServ will be very valuable in the future as more challenging wells are drilled, especially when it comes to MPD operations. Knowing the real pressure in the well at different locations in the drillstring is also very valuable.
Stick slip represents another industry challenge; there is a high cost factor associated with downhole vibration that ruins the drill bit and other downhole equipment. NOV has developed a system called SoftSpeed to detect and prevent stick slip from occurring without the use of downhole sensors.
Our continued effort to optimize the drilling process has been furthered by the Advanced Drilling Systems (ADS) service that attempts to optimize the bottomhole assembly that is being used. The ADS system employs a high-definition data collector (HD black box) that measures vibrations and abnormal behaviors downhole. When the well is drilled and the black box is pulled out of the hole, the data collected in the black box is analyzed by NOV’s experts. Suggestions and changes to the bottomhole assembly are then made to optimize the drilling performance on the next well. Often many wells are drilled in the same area with similar drilling formations, and we can optimize the drilling performance on the next wells drilled.
Some years ago, Transocean challenged the industry on how to make a top drive better and more reliable. The top drive is the single piece of machinery on a rig that causes the most downtime. By focusing on modular design, redundancy on components, and easy repair and replacement of parts in case of failure, NOV introduced our new TDX 1250 Top Drive, which is smaller and lighter than top drives with similar capacity. We are now developing smaller-capacity versions of the TDX Top Drive but still focusing on modularity, redundancy and easy repair to increase the uptime of the equipment.
Recently NOV introduced another new technology that has impact on blowout preventer safety – a low shear ram. This shear ram needs less force to shear the pipe than “standard” shear rams, and we have performed numerous tests at our facility in Houston to prove and validate this patented technology. The ram is smaller and more efficient than conventional BOP rams, requiring a minimum of two times less force to shear.
Will NOV continue to invest heavily in the drilling and completions segment? If so, where will the majority of the investment be focused and in what service areas?
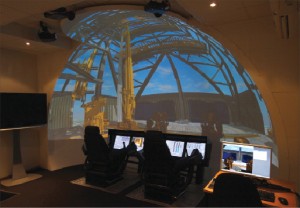
We will continue to invest in drilling and completion, but we are also investing in the FPSO segment. We recently acquired Advanced Production and Loading (APL) in Norway, which designs and manufactures turret mooring systems and other products for floating production, storage and offloading vessels (FPSOs) and other offshore vessels and terminals.
Distribution services is also an area that we will continue to expand. There is a cost saving to be realized when all the parts and needed materials are available on the rig, whether offshore or on land. We are thinking the same for drilling as we are doing in our manufacturing plants, making it easier for the customer to do business with us. The “RigStore” solution we offer means that NOV is storing the parts and equipment on the rig free of charge, and the customer doesn’t pay for it before they actually take it out of Rig Store and use it.
Will the Macondo incident have an impact on the way your company conducts its operations?
I don’t think so, but there will be more requirements related to equipment certification and maintenance. It will not have an impact on new products but will change the repair side of the business. In the North Sea, there are government requirements for equipment to be recertified after, for example, two or five years. The intervals between the re-certifications vary with the type of equipment. This means that the equipment is sent onshore for different type of checks and tests, for example, verification of welds and wall thicknesses, performance using new pressure tests, determination of wear and tear in general, and refurbishment of the equipment. I believe there will be more focus, and maybe government requirements, on equipment maintenance and recertification in the GOM as well. This will mean more work on the repair/service side of the business.
What challenges stand in the way of ensuring that quality objectives are being met?
Training is an important issue, both internally and externally. SPE/IADC conferences during the last decade have focused on “the big crew change” in the drilling industry, with “the old guys” leaving and younger people coming in. I personally am not that afraid of the “big crew change” as long as we train our people. And they also have a lot of good, new ideas to bring to us! But it is our responsibility as an industry to train our people and to improve quality and safety. NOV has set up training facilities in several places in the world – Houston, Norway and Singapore – and is in the process of setting up a center in Brazil.
To improve quality, we test all of our equipment before we ship it to the customer – well and factory acceptance tests. This is something that we have done for a long time, but we are always looking into how we can improve this further.
The newest type of testing that we are expanding in now is what we call hardware-in-the-loop simulations. We use this technique to test complicated control and software systems before actually installing the equipment on the rig. The control system “believes” that the machines are there, and we can simulate “the real world” without the machines being there. By doing this, we can reduce costs and get new products faster to the market, while making sure that the equipment is safer to maintain the quality component.
As sharpening performance and cutting costs are usually operating imperatives, what issues stand in the way of achieving these goals?
We need to review our business models and determine how we can work together as an industry. The industry needs to interact differently than we do now.
Overall, what hard truths about drilling and completions equipment are suppliers facing today?
More technology needs to be included in the design of the big drill vessels today. Technology must be made available to help drillers and operators, making it easier for them to make the right decisions. It is not really technological equipment that is expensive but rather the services that surround the equipment. If we can better prepare the rigs for both drilling and completion scenarios, this will drive the cost down.