ICD completions, optimized cleanup practices maximize productivity for horizontal wells
By Ali M. Shahri, Khalid Kilany, J. Eric Lauritzen, Saudi Aramco; Nashat Hassan, Varma Gottumukkala, Olusegun Ogunyemi, Schlumberger
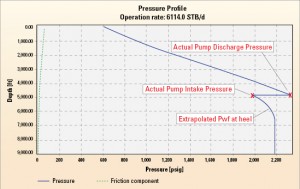
When Saudi Aramco switched to oil-based mud (OBM) to drill new horizontal wells with inflow control device (ICD) completions, the operator encountered problems that included increased solids, thick mudcake, and inability to adequately clean up and flow back these long horizontal wells.
Working with Schlumberger, field evaluations and a comparative case study were conducted that examined different cleanup methods. These included coiled-tubing-deployed nitrogen kickoff and natural flow versus chemical treatments. Each well also had an upper completion with an electrical submersible pump (ESP), a key component in evaluating the effectiveness of each method. Factors such as cleanup time and flow rate were also investigated.
The study resulted in best practices for the cleanup of long horizontal wells, drilled in sandstone reservoirs with OBMs using ICD completions. The key component of these best practices includes the use of chemical treatments to help break up the mudcake, particularly when flowback rates must be kept low (below 25 psi). Additionally, conditioning OBMs to adjust the formula and particle sizing and concentration to avoid damage mechanism is also recommended.
In a field application of ICD completions combined with the best cleanup practices discussed here, the operator was able to flow back all wells and achieve 100% oil production at no additional intervention cost.
This article provides an overview of the comparative study and findings, with a focus on cleanup. Other significant challenges and design factors are described briefly for technical and project context.
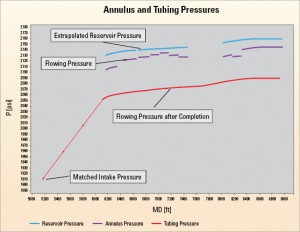
OVERVIEW, CHALLENGES
New wells were drilled in Safaniya, one of the biggest offshore oilfields in the world, located in the northern area of the Arabian Gulf in Saudi Arabia. Forty years of production experience in the field has shown that these sands are unconsolidated and have potential for fines migrations, which can plug screens, perforations, tubular and surface flow lines.
Horizontal wells were drilled to maximize reservoir contact for improved recovery. However, in these sandstone reservoirs with heterogeneous permeability, horizontal wells can result in pressure variations along the laterals and across layers, uneven reservoir sweep and early water/gas breakthrough.
To mitigate these problems, the wells were completed with integrated sand screen and ICD completions. ICDs are designed to balance inflow distribution along the entire wellbore and counteract the effects of heterogeneous reservoir properties. ICD completions also help to create the required pressure drop for mudcake breakup in flowback and cleanup operations.
Sand control and optimum screen size were studied using grain-size distribution tests and selection criteria. Optimum sand control that creates minimal restriction to production is based solely on the ability to retain sands without plugging.

Other key challenges that had to be addressed to optimize performance in this development scenario are discussed below.
• Formation damage during drilling. Drilling fluids are designed to create a low-permeability mudcake during drilling to minimize invasion and formation damage. Near-wellbore damage has the greatest impact on productivity and can be particularly problematic in open-hole completions that do not have perforations to bypass this near-wellbore damage. Wellbore flowback and mudcake cleanup are crucial to well productivity.
In these wells, core flood tests determined that formation damage mechanisms in these wells were poor mudcake cleanup, fines migration and fluid retention. The poor cleanup was attributed in part to drawdown pressure applied at reservoir depths during initial flowback that was limited to about 15 psi because of high reservoir permeability and flow restrictions associated with flare equipment on the rigs.
• Drilling fluids and associated solids invasion. Based on experience in this field and past drilling performance problems with water-based mud (WBM), new wells were drilled with OBM. Benefits include increased wellbore stability, lubrication, and temperature stability and reduced risk of differential sticking.

However, OBMs can also cause problems, such as increased likelihood of particle invasion, reduction of relative permeability to oil, and blocks in sandstone reservoirs caused by emulsifiers used in the OBM – problems that are of great concern when fines migration is already an issue.
• Cleanup processes. In most cases, backflow from the reservoir is expected to lift mudcake and remove infiltrated particles, but effectiveness depends on mudcake quality, applied drawdown and inflow rate along the wellbore. To remove mudcake typically requires a minimum drawdown of 25 psi. As mentioned, drawdown for the wells studied was limited to about 15 psi.
CLEANUP PROCESSES
The cleanup processes studied included flowback without any chemical treatment and flowback after chemical treatment using treatment fluids.
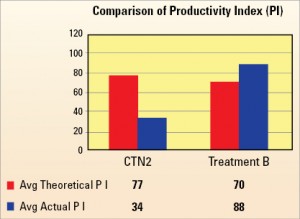
• For flowback without chemical treatment, ICD screens were run inside the open hole. Nitrogen was used to unload the well and pumped in through coiled tubing. After the well was kicked off and flowed to surface with 100% oil traces, it was killed by circulating brine for flow line hook-up at a later stage.
The upper completion was run in the hole, which included an ESP and formation isolation valve (FIV). To function-test the ESP, evaluate the flow rate and clean up, the well was produced for a short time. The ESP gauge data provides intake and discharge pressures at pump depth (Table 1).
• Flowback after chemical treatment. Similar procedures were used for the chemical treatments tested. After the ICD screens were deployed to total depth, water-based surfactants were used to displace the OBM drill-in fluids and reduce filter cake plugging of the sand screens, which testing had shown was also a problem.
OBM conditioning and surface screen testers were used to prevent screen plugging from OBM solids, and chemical treatments were also applied to screens.
Chemical treatments were allowed time to soak while test strings and upper completions were being run. Then the wells were flowed back and tested, observing flowing pressure, rate, watercut and both filter cake and chemical residue.
• Evaluation methods. Cleanup methods were evaluated using these two methods: 1) well performance from production logging tests (PLTs) with ESP real-time data monitoring, and 2) comparing theoretical and actual PI. (Discussions of these methods can be found in SPE paper 120651.)
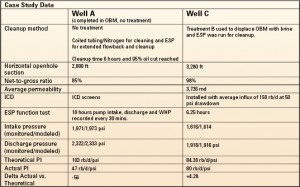
CASE STUDY RESULTS
Over a two-year period, many wells were drilled and completed with ICD screens; many different cleanup methods were used. Permeability contrasts obtained from LWD logs allowed different ICD pressure regulation configurations, which were used to optimize flow across horizontal open-hole sections, averaging lengths of 2,500 ft.
Table 1 shows data from two example wells, each using different cleanup methods described above. The following discussion explains how some of the data were derived.
Figure 1 shows how the actual ESP intake and differential pressures were derived for Well A (no treatment). Then those values can be extrapolated to derive the flowing bottomhole pressure (FBHP) (2,140 psi), which is then used to calculate the actual Productivity Index (PI) of 47 RB/d/psi.
Figure 2 shows the pressure loss through ICD screens – which is the difference between the sandface pressures inside ICDs sections – and shows the pressure drawdown inside the ICDs.
Theoretical PI was calculated using the calculated flow rate from the pump curve and the static intake pressure extrapolated to the open hole as inputs to the near wellbore inflow modeling program.
The actual PI for Well C was calculated, after the completion, from FBHP and static BHP at the heel, which were derived by extrapolating the static and dynamic pressures to the open-hole horizontal section (Figure 3).
Well C (Treatment B) had an actual PI of 84.28 rb/d/psi and theoretical PI of 80 rb/d/psi, indicating that Treatment B provided effective mudcake removal. Actual and theoretical PIs were derived similarly as explained above.
COMPARING METHODS
Figure 4 shows the difference in actual vs theoretical PI plotted against time. Figure 5 shows the average, actual and theoretical PI plotted for each treatment method over eight wells. These two figures clearly show a strong relationship between the nature of the treatment and production improvement, with PI for Treatment B exceeding the theoretical PIs, while the coiled tubing and nitrogen method actual PI was below the theoretical.
Regarding cleaning time versus effectiveness of treatment, no clear relationship can be seen in Figure 4. However, the ESP data collected for function testing show that the combination of time and flow rate is crucial for well cleanup.
This article is based on SPE 120651, “Best Cleanup Practices for an Offshore Sandstone Reservoir with ICD Completions in Horizontal Wells,” presented at the SPE Middle East Oil and Gas Show and Conference, 15-18 March 2009, Bahrain.