Automation, equipment redesigns for 24-hour pumping among focus areas in well completions
Shift to more simulfracs/trimulfracs and nonstop pumping amps up need for more horsepower, better equipment reliability
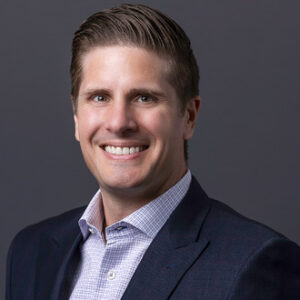
By Stephen Whitfield, Senior Editor
Zach Wilbur is Senior VP – Operations Support at NexTier Completion Solutions.
Heading into 2025, how would you describe the state of the completions space?
I think it’s at a place where we’re optimistic for some stability. We saw a lot of opportunity for growth from 2021 to 2023. In the past, we would have grown at a very fast rate, but just like our customers were doing, we were much more capital disciplined in the way we allocated the money that we had to spend.
So we saw that extreme growth recovering from 2020, and then from early 2023 through 2024 the industry headed in the opposite direction. Rig count was going down, and frac crew count was going down. The question became how do we manage costs inside of that? We feel like the completions sector is at a point now in 2025 where activity level is going to be flat. There may be some opportunities to grow, and there may be some slight changes in activity, but we’re preparing for an activity level that’s likely to be flat.
We’re still going to develop technologies that add value to our portfolio, but we are focused on improving our overall margins and cash flow for the business in a flat market. Of course, that could change quickly. That’s just the way the completions business is.
To what extent is the completion business tied to the drilling business? How much of your strategy is reacting to what’s going on in the drilling world?
Certainly, the completions business is very closely tied to the drilling rig count and the wells drilled. The more wells being drilled, the more activity there is for frac fleets.
There used to be a large surplus of well inventory, especially coming out of 2020, because of the excess DUC (drilled but uncompleted) wells. We’ve consumed a lot of that excess inventory. Even while the drilling rig count was coming down, frac activity kept improving because of the DUC wells. By 2024, that excess DUC inventory was virtually exhausted.
Now, the completions business is tied more closely to rig count, and that gives NexTier a bit of an advantage when you consider our relationship with Patterson-UTI Drilling Company. (NexTier was acquired by Patterson-UTI in 2023.) We talk about what rig activity is looking like, and there’s a lot of value in having that synergy from a macro perspective on what’s happening with rigs across the industry.
What other value does working under the same umbrella as Patterson-UTI Drilling give a completions provider?
It’s focusing on providing “bit to barrel” solutions for our customers. We have opportunities from our customers that come in with an efficiency target on drilling and completion, and because we are integrated throughout the entire well construction and completions process, we have the capacity to work with them and deliver on those targets. The integration opportunities between how the well is drilled and how it’s completed are there and can be optimized across the full cycle of the wellbore. We’re leveraging those opportunities where it makes sense and drives value for our customer and Patterson-UTI.
What developments on the cementing side are we going to see in the near term?
There are improved cement slurries that are optimized for longer length laterals or slim-hole designs. There are also technologies being developed and utilized for customers to prevent gas migration and improve overall zonal isolation for the life of the well. We’re working actively with our suppliers, our partners and our customers to test and deploy those technologies. We have a robust lab in The Woodlands, NexTier’s Chemistry Innovation Center, where we’re testing different cement blends right now.
We also have built a brand-new quintuplex cement pump, which is a first in the industry, to help with the increased pressure and increased pump rate that you’re seeing at the drill site from longer-length laterals and slim-hole designs. And then we’re continuing to invest in our cement bulk plants. Over the past year, we’ve increased our overall bulk storage by around 60%.
We’re seeing the industry push further and further with lateral lengths, to where laterals that were once thought impossible are now commonplace. Do you think the equipment we have on the completions side is sufficient to help drillers push lateral lengths further than what we’re seeing today? If not, what improvements do you see happening to help in this area?
On the completions side, talking about frac specifically, there is certainly some increased pipe friction on the extended laterals, and there are opportunities for those zones closer to the toe to have higher pressures. There is also a request from the customer to pump at a faster rate.
Certainly, we do have the equipment to help us achieve the frac rates we need at those higher pressures, but I wouldn’t say we need a huge redesign of equipment at the well site. What has happened across the industry is that frac fleets are getting much larger in terms of total horsepower deployed to support the demand for those higher pressures and pump rates.
What’s also been impactful is our customers’ completion strategies. Yes, they’re drilling these longer wells, and they also want to complete more lateral feet per day than they ever have, and they’re working with us to do that.
How are they doing that? The industry started with single well operations and moved on to zipper fracking, which has been around for a while but has improved significantly over the last two years. Now we’re pumping completions as simulfrac (treating two wells at once) and trimulfrac (treating three wells at once), which can be even more efficient but also requires more horsepower at the well site.
Beyond that, customers are looking at nonstop 24-hour pumping operations. They want to see how we can have continuous pump operations for 24 hours around the clock and improve our overall lateral footage per day.
This push for 24-hour pumping operations has driven a lot of redesigns of our equipment, because it wasn’t initially designed to do that.
Have your customers brought up any demands for equipment that can help improve ESG in completions?
Yes, what started as purely an ESG focus also has the benefit of saving overall cost on their AFE by using natural gas to displace diesel. It’s a win-win when you can get the lower emissions benefits while also getting the fuel cost savings. That has driven a lot of our equipment toward natural gas-fueled equipment that can also pump these longer laterals.
Are you talking about just using natural gas and dual-fuel gensets?
Yes, it’s both. Our main engine technology is what we call a Tier IV dynamic gas-blending pump. It can blend diesel and natural gas, CNG or field gas, whichever one the customer wants to utilize at the well site. Beyond that, we also have electric-powered pumps and straight 100% natural gas-fueled pumps in our system.
E-frac has become more of a player in the frac space as operators look to move away from diesel. Do you see e-frac gaining a greater market share in the near-term future?
Let’s talk about the overall expenditure for an e-fleet. You have a dynamic where an e-fleet is more capital intensive up front. However, the amount of capital needed to maintain that electric equipment is somewhat lower. Over the lifespan of the equipment, you can potentially have a lower cost per hydraulic horsepower on maintaining the e-fleet than you would on a conventional pump.
But you also have to account for the cost to deliver power to that e-fleet, typically with natural gas-fueled generators, and that can be a very significant capital spend. For a lot of customers today, with diesel costs where they are, e-fleets don’t make a lot of sense. The fuel savings they can get moving from a diesel system to the Tier IV dual fuel blend, which is typically around 70% natural gas and 30% diesel, is noteworthy. It goes back to being able to improve ESG performance and save money in the long run.
So, what’s the profile of a customer who would use e-frac? Who’s purchasing this?
There’s a portion of the operators, primarily the large multinationals, who want the combination of lower fuel cost and diesel emissions reduction with an e-fleet, and are willing to support the additional cost of electric power generation to do it.
I think that e-fleet popularity is dependent on a few things. Some of those being: What are natural gas costs, and what are diesel costs? What are the operators telling their investors that they’re going to deliver in terms of potential ESG benefits?
You brought up pressure pumping earlier. We’re seeing these high-horsepower pumps make a serious dent in this space, with 5,000-hp pumps becoming more and more popular. Do you think we’re reaching our limits as to how much horsepower we can get out of these pumps?
Certainly, there are designs right now that can go higher than 5,000 hp. There are some equipment manufacturers developing 6,000-hp to 7,000-hp pumps right now. The real question is not that pump size. Holistically, whether conventional or electric, you’ve got the drive motor, the power end and the fluid end.
It’s the power end and the fluid end that are the limiters. You can have a 7,000-hp drive motor, but that doesn’t mean you’re going to get 7,000 hydraulic horsepower out of it – the power end and fluid end are going to fail before you can fully apply that horsepower. The design of the power end and the fluid end hasn’t evolved as quickly as the engine, transmission or electrical components. I think the manufacturers will ultimately get to where they need to be on power end and fluid end designs, but there’s still some room to move.
The other side of this question is – other than in the Haynesville and sometimes in the Delaware Basin – treating pressure is not the issue. It’s really the pump rate that I’m more concerned about. I’m not as concerned about how much horsepower per pump we’re going to have in a lot of these basins. Honestly, traditional pump horsepower is going to work just fine to achieve the rate that you want.
Are there any particular challenges you’re seeing in wireline that we need to be looking out for in the near-term future?
It’s a very good question. From a wireline perspective, it’s a similar challenge to everything else in completions. How do we go to these deeper wells? How do we ensure that we’re shooting perforations that are going to accept the fluid that’s being pumped down at that increased depth? We’re talking about perforation efficiency and cluster efficiencies, and just improving the overall reliability of the equipment at the surface to ensure that wireline doesn’t get in the way of the larger frac operations.
We’ve made a lot of investment at NexTier over the last few years in wireline. By the end of 2025, most of our wireline units will be electric. That improves the efficiency, the quality and the safety – all of those things are tying together, and that’s going to be a big differentiator in the wireline market.
We’ve seen a lot of talk within the industry about automation, machine learning and AI-based systems in drilling. Do you think these technologies can provide value on the completions side? Why or why not?
I think there’s value anytime you can reduce overall error rates and improve quality, and we can leverage automation, machine learning and data science to help us do those things. Whether that’s focused on internal costs, savings or operational efficiencies, there’s value.
We have many deployed solutions and ongoing projects that we’re working on from an automation and machine learning perspective. I’ll give an example related to equipment health. Historically, we’ve used what we call RAG (Red, Amber, Green) limits: Green is good, amber is not so good, red’s bad.
We set limits with numbers correlating to each color. As we’ve consolidated all this data that we’ve been bringing in from our equipment over the past few years, the data provides insights into the trends.
We can see in the data, for instance, a trend of temperature on an engine before it gets to amber. We’re starting to build that kind of machine learning in trend tracking, so that it can notify us if something’s happening before an amber or red event happens.
Automation is the same thing. We are working on getting our equipment to run itself based on all of the information that it’s taking in. We have wireline and pump-down automation already deployed to a majority of our fleets that are running those two services, and we are developing that on the frac side, as well. That will continue to evolve and grow within NexTier over the next few years.
So where do you see people fitting into this automated landscape?
Absolutely, 100% you’re going to need people who are very smart and who know how to manage these systems. You’re still going to have to move equipment around from one location to another. People are still going to have to maintain power end and fluid end components to make sure that they’re ready to pump the stages. Certainly people are going to continue to play a big role in what we do.
From an automation perspective, the skill sets that we need may change. Perhaps we will need more people focused on digital, software and electrical, but we are using the people we have today and are training them to get there. We’re putting in those training programs so they can evolve their careers along with us as our company evolves.
Would you say there are any “must haves” in a completions package today – as in, is there a certain size of casing or production tubing or a certain packer that you need to have to complete the wells that are being drilled today?
I don’t think I would phrase it in terms of “must haves.” We’re very flexible with our customers. As they tell us what their completions program looks like, we provide them with what we think is the most effective execution strategy to complete it.
Certainly there are things that make it easier. That may be a toe sleeve that’s pressure activated, for example. Larger casing enables us to pump at higher rates and lower pressures, which is less damaging to the equipment. There are things that I’d like to have, but there’s no “must have.”
I think the biggest thing we’ve always talked about from a drilling perspective is to drill the well in the zone. Completions can provide the best frac job in the world, but if the well is drilled out of zone, it’s not going to produce. You’ve got to make sure you drill the well in the zone throughout the entire production interval – that’s critical.
What do you see as the next step-change for improving safety at the well site?
It’s likely to be automation. How can we reduce the amount of hands-on activities that are happening at the well site and make sure we’re improving the efficiency and quality of the equipment that’s at the well site? If we can teach a piece of equipment to protect itself, it can fail less often. That means we have to maintain it less often, which means we are handling it less often. If you’re reducing the amount of those kinds of activities, you’re improving your overall safety performance.
The flip side of this, however, is that automation may introduce other safety risks that we just haven’t seen yet. As we identify those things, we’ll put in the prevention and mitigation measures for moving forward.
Another big aspect of improving safety that NexTier has focused on is the move toward preventing serious injuries and fatalities (SIFs), and using that as the primary metric for measuring safety performance. We’ve started to focus on stopping the things that can truly alter a person’s life, and as we’ve done that, we’ve also seen a reduction in the smaller incidents.
I think that’s going to be evolutionary as more and more of the industry comes on board with that way of thinking. NexTier was an early adopter of using SIF prevention with some of our multinational customers, and I think the industry is seeing the potential benefits, and they’re likely to get on board, as well.
Do you think TRIR (total recordable incident rate) can co-exist with SIFs as a metric for safety, or should TRIR be phased out?
They’re both valuable and needed. SIF is still relatively new, and some may measure it differently, while TRIR is defined the same way across the industry. As the industry evolves and SIF becomes more standardized, that’s probably the metric that will be more prevalent.
Do you think there’s enough momentum to see that kind of shift toward a standardized definition of SIFs?
I think it will take time, but it will eventually filter its way through the industry and become standard.
Recruitment and retention of young people is a continued challenge for many in the industry. What do you think the industry could be doing that it isn’t already to help reach out to people starting their careers?
One thing that I think we can do better as an industry is highlighting what the industry brings to the world.
Everybody knows you need oil and gas to power your car and power your home, but there’s a host of other things that we do with petroleum products. It’s the clothes you wear and the medical equipment that saves lives. It’s in so many things that people use on a day-to-day basis that they just don’t know about. I think that’s one part of it.
The other part is showing young people that we’re continuing to evolve as an industry and that we offer opportunities to grow their careers.
As an example, we have an employee here at NexTier who started 20 years ago as an equipment operator trainee. Today he’s a vice president in this organization.
That kind of opportunity exists across the industry. We have field engineer trainees who get started in the field and work their way up to become leaders in the organization. You see that across the industry. We also have folks who start off in operations, and they end up in other supporting roles, such as human resources or supply chain or finance.
We need to continually highlight the opportunities that the industry provides to the younger generation that’s coming into the workforce. They have a vast amount of potential that they can achieve in the oil and gas industry if they give it a chance. DC