Supercapacitor-based systems show potential to cut emissions while improving power quality
In field tests, supercapacitors can both charge/release power much faster and smooth out voltage fluctuations when replacing batteries
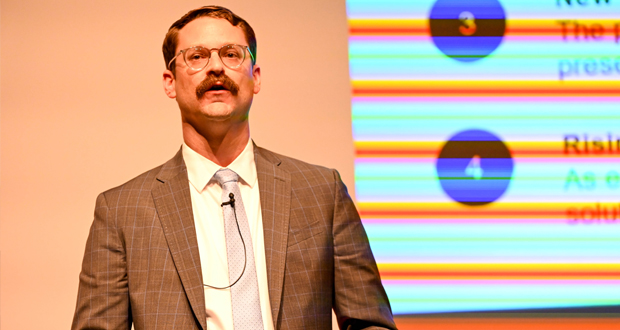
By Jessica Whiteside, Contributor
Got gremlins in your rig’s electrical system? A supercapacitor could help with that. That’s one side benefit Canrig Drilling Technology has identified during field testing of an energy storage system (ESS) that relies on supercapacitor technology instead of traditional lithium-ion batteries.
The primary impetus behind implementation of the supercapacitor ESS was to produce power more efficiently – reducing fuel consumption and related emissions – in settings where highline electrical power is not an option. However, the supercapacitor’s added ability to smooth out voltage fluctuations in the electrical system has Canrig considering what other rig issues it might help address.
“We’ve seen a big increase in the quality of the power on the rig, which really helps improve operations. A lot of your electrical gremlins go away from that,” said Luke Trueheart, Product Line Manager, Energy Transition at Canrig, part of Nabors’ rig technologies segment. “That’s something we’re working on with the prototype testing we’ve done – to see what we can apply this to. Do we use a supercapacitor in some form other than ESS? Can it go on the rig and be standard as part of a VFD (variable frequency drive) package to improve the quality of performance on the rig?”
Speedier power
Batteries are popular for energy storage because they are energy dense and can store large amounts of energy for a long period. What they aren’t known for is charging quickly – that superpower belongs to supercapacitors. Unlike batteries, supercapacitors are power dense. This means not only can they charge up more quickly, often in seconds, but they deliver power faster, too. This makes supercapacitors ideal for applications requiring bursts of power from rapid charge/discharge cycles such as regenerative braking in elevators or hybrid vehicles – or the high but frequently shifting power demands on a drilling rig.
Speaking at the IADC World Drilling Conference in London on 20 June, Mr Trueheart cited a tripping operation as an example, where the power needed could quadruple the base load on the rig for just a few seconds. While efforts with battery-based ESS had proven successful, Canrig wanted to see if it could provide power more immediately with a supercapacitor. With the faster charge/discharge times of the supercapacitor ESS, “we’re over 10 times the speed of a battery,” he said.
“One of the things that we’ve seen as a benefit is improved acceleration times of your drawworks or, really, any electrical motor. Currently, you’re limited by how quickly the gens can ramp up in power to supply the needed amperage to the system. With the capacitor, we can supply it faster than anything else could. It’s there, it’s available, it’s instantaneous.”
Tied into DC rather than AC
The supercapacitor ESS works differently than a typical battery system. While most batteries are tied into the AC bus, the capacitor is on the DC side.
“Being on the DC bus allows us to quickly supply the energy back to the drawworks when it’s hoisting,” Mr Trueheart said. “But then when we come down with the blocks, we’re able to capture all that energy. We have gravitational force when we travel down, and then we slow the blocks to stop them at the rig floor – and that’s power that we can pull back into the capacitor and store to use again in the future.”
This waste energy captured by the supercapacitor ESS can be deployed in place of diesel-generated power. While this would be possible with a battery, the amount of energy capture would be much smaller. Canrig has seen an average of 2 kilowatt hours of energy stored in the supercapacitor for an empty-block downward trip from the crown to the ground, he said. “The higher the hookload we get, the more energy we get back into the capacitor.”
Fuel efficiency while using the supercapacitor ESS reached a rolling average of close to 15 kilowatt hours per gallon. However, there is a jump in instantaneous efficiency through each trip cycle, Mr Trueheart said, because the single engine used can run at a constant load for the whole operation while the capacitor supplies the extra power needed to hoist. “We see that jump in efficiency because we’ve got a lot of power coming into the bus that’s essentially free from our 2 kilowatt hours, and we’re basically able to stay almost constant with the charge, which means we’re tripping with using almost no fuel.”
The company has projected fuel savings of 25% through use of the supercapacitor ESS compared with about 20% from battery systems. A large portion of that savings comes from capturing the regenerative power from the blocks traveling down, Mr Trueheart said. “There’s not much other energy on the rig to capture from a regenerative standpoint. There’s some voltage fluctuation in the system that we can take advantage of, but it’s fairly minimal. The majority is downward block movement.”
Fewer electrical gremlins
Beyond energy savings, implementing the supercapacitor ESS in places like the Permian has led to improvements in rig electrical quality, with the supercapacitor essentially acting as a voltage regulator for the rig, Mr Trueheart said. This benefit can help to address a common rig problem: high voltage fluctuations, which are bad for drives and certain electrical components and create a lot of havoc in the system that can lead to premature failure.
“With the capacitor on, we’re able to greatly reduce the overall noise in the system,” he said, pointing to a dramatic 30-volt reduction in instantaneous real-time voltage fluctuations on the DC bus when comparing operations with the supercapacitor ESS to those without.
Theoretically, the improvement in voltage fluctuation with a supercapacitor should lead to a decrease in electrical system maintenance costs; however, there hasn’t been enough testing time to prove that out yet, he said. DC