Automated geosteering algorithm shows promising ability to match human geological interpretations
H&P undertakes field testing in Haynesville to validate technology that supports more efficient analysis of target formation
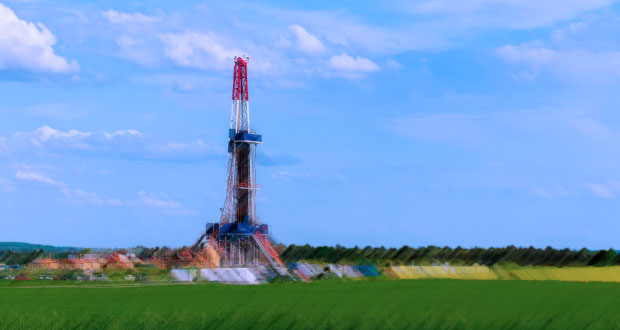
By Jessica Whiteside, Contributor
The developers of an automated geosteering algorithm aim to take the more mundane tasks related to the monitoring of geological data and generation of geological interpretations off the plate of the geosteerer, so they can apply their expertise to more complex challenges.
Geosteerers interpret real-time geological data from downhole logging-while-drilling tools, often a gamma ray module, to help drilling crews make directional changes for a better path to the pay zone. Geosteering analysis is particularly important in two key areas of wellbore placement: achieving the optimal landing point and guiding the lateral through the target formation.
The geosteering process is labor intensive, requiring continuous monitoring and interpretation of data that can limit a remote supervisor to watching only two or three operations at a time. But what if that one expert could simultaneously monitor even more wells, with less stress and greater efficiency, through the application of technology? That thought was one impetus for the automated geosteering algorithm that Helmerich & Payne (H&P) developed and field-tested on two Sabine Oil & Gas wells in the Haynesville Shale.
The geo-correlation algorithm is designed to expand the geosteering capacity and efficiency of remote operations centers by using automation to handle routine monitoring, as well as survey updating that requires no immediate decisions. This would free up geosteerers to focus on the most challenging intervals in each well where meaningful decisions are required, such as steering changes or choosing between multiple interpretations when enough data is ready for review.
“It’s not that we want to replace someone or remove their job. It’s that we want to make sure that person can be more effective, watch more wells and leverage their talents in a better way,” said Marc Willerth, H&P Technology Development Manager. He discussed the algorithm and its field testing at the 2022 IADC/SPE International Drilling Conference in Galveston, Texas, on 10 March.
Minding the misfits
To help the geosteering team identify the best pathway through the formation, the algorithm uses a stratigraphic heat map to visually represent interpretations of geological data, including stratigraphic depth and gamma ray signature measurements.
The heat map’s coloring indicates the probability of encountering rock that matches type log expectations. Areas of low probability (high misfit) appear as yellow, while those with higher probability (low misfit) are preferable and use darker tones.
“The theory here is that if you build a path through these dark zones, this combines both what rock you are likely measuring from a geology perspective with what rock you are likely measuring from a geometry perspective,” Mr Willerth said.
Validating the system
H&P had previously tested the algorithm against historical drilling data, but the Haynesville project provided the first opportunity to apply the algorithm to the real-time workflow of a drilling operation as crews developed the lateral sections of the two subject wells.
For this field trial, the team intentionally chose an area featuring benign geology with no major faults or dips so it would lend itself to straightforward interpretations.
“Basically, if we couldn’t steer this with our algorithm, we were going to struggle just about anywhere,” Mr Willerth said. “But we thought it was a good opportunity to give it a try, and it’s also potentially your highest value place for an early automation solution. If you can take the simplest things and allow expertise to be focused on the more complicated areas, that in and of itself is already a win.”
The field deployment offered a head-to-head comparison of the interpretations of traditional geosteering services and the automated system, which was periodically monitored by a geo-professional. The team’s goal was not only to see if the algorithm could produce results similar to a human, but also to quantify how much effort would be required from a human to ensure that the algorithm’s interpretation was reasonable.
The team checked the interpretations for three primary factors: estimated landing point, modeled geologic structure throughout the lateral, and the estimated footage of the wellbore in the target zone. In both test wells, the automated system estimated the same landing point tie-on and percentage in zone as traditional geosteering.
“We were excited to see that there was broad agreement in the key variables we were testing,” Mr Willerth said.
While the algorithm’s estimated bed dips across the lateral also closely matched those from the human interpretation, there were some minor issues in which the algorithm added irregular artificial structures – a hump in the first well and some jagged cusps in the second – that required intervention through the addition of control points to create a more realistic formation shape for the area.
Defining control points
To address the unusual hump depicted in the first well, for example, the team set control points of known stratigraphic depth and known measured depth to force the algorithm to find a path through that point. Flattening the cusps in the interpretation of the second well required four control points. The ability for a geologist to intervene like this to address anomalies in the automated interpretation is analogous to checking and fixing the work of an assistant, rather than having to do all the work yourself.
“Instead of having to maintain an interpretation constantly, you can just verify what is going on and intervene one or two times to produce this same type of interpretation,” Mr Willerth said.
The team considered the number of control points to be a marker for the amount of manual effort needed to reach an acceptable automated interpretation. They estimated it would take a geo-professional five to 10 minutes to update a typical control point. Compared with the large number of monitoring updates required in traditional geosteering, relating to potentially hundreds of surveys, the low number of interventions required in the test wells represents the removal of “a huge amount of human effort,” Mr Willerth said.
“This suggests that we could potentially dramatically expand the capability of human geologists to monitor more and more wells without compromising service quality,” he said.
Refining the technology
The team plans to expand testing of the algorithm to basins with more complicated geology to ensure that the results can be replicated over a wider range of geological conditions. Since the completion of the initial field trials, the company has modified how the algorithm analyzes the heat map, in order to reduce the amount of manual intervention required for realistic results. After running the Haynesville test well data through the updated algorithm, the need for control point intervention dropped to none for the first well and just two control points for the second.
H&P also expanded the algorithm’s capacity to accept different forms of human intervention, in addition to control points. The new functionality would enable a geologist to tell the algorithm to insert a fault of a certain size at a certain location, for example, to reflect their seismic knowledge of the area. The purpose of the algorithm is to enable the human to do the most important things – and not do the unimportant things, Mr Willerth said.
“Selecting where a fault is, selecting the size of the fault – this is an important thing for a geologist to be analyzing and putting in there. Saying the formation has continued along the same dip for another 500 feet, saying there has not been a major change, is something that you might as well have a computer look at, and let the human plan for the next well.”
H&P is also considering developing other features for the algorithm, such as the ability to actively alert the geosteering supervisor to changes in certain metrics.
“That really expands how much a person can watch, because now you know when to look at it as opposed to just checking every so often,” Mr Willerth said. “It’s nice to only have to have a human intervene five times. It’s even nicer if you can tell them when they likely would need to intervene.” DC
For more information, please see IADC/SPE 208697, “Field Validation of an Automated Geosteering Algorithm in the Haynesville Shale.”