Collaborative engineering unlocks optimal design for MPD system on land drilling rigs
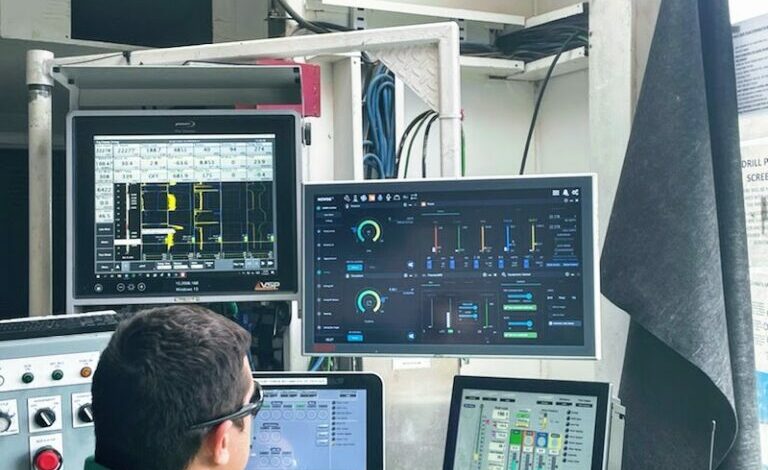
Fit-for-purpose design emphasizes integration with both hardware and the rig’s automation platform, supported by stepwise implementation plan
By S. Hovland, R. Gonzalez, I. Knight, H. Patil, Frontier International; G. Matherne, Precision Drilling
Managed pressure drilling (MPD) is a technique commonly used to control wellbore pressure during well construction. In its most common form, it is facilitated by installing specialty equipment that creates a closed circulation system, paired with an MPD choke system that can selectively apply surface backpressure to the wellbore by throttling the flow through the choke. The surface backpressure will depend on the flow rate through the choke and the choke opening percentage, which is manipulated by an automatic control system that considers readings from field instrumentation, as well as user inputs.
MPD equipment selection and complexity will depend on the risk level of the planned operation, with considerations such as formation pressures, permeability and any specific drilling challenges in the field to be drilled. For example, while a single MPD choke may be sufficient to achieve the drilling objective, a second choke is sometimes installed for redundancy and operational flexibility. Additional flow meters may or may not be installed, depending on the criticality of the operation and the need for measurements, such as return flow rate and density.
Although MPD is a mature technology, there are still challenges in executing MPD projects. In many cases, complex equipment packages and rig interfaces lead to oversized drilling crews and, ultimately, high operating cost. The temporary nature of MPD service contracts often lead to sub-optimal installations, such as equipment taking up too much space, as well as unnecessary redundancy in sensors between the rig system and the MPD system.
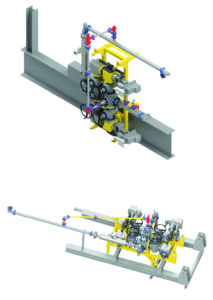
Challenge
In some fields, MPD is used routinely to optimize drilling performance and achieve drilling objectives. One such field is in the Haynesville formation. In 2020, a client in this basin was using MPD on multiple drilling rigs in the area. The client’s entire drilling rig fleet was comprised of Precision Drilling’s Alpha Automation series of drilling rigs. Additionally, most of these rigs were utilizing MPD services from various vendors for this campaign.
The question was posed: Can we use digital automation technology to:
Reduce cost to the client, MPD vendor and contractor?
Reduce crew size?
Integrate MPD and rig hardware?
Bring consistency and repeatability to the operation?
Optimize drilling and move times?
In an initial scoping phase, the client, Precision Drilling and Frontier International collaborated on developing high-level requirements for equipment and functionality based on learnings from previous operations in the field. It was decided to standardize on a dual choke manifold setup, with a Coriolis flow meter to assist in monitoring placement and displacement of drilling fluids.
An overall strategic objective was to increase the utilization of the MPD system by reducing the operating cost associated with using the technology.
Engineering collaboration
To meet the objectives outlined above, the engineering team at Frontier developed rapid prototype drawings of different equipment configurations based on an extensive library of digital assets. Special attention was paid to safe and efficient mounting options, optimal orientation, weights, dimensions and accessibility for field service and handling.
The digital assets were then shared with Precision Drilling’s engineering team, which placed the equipment in three-dimensional models of the drilling rigs to verify fit and feasibility. These in-house engineering capabilities at both Frontier and Precision Drilling enabled rapid concept verification throughout the planning phase, until the integration concept was risk assessed and the design had been validated by both teams. Detailed manufacturing drawings were completed once the main equipment design was verified, and the manufacturing of system components was started.
Precision Drilling has a fleet of slightly different drilling rigs, which required two different layouts to optimize implementation on both rig types. The left side of Figure 1 shows an example general arrangement drawing for equipment layout and mounting in the rig’s substructure for rig type A, while the right side shows the design for rig type B.
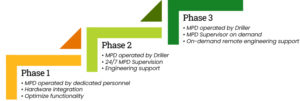
In addition to layouts “A” and “B” for the Haynesville, a third layout “C” was utilized for permanent installations in Canada, where the substructure is enclosed and winterized.
Aside from hardware integration, a key piece of the strategy was to fully integrate the MPD control system with the rigs’ Alpha Automation drilling platform. Designed to enable automatic and repeatable performance, Alpha Automation is a key part of Precision Drilling’s service delivery. By automating the most common sub-operations in drilling, the automation system delivers a standardized and optimized slips-to-slips drilling process. It also allows for installation of third-party apps that receive high-speed, quality data directly from the drilling machines. Development of an MPD app that runs on this platform would serve multiple purposes:
Fully automate key repeatable activities in the MPD process by leveraging the holistic Alpha Automation system;
Enable drillers to monitor and control (as required) the MPD process from the drilling chair;
Remove unnecessary sensor and user interface redundancy and improve the quality of data used for MPD; and
Simplify per-rig integration work by having a standard interface that can be quickly deployed on new rigs.
Implementation plan
A three-step implementation plan was put in place to ensure successful mobilization of the MPD concept (Figure 2).
Initially, the MPD system was to be installed on a single rig and be operated by dedicated MPD personnel from a standalone user interface, while involving the rig personnel in the decision-making process to start maturing the concept and prepare for a handover of responsibilities. This time would also be used to collect feedback and implement field-specific learnings into the MPD control system and the MPD automation app that the drillers would be using eventually.
In the second implementation phase, the MPD app was to be installed on the rig’s Alpha Automation system. The driller would assume control of the process and control and monitor the MPD operation from the driller’s chair. Drillers in the Haynesville are accustomed to drilling with MPD. However, for a driller to assume responsibility of the whole process requires training and verification of competency, as well as confidence that the crew can handle planned and unplanned scenarios. To this effect, MPD supervisors were planned to be on site 24/7 to train the driller in executing the MPD operation. Once the app implementation was successful in phase 2, the same approach would be taken on other rigs, according to a ramp-up plan based on the client’s drilling program and MPD requirements.
The third phase in the implementation plan was to let the normal drilling crew run the MPD system on their own, with specialist support available on demand and for especially challenging operations. This would only be done once it was determined that the MPD system could be operated in fully automated mode and the drilling crews were deemed competent to operate the system without supervision.
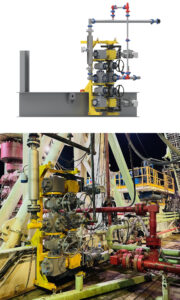
Project execution
The MPD equipment package was manufactured as per the engineering design and mobilized to the first rig in November 2020. Permanent piping was installed as per engineering design, with slight adjustments made in the field as required. Figure 3 shows the engineered concept compared with the actual installation for rig type “A.”
For the first well, the system was operated by dedicated MPD personnel from a standalone human machine interface. For the second well, the MPD app was installed on the rig’s automation system, as shown in Figure 4.
During the training phase, the MPD supervisors coached the drillers on how to operate the MPD app and how to perform common MPD tasks. Focus during the operation was on keeping the system in automatic mode as much as possible, which would keep the operation simple from the driller’s point of view, while allowing the system to execute automatic tasks in response to the rig’s automatic drilling process. The supervisors were on location for the first two wells. During that time, the drillers were exposed to different MPD processes, including drilling and connections, tripping, pill placement and displacement, and casing running.
The MPD app was designed for driller operation, allowing instantaneous overview and control of main process parameters and requiring no specialist knowledge to operate. Having the app running on the driller’s automation platform meant that no new or additional screens or monitors were required, reducing the additional workload put on the drillers compared with separate automation systems.
An important advantage of using the advanced drilling automation system is that drilling and connections are performed automatically and in a repeatable and consistent way, with no change in practice from driller to driller. This allows for standardization and optimization of the drilling process and makes it very easy for a driller to monitor MPD performance without having to intervene manually during normal operations. While drilling ahead, the driller sets the MPD app in automatic mode and monitor the performance on their regular electronic charts, where key MPD parameters are available for local and remote monitoring.
After successful execution of one well using the driller-operated app on the first rig, the same solution was implemented on 12 other rigs in the area, as well as one rig in Canada. Integrated single choke installations are ongoing in the Lower 48, as different basins require fit-for-purpose solutions. Each new controls integration requires only installation of the MPD app, which is done remotely via a network connection in a matter of minutes, significantly reducing the time needed for installation and commissioning on new rigs.
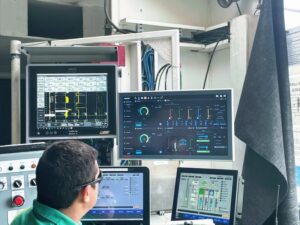
After the first two wells, operations transitioned into phase 3 implementation. The 24/7 MPD supervisors were demobilized, leaving one supervisor to support multiple rigs on demand and for challenging operations. The operation was also supported remotely by an engineering team that performed MPD calculations, which were presented to the rig crew in a way that made it easy for them to execute per plan.
Conclusions
All original goals that were set out at the beginning of the project were achieved. It demonstrated successful leveraging of Precision Drilling’s digital toolbox and resulted in a safe, effective and repeatable system for managing wellbore pressure on Precision Drilling’s Super Series rigs.
This project demonstrated the advantages of collaboration on MPD requirements, high-level design and detailed engineering. By having shared objectives and a joint vision, the involved parties developed an optimized and robust design that significantly reduced cost and complexity of MPD services. Leveraging digital tools in the engineering process ensured quality and safety throughout the project. Collaboration on control system requirements, testing and verification ensured that the solution was fit for purpose, enabling drillers to safely execute MPD operations without the need for dedicated personnel. DC
This article is based on a presentation at the 2021 IADC/SPE MPD and UBO Conference, 14-16 September.