Interactive videos, mobile app and better red zone management among KCA Deutag initiatives to strengthen drops prevention
By Stephen Whitfield, Associate Editor
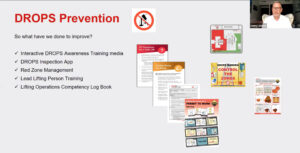
Dropped objects, or drops, still present one of the biggest hazards in upstream oil and gas. According to Kenny Adams, Head of Land Drilling QHSSET at KCA Deutag, more than 60% of all high-potential incidents (HIPOs) in the industry are related to drops, and they continue to account for many fatal and potentially fatal incidents.
Speaking at the virtually held 2021 IADC Drilling HSE&T Asia Pacific Conference in May, Mr Adams discussed some of the systems and training KCA Deutag has introduced to bolster its dropped object prevention scheme (DROPS), as well as how the drilling contractor has adopted these systems into its organization. These initiatives include interactive DROPS awareness training media, a DROPS Inspection application, lead lifting person training, and a lifting operations competency logbook.
“Drops affect us all,” Mr Adams said. “It’s important that we focus on managing the risk of dropped objects within our organizations, with a focus on making it part of our HSE systems and processes.”
Discussion starting points
Developed by KCA Deutag’s HSSE team and Reuzer, a provider of digital training technology, the training media consists of interactive videos designed to encourage discussion between rig crews and HSE advisers. They cover best practices in drops prevention and management, with a focus on identifying the potential for a person onsite coming in contact with either a static dropped object – an object at rest that falls from its original position – or a dynamic dropped object – an object that would not have fallen without another object hitting it.
The interactive element of the training videos comes from what Mr Adams termed “pause points,” or breaks within the video where personnel can discuss the instruction provided in greater detail. Mr Adams said that, in adopting the training videos for use among its rig crews around the world, KCA Deutag has focused on making sure the information disseminated within the videos is easily understood globally.
For instance, the company offers DROPS videos in English, Arabic and Russian, the three primary languages spoken within its operations. The videos also rely heavily on imagery and animation to convey procedures. Further, KCA Deutag has placed posters on its rig sites featuring imagery from the videos to help reinforce the messaging.
Mr Adams described the training videos as the starting point of a discussion with its personnel on drops prevention. KCA Deutag encourages honest feedback from workers on the videos, and it occasionally films its personnel as they watch the training videos to gauge reactions.
“We want to know what people have learned from the training videos and what they want us to do differently. We want the engagement that gives us the confidence that the knowledge and understanding is there,” he said.
KCA Deutag’s DROPS Inspection application, which can be downloaded to a tablet or mobile device, provides a monthly inspection checklist that is broken down into different zones within a rig site. Every rig or facility has an inventory of potential dropped objects from both structurally attached items and items attached to equipment. This inventory contains details of every potential dropped object on or within any elevated area of the worksite. Each item listed on the inventory can have a photograph taken and recorded, and these photographs can be used as reference material for DROPS inspection check sheets and periodical inspections.
Mr Adams said the app provides a user-friendly inspection process, ensuring all necessary details are available and allowing for completed inspections to be reviewed and verified remotely. “The app allows us to move around the rig and give us a picture of what a potential drop could be. It reduces the need for paperwork. Everything’s in the system, so we always have access. I can go and verify that the drops inspections have been performed to the standards required.”
Improving the safety of lifting operations
KCA Deutag’s DROPS lead person lifting training aims to address another major cause of serious or high-potential incidents in upstream oil and gas by creating a framework that defines how all lifting equipment and lifting activities are managed within the organization. The worksite DROPS lead refers to the individuals responsible for the implementation and compliance of DROPS standards for a given rig or facility. This person ensures that DROPS inspections are done regularly, that they are verified, and the rest of the rig crew is trained in the DROPS campaign.
The five-day course covers 20 key objectives, with three days spent learning theory and two days of hands-on training in the field.
A complementary “Train the Trainer” course was also developed specifically for the worksite DROPS leads who are delivering the training. The course is designed to teach professionals how to tailor their course materials for different audiences and how to customize the courses to focus on specific assets, locations or operations.
The Lifting Operations Competency Logbook is the mechanism that measures whether the framework for lifting equipment and activities established in the lifting training is both understood and properly executed by the rig crew. An assessor – who could be the worksite DROPS lead or another person designated to measure competency – uses the logbook to grade the competency of its personnel in lifting operations. The methods of assessment include an observation of personnel during a task; oral and written questioning; an inspection of a given product; and records showing the personnel was involved in a given task.
Mr Adams said the logbook also incorporates knowledge and skills assessments, including assessments for forklift and mobile crane operators. “Some of our operations employ third parties for crane operators and forklifts, but just because someone comes to us with approval and a license, it doesn’t mean that they’re competent. We need to do our duty of care to make sure that people are competent. Assessments like this give us the confidence that the operators know how to manage the equipment without bypassing the safety devices.”
Red zone management
Another area of focus for KCA Deutag is standardizing the definition and management of red zones for all of its rigs, regardless of location. This effort recognizes that an inconsistent definition of what constitute a red zone can hinder effective management.
“With some of our countries, the red zone was the size of a football pitch, and then in different countries you have a more limited space,” Mr Adams said. “In that situation, we had to figure out what was realistic and practical. What could potentially fall off the derrick? What could potentially fall off the catwalk area? We asked the teams about their red zones. What size did they think the red zone needed to be, realistically, to reduce the risk as low as reasonably possible?”
KCA Deutag prioritized placing fixed barriers within each red zone to reduce the possibility of dropped objects coming into contact with personnel, as well as mechanisms that reduce the need for personnel to be in the red zone at all. One example is the installation of air-conditioned cabins near the catwalk area that allow personnel to safely observe operations.
“It is important to think about human factors when you’re putting in the schematics and working with the teams,” Mr Adams said. “When you put an air-conditioned cabin near the red zone, you’re giving people an option. What would you rather do – sit on a barrier inside the red zone or go to a more comfortable area? As a human, you’re probably going to go to the comfortable area.” DC