Are electrically powered fleets the future of fracking?
E-frac systems tout emissions reductions and lower costs over time, but higher upfront capital requirements and lead times remain barriers
By Stephen Whitfield, Associate Editor
As the shale completions industry navigates the current economic and ESG landscape, it continues to be challenged by two significant and growing requirements: to find new cost efficiencies and to reduce its carbon footprint. While there is no magic bullet for either of these challenges, electrically powered hydraulic fracturing (e-frac) fleets are shaping up to be one solution in the toolbox.
Currently, e-fracs make up only around 10% of the overall US frac market, according to Matthew Moncla, Chief Operating Officer at US Well Services. He estimates there are just 12-13 such fleets currently running in the US. However, growth in the market share of e-fracs is highly anticipated in the coming years, with some forecasting it could reach 30% within five years.
There is reason to believe such significant growth is possible. E-frac systems utilize electrically powered pressure pumps running on modular gas turbine generators, as opposed to the diesel-driven pumps of a conventional system. The turbines make electricity using CNG, LNG or site-produced field gas that may otherwise be flared. This means both fuel savings and carbon reductions are possible.
- E-fracs currently make up only around 10% of the US frac market, but some believe its market share could triple in 5 years.
- By replacing diesel-fueled combustion engines with electric motors, e-frac systems have generally shown noticeable reductions in greenhouse gas emissions.
- Fuel savings are possible with e-frac fleets, as are savings in repair and maintenance, but e-fracs require a considerably higher upfront capital cost, which can be a deal-breaker in the current market.
According to Evolution Well Services, its seven e-frac fleets combined have saved operators between $1 million to $1.5 million per month, compared with using conventional fleets. This has been achieved simply by leveraging locally produced natural gas as a feed source. If comparing fuel costs against diesel systems that meet the US Environmental Protection Agency’s (EPA) Tier IV standard on new engines for off-road equipment, then US Well Services believes savings up to 85% is possible through the use of on-site field gas, depending upon the price of diesel.
When it comes to carbon emissions, e-fracs – not surprisingly – win over diesel systems. NOV, which entered the e-frac market late last year with its Ideal technology, says CO2 emissions can be reduced by up to 74% compared with Tier IV diesel fleets and flaring gas. In this scenario, the flared gas would be used to power the e-frac system.
In a 2020 study conducted with an independent, third-party company, Evolution found that its e-frac fleet has an 18.1% lower greenhouse gas emissions profile than a Tier IV fleet.
“In 2020, the shale industry faced one of the most challenging market cycles in history, coupled with a continued push to improve its environmental standing, said Nick Ruppelt, Director of Sales and Marketing at Evolution. “The clean-burning nature of natural gas is a primary driver for the overall success of the shale industry, and this transition away from diesel fuel also helps drive a significantly cleaner and cost-efficient operation.”
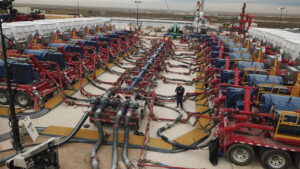
But there are other advantages, too, when it comes to reliability and logistics. For instance, Evolution says the turbine that powers its e-frac system can run for as many as 30,000 hours between startup and the first turbine hot section overhaul in a hydraulic fracturing application. US Well Services, which offers both electric and conventional diesel frac fleets, said it’s seeing a much longer useful life for components of its Clean Fleet e-frac system compared with its conventional pressure-pumping equipment. Such components include the electric motor, transformer and variable frequency drive, which replace the engine and transmission. Engines and transmissions have many more moving parts and require much more frequent maintenance intervals, the company said.
Some e-frac systems also allow shale operators to use fewer pumping units on site compared with a conventional diesel-powered system. While a conventional diesel fleet typically requires 20 or more trailers, e-frac systems can require as few as eight pump trailers, according to Evolution.
There are pros and there are cons
Like other e-frac systems on the market, Clean Fleet touts emissions reduction as a key advantage. According to third-party testing conducted on US Well Services’ diesel and electric fleets operating in Texas in 2019 and 2020, a dry Clean Fleet system produced a 44% reduction in greenhouse gas emissions versus a Tier IV diesel. A water-injected Clean Fleet system can cut pump-related CO2e (CO2 equivalent) by 42% and NO2 by 13%.
The system also saw a 94% reduction in particulate matter versus a Tier II diesel when field gas would have been flared otherwise. Mr Moncla attributes these reductions almost entirely to removing diesel engines and replacing them with a natural gas turbine generator.
The technology also provides a 95% reduction in low-frequency noise, which makes it easier to use in densely populated areas. In fact, the system is so quiet, Mr Moncla said, that red and green lights have been installed on each pump so that workers know if a pump is in operation.
E-fracs do require a higher upfront capital cost than conventional fleets, however, which can be a deterrent for some operators. US Well Services estimates that the upfront capital cost of its e-frac system is around $50 million, compared with $40 million for a Tier IV diesel fleet. However, that difference can be recouped over time. For example, eliminating combustion engines and transmissions also removes key sources of failures and expenses.
Over five years of ownership, US Well Services estimates $40.9 million in repair and maintenance expenses and $17.3 million in maintenance CAPEX for its e-frac system. That compares with $64.4 million and $25.8 million, respectively, for conventional diesel, adding up to $15 million saved in five years.
Another consideration is the longer lead time for e-fracs, which can become a sticking point for some companies in the current economic environment. Once a contract is signed, the customer typically needs to wait five to six months, according to US Well Services; diesel fleets are typically available for immediate use.
“There are a lot of electrical components that you need to build once you get a contract, and those things have lead times,” Mr Moncla said. “We’re talking about the turbines, electric motors, switch gears, transformers, cables, and then you have to install everything. It’s a process that you have to do for every pump. Getting an electric fleet requires making a commitment.”
Because of this extra time needed to get an e-frac fleet up and running, US Well Services requires longer-term deals, typically two to three years, for the Clean Fleet. Contracts for the company’s conventional fleets average just one year.
While the longer-term e-frac contracts have helped the company to stay active during the downturn, Mr Moncla said procuring new deals has been difficult in the current environment, which favors short-term deals for conventional fleets. However, he expects demand to pick up once the industry recovers.
“Part of the reason why we only have five electric fleets is because of the turbulence in the industry. Right now, customers do not want to be tied up in three-year deals in the midst of this downturn. But things are changing quickly, and they are also realizing ESG is here to stay,” he said.
On 12 January, the company announced the finalization of a three-year extension of a contract with Range Resources for use of Clean Fleet in the Appalachian Basin. The following day, the company announced it had signed two contracts with EQT Corp, one of which was a three-year extension of an existing e-frac fleet contract and another for the deployment of a second fleet. US Well Services also announced a two-year contract with Shell in January 2020.
Although these recent contract announcements are positive indicators, Mr Moncla said it is unlikely that e-frac will see measurable expansion across the wider industry until businesses fully recover from the current downturn.
“Capital is really fleeing out of the industry, and that definitely hurts when you want to try to build a $50 million fleet,” he explained. “We need to be able to go out and raise capital.”
Reduced footprint
Evolution Well Services currently owns the largest electric frac fleet in operation, located in the Permian Basin, Eagle Ford Shale, Marcellus Shale and other basins. The company designs, engineers, fabricates and operates the electric fleets and power generation in-house with the help of affiliate company Dynamis Power Solutions, which specializes in building mobile power plants and turbines.
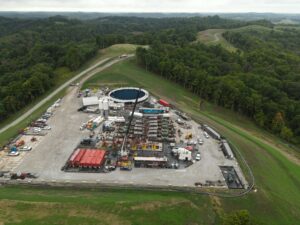
Evolution markets its e-frac fleet as having a much smaller physical footprint than conventional diesel fleets. Each trailer doesn’t require its own engine or transmission. Instead, the pumps in the system are powered by a single 35-MW aeroderivative gas turbine. Developed by Dynamis, the turbine is a lightweight variation of a standard industrial gas turbine.
The utilization of power-dense electric motors instead of reciprocating engines and large transmissions means that the company can fit more power onto each pump trailer. Instead of the 2,250- or 2,500-hp trailer that would normally be on a diesel system, Evolution’s system utilizes approximately 7,000-hp spread out over two pumps on a single trailer. This drastically reduces the number of trailers required for a 56,000-hp fleet to just eight.
“When we designed the electric fracturing fleet, lean methodologies were integrated into every decision we made,” Mr Ruppelt said. “One of our primary goals was to eliminate the maintenance-intensive and footprint-heavy reciprocating engines and upgrade to the reliability of aeroderivative turbines. Also, the increased power density coupled with other design innovations helps lower pad construction costs, reduce trucking needs, increase safety and lead to a more efficient and sustainable operation.”
As with other e-frac fleets, Evolution’s system is geared toward remote operations. The physical layout of its equipment has been engineered to minimize the personnel required during rig-up and rig-down, with crew members controlling pumps remotely from a data trailer. Onsite personnel requirements can be reduced by more than 50% versus a conventional diesel system, the company says.
Like US Well Services, Evolution cited the longer-term nature of e-frac contracts as an advantage during the current downturn. In 2018, the company signed a three-year contract with CNX Resources for operations in the Marcellus.
Evolution’s e-frac fleet stimulated CNX’s RHL 99 shale pad last year, using approximately 140,000 Mcf of natural gas in lieu of diesel. That equates to a fuel savings of approximately $2.4 million, according to CNX. In January 2020, Evolution also signed a two-year deal with EQT in the Marcellus. It is operating three other e-frac fleets in the Permian and two in the Eagle Ford.
Ease of use
NOV is still in the early stages of commercializing its Ideal e-frac system, which the company says is the industry’s first fully remote-operated 5,000-hp e-frac fleet available for commercial use. All functionalities can be managed from a fully electric control van, and none of the onsite equipment requires an onboard operator, according to Travis Bolt, Product Development Manager at NOV. The remote operational capability moves personnel away from hazardous equipment and environments.
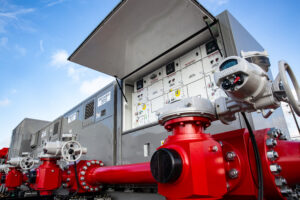
“Our goal was to not have our customers put operators out on the equipment while it’s operating. We wanted to put all the parts and pieces in place to remove the operators from the equipment and give them the feedback that they can operate it from a remotely located control system,” Mr Bolt said.
The technology also offers a smaller footprint over conventional fleets. It features a 42% reduction in the mean square footage dedicated to fracturing on a well site compared with a diesel-based system.
The footprint reduction was due largely to replacing reciprocating engines and drive trains with electric motors, according to Mr Bolt. This allows the system to increase the horsepower on each frac pump trailer.
The trailers on the Ideal system each carry a 5,000-hp continuous-duty pump and power train, which means that only 10 pump trailers are needed to deliver 50,000 hp. Additionally, the system utilizes a fully electric process plant with redundant mechanical and electrical systems, including a 150-plus bpm dual-frac blender, supporting conventional, slip stream and simul-frac operations with a modular auger system. The Ideal system can also support an electric hydration trailer and dry additive unit.
NOV also focused on reducing risk and complexity in all areas, from electrical hookup to rigging iron, as well as making the system easy to use.
In addition, the system is generator agnostic – it can accept turbine or gas generator power, meaning that pressure pumpers can use centralized field power, mobile power generators, a highline power supply, or any other system to power the equipment.
Last November, NOV announced a deal with NexTier Oilfield Solutions to partner on a field test. NexTier will test the operational capability of the Ideal system in the field and under normal operating conditions, and it will have the option to move from the test phase to future purchase of the first Ideal fleet. DC