Crew health, availability prioritized as companies strive to ensure proper incident response readiness
Contractors and operators are also looking to enhanced communication, logistics to mitigate risk of any unexpected events
By Stephen Whitfield, Associate Editor
In the oil and gas industry, companies recognize the essential role that they play – not just in terms of supplying the world with the energy it needs but also in protecting its workers and the environment throughout the drilling process. So earlier this year, facing the looming threat of COVID-19, many companies took early steps to prepare their staff for the possibility of interruptions and changes in workflow. For some, this took place weeks before the World Health Organization officially declared it a pandemic.
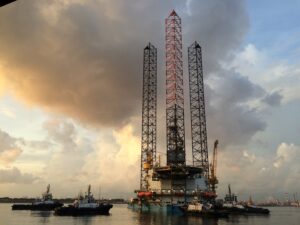
That preparation has proven essential, ensuring not only operational continuity but also that drillers and operators stay ready in case of an unexpected development, such as a safety or well control incident that could potentially cause serious damage.
“The industry has been extremely proactive in terms of setting up this kind of protocol. We face a consequence profile that’s greater than any other industry,” said Joe Leimkuhler, COO of Beacon Offshore Energy, an E&P company focused on the deepwater Gulf of Mexico. Mr Leimkuhler also serves on the board of directors for HWCG, a well containment consortium.
So far, Mr Leimkuhler said, he doesn’t believe COVID-19 has had a negative impact on how companies prepare for potential incidents. Virtual meeting software, such as Zoom and Skype, already allow for office-based and field-based staff to simulate incident response and activation of well containment plans.
“A lot of companies already have these capabilities set up in virtual networks. You have command centers with a high degree of virtual capability, with voice-activated virtual meetings where you can tie in your emergency response network, your incident commanders and your providers. You can reach out to the US Coast Guard and other regulatory staff. To a large degree, if you have ongoing offshore projects and significant operations offshore, away from your home or regional office base location, you’ve probably been operating a significant portion of your operation on a remote access basis for some time prior to COVID-19,” he said.
However, a virtual connection is not a catch-all solution, and in an environment fueled by COVID uncertainty, drillers and operators have to adapt to any situation.
Crew availability
A key aspect to managing this uncertainty, Mr Leimkuhler said, is ensuring the availability of staff. Beacon receives weekly updates from key emergency response providers, ensuring that 95% or more of its staff, as well as key suppliers, are available to respond to an incident.
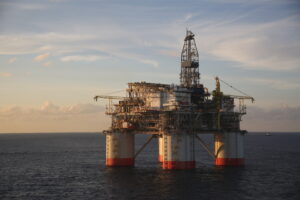
The company believes it has enough redundancies built into its incident response protocol – such as multiple providers of offshore oil skimming services – to cover for staff who may not be available to mobilize at any given time.
Another key to maintaining this level of availability is simply keeping crews healthy. Beacon has been performing medical screenings of personnel headed offshore at the heliport since 2 February. Crew members who have traveled to international hot spots are prevented from going offshore.
There’s also been a greater focus on contractor/vendor readiness as essential to maintaining continuity, Mr Leimkuhler added. Beacon now receives weekly updates from key providers assessing their state of readiness, with information about overall crew health and potential logistical challenges. The company has suspended offshore crew basket transfers, moving all personnel to and from the rig via helicopter. Daily medical checks are conducted for all offshore personnel.
“When you are in a crisis and you need to act fast … you need to empower people.”
– Erik Roesen Larsen, Maersk Drilling
“We’re doing screening at the individual level and testing people prior to going offshore. Locations are reporting into BSEE (US Bureau of Safety and Environmental Enforcement) every day what their offshore statuses are, and we’re making sure that, as an industry, we have a level of consistency on how we evaluate the exposure and risk level of each location.”
Beacon is currently operating one rig, the Transocean Deepwater Asgard drillship, in the US Gulf of Mexico. Mr Leimkuhler said the environment of an offshore rig can be challenging – it puts people working and living in close quarters over an extended period of time, which can increase exposure risk. On the other hand, it also offers a higher degree of control.
The nature of offshore drilling operations, where most crew members spend the bulk of their working hours outside, is conducive to social distancing, said Jeff Sproul, QHSE Supervisor – US Gulf of Mexico Offshore at Nabors. However, the size of a rig’s interior quarters necessitated additional measures for crew members’ rest periods. Nabors provides drilling rigs and associated services globally and is currently operating several platform rigs in the Gulf of Mexico.
“With the layout of the platforms and the limits implemented by our operators on frequency of travel, contact tracing is possible,” Mr Sproul said. “If someone tests positive, who did they share a room or a bathroom with? Were they working closely with someone? Did they spend time in a meeting room with other employees or third-party workers? Did they share a ride to the dock or heliport with someone? We even had contract tracing performed on a crew boat where a worker tested positive. Fortunately, no one else onsite was infected, but operations were suspended and everyone was sent back on land to quarantine while we awaited the test result.”
Communication
Maintaining a rig’s operational readiness in case of an unexpected development requires effective communication between all stakeholders.
At an IADC/Drilling Contractor virtual panel discussion on 23 June looking at HSE performance amid COVID-19, one panelist said that his company’s main priorities early in the pandemic included ensuring consistency on rigs.
Because Maersk Drilling has a significant presence in Europe, with rigs located across the UK, Danish and Norwegian sectors of the North Sea, the company had to address a myriad policies and guidelines regarding COVID-19 that came from each country, said Erik Roesen Larsen, Vice President and Head of HSSE. Combined with complications from policies of the home countries of its European suppliers, the need to develop consistent protocols for interaction on the rig was further amplified.
“In order to manage our performance throughout this situation, we have to communicate and coordinate extremely closely with our customers and with all other third parties,” Mr Larsen said. “We know on a drilling rig that we have many different companies represented, and they have different protocols. But it’s important to establish that, when you’re on one of our rigs, you operate under our rules. Checking into a hotel room doesn’t mean you’re buying the hotel. We asked people to adhere to a limited number of guidelines when they went to work on our rigs, and that helped to create a certain stability in our operation.”
Additionally, Maersk established a task force devoted entirely to keeping its rigs running during the pandemic. This task force would not have been effective in developing COVID-19 protocols without the willingness of senior management to delegate authority and decision making, Mr Larsen said.
“In a situation like this, siloed thinking simply does not work. You have to break down siloes from the very beginning,” he added. “When you are in a crisis and you need to act fast, there’s not any room for micromanagement. You need to empower people.”
Logistics
Operational readiness is essentially the ability to deploy and operate systems, and logistics are a key part of that. Many companies are continuing to feel a strain on those logistics, as COVID-19 travel restrictions and other guidelines make it more difficult to move things around, especially across international borders, in case they’re needed on a rig.
While Beacon does not have to navigate the challenges of moving crew and supplies between countries, the company does have offices in Louisiana and Texas. Regulations on travel between the two states back in March and April forced the company to take additional action to ensure smooth logistics. While Beacon – as an essential business – was exempt from the 14-day quarantine ordered by Texas Governor Greg Abbott for those traveling into Texas from Louisiana, the company did need to draft documentation for traveling personnel.
Logistical planning is crucial to incident response even in normal times, but in the post-COVID world, companies need to be extra diligent in anticipating any potential interruption to the movement of crew and equipment, Mr Leimkuhler said. Trucking services is one example of something that logistics managers now keep their eyes on constantly.
“Offshore incident response involves moving around a lot of equipment, and in most cases that equipment has to be moved as a permitted load. Is our documentation adequate enough to get a permitted load so that, for instance, we can move our BOP capping stack down to the port without any problems?”
At Maersk, logistical support was also an early focal point. With numerous countries around the world going into varying forms of lockdown during the early stages of the pandemic, Mr Larsen said, the company realized it needed to think outside the box to ensure that rig crews and equipment could be moved and get to where they need to go.
For instance, when Poland announced its shutdown, banning travel in and out of the country, Maersk organized a shuttle service with a local company to take crew members from Poland to Germany, allowing for greater freedom of movement to other operations. Crew coordinators in Angola and Ghana also procured private planes to continue crew changeovers after travel restrictions were heightened in those countries.
Mr Larsen acknowledged that the actions taken since the virus outbreak have not been easy on Maersk’s crews, but the work that’s been done to increase readiness to execute has paid off and, moreover, would prove valuable in case incident response is needed on short notice.
“In this environment, you have to think ahead and you have to prepare,” Mr Larsen said. “As soon as we saw the issue at hand, we pre-positioned crews in countries where we thought it would be increasingly difficult to move people in and out. This allowed us to establish critical positions in faraway parts of the world. If we had to move a rig in Australia, we had a crew pre-positioned there to help if we needed help. Of course, that puts a strain on our crews, but this was only possible for us to do because our crews were willing to play along with us.” DC