Saipem’s drilling data performance tools aims to draw value from raw data
By Joshua Baethge, Contributor
Saipem has developed a new drilling data performance tool that paves the way for better decision making on drilling rigs. The project was driven by the company’s realization that how well it leverages multisource data can create both short-term and long-term competitive advantages. Especially amid current market conditions, drilling contractors must identify ways to drill faster, better and safer in order to compete for the fewer contracts that are being awarded.
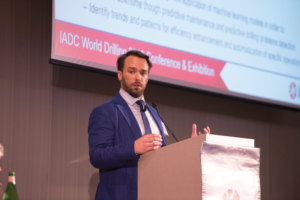
“Data is an asset,” Luca Motti, Saipem’s Digital Transformation and Innovation Leader, said at the 2019 IADC World Drilling Conference on 19 June in Milan. “As we want to maximize the value of our investments, we have to maximize the value of our data.”
While the oil and gas industry has widely adopted sensors and real-time monitoring, the raw data collected is of limited value on its own. Only when the data is processed and organized will it become information, and value is then only gained when insights are drawn from the information. This is where Saipem’s tools comes into play.
Saipem’s software takes an integrated data collection approach by combining high-frequency data from sensors with daily reporting data on phases and equipment. The result is a more accurate evaluation of drilling performance, with objective time breakdowns and impartial KPIs. “It means that we are collecting data from a quantitative point of view and from a qualitative point of view,” Flavio Ferrari, who manages Saipem’s offshore drilling operations performance, said.
Among the short-term gains expected from this technology is the ability to use sensor-based activities detection to conduct real-time data analysis. This information will allow rigs to measure their performance more effectively against similar equipment and conditions, providing benchmarks among multiple rigs and wells. The statistical analysis of key performance indicators like connections, tripping and casing will also give crews direction on how they can improve productivity.
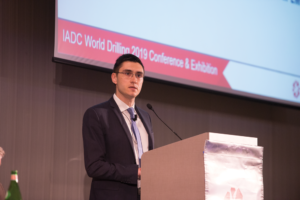
In the longer term, measuring true productivity will identify opportunities for improvement, particularly around invisible lost time. Saipem’s system consolidates multiple sources of data from all rigs every day. Over time, this will allow the company to calculate realistic technical limits. Greater analytical capabilities will also facilitate investigations into the root causes of nonproductive time. Further, algorithms will reduce downtime by helping teams better anticipate maintenance issues and drilling problems. They will also better identify trends and patterns for efficiency enhancements.
“Solutions such as this allow us to increase the value of the data, transforming raw data from sensors into information,” Mr Motti said. “It allows us to draw decisions and conclusions.”
Saipem has so far implemented the technology on two onshore rigs operating in Kuwait and has finished one offshore pilot deployment. Plans call for the tool to be introduced across the company’s fleet, likely by year-end, as long as constraints related to network infrastructure and internet connectivity can be addressed.