Walking MPD-Ready rigs developed with integrated hardware, software to overcome operational inefficiencies
All managed pressure drilling equipment skids with rig, eliminating nonproductive time when moving between wells for multiwell pad drilling
By Juan Pinzon, Nabors Drilling Solutions
While many industries are undergoing rapid digital transformations, the oil and gas industry has been slower to adopt technological innovations on the software front. Over the years, the adoption of managed pressure drilling (MPD) has been hindered by the perception and evolution of MPD gradually changing from a single event management solution to a general efficiency approach. Conclusions about justifications for adopting this technology have previously been made based on one-well MPD operations.
An MPD-Ready rig is a transformational technology that has been used to drill safer and more economical wells, while achieving operational and business value and accessing challenging drilling environments to meet well delivery and production targets.

When complex wells are not delivered on time (e.g. due to downhole conditions), they can impact the return on investment dramatically. Multiwell pad drilling projects are exposed to diverse challenges in both surface and downhole conditions.
At surface, location dimension is subject to lease space; when small, the need to reduce the footprint of rig equipment is critical. The integration of additional equipment into the rig, such as MPD, can impact the efficiency of skid operations between wells.
Downhole, conditions are subject to field depletion, where narrow mud weight windows are more common. This can result in nonproductive time (NPT) if conventional drilling methods are utilized. Excessive mud weight and lost-circulation material can be detrimental to the formation productivity index due to high skin damage. Unsuccessful casing and cementing operations can lead to mechanical integrity issues, which can impact well life. In some cases, it can force production to be stopped for well intervention.
When MPD technology is applied, however, efficiencies in well delivery have been demonstrated.
MPD services have been offered for more than two decades. While some believe it has the potential to be a widely used technology, thus far it has been met with relatively limited acceptance by operators. Accepting it requires taking a general approach where critical milestones are considered during the planning stage in order to maximize successful application during the execution stage, as well as a learning curve to capture the benefits with the right scope identified.
The use of a fit-for-purpose MPD-Ready rig has increased the utilization of MPD applications beyond traditional narrow windows, as well as in critical tasks, with clear benefits. This is accelerating the perception of MPD as a mature and risk-controlled technology with a consistent approach during the well construction process.
The demand for MPD technology requires rigs that are equipped with reliable systems, as well as strong competency of people to operate those rigs in a safe and efficient environment.

For years, land drillers in unconventional plays have seen the benefits of MPD in overcoming typical drilling challenges. These can include full losses; excessive torque and drag; stuck pipe incidents, followed by expensive sidetracks; and not being able to run casing to bottom.
Although MPD can help overcome these challenges, there is potential for operational inefficiencies that result in NPT when MPD components are not integrated as part of the drilling rig. Conventional MPD service (call-out) delivery requires high costs of rig survey and engineering, rig up/down labor and time, and redundant HSE management systems.
MPD-Ready rigs are designed to overcome these challenges. They feature integrated hardware and software components, as well as the required flow paths, to ascertain the downhole pressure limits and manage annular hydraulic pressure during drilling operations. All equipment skids are built into the rig and eliminate NPT when moving between wells for multiwell pad drilling.
MPD-Ready Rig Integration
Elements impacting MPD integration into rigs include the technology to be used for execution, purpose of the application requested by the operator and regulatory application approvals.
Rig Factor – The What, the Technology
Engineering equipment into the rig and maintaining it as rig inventory eliminates expensive rig up/down times and personnel costs. The equipment cost is reduced by leveraging existing rig drives, manifolds, tanks, pumps and gas buster.
There is also a people factor associated with training and developing the current and new generation of rig personnel beyond basic rig equipment functionalities and basic well control skills. Personnel involved with MPD operations require detailed attention to ensure that operational risk management, well control and associated managed pressure activities are aligned to well construction delivery goals. Training is a joint effort between the drilling contractor and the operator, where engineering and operational matters are critical. The outcome drives performance when these milestones are aligned.
Figure 2 describes how the MPD-Ready rig provides the platform for closed-loop automation. Mapping and routing is driven by the scope of work (drilling program, basis of design, influx management matrix). The instructions are driven by the controls (commands to adjust operational requirements). The execution is driven by the hardware (MPD chokes), and the alert and re-route is driven by warning signs to detect deviated conditions from the expected plan.
Using non MPD-Ready rigs or traditional MPD call-out service can impact automation efficiency due to additional processes required to connect human, equipment and warning indicators for risk-controlled operations.
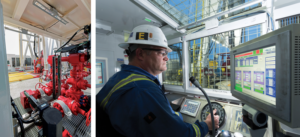
There are four fundamental aspects that must be fully understood: well control, stripping, cementing and operational excellence. The concepts arising from these aspects must be aligned with the automation features of the hardware, i.e. chokes, manifold (Figure 3), software integration into the human-machine interface (HMI), and training required for the end user, MPD technician HMI and driller HMI (Figure 4).
Well Control
For MPD integration, an influx management matrix (IMM) is created and agreed upon by the operator and drilling contractor before operations begin. The purpose of the IMM is to clearly define acceptable limits and actions that should be taken upon reaching any of the trigger points. It is created via hydraulics analysis concerning kick tolerance, based on kick intensity and kick volume. After acceptance by both parties, the rig crew is trained on its use such that when operating conditions prompt a change in drilling activity, the driller takes immediate and appropriate action without delay.
Stripping
Even with MPD, stripping operations can prove difficult when threading a narrow drilling window – especially if the data is parsed between companies, communication is hindered by operating location, and the hardware configuration allows for separate and simultaneous operations.
With MPD-Ready rigs, personnel work side-by-side, constantly communicating during the same operation while being able to view all of the same data together. Further, MPD integration into the rig allows use of existing rig pumps for stripping operations, eliminating the need for additional capital equipment costs and rig-up of auxiliary pump(s), which are typically needed by traditional MPD call-out services.
Managed Pressure Cementing (MPC)
The MPD-Ready rig’s walking system is also used to hold surface backpressure (SBP) while cementing critical sections in order to maintain equivalent mud weight (EMW) at total depth at or above the desired pressure. Maintaining constant EMW while circulating cement is particularly crucial in order to ensure a proper cement job. MPC mitigates inconsistency in the cement column due to formation fluids while condensing slurries to fortify the setting process, increasing its integrity.
Operational Excellence
Operational challenges can be addressed by a combination of adjustments in the operating and modeling software, downhole data, MPD equipment and refinements to operational practices.
Real-time modeling and visualization software with downhole pressure display equipment modifications are instrumental in operating the equipment and calculating the amount of backpressure needed to drill through narrow mud windows. Automated methods of accurately controlling the choke to respond to required parameters (drilling or tripping), including monitoring and reacting features to losses or gains, to hold constant bottomhole pressure on connections are critical. Downhole and surface data are used in conjunction with the software to maintain the appropriate backpressure using equivalent circulating density (ECD) and to confirm that the required backpressure is held during connections.
Operator – The Why, the Purpose
A definition of scope of work or the purpose of the technology include static balance, wellbore stability, narrow mud weight window and severe depletion. MPD must be executed in a responsible manner. Rigorous safety processes must be in place to ensure the well design and well control workflows are aligned to risk management, HAZIDs, etc. The readiness of the MPD system must be reliable, and it must be able to detect an influx. If the intensity is high, can you control it? Operational procedures must be clearly defined for each mode: drilling, tripping with bottomhole assembly and tripping with casing string, with all risks considered. Regulators look for tasks that address risks.
Regulatory – The How, the Application
The minimum requirements (technical) and approval process are as per regulations stated in specific documents. During a recent IADC UBO & MPD Committee meeting, the US Bureau of Safety and Environmental Enforcement defined MPD as a process used to mitigate risks and cost involved on wells that have narrow downhole limits by proactively managing the annular hydraulic pressure profile. Training and competency is needed: How do we react to unexpected events? In the case of an influx, is the well killable? The big picture is to ensure that diligence is done so MPD operators and drilling contractors do not lose overall control of well integrity.
Conclusion
The use of MPD-Ready rigs in unconventional plays has changed the way challenging wells are drilled by delivering a cost-effective automated solution for controlling fluid losses and a safe influx management system, while ensuring successful MPC operations for optimum zonal isolation and completion and production tasks for addition of reserves in strategic portfolios. MPD-Ready rigs are now part of the rig DNA.
What Is Next?
Market conditions will continue to drive change. A true MPD-Ready rig investment is typically driven by long-term strategy for rig marketability and application of new technologies without any cash flow constraints, which is impacted when the application is driven by short-term needs.
The focus on MPD-Ready rigs will continue to enhance drilling performance by increasing reservoir contact efficiency and safe delivery of quality wells. DC