In-situ riser inspection system provides ultrasonic wall thickness, crack detection in a single run
Tool helps to ensure riser integrity, can be deployed for inspection without the need for the riser to be pulled
By Kelli Ainsworth, Associate Editor
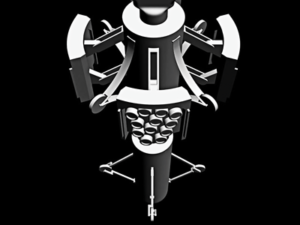
As managed pressure drilling (MPD) becomes a more commonly used and accepted technology, particularly in deepwater wells, it is critical that the drilling riser remains a reliable primary barrier. DNV recommended practices advise that risers be inspected every five years, but many of the common methods for riser inspection either provide indirect measurements or require the riser to be pulled for inspection.
“It’s very costly and time consuming,” said Deitmar Neidhardt, President of Intrgate, a technology strategy company, in a presentation at the 2017 OTC on 1 May in Houston. “It’s also quite dangerous because we have to handle 30- to 50-ft risers. The crews, especially during bad weather, have a lot of challenges to handle the risers properly.”
To provide accurate and direct measurement of the riser and potential anomalies, Intrgate and Weatherford have developed the Offshore Riser Inspection System (ORIS). The tool, still in prototype stage, provides in-situ ultrasonic wall thickness and crack detection of the drilling riser in a single run, without the riser being pulled. “You can reduce the riser joint handling and make significant savings when you compare it to bringing the riser onshore for inspection,” Mr Neidhardt said.
Inspection techniques, such as magnaflux leakage and eddy current testing, only provide indirect measurement of flaws and anomalies in the riser. Ultrasonic wall thickness and crack detection can provide a more direct measurement of anomalies. For this type of measurement, an ultrasonic probe emits an impulse, which travels to the wall of the pipe or riser and is reflected back, and the time it takes for the signal to return is measured.
A standard reflection time is identified, and when the measurements are run, a delayed reflection indicates an internal abnormality in the pipe; an early reflection indicates an external abnormality. “Ultrasonic wall thickness gives you exactly the position and exactly the severity of the anomaly, allowing you to plan ahead for maintenance and, if required, replacement,” he said.
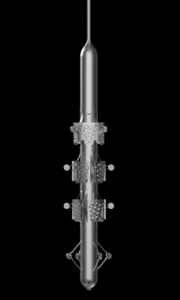
This type of measurement is commonly used for pipeline integrity management, but there have been challenges to using it in the drilling industry thus far. For one, it requires a clean and smooth interior surface and a constant water supply between the sensors and the wall. “The inspection speed is variant, and we often lack full coverage,” Mr Neidhardt said. “That is how we find the riser stacked on surface.” However, the need for good water coverage means the inspection can’t be performed with the riser on the rig; it has to be taken to shore and submerged in a bath and tested.
The ORIS was designed to provide the accuracy and benefits of ultrasonic wall thickness and crack detection without the need to pull the riser for testing. The system can be run before, during or after BOP testing. The system consists of the ultrasonic inspection tool and a wireline logging unit.
After the riser is reverse-circulated with seawater, the tool is lowered on wireline into the riser. While it descends, a casing caliper locator can take readings. Before it reaches the BOP, the tool is stopped in the first riser joint.
The tool’s sensor pads then expand and take a baseline reading to confirm operational parameters, signal strength and proper tool setting, and is run. If there’s concern about a potential anomaly in a particular joint, the tool is run to one joint below the section of concern. There, it takes a baseline reading and measures the section of concern at a higher signal density for an improved resolution of the potential anomaly.
When the inspection is complete, the tool is recovered and the data it has recorded can be reviewed onsite, as well as displayed via satellite onshore for monitoring. “Knowledgeable decisions can be taken in view of future operations and riser joint exchange programs,” Mr Neidhardt said. “Sections of concern can be repaired or replaced depending on the severity of the fault.”
The use of the ORIS could reduce the overdesign or drilling risers because it can accurately ensure riser integrity, Mr Neidhardt said. “That will allow us to reduce wall thickness, which in turn will reduce the weight, which requires less buoyancy,” he added. “In turn, that reduces vortex-inducted vibration.” DC
For more information about the system, see OTC 27945, “Drilling Riser Integrity Assurance for Deepwater Floating Drilling,” presented at the 2017 OTC, 1-4 May, Houston.