Data acquisition capabilities, durability enhanced in new crop of coiled-tubing, intervention tools
Real-time downhole data allowing operators to see more of the well, make on-the-fly adjustments while intervening
By Kelli Ainsworth, Editorial Coordinator
The need to keep pace with the increasingly long laterals that operators are drilling remains a driver for R&D efforts around well intervention and coiled tubing (CT). However, in the current price environment, that innovation must be coupled with the ability to lower costs. New CT and intervention technologies appear to be achieving such cost reductions by increasing equipment durability, which results in fewer trips out for replacement. In addition, more real-time data collection is being used to make real-time adjustments to maximize efficiency.

For the North American unconventional market, one silver lining to the market slump is that it’s providing the industry with an opportunity to reexamine the intervention tools in its toolbox. There had been no good time to do that since the shale boom began, Jorge Mitre, Managing Director – Coiled Tubes at Tenaris, said. “The service companies and oil and gas companies started by using the available technology to tackle the shale business. They took the tools they had in their toolbox at that time and did the best they could with them,” he said. “I think this crisis is forcing the industry to look into those tools and refine them.”
Improving CT intervention tools should be a collaborative process between operators and service companies, said Curtis Blount, Senior Fellow Engineer, Global Completions Engineering for ConocoPhillips. While such collaboration already takes place to a certain degree, he urged service companies to make “better use of industry forums and one-on-one meetings with operating company engineers and scientists to update them on what trends they see and new tools and techniques they are working on. And more importantly, seeking comments and input early in the development phases.”
For ConocoPhillips’ part, the operator is focused on investing in field trials once new technologies make it out of the initial development stages. Mr Blount noted that his company is particularly interested in small-diameter well tractors and other extended-reach tools that can facilitate the push into ever-longer laterals. “Extended-reach horizontal lengths are pushing the practical, economic and sometimes technical limits of coiled tubing,” he said. Further, because many extended-reach wells also experience high pressure and temperatures, he would like to see upgrades in the temperature ratings of intervention tools.
Mr Blount said he also sees opportunities to improve data acquisition through well intervention using tractor-conveyed wireline, “continuous solid-rod” conveyance and coiled tubing-conveyed technologies. While using coiled tubing as a conveyance for logging tools is an established practice in the industry, downhole measurement tools have made great strides. New measurement tools and new methods for data acquisition, including those conveyed on coiled tubing, are providing better results. “Numerous optical camera tools and techniques have been developed, resulting in significantly better images and understanding of downhole problem areas.”
Listening to feedback

As the measured depths of horizontal wells increase, technical demands on coiled-tubing pipe have increased, as well. “We have to stay alert and engaged to make sure the coiled tubing reaches the total measured depth of those wells,” said Teoman Altinkopru, Vice President of Well Intervention at Schlumberger. “It certainly poses a challenge to service companies because you have to keep your technology up to date with the fast-changing well profiles, including technical specifications of surface equipment and the coiled-tubing pipe itself.”
In response to operator requests, the company has developed a more robust version of the ACTive real-time downhole coiled-tubing services that can be used in more challenging well environments. ACTive services were originally launched in 2008 and provide downhole measurements conveyed on fiber-optic, telemetry-enabled coiled tubing. The platform provides real-time downhole pressure and temperature measurements and includes a real-time casing collar locator. The latter compensates for the fact that, due to the residual bend in the carbon steel tubing, coiled tubing can get off-depth. A casing collar locator can be useful in depth-sensitive operations like perforating.
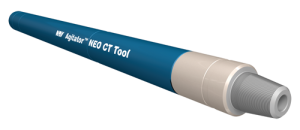
The newest version, the ACTive Xtreme CT real-time rugged downhole measurement tool, is being launched this year. Compared with the original tool’s flow rate of 2 bbl/min and temperature rating of 300°F, the new version can pump at 8 bbl/min and operate in up to 350°F. Further, due to requests by operators drilling in North American unconventionals, Schlumberger has added milling capabilities. “In the past, if our customers needed the real-time measurements during milling a plug, which is a high-volume market in unconventionals, we couldn’t use the ACTive service,” Mr Altinkopru said. “But the ACTive Xtreme tool enables the milling of plugs while gathering real-time downhole information.”
More and more operators are requesting real-time measurements, he continued, because they can help them make on-the-fly adjustments. “Historically, the industry has worked on best practices, rules of thumb, lessons learned in the field and previous failures that built a knowledge base on how to better design the next job,” he said. “Although these things are very valuable, there is nothing like getting real-time downhole responses from the well as you are intervening it.”
Last year, Mr Altinkopru said, more than 360,000 plugs were set and milled with coiled tubing in North America. “None of it was previously done with real-time downhole measurements,” he added. “Now Schlumberger is introducing that ability to the industry to really optimize downhole parameters, such as weight on bit.”
In March, Schlumberger is also launching the ACTive Q real-time flow measurement service to provide real-time downhole distributed flow measurements on coiled tubing via the ACTive DFLO CT real-time flow measurement tool. This tool, also borne out of operator requests, took seven years to develop due to the difficulties of obtaining flow measurements via coiled tubing. Typically, the industry attaches spinners to downhole tools to measure flow rates, during interventions both before and after the stimulation. However, spinners don’t work well at low flow rates and in harsh environments and are easily damaged during coiled-tubing applications. They also are not compatible with stimulation fluids pumped from the surface during intervention, many of which are corrosive.
“At the surface, customers want to identify how much of the pumped fluid is in each zone and modify their diversion techniques to ensure the subsequent pumped stimulation fluids are directed into the zone of interests,” he said. “Spinners cannot withstand those fluids.”
To overcome such challenges, the company developed a proprietary calorimetric sensor package that replaces fragile spinners and avoids time-consuming multiple runs. In a well, Mr Altinkopru said, the ACTive DFLO tool is able to determine where the flow is going to and how much flow each zone is taking, individually. The tool has lower and upper sensor arrays to detect fluids moving away from the injection ports, upwards or downwards in the wellbore.
Each sensor is comprised of three probes: one central heating element that locally increases the temperature of the fluid and two probes measuring ambient temperature. The probe downstream from the heater will be warmer than the one upstream. Comparing the two temperatures will provide the fluid direction. The fluid velocity is calculated based on the heat transmitted to the fluid and the known thermal behavior of the fluid. The flow rate is then calculated based on the fluid velocity, the fluid direction and the wellbore diameter.
On the flip side, when fluid is being pumped into the well, the tool can tell where the fluids are going and provide an injection profile along the length of the zone of interest, he added. “It tells the engineer where the fluids are going at an unbelievable accuracy,” he said.
Around a year ago, water injectors located in a mature field in Central America started showing signs of reduced injectivity. To optimally acidize the dolomitic carbonate formation, high-quality, real-time flow data were required to assess the true fluid intake along the horizontal intervals of those wells and to monitor and adjust the treatment while it was still in progress. During the job, the ACTive DFLO tool was used to measure fluid velocity and detect flow direction to ensure the stimulation fluid was being forced into the right section of the wellbore, as opposed to flowing back to shallower thief zones as it had during simple CT spotting. The results showed improved zonal coverage of the injection water and deeper reach along the horizontal sections, reduced skin value which indicated that formation damage had been effectively bypassed, and a 300% improvement in the injectivity index of the stimulated wells.
Upcoming IADC book aims to address potential uses, limitations of coiled tubing
By Kelli Ainsworth, Editorial Coordinator
Even in the current low-price environment, the coiled-tubing business has stayed busy and is likely to grow, Les Skinner, who has more than 40 years of oilfield experience, said. Operators are turning to drilling sidetrack wells to access reserves that may not have been tapped during a field’s initial development. It is generally less expensive to do this with coiled tubing than with a drilling rig, Mr Skinner said. “Producers want to make sure they maximize their production so they can keep their income up as best as they can in the current economic environment,” he added. “The drilling rigs are being stacked, but coiled-tubing units are being deployed everyday.”
IADC is preparing to publish a book, written by Mr Skinner, this spring, titled, “Coiled Tubing Operations.” It addresses the myriad uses of coiled tubing, such as fishing, sidetracking and conveying tools to the bottom of a directional well. Some of these applications may not be widely known within the industry, Mr Skinner said. “I think a lot of people in the industry don’t recognize the capabilities or uniqueness of coiled tubing,” he said.
Coiled tubing can be particularly useful for maintaining well control in underbalanced applications, for example. “You can maintain underbalance throughout the entire drilling and completions process if you used coiled tubing as the platform for the work on the well,” Mr Skinner said. “You can pump through it while you’re in going into the hole or coming out of the hole, so well control becomes much better.”
The book also discusses coiled-tubing drilling, which has been gaining popularity in Canada and Alaska’s North Slope due to the potential for fast tripping and overall faster drilling times, Mr Skinner said. He noted that in some cases, a well that would take eight to 10 days to drill with jointed pipe could be drilled in just two days with coiled tubing.
Despite these benefits, Mr Skinner recognized that coiled tubing “is not a panacea. It doesn’t work everywhere, and it doesn’t work for every section of the hole.” That’s why the book also points out some of the technology’s weaknesses and limitations. For example, he said, it would not be the best choice to drill a 40,000-ft extended reach well due to the potential for fatigue, buckling and lock-up.
The book also outlines the individual components of a coiled-tubing unit – such as the injector head, reel and power systems – and explains their functions. “It’s an integrated unit. It’s not just a single piece of equipment,” Mr Skinner said. “I think people often view coiled tubing as a lot of spooled pipe on a reel, and they don’t realize there’s so much hardware that goes along with it.”
The primary audience for the book, he said, is people with two to five years experience in the field who have little or no experience with coiled tubing. “It’s for the inexperienced oilfield person who wants to know something about coiled tubing, but it’s not designed as an operations manual.”
Providing a complete picture
Norwegian-based Ziebel has also been focused on developing well intervention tools with enhanced data acquisition capabilities. Neil Gardner, VP of Marketing and Technology for Ziebel, said he believes the demand for data acquisition via intervention will increase, particularly in the US unconventional market as operators look to reenter and refrac existing wells. “When you do that, you need downhole information about where your hydrocarbons are coming from so that you can make decisions on how to improve productivity,” he said.
One of the standard methods for gathering well data is the production logging tool (PLT) conveyed on a coiled-tubing string. It is able to provide data only from the specific point in the well where it is located at a given moment. This can be problematic, Mr Gardner said, because horizontal wells often don’t flow at a steady rate. There are sometimes cyclical surges of fluid through the well. If the PLT happens to be at a certain depth when a surge occurs, then it could provide an inaccurate picture of the well’s flow. “The nature of the flow in unconventional wells makes it very difficult to get the true picture of how they’re performing, unless you can see the whole well at one time,” he said.
The notion of seeing the whole well lies behind the company’s Z-Rod, a 15-mm carbon composite rod embedded with fiber optic lines. It provides distributed fiber optic (DFO) sensing for flow identification, production optimization, well integrity and stimulation monitoring. In a DFO system, the entire length of the fiber acts as a sensor, so data is recorded continuously rather than at individual points. At the same time, the rod can be used to convey conventional downhole sensors to record information in memory mode for later use and analysis. The rod, which was commercialized in 2008 and performed its first job in the Middle East, was deployed on its 100th job in November. The milestone operation was performed for ConocoPhillips to help determine the flow profile of zones in a North American fracked unconventional well.
The primary application for the rod is to provide information about how a well is performing and where production is coming from, allowing operators to address production problems through workovers or changes in their completion design. It can also be used to monitor stimulation treatments, such as acid treatments and scale inhibitor treatments, as the carbon composite material is resistant to hydrochloric acid, hydrogen sulphide and carbon dioxide. “This gives real-time feedback as to the success of the treatment placement and can be used to confirm production gains when the well is subsequently flowed post-treatment with the Z-Rod still in the well,” Mr Gardner said.
A potential future use for the carbon rod is monitoring frac treatments while in the well to determine where the slurry is being delivered downhole. Ziebel will be testing this capability in 2016, working to determine what pump rates the rod can withstand before unacceptable erosion occurs. “This application will be of great interest when re-fracking becomes more widespread than it is today,” Mr Gardner said.
Ziebel is also developing a higher-temperature version of the Z-Rod that can withstand the 320°F downhole environment of the Eagle Ford, Bakken and other higher-temperature plays. “Today, people who get data from the Eagle Ford are damaging PLT strings and wireline cables when attempting to gather data in those hot wells,” he said. The tool is currently rated to 280°F, but the company hopes to push that to 350°F. The challenge is to develop a composite material that is able to retain the necessary strength and stiffness properties at higher temperatures. The company is currently testing potential compounds and expects to have a higher temperature-rated Z-Rod ready for field trials late this year.
In addition to improving the temperature rating, Ziebel is working to add copper electrical conductors to the Z-rod so it can be attached to a well tractor. Doing so will enable the tool to go further into horizontal wells. Currently, it can reach between 3,000 to 6,000 ft beyond the heel of a well, but Ziebel modeling indicates that by attaching the rod to a tractor, it can increase the tool’s reach by an additional 8,000 to 10,000 ft. This will allow the rod to provide DFO measurements over most, if not all of, the length of any unconventional well.
Bringing more value
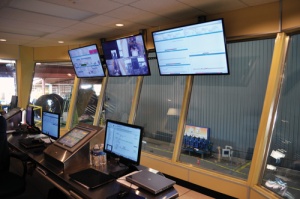
In addition to demands for increased functionality from well intervention tools, service companies and equipment manufactures are also being asked to deliver solutions that decrease the overall cost of the intervention operation, Michael Rossing, WHO Product Line Director for National Oilwell Varco, said. “To us, that means bring more value. The cost of any operation is not the sum of the products or services but rather the sum of how these products and services interact.”
In May, NOV released an addition to its Agitator line of oscillation tools, the NEO. The tool sends pressure pulses along the coiled tubing’s longitudinal axis that breaks static friction between the coiled-tubing string and the wellbore or casing, which helps prevent buckling. “This product is all about helping our clients get deeper into horizontals,” Mr Rossing said. “It will actually enable the completion of longer laterals.”
The tool was modified to improve the overall performance by increasing operating pressure up to 10,000 psi, compared with pressure limitations of 5,000 psi in earlier Agitator tools. The power section has also been redesigned to allow pumping at higher flow rates. In addition, the valve assemblies have been designed to work more effectively. Together, these changes produce axial vibrations that work on longer lengths of coiled tubing. This reduces buckling, allowing for an increased weight on bit and higher ROP.
In a field test in Q1 2015, a 3 1/8-in. Agitator NEO CT Tool was run during a cleanout operation in a well in Zavala County, Texas, in the Eagle Ford. It was run on a 2 5/8-in. coil with a flow rate of 5 bbl/min. The tool reached a total depth of 15,784 ft during this cleanout run in a single trip.
Improving durability
Since the advent of horizontal drilling and the resulting shale boom, CT has been consumed and worn out very quickly, Mr Mitre of Tenaris said. This is partially due to the accelerated tubing fatigue associated with significantly increased operational loads and more damaging operating environments. Longer horizontal well sections and higher operating pressures necessitated the use of bigger diameters and higher yield strength coiled tubing. To increase the reach of coiled tubing, the diameter has to be increased, with consequent tubing strain increase while bending in the reels.
As horizontal wells have gotten longer, the typical diameter of coiled tubing used in longer horizontal wells has increased from 2 in. to 2 5/8 in. High internal pressure adds to the bending load and strains the tubing is subjected to, thus requiring higher-strength tubing materials. Additionally, the use of recycled water during intervention operations has introduced microbial corrosion as a challenge.
In response, Tenaris has developed BlueCoil, a CT technology platform that can produce higher yield strength tubing than with the conventional manufacturing process but without compromising the life of the bias welds that are needed to produce the necessary length of coiled tubing. It is made from a patented steel chemistry and a proprietary heat treatment process and was designed to provide higher strength and improved fatigue and corrosion performance. Development began in 2011, and the first strings were put in the ground in commercial applications in mid-2015.
Often, it can be difficult to increase a coiled-tubing string’s yield strength without compromising the welding, Mr Mitre said. Specifically, as a tubing string’s yield strength is increased, the fatigue life and environmental resistance of the bias weld decreases. The lower fatigue life and environmental resistance of the bias weld then decreases the life of the entire string. “As you go high in yield strength, it’s more difficult to reliably weld the pipe,” he said. “Our intention was to develop a high yield strength coiled tubing that is not compromised in the welded areas, which we fully achieved.”
The most commonly used BlueCoil has a yield strength of 125 ksi, compared with the conventional 110 ksi. In field testing, all conducted in Texas, 17 jobs were performed with a 20,500-ft string. These jobs included 26 full runs in and out of multiple wells at depths ranging from 15,000-17,000 ft, and they accounted for 41% of the string’s used life, according to a third-party model based on correlation of extensive BlueCoil lab test data. An equivalent conventional 110-ksi string would have accumulated 110% of its predicted fatigue life during the same field test jobs, Mr Mitre said, which means BlueCoil has a field fatigue life that is more than double that of conventional coiled-tubing strings.
By increasing the tubing string’s yield strength, the tubing can be lighter but just as strong. “You can obtain tubing strength with the steel yield strength or with the thickness of the pipe,” Mr Mitre said. “So if you can increase yield strength, you can use a lighter pipe and, therefore, it’s easier to carry and easier to manage.”
Currently, the company is working to identify additional steel chemistries that would enhance the BlueCoil system’s H2S corrosion resistance. The goal is to be able to tackle challenges in markets like the Middle East where unconventional operations are starting. “Having a platform to develop new steels gives us freedom to start experimenting with different chemistries and looking to sour service products, which will definitely be very helpful when it comes to environments that are H2S heavy, like in Saudi Arabia.” DC
ACTive, ACTive Extreme, ACTive Q and ACTive DFLO are registered terms of Schlumberger. Z-Rod is a registered term of Ziebel. NEO is a registered term of NOV. BlueCoil is a registered term of Tenaris.