Beyond ROP: Industry taking systems view to drilling optimization
Better sensors and simulations that integrate real-time downhole data are being used along with torque-limiting devices and intelligent drilling systems
By Katie Mazerov, Contributing Editor

Optimized drilling once meant drilling farther and faster to achieve high rates of penetration (ROP) using efficient, cutting-edge technologies and approaches like pad drilling. Today, with oil prices remaining low, that need for speed has given way to a more balanced approach, with operators taking a step back and a wider view of downhole drilling optimization.
Click here to watch a video interview with Jon Rhodes, Drilling Services Business Development Manager for Baker Hughes, on the company’s new drilling optimization service.
Sophisticated sensors, significantly improved data management and analysis, automated systems that take humans out of the loop and real-time monitoring are helping drillers to manage costs and gain efficiencies. ROP and efficiency are still important – yet, utilizing data more effectively to understand the drilling process and to extend bit and equipment life and reduce the number of trips downhole are also critical to increasing well value and maximizing assets.
“With the downturn, operators are shifting from the mantra of ‘drill, baby, drill’ – maximizing ROP at the expense of other parameters – to a focus on drilling consistently to reduce time to reach total depth (TD), optimizing every stage and preventing tool damage,” said Liam Lines, Research Engineer for Weatherford Drilling Services and 2016-2017 SPE Distinguished Lecturer. He defines downhole drilling optimization in four key categories:
• High-quality sensors and measurements to improve drilling efficiency but also to prevent tool damage and mitigate downhole vibration and shock;
• Simulations and models that integrate torque-and-drag, shock and vibration and hydraulics to gain more meaning from downhole data and engineer out problems before they occur;
• Downhole tools, such as torque-limiting devices and shock subs, to prevent stick-slip and shock in conjunction with intelligent drilling systems, such as top drives and auto-drillers;
• Training crews to interpret large amounts of complex data and downhole situations and increased use of automated systems that take humans out of the loop or tell drillers what actions to take.

One large independent believes this is an “exciting time” for drilling optimization and automation. “Commercial drilling automation systems are being introduced, and the industry is seeing the improvement potential possible with these tools,” said Matt Isbell, Drilling Engineering Advisor for Hess Corp. “The new automation systems also provide more measurements and faster data-acquisition rates. Drillers use this information to better understand and control the drilling process. Engineers use it to improve the design of the drilling system. This drives out inefficiency and improves the capability for drillers to control the automation systems and stabilize the drilling process at higher ROP. These new, improved and automated control systems are driving performance improvement.”
Many factors limit wellbore delivery during a run, Mr Isbell said. “Drilling optimization processes were developed to address these limitations and reduce well delivery time and cost. Drilling optimization is about balancing the drilling system capability with the operating method to complete well objectives.” It happens by managing what he calls three learning cycles:
• A real-time learning cycle with the drilling system in the ground;
• A run-to-run cycle, where small changes to the drilling system, like a bit or motor change, can be made; and
• A well-to-well cycle, where the drilling system can be changed substantially.
“In this way, the drilling team methodically learns about obstacles preventing a better result and is always improving the drilling system and how it is used.”
Associated system measurements enabling automation also are helpful to uncover drilling limiters as they provide a better understanding of the drilling process and engage problem solving. “Downhole measurements have always been useful but are difficult to justify as they require expertise and extensive analysis time to interpret and apply,” Mr Isbell continued. “Together, the measurement and control systems give a better understanding of the drilling process, allowing engineers and drillers to improve the drilling system and quickly make the most of how they use it in real time. Next, a better real-time visualization method is needed that will assist the driller to intuitively use the multitude of measurements to improve well delivery.”

Operators can successfully drill in many different arenas if they are good at learning and adapting quickly, he suggests. Developing and capturing knowledge, then applying it in standardized processes, creates a rapid learning experience, resulting in drilling excellence. “Great companies systematically do this and apply it across multiple drilling campaigns to manage risk and maximize drilling performance. The new automation tools and measurement information will act to further enable and standardize this basic process.”
Incentives to Optimize
Reflecting this trend, National Oilwell Varco’s (NOV) eVolve Optimization Service saw the biggest uptick in two years during November and December 2015, said Tony Pink, Vice President, Dynamic Drilling Solutions (DDS) for NOV. “American operators want to drill wells as cheaply as possible, but until the downturn, there was little time or incentive to optimize.”
The eVolve service provides tiered drilling optimization capabilities using downhole tools and surface automation to feed real-time downhole data into the rig’s control system. The system’s ADVISE tier, which uses memory tools, can be installed on any rig in the US. The AUTOMATE tier delivers optimization using downhole tools linked with the company’s IntelliServ Wired Drill Pipe Network (WDP) to send data back to the rig.
“We’re talking about optimizing the entire drilling process, which can only happen by connecting what is going on dynamically at the bottom of the hole back to the machine at the surface,” Mr Pink explained.
“Typically, we do a four- or five-well project, looking at what the customer is currently doing, and follow up with an optimization cycle of analysis, planning and execution. We take data from downhole tools, merge it with surface data and then provide a set of answers to the customer. If the data indicate an issue with the bottomhole assembly (BHA) design, for example, we redesign the BHA, go through the optimization cycle again and measure the changes.”

The service also addresses invisible nonproductive time (NPT), often hidden in drilling reports. “The report may indicate 22 hours of drilling time, but actual drilling time was 19 hours, the rest being downtime,” he said. “We find that invisible NPT and turn it back into useful time.” One solution reduces connection times, which eat up total drilling time. “Using the AUTOMATE-tier high-speed data capability, we can get a survey before we even make the connection and reduce a 7-minute connection to 1 ½ to 2 ½ minutes.”
The AUTOMATE tier has saved operators more than 30% of rig time in the Eagle Ford and Bakken plays, he added, and is seeing strong interest in Norway, where it has been installed on two jackups, the Maersk Intrepid and the Rowan Viking.
IntelliServ2, NOV’s latest-generation WDP, upgraded in 2014 and 2015, delivers increased reliability and ease of use at a reduced cost of ownership, said Brian Van Burkleo, Director, Business Development for IntelliServ. “Operators, of course, rely on downhole data to drill wells. WDP enables this same critical data to simply be acquired faster. It’s about small but frequent time savings in surveys and downlinks.” Whereas conventional mud pulse telemetry operates at 6 to 12 bits/sec, WDP delivers 57,000 bits/sec, he noted.
Mr Van Burkleo anticipates the technology is entering a growth phase with the new-generation system, which includes data link repeaters placed along the drill string to boost signals to the surface, a network controller at the surface and improved inductive coils. The first IntelliServ2 string, installed on a rig in December 2014 in the Bakken, has drilled more than 140,000 ft. On one 16-well project, the system’s high-speed telemetry capability enabled immediate transmission of downhole data and closed-loop drilling automation, reducing drilling time by multiple days per well compared with previous vertical and curve pads.
At the end of 2015, NOV had four permanent WDP installations globally and anticipates 16 permanent installations by year-end. “Where we’re seeing the greatest adoption and WDP delivering net cost savings to operators are those high-volume, high-cost multiwell fields in the North Sea and offshore western Australia, and high-volume, low-cost wells on US land, the Middle East and Southeast Asia,” he said.
Actionable Data, Pre-Job Planning
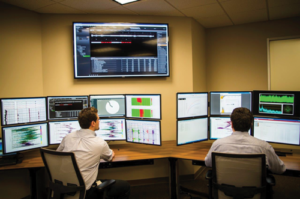
Providing actionable information for rig crews was a key driver in the design of the Schlumberger OptiDrill real-time drilling intelligence service. “We engineered a technology that not only generates and records large amounts of data but also provides a set of real-time actions to the rig floor crew that executes drilling,” explained Yezid Arevalo, Drilling Solutions and Interpretation Product Champion for Schlumberger Drilling and Measurements. “We look at how we use downhole drilling measurements to understand the drilling process better to mitigate risk and uncertainty and improve performance.”
Commercialized in November 2014, the service is designed with three key elements:
• The sub itself, which is located in the BHA and provides comprehensive, high-frequency measurements of the drilling process, which can be used in real time and for longer-term analysis;
• An interface that integrates downhole and surface algorithms to provide automated answers that facilitate clear directions to the driller. Instead of a red light or alarm that signals something is wrong, animations illustrate what is actually happening in real time, indicate the severity of the situation and present a diagnosis. “It provides specific directions for optimizing drilling parameters, such as increasing weight on bit (WOB) or rpm by a specific amount,” Mr Arevalo explained.
• High-level, often remote, interpretation of data using real-time models of aspects of the drilling process to understand longer-term trends.
Especially suited for complex, high-profile wells, the OptiDrill system has been implemented in the North Sea, Gulf of Mexico (GOM), West Africa and Brazil. In the GOM, the system’s high-frequency capability was used to identify changes in resonance frequencies for several operators experiencing high torque in BHA connections while drilling long salt sections. “When we eventually ran the high-frequency tool, we saw some specific changes in resonance frequencies regarding lateral vibrations and torque that could be simulated,” Mr Arevalo said. “Using the high-frequency data to feed back into and correct the surface models, we saw why the connection at the BHA was overtorqued and the connection at the bit was not. This enabled us to make changes in the BHA to correct the problem.”

The planning phase of a well, involving both service company and operator, is critical for determining which system is best for a given formation, he continued. “The earlier we engage with our customers, the better the results are in terms of performance. At Schlumberger, we are committed to setting drilling performance objectives with our clients and being rewarded only if those objectives are achieved. We have to question and challenge which technology goes downhole, as well as the limits of the rig. Often that is where real optimization occurs.”
The Schlumberger ROPO rate of penetration optimization software, the latest version of which was introduced in 2014, reads real-time drilling data and provides an optimum set of parameters, specifically rpm and WOB, to obtain maximum ROP in any circumstance. In the planning phase, the drilling team establishes a drilling envelope based on the constraints of the drilling system and the formation.
The software also models bit/rock interaction, relating WOB and rpm with ROP and torque. “Once we have that model, the system matches the current drilling data to the model so we can consistently optimize the position in the drilling envelope throughout the run,” he said. “At the end of the process, we evaluate how well we actually executed the plan to measure performance and enable continuous improvement.”
RFID-Actuated Tools
Weatherford, which is also placing more emphasis on pre-job planning, recently established a global Drilling Engineering and Optimization group to ensure consistency and best drilling practices in addressing downhole issues, such as torque-and-drag and stuck pipe. The company is ready to begin field trials of a new torque-limiting tool, which is expected to demonstrate significant improvements in ROP while also reducing damage, Mr Lines said.
Improvements in sensors, with an emphasis on capturing high-frequency downhole data, have enabled the industry to move from recording one data point every five seconds to 1,000 samples per second. “The ability to take a high data-rate snapshot every few seconds has really opened people’s eyes to how damaging the downhole environment can be,” he noted. “Damage leads to downtime, multiple trips and delays in deviating around stuck tools.”
Cost is an important consideration in the company’s increasing integration of radio frequency identification (RFID)-actuated tools to provide single-trip solutions, according to Alex Goodwin, Global Business Development Manager, Performance Drilling Tools for Weatherford. “For underreaming operations, for example, we can use the sensors in our RFID underreamer to record vibration and torque that may not be recorded by M/LWD tools, which are typically positioned at the bit 150 ft below the underreamer. With that data, we can modify the BHA by adding stabilizers or changing drilling parameters for future jobs.”
Mr Goodwin, who is also product champion for the JetStream RFID circulation sub introduced in 2015, said RFID tools provide greater operational flexibility and efficiency than mechanical ball-drop activation systems. The latter are often limited by the restrictive inside diameters (ID) of M/LWD systems. RFID technology allows tools, such as underreamers to eliminate ratholes and circulation subs for wellbore cleaning, to be deployed on the same BHA and independently controlled. The technology enables the underreamer to open and close as many times as needed and allows the circulation sub to be activated to clean the wellbore without making a second trip.
“With the reamer open, we can only rotate the drill string at 120 rpm in some wells because of torque and vibration, but by closing the reamer at TD, we can go to 150 or 175 rpms and higher flow rates, which may be necessary to remove cuttings and effectively clean the hole,” he said. “Drilling and cleaning the well properly helps ensure that the casing string makes it to TD, which optimizes the completion.”
Achieving a Balance

Approaches to drilling optimization depend on operator philosophy, ranging from focusing on overall asset efficiency to focusing strictly on operational cost, said Jeremy Greenwood, Chief Advisor for Drilling Performance for Halliburton’s Sperry Drilling PSL business line. “Drilling optimization is about achieving the best balance between the two that delivers highest overall well value. Only focusing on the instantaneous drilling speed and daily authorization for expenditure limits a driller’s perspective and can ultimately reduce overall well production and increase completion costs.” An analytical and interpretative process informs operators on how their drilling system is actually behaving as opposed to assumed behavior, he noted. “The physics of drilling mechanics does not change, only the ability to observe what is really happening downhole.”
Sperry Drilling launched the DrilSaver Vibration Monitoring System 20 years ago to reduce failures and improve penetration in hard rock using PDC bits. “The technology was specifically designed to identify stick-slip vibration by looking at torque signatures and identifying the frequency and amplitude of the cyclic pattern in the torque, allowing the severity of the torsional vibration to be quantified,” Mr Greenwood explained. “The aim is to keep the equipment, especially the bit, in the hole operating as long as possible and prevent it from wearing out. Wasting all the energy in vibration, as opposed to cutting the rock itself, reduces ROP and damages the bit.”
Now in its third generation, the system analyzes other drilling parameters, such as torque, rpm, and hookload and standpipe pressure, that provide energy into the drilling system. “We’re seeing a lot of applications in deepwater, where efficiency is especially critical and reducing trips is important,” he said. DrilSaver III is also used for salt drilling to manage the mud weights needed to keep the salt stable. “If the salt starts to creep and the mudweight management for those hole sections isn’t adequate, high levels of torsional vibration are created in the drill string, which can lead to tool failure.”
Complementing the vibration monitoring is drilling efficiency software that combines a geology model with a mechanical model of drill bit behavior to calculate the optimum drilling parameters needed to achieve expected penetration rates, creating a road map for the driller. With real-time capability, the system updates rock strength calculations based on rock drilled to compare actual drilling parameters, such as weight, rpm and flow rates, with optimum values to help achieve the best ROP and maintain bit life. “The recommended instantaneous ROP may be slightly slower, but if it extends the bit life so the overall shoe-to-shoe time is less, the net gain can be more than if we drill too aggressively and wear out bits prematurely,” Mr Greenwood noted.
A third system quantifies where efficiencies actually were derived during the drilling process by determining the time spent on over 40 activities within the categories of drilling, tripping and making connections.
Developed to obtain measurements that were previously unavailable, Sperry Drilling’s Quasar Pulse M/LWD service with MWD and LWD tools rated to 392°F (200°C) helps reach TD in a single run in high-pressure, high-temperature offshore wells. In 2014, the service, along with an adjustable gauge stabilizer, was run in five wells from a platform rig in Southeast Asia. In a single-run performance where circulating temperature reached 369°F (187°C), the system drilled and logged 7,593 ft (2,284 m) to TD at 12,946 ft (3,946 m) for an average ROP of 101.4 ft/hr (31 m/hr).
A Systems Approach
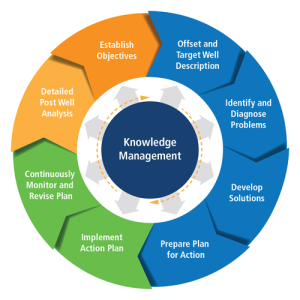
Increasingly, companies also are taking a systems approach to drilling optimization – identifying the issue, determining a course of action, applying appropriate technologies and establishing a feedback loop. “We can’t improve efficiency, reduce NPT and improve risk management in isolation or simply by tweaking one drilling parameter,” said Jon Rhodes, Drilling Services Business Development Manager for Baker Hughes. He identified three levels of downhole drilling optimization:
• Basic data gathering with a reporting system using MWD tools, applied universally in the industry;
• A more proactive management system that collects both downhole and surface data, such as vibration, torque and weight on bit, to improve drilling in real time and manage parameters to improve how the well is drilled; and
• A high-level systems approach that looks at the entire drilling process by gathering offset data on similar well types, actively managing parameters while drilling and doing in-depth pre- and post-well analysis to optimize current and future wells being drilled.
Which level to apply is often determined based on the cost and complexity of the well. “The more expensive the well, the bigger the prize of improving drilling efficiencies. An exception could be in the case of a specific issue, such as stuck pipe or vibration damaging the BHA,” Mr Rhodes said.
Baker Hughes applies a systems approach to drilling optimization using a Knowledge Management Wheel that outlines the process, from establishing clear objectives to detailed post-well analysis, with downhole data provided by the company’s CoPilot real-time drilling optimization service. In 2015, the method was used to improve hole quality and enhance production in a North Sea directional well. A high-efficiency PDC bit was optimized using a bit tilt analysis, while the BHA was enhanced with a rotary steerable system. The drilling optimization service was applied to further reduce downhole drilling dysfunction. The well was drilled to TD in one run as planned, with a below-rotary table time of 13 days compared with the planned 26 days.
As technology develops, continued improvements in data gathering, interpretation and management to identify and mitigate previously undetectable downhole events have been an important step-change, Mr Rhodes added. This year, Baker Hughes will launch an enhanced drilling optimization service that incorporates CoPilot 2.5 and a new downhole drilling dynamics sub that acquires high-frequency downhole data, both in real time and in memory for post-well analysis, to better understand what is happening downhole. “The new service will, among other enhancements, double the frequency of downhole data acquired,” Mr Rhodes explained. “Downhole data that traditionally was gathered at about 460 hertz will now be gathered at 1,000 hertz, or about 1,000 data points per second.”
An emerging trend involves both operators and service companies investing in more automated drilling optimization technologies to drive better efficiencies. “With greater automation, we’re moving the experience away from the individual to an algorithm in a computer based on thousands of hours of experience, with data automatically interpreted in milliseconds,” Mr Rhodes said. DC
eVolve and IntelliServ are trademarks of NOV. OptiDrill and ROPO are marks of Schlumberger. JetStream is a registered term of Weatherford. DrilSaver is a trademark of Halliburton, and Quasar Pulse is a service mark of Halliburton. CoPilot is a trademark of Baker Hughes.
Click here to view a video of Schlumberger’s OptiDrill service.
Click here to read about Petrolink’s use of cloud-computing.
- At the end of 2015, NOV had 4 permanent IntelliServ Wired Drill Pipe Network installations globally and anticipates 16 permanent installations by the end of 2016.
- Improvements in sensors, with an emphasis on capturing high-frequency downhole data, have enabled the industry to move from recording 1 data point every 5 seconds to 1,000 samples per second.
- Sperry Drilling’s Quasar Pulse M/LWD service is rated to 392˚F (200˚C). It has been deployed to help operators reach TD in a single run in high-pressure, high-temperature offshore wells.