Mechanical pressure relief system protects riser against overpressure during MPD, riser gas handling
System does not require second umbilical, can be resealed after flowing drilling mud at high rates
By Brian Piccolo and Christian Leuchtenberg, Managed Pressure Operations
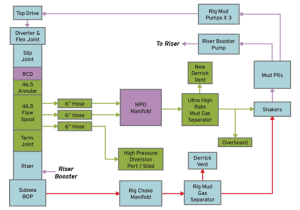
Managed Pressure Operations (MPO) has designed and manufactured a redundant, mechanical pressure relief system for installation on the drilling riser to protect against overpressure during managed pressure drilling (MPD) and riser gas handling (RGH). The Riser Safety Valve (RSV) protects against human error and equipment failure that can cause the riser to be fully shut-in while being pressurized by formation flow, gas migration, and/or circulation with the mud pumps. In a riser overpressure event, the RSV diverts flow overboard via port or starboard diverter lines in a similar fashion to the conventional rig diverter system.
The requirement for a riser pressure relief system was originally developed in 1999 during the joint industry project (JIP) titled “Drilling with Lightweight Fluids,” which was run by Petrobras with participation from other operators and service companies. The analogy made during that JIP, which was the first to run a pressurized riser during an MPD operation, was that a riser full of pressurized fluid of significant volume, possibly gas and flammable inventory, should be treated the same as a high-volume separator vessel, for which it is mandatory to have a pressure relief system. In both cases, an overpressure event can burst a pressure-containing system, resulting in the uncontrolled flow of a large volume of flammable fluid. Such a scenario is especially concerning in a riser gas event where a substantial portion of the released fluid may be hydrocarbon gas.
The solution used for the field test of the 1999 JIP, which was carried out in 2000, was to have a rupture disc on a third outlet of the riser flow spool. The service company, Weatherford, continued to use this design in its RiserCap system that was deployed for the next 10 years.
Subsequently, MPO developed PLC-based overpressure protection systems that can reseal on cuttings. However, these systems have a cost impact due to the requirement for a second umbilical to maintain redundancy in the event of a communication error.
As such, the RSV was designed as a fully mechanical and low-cost alternative to the PLC-based systems and ultimately does not require a second umbilical. The RSV can also reseal reliably after flowing drilling mud at high rates.
Riser Pressure Relief Systems
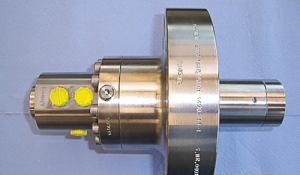
Deepwater drilling risers have been designed as conduits to transport wellbore returns to the rig during conventional drilling operations or to divert returns overboard in the event of a shallow gas kick or an influx escaping past the subsea blowout preventer (SSBOP).
With the recent deployment of MPD and RGH systems beneath the telescopic slip joint, the most significant pressure limiter in the riser is isolated. As a consequence, a drilling operation is now able to apply a safe amount of backpressure to the riser for purposes of controlling wellbore pressure during MPD in difficult hole sections or processing riser gas returns in an environmentally sound and safe manner.
While the results of a global riser analysis will indicate that the drilling riser can withstand a substantial amount of pressure when under the control of an MPD or RGH system, one should be aware of the fact that the riser is still not intended to serve as a pressure containment system in the same manner as the SSBOP and wellbore. Instead, the riser is a long pressurized vessel with inventory volumes similar to a large production separator, which requires a pressure relief system to prevent burst and the subsequent uncontrolled flow of flammable fluids. Vented pressure should ideally be directed overboard via designated diverter lines.

A riser flow control system can be an MPD system with a rotating control device (RCD) and/or an RGH system with an API 16A annular beneath the slip joint. Regardless of whether one is using an MPD or RGH system, there will also be a flow spool, which permits riser flow to be diverted to a choke manifold at surface and a high flow rate mud gas separator. On a deepwater drilling vessel, flexible hoses connect the flow spool to the topside equipment. Figure 1 shows the installation of a combined RGH and MPD system. By removing the RCD, it represents an RGH system.
Since the riser is designed as a flow conduit and not a pressure containment system, a continuously available pressure relief system is needed to protect the riser against a control system failure, operational error, or a blockage in the lines while transporting riser returns to the rig. In such circumstances, a pressure relief system provides an alternative flow path out of the riser for drilling returns so that the riser is not overpressured.
While pressure relief valves on topside manifolds can address many of the potential overpressure risks considered in a failure modes effects analysis, the requirement for dual isolation ball valves at the hose-gooseneck connection on the flow spool can cause the riser to be isolated from surface, creating the possibility of an overpressure event. MPO is especially concerned with such an event occurring during troubleshooting operations when the risk of human error is inherently increased in any industry. For this reason, riser pressure relief valves are required on the flow spool.
Recent attempts by other designs to change this status quo that was established in 1999 should be treated with extreme caution. The idea that procedures could be used to circumvent the need for a safety system is taking the industry backwards after having a track record of riser overpressure protection going into the second decade.
Limitations with Existing Pressure Relief Systems
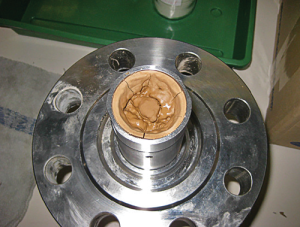
Existing pressure relief systems in the industry are limited for operational and economic reasons. The two current mechanical pressure relief options are the traditional mechanical pressure relief valve and burst discs. The traditional mechanical safety valve lacks the ability to reseal after flowing mud with cuttings as a result of erosion. The burst disc ruptures in the event of an overpressure event. Once the seal has ruptured, maintenance procedures are required to replace the burst disc. In either case, the lower marine riser package will need to be unlatched and the flow spool retrieved to surface for maintenance, which results in nonproductive time.
PLC-controlled pressure relief systems are also available, which can operate isolation ball valves to relieve pressure. High-specification subsea isolation ball valves can reliably reseal on cuttings. However, a loss of electrical power or instrumentation can cause an unintentional opening of the relief valves in order to ensure a fail-safe condition. Such a case can cause an environmental hazard by diverting oil-based drilling mud overboard when there was no overpressure event to begin with. In contrast, a lack of system availability during a riser overpressure event can cause the riser to burst, resulting in danger to the rig and crew, as well as an environmental hazard. For this reason, such PLC-controlled safety systems are deployed with two umbilicals, resulting in additional cost.
The RSV
A mechanical riser pressure relief system has been designed, tested and manufactured that has the advantages of being continuously available like the rupture disc or traditional mechanical pressure relief valve but is also able to reseal after flowing riser returns. The system does not require the cost of two umbilicals to ensure a low risk of unintentional actuation. The proposed system, the RSV, utilizes two independent, high-reliability subsea ball valves to vent riser returns due to their ability to reseal. Each ball valve has a hydraulic actuator, which is mechanically signaled to open via a pilot valve actuator (PVA).
The PVA is a combined piston and pilot valve assembly. The PVA piston is in pressure communication with drilling mud in the riser bore, causing it to retract at a set pressure. The retraction of the piston energizes the pilot valve to permit the flow of pressurized hydraulic fluid from a subsea accumulator bottle to actuate the ball valves. The ball valves remain open until manually reset. The RSV system is fully independent and redundant. It is comprised of three key components: isolation ball valves, PVAs and locally installed accumulator bottles.
The PVA effectively consists of an off-the-shelf pilot valve, enclosed in a housing and connected to the flow spool via an API flange connection. The piston face extends through a bore in the flow spool so that the piston can be in pressure communication with the drilling mud. The PVA is designed to withstand exposure to wellbore fluids and seawater and has as variable set point range of 500-2,000 psi.
Since the RSV is directly actuated by the pressurized drilling mud itself and does not rely on a PLC control loop, the risk of unintentional actuation of the RSV due to a power or communication failure is eliminated. When combined with the fact that the hydraulic energy required to operate the RSV is stored locally, the RSV effectively eliminates the need for two electrohydraulic umbilicals to safely conduct MPD and RGH operations.
To further improve the reliability of the RSV, the remaining single umbilical can still be used to open the RSV isolation valves via PLC control. Under this configuration, the signal for actuation is delivered by two diverse means. The first mechanism is via the force of the pressurized drilling mud on the PVA piston face. The second mechanism is via a pressure sensor in communication with drilling mud in the flow spool bore. Diversity reduces the risk of common mode failure.
Installation on a Direct Hydraulic RGH System
The RSV is installed on the first manufactured direct hydraulic RGH (RGH-DH) system. The RGH-DH series is MPO’s second generation of riser gas handling systems. The RSV system is also configured with a PLC to maximize reliability as described earlier. The RGH-DH and RSV have been designed to DNV OS E101. This system is capable of closing an API 16A 3K psi annular in under 5 seconds to respond to gas breakout in oil-based mud.
As part of validating the RSV system, the PVA, which is a novel component, underwent industry standard and internal testing by both the valve manufacturer and MPO and MH Wirth. Vendor testing validated that the PVA met and exceeded applicable API 6A, API 17D, API 16D standards. After passing vendor testing, the PVA was tested in a custom-designed mud chamber where the valve was exposed to drilling mud with riser temperature and pressure conditions.
During this time, the PVA was operated under high and low temperatures on the seawater and mud side. Finally, the valve was removed from the mud chamber with a mud filter cake permitted to dry on the face of the piston. After several days, the valve was returned to the mud chamber with the hardened filter cake intact and still functioned as required. The entire battery of tests was conducted without redressing the valve and passed successfully. The valve was cycled thousands of times without failure.
In conclusion, the RSV system can enhance the safety of RGH and MPD operations by ensuring that a continuously available pressure relief system is installed on the riser. This system does not include the cost of a second umbilical associated with PLC-controlled systems and the nonproductive time associated with performing maintenance on a traditional pressure relief system that cannot reseal after use. The RSV system embraces the philosophy that simple mechanical systems are often lower in cost and more reliable than complex electrical systems. DC
This article is based on a presentation at the 2016 IADC Managed Pressure Drilling and Underbalanced Operations Conference, 12-13 April, in Galveston, Texas.