Liner system designed to provide effective isolation in high-risk, high-cost HPHT wells
System combines advanced PBR, liner-top packer, liner hanger to operate in extreme bottomhole conditions
By Sean Yakeley, Weatherford
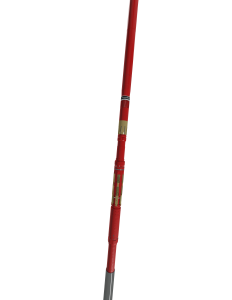
Well environments with increasing pressures, temperatures and depths are becoming the norm in hydrocarbon recovery. These complex and harsh-environment reservoirs drive the need for high-performance completion systems with more durability and reliability than conventional equipment. Innovative technology is paving the way for the industry to delve further into these challenging and risky frontiers, in which the cost of failure is enormous.
Liner systems provide a variety of benefits to enhance wellbore economics and efficiency. Installing a liner can reduce casing and cementing costs and minimize rig time. Liners enable the drilling of deep wells with smaller, more efficient rigs, and they facilitate efficient casing of open-hole sections below previously installed casing. Liner systems also ensure zonal isolation while reciprocating during well conditioning and while rotating during cementing operations. Additionally, they provide annular barriers relative to long casing strings that tie back to the surface.
Typically, a liner system consists of a polished bore receptacle (PBR), liner-top packer and liner hanger. The liner, or casing string, is run into the well and suspended below the wellhead within existing casing by means of a liner hanger. The drill pipe, or work string, lowers the liner to the desired setting depth and is retrieved after the liner is set. The PBR provides a means of tying back into a liner with either a tieback seal stem or a tieback packer.
Today, the majority of wells worldwide include liners, and initial well designs often factor them in. A complete liner-hanger solution exists for virtually every well type.
For example, a deepwater or ultra-deepwater well might include as many as five or six liners in various sizes as an alternative to running long, heavy casing strings that put stress on rig equipment. In extended-reach laterals, liners equipped with centralizers and friction rolling cones overcome friction to move equipment downhole more easily.
In recent years, liners and related equipment have evolved to withstand high-pressure, high-temperature (HPHT) conditions. Reliable packers and seals prevent unwanted gas migration and minimize the effects of long-term hydrogen sulfide (H2S or sour gas) and carbon dioxide (CO2) exposure.
These enhanced capabilities help reduce equipment degradation and prevent isolation failures, which can result in increased costs and delayed production because of the need for second or contingency trips into the well.
HPHT challenges
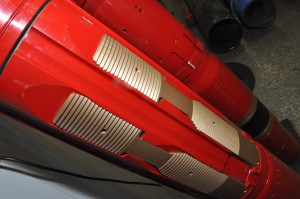
Last year Weatherford launched the IntegraLine high-performance liner system with swage technology. The system combines an advanced PBR, liner-top packer and liner hanger to operate beyond the limits of conventional equipment. It operates in extreme HPHT reservoirs with conditions up to 400°F (204°C) and 15,000 psi (86.2 MPa). For cases that require continual pressure integrity from the surface to the bottom of the well, a tieback seal stem is available.
Although applicable to any well type, the liner system is especially suited for mitigating risks in difficult, high-cost environments. The liner system components are interchangeable and are available in multiple casing sizes, including 7 in., 9 5/8-in. and 13 3/8-in. The system can be installed and configured to meet specific performance needs and to accommodate a variety of well designs and subsequent design changes that can occur because of unplanned events during the drilling process. The system integrates with the full suite of Weatherford well completion tools.
Dependable setting
As the anchor supporting the weight of the liner casing, the hydraulically set extreme liner hanger can hold loads that exceed 1 million lb (453,592 kg) in wells with challenging deviations and buckling. In these scenarios, the applied pressure is converted to a mechanical force that sets the hanger slips into the parent casing, which reduces the requirements for downhole reciprocation. The hanger has a bearing that enables rotation of the liner after the liner is set and during cementing operations to improve cement bond quality. High-durability seals expand the functionality and reliability of the hanger in environments with extreme bottomhole conditions, including H2S, CO2 and 400°F temperatures.
Seals for isolation
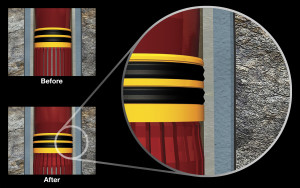
A key element of the liner-hanger assembly is the HPHT liner-top packer, which provides an immediate point of isolation between the reservoir and the wellbore. Engineered for reliability, the packer forms a seal that holds for the life of the well, even in fully cemented operations. Hold-down slips and an integral body lock ring system anchor the packer to the parent casing to ensure the packer remains set. The packing element incorporates a metal seal carrier that expands outward into the parent casing using a cone. The result is a robust seal highly resistant to H2S and temperatures above 400°F.
As a permanent barrier between the liner outside diameter (OD) and the host-casing inside diameter (ID), the packer seal prevents gas migration and isolates annular pressures. It also offers less susceptibility to swabbing-off than conventional, all-elastomer seals when running in the hole or circulating at high flow rates during well cleanup or cementing. For cemented liner applications, a packer assembly without hold-down slips provides a streamlined design option.
Protection and backoff protection
The system has a PBR engineered to withstand burst and collapse effects when tied back to surface. The PBR provides the extension needed for setting the liner-top packer. It also protects the running tool assembly as it is run in the hole. The honed ID provides a smooth surface for sealing. The PBR features a chamfered upper end and a threaded lower end, which makes up to a threaded connection with O-ring seals on the packer to form a hydrostatically locked space that prevents back-off during liner rotation.
In wells that require liner casing extending to the surface, or tied back, a seal stem stabs into the PBR to provide greater pressure integrity. After the liner is set, the seal stem is run and then connected up with the production tubing or drill pipe. The seals slide into the liner where the PBR is located to provide isolation for continual pressure integrity all the way from the surface down to the bottom of the well. Today, an estimated 20% of liners are tied back to the surface.
Zonal isolation application to TD
In unconventional plays, effective and reliable liner systems are essential to the safe execution of high-pressure hydraulic fracturing operations in long and deviated wellbores. For example, a major operator in an unconventional play in Alberta, Canada, installed the Weatherford liner system for an extended-reach gas and condensate production well with potential bottomhole pressures during stimulation between 10,000 and 12,000 psi (68,948 to 82,737 MPa) and temperatures as high as 300°F (149°C). The project marked the first time the SwageSet HPHT liner-top packer was run and set in an onshore well to provide zonal isolation.
The objectives consisted of safely reaching total depth (TD), cementing the 4 1/2-in., 15.1-lb/ft liner and effectively isolating the liner top in 7-in., 35-lb/ft casing. The operational team used a reamer shoe to prepare the wellbore for installing the liner system, which included the PBR, the 4 1/2-in. packer, a hydraulic rotating extreme liner hanger and a landing collar.
The team ran a 5,905-ft (1,800-m) liner to a depth of 15,419 ft (4,700 m), with the top of the liner set at 9,514 ft (2,900 m). Then the team pumped a setting ball to set the hanger with 2,610 psi (17,995 MPa) and shear the hydraulic lock on the running tools. The team used right-hand rotation to release the running tools and a wiper plug to execute cementing operations. The running tools were later retrieved with no issues.
Applying 65,000 lb (29,484 kg) of weight to the PBR activated the packer. After the set-down weight was transferred, the hold-down slips and the element were set. This process directed the total available setting force to the element to retain the force within the element and body-lock rings. The high-torque connection between the PBR and the packer eliminated any PBR back-off while rotating during drill-down operations.
Designed to contain the treatment pressure below the liner top during hydraulic fracturing and acid stimulation operations, the packer provided good zonal isolation and a high-integrity seal from the shoe to the liner top for the planned stimulation and production procedures. No safety or environmental issues were encountered during the installation.
In this case, the operator also ran a frac string to provide a continual tieback back to the surface while transmitting pressure downhole to enable hydraulic fracturing after setting the liner. A tieback seal stem sealed inside the PBR ensured robust liner setting that withstood the actual bottomhole temperature of 275°F (135°C) and the calculated bottomhole pressure of 8,288 psi (57,144 MPa). An enhanced tieback seal stem that meets the same HPHT ratings as the other system components is in development for release later this year.
The high-performance system, including the PBR, hanger, packer and related equipment, reached TD without incurring any nonproductive time. The operations to run the liner in the hole, set the packer, pump the cement and retrieve the running tools lasted approximately 42 hrs. The integrated system delivered an efficient, reliable, and safe solution that met all the operational objectives.
IntegraLine is a trademark of Weatherford.