Multilaterals yield additional production from existing wellbores
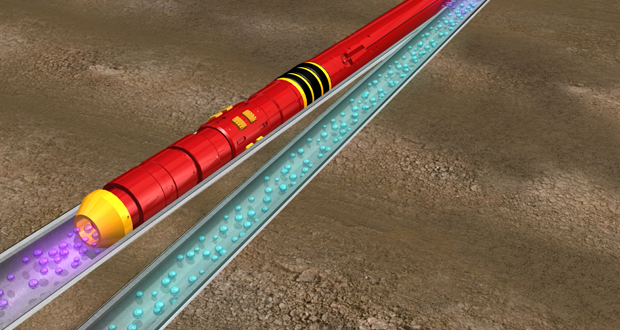
Gulf of Thailand case study: Multilateral system expands reservoir access from slot-limited platform
By Cliff Hogg , Weatherford; Stephane Huiban and Andy Timms, Salamander Energy
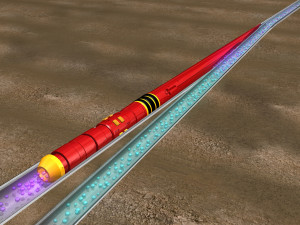
As the price of oil and budgets both continue to fall, the ability to quickly and efficiently increase reserves and production capability at minimal cost becomes an even greater priority for operators around the globe. This isn’t always an easy feat, especially offshore where slot limitations and higher development costs can impede development of marginal behind-pipe prospects.
Since the mid-1990s, multilaterals have been used to access reservoirs more economically, and higher-cost offshore developments have often provided the most fertile ground for multilateral installations. Eliminating the need for additional wellheads and surface facilities, eliminating the cost of drilling and casing a new hole from surface, and adding production without sacrificing production from an existing reservoir are all powerful incentives for a multilateral solution. The use of multilaterals, however, has not been widespread because of the perceived increase in wellbore construction risk resulting from the introduction of new multilateral components and installation procedures.
This was certainly true with earlier generations of multilateral systems, but more recent fit-for-purpose options have been introduced that minimize both installation and mobilization time requirements while providing the benefits of a multilateral well. In 2014, British-based and Asia-focused Salamander Energy initiated a multiwell multilateral program in its Bualuang oilfield in the Gulf of Thailand. The experience from Salamander Energy’s first multilateral program was positive: Four multilateral installations were successfully installed on Salamander’s Bravo platform during the second half of 2014.
Bualuang field and bravo platform
Primary production from the Bualuang Field comes from a Miocene high-porosity, high-permeability sandstone reservoir energized by a strong bottom water drive. First production from the Bualuang in 2008 was limited by the presence of a single, 10-slot wellhead platform. In 2012, a second 16-slot platform, Bravo, was installed to more rapidly access existing reserves. However, by the beginning of 2014, all 16 slots on the platform had been used. Rather than investing in a third platform, Salamander decided to install multilaterals in multiple wells on the Bravo Platform as a cost savings measure. This allowed the company to gain more production from the reservoir without sacrificing production from existing producing wells.

Among Salamander’s requirements for the multilateral system were:
• Low-risk installation to reduce risk to existing production from the main bore;
• Ability to install the multilateral in a high-inclination/horizontal position, to stay in the top portion of the reservoir to avoid water coning issues;
• A TAML Level 4 cemented junction to provide the ability to kick off the lateral in soft, sandstone formation without risking hole collapse;
• Compatibility with rotary steerable and PDC bit drilling programs used in the lateral drilling program;
• Full isolation of the existing main-bore reservoir during drilling and completion of the lateral leg;
• Full-bore access into the lateral bore to drill out the lateral shoe and drill into the target zone; and
• Ability to run screens through the junction without damage.
In addition to these technical requirements, Salamander required a system – both equipment and specialist personnel – that could be rapidly mobilized to meet the timelines necessitated by the end-of-contract date for the drilling rig.
Salamander selected Weatherford’s OneTrip StarBurst Multilateral System, which uses a hollow whipstock assembly as the platform to mill a casing window using QuickCut milling technology and procedures. The 2° angle of the concave ensures a longer window length and full compatibility with rotary steerable drilling systems. Once the window has been milled and the lateral wellbore has been drilled, standard casing is run in the lateral bore and tied back into the main-bore casing above the junction point. The casing is then cemented to provide maximum mechanical support. After the lateral wellbore has been constructed and the formation has been stimulated as desired, perforating charges are used to perforate through both the lateral liner and the hollow whipstock assembly to regain production from the main bore of the well.
Installing multilaterals

After the decision to initiate a seven-well project using the OneTrip StarBurst Multilateral System, mobilization of necessary equipment and personnel began in spring 2014, and the first well installation was planned for late May. With minimal specialized equipment required for the actual window milling portion of the job, equipment was quickly brought in from other locations in the region. Bringing in the needed perforating charges proved more problematic, however, because political and government conditions in Thailand at the time prevented the movement of most explosive products. As a result of this delay, the first multilateral well installation began in early August 2014.
After pulling the existing completion and completing a wellbore preparation run, the packer, hollow whipstock and window milling assembly were made up and run in a single trip. The packer was then hydraulically set in 9 5/8-in., 43.5-lb/ft casing at a measured depth of 1,387 m, where the wellbore presented an approximate 73° inclination.
Prior to setting the packer, a standard MWD system was used to determine and alter the orientation of the whipstock assembly. On this particular well, the whipstock was oriented at 15° right of the well high side after it was determined that such orientation would provide an optimum drilling path and departure for the planned lateral bore. Once wellbore fluid had been circulated over to a 9.2-lb/gal mud, the milling assembly was sheared from the whipstock and the entire window, including 5 m of rathole, was milled in approximately 4.5 hrs.
Approximately 1,300 m of 8 ½-in. hole were drilled, using a rotary steerable system in conjunction with MWD and LWD systems. A 7-in. liner was then run, hung back in the main bore and cemented in place. The 7-in. shoe was then drilled out, and approximately 800 m of 6 1/8-in. hole were drilled into the reservoir, again using geosteering. This lateral reservoir was then completed with 4 ½-in. stand-alone screens.
Regaining access to the mainbore
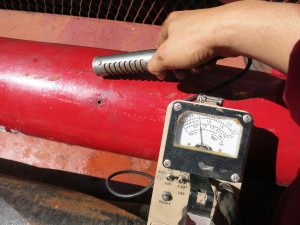
With the lateral bore completed and producing, operations were initiated to regain main bore production access by perforating through the 7-in. liner and hollow whipstock. A perforating gun with 9 ft of charges at 4 shots/ft and aligned along a single axis line was run downhole. The perforating charges had been specifically developed for the OneTrip StarBurst hollow concave system to provide short penetration lengths, maximum hole size and minimum debris compared with typical perforating charges that seek long penetration depths. The perforation gun was run below an MWD system to orient it so that the charges would face toward and penetrate into the open pocket of the hollow whipstock. The MWD assembly also provided the gamma ray logging necessary to identify the radioactive tags run at the top and at the bottom of the whipstock face to confirm proper setting depth of the perforating gun.
With the radioactive tags confirming proper setting depth, the guns were oriented in the direction of the hollow concave, and the assembly was pressured up to fire the guns. Pressure immediately dropped 40 psi, and losses of 450 bbl/hr were recorded, which confirmed that access to the main bore had been achieved. After the perforating assembly was retrieved from the well, an electric submersible pump was run and set just above the junction to provide commingled production from both wellbores to surface.
Creating multilaterals in remaining target wells
During the next two months, a OneTrip StarBurst Multilateral System was installed in each of three additional existing wells, at measured depths of between 944 and 1,000 m and at well inclinations between 53° and 62° at the junction depth. In all three installations, the hollow concaves were set without difficulty in the 9 5/8-in. casing, and the casing exits and rathole were milled in single trips in less than 7 hrs. Similar lateral completions combining cemented 7-in. intermediate casing and 4 ½-in. screens in the production zone were used in all three remaining wells.

Finally, in two of the remaining three wells, the concaves were located and perforated without difficulty, and successful access into the main bore was confirmed by a change in fluid losses after perforating. On the final multilateral of the project, a malfunctioning firing pin cartridge resulted in an extra tubing trip to perforate back into the main bore. The second perforating run was a success, and although fluid losses weren’t initially seen, a follow-up 200-psi injection test and resulting pressure drop verified the desired communication with the main bore.
In all four multilateral installations, production rates will be monitored over the coming months to determine the level of reservoir/production benefit achieved with these installations.
Lessons learned
Although the multilateral project was restricted to four installations rather than the original seven planned wellbores – because of contractual obligations of the drilling rig and the late start of the first installation – the overall project was a success and demonstrated the capability to convert existing wellbores into multilaterals quickly and with low risk. As a result, the operator will consider additional multilateral installations in the future.
Although the casing exit components of the OneTrip StarBurst Multilateral System were rapidly mobilized in Thailand, the delays caused by the inability to import the perforating charges into the country demonstrate the need to consider regulatory rules and political impacts when forecasting project times.
OneTrip StarBurst and QuickCut are trademarks of Weatherford.