Multistage stimulation: One size doesn’t fit all
Advances in plug-and-perf, fluid design, proppant placement, CT systems fill diverse needs of unconventional reservoirs
By Katie Mazerov, contributing editor

All the world’s a stage, except when it comes to unconventionals. This is a world of many stages, upwards of 50 in some regions, where fast-developing technologies, innovative fluid designs and proppant transport methods, and sophisticated reservoir characterization tools are unlocking complex formations. Just over a decade ago, these resources were inaccessible. However, as industry pushes forward in these formations, advances in multistage stimulation have become front and center in optimizing recovery and maximizing well economics.
Multistage stimulation, the practice of stimulating and fracturing multiple stages in a single well, was introduced in the US, where operators first combined horizontal drilling and hydraulic fracturing to launch the shale revolution. Over the years, there have been many technological developments to improve the process. However, one of the biggest step-changes grew out of the realization that one size does not fit all when it comes to shales. While all unconventional basins are completed using multistage hydraulic fracturing, each basin has its own, unique characteristics, with tremendous heterogeneity in the reservoir itself.
“As recently as five years ago, the thinking was that we could transport technology from one formation to another and bring in pumps to supply the horsepower,” said Brad Holms, Technical Advisor for FTS International (FTSI), a provider of hydraulic fracturing services, including pressure pumping and wireline. “Now, we know that each and every one of these rocks and reservoirs is unique and requires different approaches based on permeability and the effect of secondary fractures. That means we need to customize every fluid, every design and every fracture to get the most out of the reservoir to achieve economic success. There is no silver bullet.”
In fact, there is a multitude of tools and methods, among them new plug-and-perf technologies, advanced ball-drop methods, coiled-tubing stimulation systems, environmentally safe fluid designs and ways to optimize proppant placement that can be customized to maximize recovery. As North American operators drill longer laterals, with increased stage counts, and design intensified pad drilling campaigns, technology is keeping pace. It’s also expected to enable unconventional development in markets outside North America that are currently occurring at a much slower pace.
“Technological development of multistage completions and techniques is extremely rapid,” said Aaron Burton, Product Line Manager, Unconventional Multistage Completions, for Baker Hughes. “The primary driver behind development has been improving efficiencies and capabilities. Increasing the number of stages and injection points of fracture treatment, and spacing them closely enough to ensure the entire reservoir is contacted, is the most common tactic used today. However, we are seeing experimentation with engineering the fracture plan instead of blanket-fracturing. The objective is no longer simply increasing the capabilities but strategically placing the stages along the lateral to improve economics. Most studies indicate the average recovery rate for an unconventional well is only about 5%, so there is a lot of room for improvement.”
Expanding plug-and-perf market
Baker Hughes recently introduced the large-bore SHADOW Frac Plug for unconventional multistage plays. The plug features a large flow-through internal diameter (ID) and is used in conjunction with the company’s IN-Tallic disintegrating frac balls. Production flows through the enlarged ID, and the ball disintegrates in well fluids, eliminating the need for milling after the frac job.
The technology is opening a new plug-and-perf market for extended-lateral plays, such as the Bakken, where it is difficult to mill out plugs with coiled tubing (CT) in 10,000-ft laterals. Longer-lateral wells are often completed with the FracPoint ball-activated completion system because there is no through-tubing intervention required during or after the frac job, Mr Burton said.
The SHADOW plug provides the same isolation functionality as a composite bridge plug but is designed to stay in the wellbore indefinitely during production, eliminating the need for mill-outs after the fracture operation and shortening completion time. “This gives plug-and-perf access to wells with longer laterals. We can now run these plugs toward the toe of the well, where it is difficult to mill out plugs, and use standard frac plugs at shallower depths where CT operations are more feasible,” he explained.

The plug adds value in shorter-lateral wells, common in the Eagle Ford and Permian Basin, by avoiding plug mill-out and putting production online faster. The plug also has been designed to be milled out at a later date, if necessary. Earlier this year, the system was deployed in two wells on a seven-well pad in Canada’s Horn River Basin, allowing production to begin immediately after fracturing operations, eliminating the need for a post-frac intervention and saving the operator $300,000. The operator is now using the plugs throughout its entire completion plan, according to Baker Hughes.
In some of the Canadian unconventional markets, where the economics are tighter, CT-style completions have been used for greater cost-efficiency, with lower fracture rates and faster turnaround times, said Luis Castro, Product Line Manager, OptiPort Multistage Fracturing System for Baker Hughes. “In the US, with a greater number of prolific oil and liquids-rich plays, the economics are better, and operators have been able to afford the extra two to three days per well with plug-and-perf methods.”
The OptiPort sysem replaces the plug-and-perf design with a CT bottomhole assembly that hydraulically opens multiple pressure-balanced full-drift sleeves for stimulating an unlimited number of stages. The system, which has been used in Canada’s Viking and Bakken formations, is being applied in various US plays. It optimizes placement of proppant and frac fluid by stimulating one injection point instead of stimulating four or five perforation clusters at the same time over a 250-300-ft stage, Mr Castro explained.
“This ensures that each injection point or cluster can be fractured to its maximum potential, instead of allowing nature to take the fracture along the path of least resistance,” he said. By using CT, the system also reduces the impact of screen-outs. Circulating down the CT already in place enables the system to rapidly clean out the wellbore. An onboard sand jet perforator allows frac stages to be added on the fly. “By already having CT in the hole, we can save significant cost and time,” he noted.

In a 2013 analysis in the Granite Wash play, an operator compared results of the OptiPort system with a conventional plug-and-perf methodology in gas wells with similar reservoir and rock properties, expected ultimate recovery and estimated production rates. Both wells were drilled to approximately 12,000-ft total vertical depth and 18,000-ft measured depth through similar formations and target zones and were fractured using the same stimulation fluid and proppant volumes. The plug-and-perf configuration had 10 stages with three cluster per stage and a cluster spacing of 165 ft. The other well had 30 OptiPort sleeves set every 164 ft.
Although both wells had a total of 30 injection points, the OptiPort system reduced the hydraulic horsepower by 68%, compared with the plug-and-perf operation, by lowering fracturing rates by 60% since a single injection point was used. After producing for 90 days, the OptiPort well was outperforming the plug-and-perf well by 61% in cumulative production.
Million-dollar question
Lateral length often dictates the number of stimulation stages. However, as operators look for the optimum stage count that will maximize recovery, more is not necessarily better, said Isaac Aviles, Global Portfolio Manager, Multistage Stimulation for Schlumberger. Nor is it simply about the hardware technology. “More than horsepower, more than the tools in the ground, it is the integration of good, solid technology combined with reservoir understanding that provides the highest value to customers,” he said. “Understanding the capacity of the reservoir, knowing where to place the fractures, correctly using the appropriate tools and knowing what to do after the stimulation treatment is an integrated process that maximizes value.”
The Schlumberger Mangrove engineered stimulation design in the Petrel platform software provides insight into the geological, geomechanical and seismic characteristics of the reservoir. “Pad drilling is gaining more acceptance even in the more traditional areas like the Permian Basin. Mangrove uses the INTERSECT high-resolution reservoir simulator Schlumberger developed with Chevron and Total to explicitly simulate single-well performance,” said David Sobernheim, North American Stimulation Domain Manager for Schlumberger.
“The single-well model is then plugged into multiwell field development planning models to help operators decide the number of laterals, and where to place the laterals, off the pad in large-acreage plays. For operators, that is literally the million-dollar question.”

Mangrove also enables operators to make better decisions in designing stimulations and completions, which vary among the unconventional plays. Nevertheless, in many cases, how the individual markets developed and the methods that were successful when a particular play was first produced influence the type of completion, Mr Aviles noted. For example, in gas plays such as the Marcellus and Barnett, cemented completions using plug-and-perf techniques are still the norm. In the Bakken, where laterals are being drilled 10,000 ft out, open-hole designs with a large number of stages can be completed very quickly, moving from fracture to fracture by simply dropping a ball.
With improved plug-and-perf technologies, that trend may be changing. “In the Bakken, for example, plug-and-perf techniques in both cemented and un-cemented applications continue to gain market share,” Mr Aviles said. “Initial benefits made possible using ball-drop systems have largely been offset by the operational efficiencies developed in plug-and-perf operations in combination with technologies, such as Broadband Sequence, to enhance the production of perforation clusters.”
Schlumberger in February introduced the BroadBand Sequence fracturing technique, a plug-and-perf fracturing method that improves production by enabling sequential stimulation of perforated clusters or open-hole intervals. A combination of degradable particles and fibers goes into the entrance of the perforation/fracture, locks the fluid into that particular section and then, as pressure increases, diverts the treatment to another section.
“This technique also can increase the ratio of clusters per plug, allowing operators to take bigger slices from the horizontal section at one time,” he added. “We are able to be more efficient and divert within a particular set of clusters. This solves the well-known problem of conventional plug-and-perf operations, where only about 60% of the clusters are stimulated or contribute to production.”

Initially developed for the North American land market, BroadBand Sequence has been particularly successful in the Eagle Ford play, according to Schlumberger. In that region, Marathon Oil Company used the technology to increase oil production by 21% over a 115-day period, compared with conventional plug-and-perf methods. In one well, BroadBand Sequence split the stimulation treatment for each interval into two stages separated by a pill of composite fluid. “This feature improves fracturing distribution, allowing us to ensure adequate stimulation of each perforation cluster and reduce over-flush effects common in plug-and-perf completions,” Mr Sobernheim said.
Ramping up R&D
“Coming back to the Bakken, tools used to enhance operational efficiency of ball-drop systems include the Schlumberger ELEMENTAL degradable alloy,” Mr Aviles said. “This innovative material offers steel-like strength but dissolves in a matter of hours or days when exposed to water and temperature. The alloy is used for various applications, including the Falcon multistage stimulation system, which uses degradable balls to activate individual stages. Operators use ELEMENTAL fracturing balls to eliminate the need for a costly mill-out operation after the fracturing treatment is complete, as there is no risk of balls becoming stuck downhole, compromising the well’s production.”
As the US unconventional market continues to grow, with operators ramping up activity in newly discovered plays, service companies have followed suit with ongoing research and development efforts. In 2013, FTSI opened a corporate technology center in Houston to focus on developing more effective fracture designs, new fluids,

proppant transport systems and customized solutions for specific reservoir requirements in the US unconventional market. “We now understand that a lot of hydrocarbons are being left behind, so we’re developing tools and methodologies to improve recovery,” Mr Holms, Technical Advisor for the company, said.
R&D efforts at the center are targeting reservoir understanding and ways of better designing and optimizing completions to enhance economics for customers, explained Mahmoud Asadi, Senior Vice President, Technology for FTSI. “These reservoirs are so much more complex than we originally thought and need to be produced with technically unique solutions, not just brute force. The longer the laterals, with 55 or more stages in some cases, the more complicated each stage is in terms of spacing and reservoir variability. As this brings a whole new level of economics into play, we are continually customizing methodologies for our customers.”
FTSI has developed a new stimulation methodology for delivering fluids with the optimum volume, viscosity and velocity (V3) based on the mineralogy and rock properties of the reservoir. The V3 system was deployed earlier this year in a highly fractured reservoir in Texas, where the operator was experiencing lower comparable results than another operator in a nearby offset, using the same stimulation and completion methods. Early results indicate the system has been effective in increasing initial production rates and slowing production decline, according to FTSI.
The company’s NPD Nanotechnology Solutions platform adds a solution to hydraulic fracturing fluid to accelerate the recovery of hydrocarbons by displacing fluids and solids, such as paraffin, from the formation, or from the proppant pack or downhole equipment, improving the oil/water cut, Dr Asadi explained. The technology increased production in some wells FTSI completed during 2012 and 2013 from 3% to 12% in the Mississippi Lime and from 12% to 65% in West Texas.
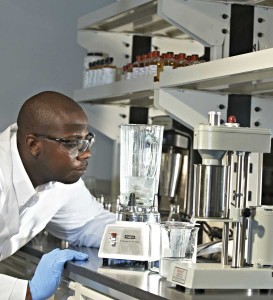
The Aquacor Real-Time Bacteria Detection service, introduced by FTSI in late 2013, analyzes samples in 24 hours to determine more precisely which biocides should be added to the fracture to remove and prevent further growth of bacteria in the well. “The conventional method takes about 28 days to identify bacteria and determine which biocide to apply,” Dr Asadi said. “In that time, we will have already completed the fracture. By applying the correct biocide earlier, we can reduce costly and time-consuming repairs to equipment that might be damaged by bacteria.”
Equally important as cost and reliability of new technologies is environmental safety, Dr Asadi noted. “Products have become more environmentally conscious and, at the same time, they are performing as well, if not better, than what they are replacing and can be more cost-effective.”
One of FTSI’s newest fracture fluid transport systems, Diamond Fracturing Fluid, replaces guar, commonly used in gel-based fluid systems. The fluid uses a polymer that contains biodegradable and naturally derived components that produce less gel residue than guar and can be used in crosslinked fracturing designs in temperatures up to 250°F. “This fracturing fluid system can be more cost-effective and delivers more viscosity and better clean-up than a guar-based solution,” Dr Asadi said. “It also provides greater stability to temperature and dissolved solids.”
New transport system

Proppant manufacturer Santrol, a Fairmount Minerals company, is field-testing a proppant transport technology that extends the fracture length.
Propel SSP transport technology was developed as an alternative to conventional frac fluid transport systems, such as slickwater and high-viscosity gels. “Instead of pumping gel and blending it with sand, our new technology treats sand, or any proppant, with a polymer that attaches to the proppant itself,” explained Brian Goldstein, Product Director, Propel SSP Proppant Transport Technology.
When the coating is blended with water at the job site, it expands to 300% of its original size and hydrates around each individual grain of proppant. This gives the proppant near-neutral buoyancy, or suspension, so it can float through the water at a much lower viscosity than with slickwater, but with the carrying capacity of a crosslinked gel system, to increase the fracture surface area. “By transporting the proppant farther out into the fracture, we are able to place it where desired and produce hydrocarbons at higher recovery rates than currently observed by operators,” Mr Goldstein said.
Unlike gel, which has properties that that can damage the formation, the polymer coating cleans up easily in the formation and leaves little or no residue, while enhancing production from the targeted fractures, he added. “The growth of multistage hydraulic fracturing of US land-based wells is driven by the opportunity to improve efficiency. This proppant transport technology is delivering value for customers by maximizing production in ways that are efficient with less chemical handling on the surface.”
The new proppant category, which is being tested in several US shale plays, is expected to be commercially available later this year.
With the growing trend to drill longer laterals with higher stage counts, Santrol in the last year nearly doubled the number of proppant distribution terminals, with more than 50 now located throughout the US and Canada in all the major shale plays. “We’ve found it is important to have multiple terminals within basins so customers can pick up proppant as close to the wellhead as possible and limit transportation and other logistical delivery challenges,” said Nick Johnson, Vice President, Marketing for Santrol.

The type of proppant is defined by the basin, specifically depths, hydrocarbons, the fluid system being used and closure stress of the formation. “In the Bakken, where wells are typically deep, with closure stress above 6,000 psi, a stronger pre-cured, resin-coated proppant reduces fines that could be generated if a proppant crushes. This results in better short-term and long-term production,” Mr Johnson said. “For relatively shallow wells, seen in the Permian Basin, the lower closure stress increases the chance for proppant flowback. In this case, a curable resin-coated proppant bonds the grains together to keep the proppant pack locked in the formation to improve hydrocarbon production.”
SHADOW, IN-Tallic, FracPoint and OptiPort are trademarked terms of Baker Hughes. Mangrove, Petrel, INTRESECT, BroadBand Sequence, ELEMENTAL and Falcon are marks of Schlumberger. The INTERSECT simulator is a joint product collaboration of Chevron, Total and Schlumberger. NPD and Aquacor are registered terms of FTS International; Diamond is a trademarked term of FTS International. Propel SSP is trademarked term of Santrol.