DEA 164: What does a next-gen ranging MWD look like?
Also, your tax dollars at work: Using USA’s 17 national labs to advance drilling tech
Staff reports
The Drilling Engineering Association (DEA) continues to serve the industry as a key forum for learning about cutting-edge technologies and for forging alliances through joint ventures to solve industry’s pressing technical challenges.
Updates about DEA projects and presentations on cutting-edge technologies were presented during the DEA Technology Forum, held during March and sponsored by Weatherford in Houston. DEA’s next Technology Forum will be sponsored by Halliburton on 27 September at the company’s North Houston location.
Next-gen ranging MWD
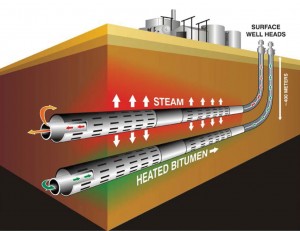
Currently, DEA members are engaged in project DEA-164, “Next-Generation Directional MWD Tool Requirements for Improving Safety and Accuracy.” Sponsored by ConocoPhillips and Baker Hughes, the project has gained numerous contributing participants, including Maersk Oil, Apache Corp, ATK Missile Products, National Oilwell Varco, Weatherford and Bench Tree.
A final report available to participants is planned for release in March 2013. A public report will be issued in September 2014.
“There are a lot of applications where you need ranging in high-angle and distorted magnetic fields,” said Son Pham of ConocoPhillips. “(Magnetic ranging) technology is fairly old.”
A next-generation MWD tool will be very useful for drilling in mature, congested fields, such as in the UK and Norwegian North Sea and on US land.
Other applications include drilling in distorted magnetic fields, high angles and interceptions, and will aid in determining absolute and relative positions quickly and accurately, as well as improve safety, he said.
Another application is “twinning” wells for steam-assisted gravity drainage (SAGD), where steam is injected into one wellbore to liquefy bitumen for it to flow up a parallel wellbore. In Canada, Mr Pham said, offsets between the two wellbores can be less than 5 meters.
The purpose of the project is to assess requirements for such well applications and report on available technologies for ranging to adjacent casing – range, accuracy, power, environmental, patent restrictions. In addition, the project will assess market willingness to pay daily rates for additional safety and readiness in everyday MWD tools. Formation evaluation is specifically excluded.
The principal investigators retained are Gordon Richardson, TechRich Consulting, and Robert L. Waters, R.L. Waters Consulting, both of whom have significant experience in this area.
Messrs Richardson and Waters will gather data from operators to define requirements and specifications, as well as to:
• Assess price tolerance for next-generation MWD service for multiple applications;
• Assess technical requirements and gaps;
• Assess IP barriers for key technologies;
• Determine whether multiple service suppliers can develop the solution; and
• Recommend a path forward for industry.
The consultants will conduct a series of face-to-face interviews with key managers and drilling engineers in operators’ drilling departments and service companies.
The project is budgeted at US $350,000 but may be increased with JIP participant approval to $490,000. Costs will be shared equally among the participants.
For information about participating, contact Robert Estes at robert.estes
@bakerhughes.com.
Tapping a US brain trust
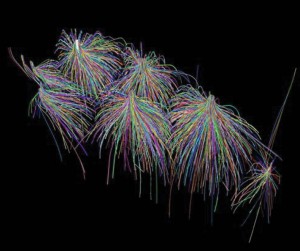
The USA boasts 17 national laboratories across the country, organized initially for a plethora of purposes – some notably to develop nuclear weapons technology.
A “peace dividend” since the warming of the Cold War has been the reinvention of these labs in search of new missions and, frankly, their institutional survival.
Chevron has moved to take advantage of this enormous expertise, attendees at the March DEA Technology Forum learned.
“These labs are conducting extraordinary leading-edge work, some of which can be converted to oilfield use,” remarked DEA chairman Ben Bloys, manager – Chevron/Los Alamos Technology Alliance.
The labs specialize in a huge array of technologies, Mr Bloys reported, including advanced sensors, nanotechnology, material science, cyber security, superconductors, alternative energy, extreme microscopy, robotics, geophysics, HPHT electronics and more.
“It’s not just physics,” Mr Bloys said. “It’s everything.”
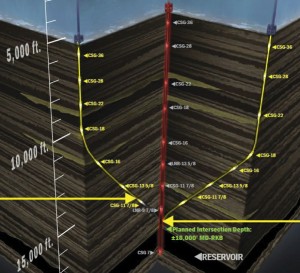
Each of the labs has a technology transfer department, and they all have been mandated to realize additional uses from unclassified research, Mr Bloys said.
In December, 2011, US Deputy Secretary of Energy Daniel Poneman announced the Agreement for Commercializing Technololgy (ACT), described as a pilot technology transfer mechanism. ACT was designed, according to DOE, to address concerns preventing private firms from working with national labs to bring new technologies to market.
Getting started
Mr Bloys offered the benefit of Chevron’s experience. First, he said, study the labs on their websites. Each has its own site. “This will give you a taste of what’s available,” he said.
When you’ve identified a lab conducting work that might have application for you, contact the lab’s technology transfer department. Present them with a problem.
“They’ll come back with a dozen ideas that would never have occurred to you,” he said.
Mr Bloys cautions, though, “These scientists don’t understand the oilfield at all … but they learn really, really fast.”
Be aware of some caveats. First, while the technologies are generally mature for their original purposes, it will require time and money to adapt them to the oilfield.
But that’s not all bad: “The odds of success with these things are pretty high, because we’re starting with a mature project.”
The oilfield is notoriously slow to develop and adopt new technologies. Numerous articles and workshops, many through Drilling Contractor and IADC, attest to this nagging problem.
Mr Bloys notes that it can take 17 years to develop new oilfield technologies. With the labs, though, “we’re at about a third of that.”
Also, contractual issues can take awhile. This is, after all, the government we’re talking about.
Tech transfer successes
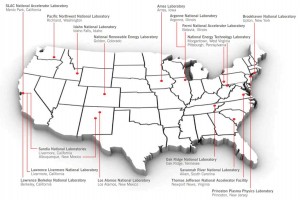
Mr Bloys pointed to a couple of success stories, starting with Inficomm. Now ready to go commercial, Inficomm provides pressure and temperature wirelessly and over high bandwidth (2 Mbps) from unpowered downhole sensors.
A key point in this project was early and aggressive field trials. “The relationship with the field people has been very helpful,” Mr Bloys said.
Inficomm produced multiple spinoffs, including TruDepth, which provides real-time data on the liquid level in wells, preventing pump burnout, increasing production and more.
SFAI (Swept Frequency Acoustic Interferometry) is another success, he said. It uses non-invasive sensors to characterize many physical and chemical aspects of the contents of pipelines and vessels. The first was to qualify oil/water two-phase flow without interference from the gas.
SFAI, now going commercial, is, Mr Bloys said, an advanced form of ultrasound but sweeps across a range of ultrasounds.
“Unlike some technologies … SFAI doesn’t really care how much gas you have in there,” he said
Closed-loop cementing
Is it time to introduce a managed-pressure cementing technology, particularly for offshore well construction? That’s a proposal set forth at the DEA Tech Forum by longtime MPD champion Don Hannegan, Weatherford. “Conventional cementing practices,” Mr Hannegan remarked, “are still conducted with an open-to-atmosphere annulus returns system. That doesn’t give us much ability to precisely measure and apply desired amounts of annulus backpressure during cementing sequences, where the ability to do so would be very advantageous.”
Most importantly, he added, industry lacks the ability to detect in real time an induced fracture during displacement.
Mr Hannegan noted that while closed-loop cementing is an extension of MPD root concepts, it could become a new technology in its own right. The MPD variation most applicable, he said, is constant bottomhole pressure.
He postulated that MPD, combined with frequent dynamic formation integrity testing (FIT), can greatly improve offshore cementing. In particular, he said, these techniques can facilitate:
• More stable wellbores, hole cleaning and pre-conditioning;
• More precise mud displacement and slurry placement;
• Real-time detection of an induced fracture;
• More precise pressure management during pre-set and curing;
• Ability to apply annulus backpressure to minimize channeling;
• Testing with MPD kit to reduce NPT;
• Provide additional documentation toward compliance with industry recommended practices for isolating potential flow zones during well construction and plug and abandonment.
Mr Hannegan told DC that dynamic FITs should be conducted as frequently as following every stand of pipe when in critical zones. The process is conducted with the rig pumps through the bit and while rotating the drill string. Surface backpressure is applied by the MPD system, eliminating the need to exercise the BOP. A dynamic FIT does not require interrupting the drilling progress, which encourages more frequent FITs than has been industry norm. Determining the pressure containment integrity of the wellbore with precise real-time measurements as the open hole is being drilled is an important precursor to optimizing casing-running speeds and contributes actual, not predicted, data inputs to cementing simulation models and conventional cementing calculations. “In short, closed-loop cementing increases the change of getting a critical offshore cementing job done right the first time,” he concluded.