A shake-up in solids control: Industry looks beyond tradition
Material is used with permission from National Oilwell Varco. Copyright © 2009 National Oilwell Varco, All Rights Reserved.
Automation, new shaker screens, rotating filter belt among innovations in fluids waste processing
By Katie Mazerov, contributing editor
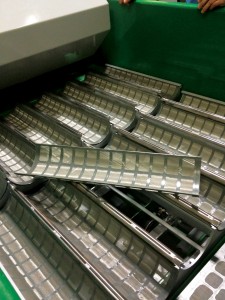
Remove all doubt from the drilling process. That mantra is one of the key drivers behind Jason Norman’s mission to streamline and – ultimately – automate solids control, waste management and drilling fluids processing. Since 2008, Mr Norman, senior fluids engineer at Apache Corp, has been engaged in a quest to find fluid-processing solutions beyond the conventional shale shaker designs and methods the industry has been using for the past century because, he said, “we, as an industry have not really attempted to do it any other way. Apache is doing just that, to see if we can make any incremental improvements to fluid handling and measurement systems.”
Important drivers in the development of new solids control technology include improved safety, lower overall well costs, improved drilling efficiency, reduced environmental impact and compliance with regulatory requirements that vary on a global scale. In association with Compatible Components Corp, a company specializing in fluid dynamics related to drilling fluid and on-site water recovery management, Apache is working to provide new options for drilling fluid separation and mixing products. Equipment repackaging is coupled with the latest technologies in fluid measurement instrumentation for potential future automation.
“We’ve resurrected a conventional shaker design, added instrumentation with a means of monitoring its efficiency and will be testing later this year,” Mr Norman said. The design, developed more than five years ago but never fully commercialized, is based on the concept of seven rows of cylindrical screens, each about half the size of a 2-liter soda bottle.
“It’s still a conventional shaker, but the screens can be pulled individually,” he explained. “Instead of changing out a $400 screen, we’ll be changing out a $40 screen.”
The design also includes elements of automation that will provide a way to measure density, particle size distribution, oil/water ratio, rheology and salinity, ensuring greater accuracy and removing people from the monitoring process.
“With our new instrumentation, we can precisely measure fluid properties going into and out of a wellbore; this allows us to quantify the efficiency of our mud system more accurately than conventional systems,” Mr Norman said. “If we can measure it, we can control it.”
Another concept being studied involves the use of the eductor, an orifice that creates energy. “We have been using the eductor for highly efficient mixing, tank agitation, automated mud mixing/pneumatic bulk handling, de-watering and oil-on-cuttings recovery,” Mr Norman said.
“From a solids removal and waste management perspective, the eductor is highly under-utilized in this industry, even though it has been used in other industries for 40 years.”
Last year, Apache tested a technology involving a combination of an air eductor and a highly efficient hydro-cyclone to process 22% oil-on-cuttings, and recovered nothing but dry cuttings. “The process was so efficient, it vaporized everything inside the vortex finder,” Mr Norman said, noting Apache will continue work on this technology to develop a means to recover the oil and water.
Changing the hierarchy
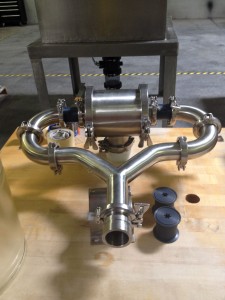
Mixer (two offset nozzles facing each other, commingling inside a chamber) in front of the centrifuge. The mixer helps break the bonds between the liquid and solids.
Underlying these efforts is a new way of thinking about the solids separation processing and measurement.
“Traditionally, shale shakers are the first line of fluid processing, followed by de-sanders, de-silters and then centrifuges,” Mr Norman explained. “We have developed some equipment around placing a highly efficient hydrocyclone as the first line of defense, followed by our shakers.
“With a reinvented nozzle/volute configuration to facilitate an improved vortex finder, removing solids is far more efficient than with conventional designs. We can remove large particles with the hydrocyclones, ultimately placing less stress on our shaker screens, increasing screen life and providing the opportunity to screen up to a much finer mesh. Using this methodology, we won’t be wearing out the screens as fast because they aren’t being exposed to highly abrasive drill cuttings.
“We’ve also learned that we can increase the efficiency of a centrifuge by placing a Chaos Mixer (two offset nozzles facing each other, commingling inside a chamber) in front of the centrifuge to create a powerful, violent mixer,” he continued. The Chaos Mixer has several centrifuge applications that include increasing the efficiency of the barite recovery , de-watering and polymer injection processes. The highly turbulent collision of fluids inside the mixer breaks the electrostatic bonds and allows for more effective solids separation.
“We also think this concept can be applied to recovering base oil from drilled cuttings.”
Another concept on the test shelf is the Spinning Strainer. Currently used in the mining industry, it is designed to process 500 gal/min through a 40-micron screen and has the ability to automatically sort and dump the drilled cuttings based on pressure differential measurement. A self-cleaning mechanism is built into this unit. “We are very excited about the results of our testing,” Mr Norman said.
“We are also developing an automated mud-mixing system using liquid eductors to pneumatically transfer bulk powders from the bulk bins to the mixing tank,” he added. “We can pull powder from each bulk bin on the skid or from any stand-alone storage silo or vacuum trailer.”
The eductor can be used with a vacuum hose to transfer lost-circulation material, such as cotton seed hulls, from the back of a dump truck. The eductor/vacuum hose also can be used as a spill clean-up device.
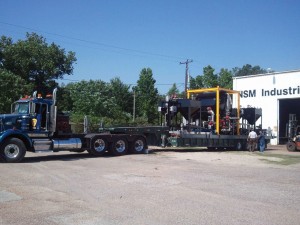
While Mr Norman said he foresees a time when shakers won’t be a part of the operation, for now they are still considered the primary method of solids control. Shale shaker advances have focused on greater screen capacity and higher g-forces to better respond to faster drilling. Shakers also have started to incorporate more screening decks in order to increase the screening capacity while maintaining the same overall footprint.
Avoiding a bottleneck
“If we’re removing 1,000 tons of solids over a one-month period now, and we have to remove the same amount over a 15-day period because drilling and rates of penetration are faster, the equipment will need to become more efficient in order to remove cuttings at the rate the rig is producing them,” said Federico Mezzatesta, director of product line management for National Oilwell Varco (NOV) Fluid Control. “Operators are looking to reduce nonproductive time and increase safety and drilling efficiency, and anything that slows down the process is creating a bottleneck that drives up costs.”
Among NOV’s technologies is the newly patented Constant-G Control, which automatically adjusts shaker g-force according to changing drilling conditions. “The g-force increases as loading on the basket increases, and decreases as the loading subsides,” Mr Mezzatesta explained. “This keeps the shaker operating at its optimum level and helps the customer maintain better control of drilled solids.”
In addition, a newly patented PXL (Premium X-tended Life) shaker screen has a cloth design that offers extended screen life while maintaining a more precise cut-point – the solid size the screen will remove. The cloth combination minimizes wire movement during operation and minimizes the risk of blinding to maintain good through-put, the amount of fluid the screen can handle.
“It’s a balancing act,” Mr Mezzatesta said. “With coarser screens, you get greater through-put, but you also allow more solids to return to your mud system. A greater percentage of solids in the mud system can require the drilling fluid to be diluted, which increases both drilling fluid and waste disposal costs. We’ve tried to design a screen with a cloth that, while in operation, does not lose its shape and allow unwanted particles to get through.”
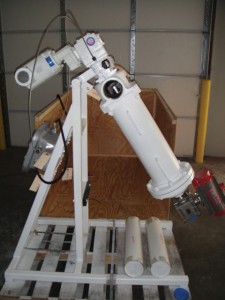
The type of drilling fluid used, as well as return fluid properties, will determine screen size and type and method of cuttings disposal. Oil-based drilling fluids provide greater lubricity than water-based drilling fluids (WBM), which can translate to faster ROP and reduced drilling time. “Non-aqueous fluids are also more inhibitive than WBM, meaning that cuttings are less likely to disintegrate within the fluid, which can assist with solids control,” Mr Mezzatesta said.
“On the other hand, the price of oil is pushing base oil costs up, and disposal regulations are becoming more stringent, so operators are starting to shift towards the use of alternative high-performance water-based systems, such as NOV’s POLYTRAXX, which perform similarly to non-aqueous fluids with lower overall costs and less environmental impact.” With the increase in drilling fluid costs, there is also increased pressure to optimize solids control equipment such as centrifuges, which are being examined more closely than in the past.
Regulations are typically stricter for non-aqueous fluids disposal, and they vary by region and state. For offshore operations, the Gulf of Mexico currently allows discharge of drill cuttings if there is less than 6.9% oil on the cuttings. In the North Sea, the UK sector allows discharge if oil on cuttings is 1% or less, while the Norwegian sector doesn’t allow any overboard discharge of cuttings.
“Through continued automation and optimization of rig equipment, as well as improved downhole telemetry, NOV is helping operators to meet or exceed regulatory requirements while minimizing their overall well costs,” Mr Mezzatesta said.
Avoiding vibration
While shaker designs continue to advance, other innovative methods are also emerging. The MudCube, a system designed by Norwegian company Cubility AS, is an alternative to shale shakers. “The MudCube is built on a unique principle that uses a revolving filter belt or screen rather than vibration to filter drilling fluid and can be monitored and controlled remotely,” said Asbjørn Kroken, vice president of engineering, and marketing and sales for Cubility.
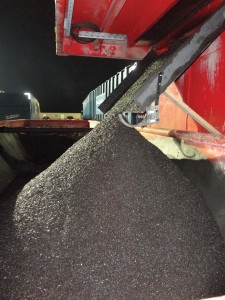
Commercially launched earlier this year, the MudCube was designated a proven technology by Statoil following an extensive verification test. Maersk Drilling Norge AS is currently installing the MudCube on the Mærsk Giant, an ultra-harsh environment jackup in the North Sea. The system was also tested in the Marcellus for onshore applications.
Further, Cubility has entered into a contract with Petrobras to test the MudCube at its test center in Norway.
The fully enclosed, lightweight system includes a web camera and uses a vacuum to pull the drilling fluid through the slowly rotating screen. On the back of the filter belt, an air knife (a hose with holes) blows air from the back side of the belt to keep it clean from sand or other particles. “There is always a clean screen to separate out the cuttings,” Mr Kroken said. The lack of vibration also eliminates noise pollution.
The theory behind the technology is that the use of a vacuum and revolving belt results in considerably less mud loss. “The system can more easily separate the finer materials, so the mud doesn’t have to be diluted as much,” Mr Kroken said. “There is less mud and therefore less waste or drilling fluid that must be transported and treated. The system can reduce waste by up to 50%.”
The cuttings, which are much drier than with a shaker, are deposited on the end of the machine for later transport to a storage facility. The 4 ½ ft by 8 ½ ft unit is roughly one-third the weight of a shaker. The filter screen weighs about 7 lbs.
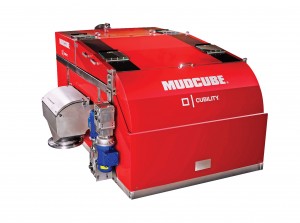
“The MudCube was initially targeted for the offshore sector because that is where the biggest challenges are due to larger volumes of mud and stricter regulations,” Mr Kroken said. “Onshore, there are also fewer issues with emissions and noise pollution.”
The system is proving beneficial in regions such as the North Sea, Gulf of Mexico and Brazil, where regulations mandate that waste from oil-based mud be transported onshore to a treatment facility, then stored in a landfill. With current rates, Cubility believes that one North Sea operator can potentially save nearly $3 million in transport costs