New bits look beyond design at overall wellbore
Advanced cutters, manufacturing methods, data analysis help extend bit life, performance
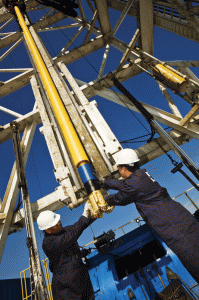
By Joanne Liou, editorial coordinator
In the wellbore, drill bits lead the way through formations to achieve longer wells more efficiently and quickly. The latest developments in drill bits share a common goal: optimize bit performance in the wellbore to save time and money. Coupling enhancements in bit design, material design and the manufacturing process, the results are consistently outperforming the previous generation. Baker Hughes, Halliburton, National Oilwell Varco (NOV), Smith Bits, Ulterra and Varel International capture some of their latest developments and improvements in drill bit technology.
Baker Hughes
Baker Hughes’ latest line of Hughes Christensen Talon PDC bits targets vertical, curve and lateral intervals with additional directional features, making it particularly suitable for the Rockies area. The bit has been launched in two basins in the Rockies, where the Talon 3D will be released by Q3 this year. The 3D version includes more directional features to make it more suitable for curve or directional drilling.
This line of bits offers application-specific cutters. “We drill in different basins in the US, with different drilling parameters, different rock in each area – we have application-specific cutters to pick from to optimize drilling performance,” Matt Zolnowsky, Baker Hughes drill bits performance engineer, said. “We are improving ROP and distance drilled… This is step-change technology that will save drilling time.”
The steel-body design features an increased junk-slot volume to improve hydraulic efficiency with a shorter bit-to-bend dimension to improve steerability and build-rate
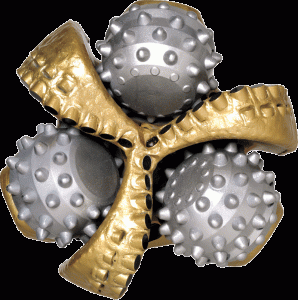
aggressiveness when necessary. Application-specific, polished cutters with superior bit body hardfacing “take these steel body bits to record footages at record ROPs,” Mr Zolnowsky said.
Data analysis is another major element of the new bit design. “We now have a very efficient way to look at foot- and time-based drilling data to help the operators optimize the drilling system,” Mr Zolnowsky explained. Data analysis reaches beyond the bit design and looks at the overall wellbore – the BHA, drill string and other operating parameters. “We hear varying stories from the rig and from the office regarding drilling performance, but looking at the actual data is the preferred source of information to optimize the system.”
In the Haynesville Shale in Bossier Parish, La., where horizontal lateral hole sections typically range between 4,000 ft and 5,000 ft, the Talon 3D 6 3/4- in. bit drilled an entire lateral section in one run and decreased section drilling time by 36 hrs earlier this year. The bit increased single-run footage by 53% and saved the operator more than $80,000 for the section. The new bit offered directional control, as well as increased junk slot area for enhanced hydraulic efficiency.
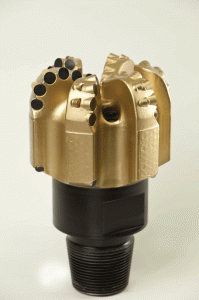
Combining the strengths of roller cones and PDC fixed cutters into a single bit, Baker Hughes recently expanded its range of offerings for the Hughes Christensen Kymera hybrid bits from 8 ½ in. to 28 in., following successes with the 12 ½-in. Spanning 16 countries with more than 385 completed runs, the bit targets hard, interbedded formations, Alan Holliday, product manager, explained. “On the design side, Kymera has become a combination of the fast-moving action of the PDC combined with the smooth roll action of the TCI,” he said.
The bit is used to troubleshoot wells where operators struggle with specific issues. “There’s a dysfunction in the hole for us to be running a hybrid – either the problem is high vibration or stick-slip, hard-interbedded formation or toolface control,” Mr Holliday said.
In Q1 this year in Colombia, the 8 ½-in. Kymera bit drilled through 460 ft of hard conglomerate rock and 1,232 ft of interbedded claystone and shale. The bit drilled 33.5 ft/hr, and the ROP exceeded 290% compared with a competitor’s offset well drilled using a 12 1/4-in. bit, replacing two PDC bits and a three-cone bit.
Halliburton
Five key technologies found in Halliburton’s MegaForce fixed-cutter bit, which debuted at the 2012 OTC, are aimed at providing an edge in ROP and ability to drill longer intervals by using SelectCutter PDC technology. “An increase in abrasion resistance and impact resistance allows the cutter to drill through different payzones,” Brad Dunbar, fixed cutter product manager, said. The thermal mechanical properties of the cutter are represented in the two materials that expand at different rates when exposed to heat. “Being able to control that thermal mechanical piece of the cutter really helps to keep the cutter from damaging itself under heat conditions,” he added.
Another key technology is the multilevel force balancing, which veers from what the industry has used in the past 25 years. Before the multilevel layout concept, there was a general force balancing across an entire cutting structure so that a transition from one rock type to another was not as smooth. The multilevel force balancing ensures a balance between the transition periods as result of the way the cutters are laid out on the profile of the bit. “We’re balancing not only the whole cutting structure, but in addition, we’re balancing the transition as those different cutter groups go through the different formations,” Mr Dunbar explained.
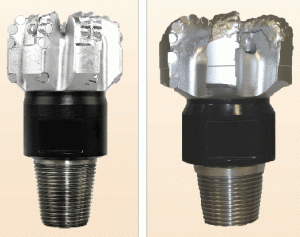
Improved matrix materials – tungsten carbide, powdered metal – offer more erosion and wear resistance to prevent damage or breakage to the cutting structure, and enhanced micro-nozzles help improve the flow of fluids across the cutting structure, according to Halliburton.
In a field trial from March to April this year in Uintah County, Utah, a 7 7/8-in. bit was used to increase footage by 31% and, at the same time, increased ROP by 20% on the same section, compared with an offset well about 100 meters away.
SteelForce, which was released in November 2011 and is more focused on high-ROP applications in shales and where particles do not have as much erosion properties, also features the enhanced micro-nozzles used in MegaForce. In the clay-intensive Haynesville Shale in East Texas and North Louisiana, this steel-body bit is often used because it does not ball up from cuttings. “Being able to get the fluid flow across the face of the bit where we need it is one big advantage,” Mr Dunbar stated.
An anti-balling coating is also applied to the steel through a heat treatment. “The outer layer of the steel turns the electrical conductivity of the steel into a negative charge. When you have a water-based mud and the particles in that mud are also negative, they start repelling each other,” he explained. “A build-up of a water surface on the bit face itself helps prevent balling through that process.”
Halliburton notes that SteelForce has been deployed to most shale plays across the US, as well as offshore GOM and in the Middle East for drilling through carbonates.
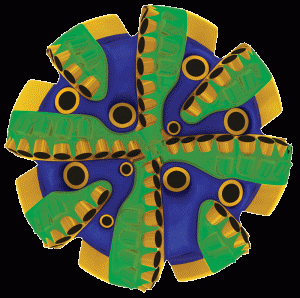
National Oilwell Varco
To bridge the gap between PDC and impregnated drill bit applications, NOV launched the FuseTek line of drill bits in April. The bits combine the abrasion resistance of impregnated bits with the high ROP of PDC bits. “We’re targeting applications that transition from medium to hard rock strength, where you normally drill with PDC bits for 80% of the run and need the durability of impregnated bits or insert bits to complete the harder interval,” Alexis Garcia, product line manager for hard rock drill bits, said. “You would have hard stringers that don’t allow the cutting structure to survive; therefore, with FuseTek, durability of the cutter structure is enhanced to drill further and faster, without the need to trip out of hole to change the bit type.”
The primary PDC cutting structure is backed by impregnated material and infused into the matrix. “The impregnated material has the capability to be a secondary structure that engages to continue drilling as an impregnated bit once the PDCs begin to wear,” Mr Garcia explained. In conglomerate and hard cherty sections, the bit becomes more impact-resistant to extend the bit life and optimizes the exposure of the material to be engaged in the formation when the primary cutting structure starts wearing out.
“The initial benefit of PDC shearing cutting mechanism is then converted to a grinding method after it loses its geometry by abrasion,” he added.
In an ongoing onshore Congo application that began in Q4 2011 involving sandstone, limestone, claystones and conglomerates, an 8 ½-in. FuseTek bit drilled 1,532 ft at an ROP of approximately 25 ft/hr. The interval was 26% longer than the previous best offset.
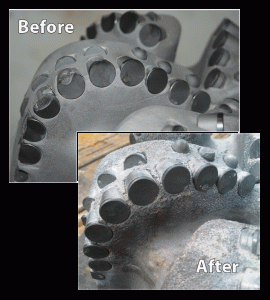
NOV also expanded its cutter technologies with HeliosEdge and HeliosImpact cutters in May. HeliosEdge increases ROP with high-efficiency cutters while HeliosImpact increases impact resistance with high-durability cutters.
The thermal-resistance technology that is applied to the bit removes the cobalt that is initially used to assist the high-pressure, high-temperature manufacture process promoting diamond-to-diamond bonding. During drilling, high frictional heat build-up on the cutting edge can generate temperatures that lead to thermal degradation of the cutter. “Diamond with cobalt binder will start to break down as it reaches 700°C, leading to cutter failure. Once the cobalt is removed from the cutting edge, the diamond itself can go to 1,200°C, providing increased durability to drill further and faster,” Tom Roberts, product line director for cutter technology, said.
HeliosEdge features altered-edge-geometry (AEG) technology integrated with thermal resistance technology. The AEG provides more efficient weight transfers, allowing faster ROP and lower cost per foot without compromising durability. The cutters target low depth of cut, torque-limited applications and can drill at least 30% faster, Mr Roberts said. Earlier this year offshore Norway, an 8 ½-in. bit drilled 1,610 ft at an ROP of 170 ft/hr, then was re-run to drill 12,300 ft at 128 ft/hr to TD. The run reflected the bit’s high ROP in an abrasive formation and set a record in the field.
The HeliosImpact cutters are better suited to withstand edge chipping experienced in harsh interbedded applications, where impact and cutter overload are the predominant cutter failure mechanism. In laboratory tests, these cutters showed a 45% improvement in impact resistance compared with conventional premium cutters, Mr Roberts said. Recently, a 9.875-in. bit was run in Nacogdoches, Texas, with the HeliosImpact cutters. When the bit was brought to surface and compared with an offset, Mr Roberts said, it could be seen that the bit with he new cutters had experienced little damage drilling through the Travis Peak and was pulled after reaching a depth of 10,700 ft.
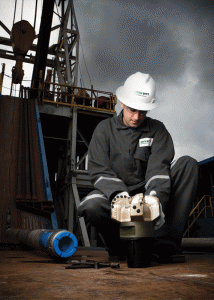
Photo courtesy of Schlumberger
Smith Bits, a Schlumberger company
Since the March 2011 commercialization of the Spear steel-body PDC bit from Smith Bits, the bit has completed more than 4,000 runs in unconventional shale plays across North and South America, Europe and Asia. The company continues to apply design enhancements, aiming to outperform benchmarks set by the original design. “For the new generation Spear product, we concentrated our design on two main areas: the first was to really optimize the slot area between bit body and borehole to allow cuttings to flow to the annulus with the lowest resistance possible, and the second was to implement our new range of premium ONYX cutters. The results have been incredible,” Steve Segal, marketing & technology manager, explained.
The new design, which was field tested starting in Q4 2011, has been deployed in areas such as Argentina, Poland, Germany, Canada and China. It features taller blades to create a more convex, bullet-shaped body, which further increases the cuttings’ sweep around and from the bit face into the annulus. While the bit itself remains the same size, the taller blade is exposed to more volume for the cuttings. “A great deal of engineering, especially in the material and design of the blades have enabled us to make them much taller without compromising their integrity,” Mr Segal said.
Keeping cutters clean to ensure cleanliness and bite into new rock involves help from the placement of nozzles. Nozzles are embedded in the Spear body, which consequently creates a ledge where cuttings can accumulate and plug the nozzles – impacting the efficiency of hydraulics. The new bit design addresses the potential for accumulation by changing the body geometry around the nozzle, providing a channel for cuttings to escape – the shale evacuation channel, Mr Segal said. “We’ve noticed again further improvement in keeping all of the nozzles open to provide maximum hydraulic energy downhole.”
An anti-balling coating that has been used extensively in sticky-shale areas such as the Middle East is an available option to further prevent cuttings from sticking to the bit area and further assists in flushing away cuttings. “This proprietary material is electrochemically bonded to the outside of the bit to create a surface that repels shale particles,” Mr Segal said. “It allows for the shale cuttings to continue their journey from being drilled to the annulus without bonding and adhering to the drill bit. These measures really make a difference in improving the penetration rate and reducing problems associated with poor hydraulics.”
The ONYX II premium cutters in the Spear bit also have been upgraded using a high-pressure, high-temperature manufacturing process of synthetic diamond, Robert Ford, product commercialization manager, said. Using advances in manufacturing techniques that involve pressures exceeding 1 million psi and 1,000°F, the new material has improved wear resistance without sacrificing impact strength, he explained.
In the Louisiana Haynesville, the new-design 6 ¾-in. bit drilled more than 6,382 ft at 40 ft/hr earlier this year. The bit completed a tight curve and lateral section in one run, and based on median ROP, the bit was 40% faster than the original bit.
IDEAS, an integrated drill bit design platform that takes into account each element of the BHA in a 4D simulation, has allowed Smith Bits to create bits with application-specific enhancements without having to go through physical iterations and runs in customers’ wells. The company took the initial five- and six-blade design of the Spear bit and created a four-blade design using IDEAS, Mr Ford said. While fewer blades often equates to higher ROP, it also means durability and directional control might be compromised. To maintain both elements, “we used sophisticated computer modeling of the IDEAS platform – our virtual environment,” Mr Ford explained. “Rather than make hundreds of bits that are all different and trying to run them in customers’ wells to see how they react, we built a very detailed model of the downhole environment and perfected the design with customer input.”
The new four-blade, 8 ½-in. Spear bit designed for the Marcellus was deployed in late 2011. This was the first time the four-blade design was utilized in this application, and the bit drilled 5,764 ft in 42 hrs at a rate of 138 ft/hr, delivering an improvement of more than 40% based on the previous Spear designs. The bit maintained stability and steerablity for toolface control.
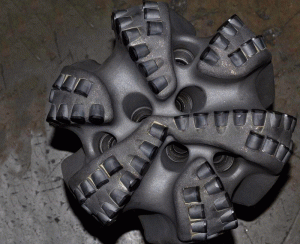
Ulterra
To support the pace of development demonstrated in the drill bits market, Ulterra is working to accelerate the deployment of new bits, commercializing new technologies in a matter of months. Implemented in 2011, the LightSpeed process is founded on “the relationship you have with the PDC vendors themselves and particularly the ability to take a new cutter that looks exciting in the laboratory and have it tested in the field more rapidly than others,” Andy Murdock, director of PDC technologies, explained. Ulterra offers two families of PDC cutters: LightSpeed XTa and LightSpeed XTi. The first targets hard-rock and high-temperature drilling, particularly in shales, to improve abrasion resistance, and the latter targets extended-reach drilling applications to improve impact resistance. “We’ve been able to drill through formations that are a lot more difficult to drill, a lot deeper than we were able to drill. We are drilling 20% to 30% more footage in many applications than we were able to drill nine to 12 months ago,” Mr Murdock said.
Each cutter is developed for a specific application. Ulterra works with different vendors to source material that meets toughness criteria and customizes cutters to meet demands for abrasion resistance.
Using LightSpeed technology, the company’s 12 ¼ -in. U616M, six-bladed matrix PDC bit with 16-mm cutters set a footage record in the Granite Wash in western Oklahoma earlier this year. The bit drilled 7,065 ft from surface casing to 8,115 ft, saving the operator approximately $88,500 versus average offset wells, Matt Mumma, vice president of engineering, said.
The company’s 8 ¾-in. U616M, six-bladed matrix PDC bit with 16-mm cutters also set a record earlier this year in the Eagle Ford. From surface casing to TD, the bit drilled the vertical, curve and lateral intervals at 93 ft/hr in one run. The bit reached TD at 9,953 ft in 107 hrs and saved the operator approximately $133,000 versus average offset wells.
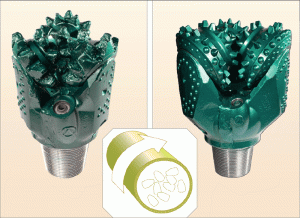
Varel
Despite the popularity of PDC bits today, roller-cones remain in high demand through the market. Varel International launched two roller-cone series within the last year to round out its product line between steel-toothed and TCI bits.
The DuraTech steel-toothed series, available from 3 ¾ to 13 ¾ in., features updated hardmetal capable of withstanding stress when additional weight and greater RPMs are needed. Updated manufacturing techniques reinforce a hardmetal to withstand impact, as well as abrasion, Karl Rose, field engineering manager – western hemisphere, explained. Varel introduced stringent quality control methods to the hardmetal because the application is completed by hand. The goal is to limit variations in the welding to improve consistency.
This series of bits has been deployed worldwide and has been most successful in GOM applications, the company said. The bits also have had successful runs in the Eagle Ford, the Rockies and the Barnett Shale.
The High Roller series, available from 14 ¾ to 17 ½ in. as both TCI and steel-toothed designs, features redesigned head forgings and an enhanced bearing. “The forging takes advantage of some of the better cleaning through hydraulics,” Mr Rose said, “streamlining some of the paths for fluid and cuttings to flow away from the face of the cutting structure.” The bearing is optimized to push the limits of handling high WOB and RPM applied to the bits. “As the rigs and equipment used on rigs continue to get bigger, stronger and provide more energy, all that still has to go through the drill bit. Bearings have to constantly be updated and improved in order to deal with and endure the energy levels that continue to increase.”
The grease reservoir system of this bit series also enhances flow of grease through the bearing. “As the bit is drilling, grease is able to circulate through the bearing to help keep it cool,” Mr Rose said. “The upgraded design greatly increases the grease with the increase in size designed to match the demands of the bearing system.”
The series is also treated with high energy tumbling (HET). This treatment is not new but is being increasingly used because of the higher energy levels encountered by roller-cone bits. The HET process is applied to cutters to alter surface attributes for more abrasion and impact resistance. “While non-treated carbide inserts will show breakage, a bit with HET is able to prevent that breakage and just show wear,” Mr Rose said.
A customer’s need in the Middle East led to one of Varel’s biggest developments in the last year: a 44-in. steel-toothed, roller-cone bit. “A customer had the need for a large-diameter hole to be able to drill the top-hole section more efficiently without tripping,” Mr Rose explained. “In the past, either reamers or another kind of hole opener had to be used.” The three-cone bit that was developed for this application has six interchangeable carbide nozzles and is able to drill without having to go back and run a reamer behind it, which mitigates risk and reduces opportunities for error.
“For a hole that size, we’re obtaining ROP up to 30 ft/hr, which is fast for something that large, with footages over 800 ft drilled.”
Talon and Kymera are trademarks of Baker Hughes. MegaForce, SteelForce and SelectCutter PDC Technology are trademarks of Halliburton. FuseTek, HeliosImpact and HeliosEdge are trademarks of National Oilwell Varco. Spear and Onyx are marks of Schlumberger. LightSpeed is a trademark of Ulterra. DuraTech and High Roller are trademarks of Varel.