Case study: Algerian underground blowout
Incident demonstrates need for well-trained crews, adequate mud equipment
By Pedro Martinez Aguilar, Repsol Exploration; Michael Arnold, John Lee, Boots & Coots, a Halliburton Service
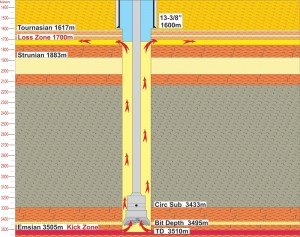
The outcome of a well control and blowout incident reflects how well a crew is trained and prepared. This article will discuss the sequence of a well control operation that occurred in Algeria in December 2008, which includes the influx, steps to identify the situation, operations to control the underground blowout and the response of the well.
An operator drilled a 12 1/4-in. exploratory well at 11,516 ft in the Emsian formation and set a string of 13 3/8-in. casing at 5,250 ft. A pit gain was observed, and the well was shut in. The maximum annulus pressure recorded after shut-in was 570 psi. A sudden drop in annulus pressure to 325 psi suggested lost circulation and was assumed to be in the Tournasian formation (5,305 ft to 6,180 ft), where severe lost returns had been recorded while drilling (5,580 ft to 5,740 ft).
The pressure drop made it difficult to assess the kick, thus hindering conventional well-control techniques.
Initial Well-Control Actions
Pore-pressure equivalent mud weight (EMW) at the Emsian formation was estimated to be 11.7 to 12.7 lbm/gal. The formation-strength EMW at the Tournasian formation was estimated to be 10.0 to 11.7 lbm/gal. Believing the well was experiencing losses to the Tournasian, 189 bbl of 11.6-lbm/gal mud was pumped into the casing annulus. The annulus pressure remained constant, indicating the possibility of an underground blowout.
As the annulus pressure continued to increase to 1,000 psi, 340 bbl of 11.6-lbm/gal mud was pumped down the casing annulus to reduce the pressure. A volume of 340 bbl of 9.9-lbm/gal mud was pumped down the drill string while maintaining a maximum choke-back pressure of 1,600 psi. After pumping the mud, the stabilized pressure was used to determine the bottomhole pressure. While adjusting the choke, an influx entered the wellbore.
To prevent the annulus pressure from increasing beyond 1,000 psi, batches of 13.3-lbm/gal mud were pumped periodically into the annulus. The initial volumes of mud contained lost-circulation material (LCM) to help cure the losses.
The drill pipe was filled periodically to avoid gas migration up the drill string. Shut-in drill pressure remained at 0 psi. Losses in the annulus were reduced when the LCM reached the loss zone, and the shut-in drill pipe pressure gauge began indicating pressure.
Sandwich-Kill Attempt
The hole was displaced through both the drill pipe and the annulus, “sandwiching” the influx into the lost zone.
The Emsian formation pressure was predicted to be between 12.1 and 12.7 lbm/gal EMW, meaning a 15.9-lbm/gal kill mud would overbalance the Emsian formation by +/- 3.2 lbm/gal. A cement unit was used to pump 818 bbl of 11.6-lbm/gal mud down the casing annulus, and rig pumps were used to pump 1,006 bbl of 15.9-lbm/gal mud down the drill pipe.
The operation was partially successful because the annulus pressure was still 600 psi at the end of the procedure. However, it confirmed that the bottomhole pressure and the pressure at the loss zone were higher than predicted.
Casing pressure began to increase, and drill pipe pressure remained at 0 psi. Once the casing pressure reached 2,050 psi, the drill pipe pressure increased proportionally to the casing pressure.
Communication between the annulus and the drill string was demonstrated by bleeding off 300 psi on the casing, causing a 25-psi drill pipe-pressure decrease. To keep the casing pressure as low as possible, gas was bled from the casing annulus until fluid was observed at the surface. Thereafter, the casing pressure could not be further reduced.
Circulation-Kill Attempt
Heavy mud was pumped down the drill string to control bottomhole pressure and to circulate gas out of the well. Without an accurate value for the bottomhole pressure, the proposed kill-mud weight was 13.3 lbm/gal, based on the mud hydrostatic pressure and the shut-in casing pressure but neglecting the height of the gas in the annulus.
After pumping began, drill pipe pressure dropped to 0 psi. Consequently, the choke had to be adjusted without a reference value for drill pipe pressure. The choke position was kept constant, adjusted only when annulus pressure increased. Mud losses were difficult to quantify, and the well was shut in when the rig ran out of mud.
During the mud buildup, temperature and pressure logs were run to the depth of the downhole motor in the bottomhole assembly. These logs indicated the fluid level was around 4,216 ft and the pressure at 11,411 ft total depth was 4,630 psi.
The temperature log detected disturbance around 5,600 ft, which corresponded to the depth of the Tournasian formation. The log response was interpreted as fluid movement. The repeat section of the log corroborated the crossflow at the Tournasian formation at the same depth where losses were experienced in drilling.
Annulus-Pressure-Control Attempt
Because drill pipe pressure was 0 psi, there was no reference for operating the choke. It was decided to maintain constant annulus pressure or allow it to decrease. Four LCM pills were pumped. As the first pill reached the thief zone, the losses decreased to zero. Subsequently, the pit levels increased, indicating slight gains. The volume pumped and the time when the LCM reached the surface indicated the hole was in gauge.
Once the losses were reduced to a minimum, the pump rate was increased and the choke was opened slightly to counteract the vacuum effect on the drill pipe. However, the mud level in the drill pipe dropped continuously.
When the choke opened to 1/16 in., casing pressure dropped more than expected. This jeopardized the control of the influx from the Emsian formation. The pumps were stopped, and after a few minutes, the drill pipe pressure began to increase. An influx of gas appeared to migrate inside the string, prompting the pipe to be displaced with 13.3-lbm/gal mud.
The well response indicated gas remained in the annulus, and the integrity of the Tournasian formation was still low. The kill operation resumed, and 239 bbl of 12.1-lbm/gal mud were pumped ahead of the 13.3-lbm/gal mud. The 12.1-lbm/gal mud did not reach the Tournasian formation. Consequently, the pressure in front of the weak zone at the Tournasian formation was minimized. At that point, more LCM pills were pumped.
While making repairs to the mud-gas separator, additional influxes entered the wellbore. When pumping restarted, pressure peaks suggested partial plugging of the ports in the circulation sub. As a precaution, no further LCM was pumped.
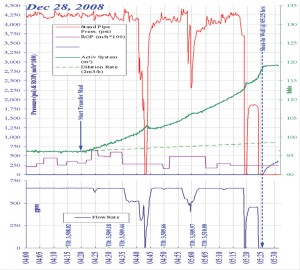
Low-Choke Attempt
Changes in the annulus pressure after shutting in the well indicated that there was still a small amount of gas in the annulus or at least above the Tournasian formation. The “low-choke” method was used, attempting to control the influx from the kick zone at the bottom of the well while allowing the loss zone to deplete to a lower pressure. The basis was to hold the choke pressure equal to or slightly greater than the last recorded shut-in value while circulating as fast as safely possible. The mud density was designed to sufficiently overbalance the kick zone.
An 11.6-lbm/gal mud provided 50-psi hydrostatic pressure, in addition to annulus friction-pressure overbalance to the kick zone. The choke pressure was calculated using the casing pressure observed at the beginning of the operation, with an additional 200-psi safety factor added. The circulating rate used was as fast as the surface equipment would allow. Sixty-three bbl of 12.2-lbm/gal mud were pumped into the annulus.
An increase in drill pipe pressure suggested the presence of gas inside the pipe. The operation was stopped when bottoms-up volumes from the Tournasian and the Emsian formations were observed at the surface, and the crew prepared to reduce the annulus pressure. Operations resumed after the drill pipe was filled.
The well was monitored, and the casing pressure was bled off 100 psi to test communication between the annulus and the drill pipe. An unexpected 200-psi increase in drill pipe pressure occurred, indicating there were now two different pressure systems partially isolated by one or more packoffs in the annulus.
Once the bottoms-up volume from the Emsian formation reached surface, the choke was opened at separate intervals to bleed off 200 psi. Four intervals were needed to reduce the casing pressure to 500 psi. Because it was difficult to keep the casing pressure stable, it was decided to fully open the choke, allowing the casing pressure to rapidly bleed off to 0 psi. No returns were recorded at surface.
The pump rate was increased without result, except for a brief increase in pipe pressure, which suggested a restriction or packoff was present in the annulus. A total of 110 bbl of mud, along with 60 bbl of water, was pumped down the annulus to compensate for the fluid-level drop. The calculated fluid level was 1,371 ft.
Once pumping into the annulus stopped and the casing pressure dropped to 0 psi, the blowout preventer was opened to monitor the well. Because of the possibility of pipe plugging and annulus packoff, the pipe was worked. Five feet of pipe movement was gained, but rotation was impossible. The well was shut in with the annular preventer when mud overflowed at the bell nipple.
An attempt was made to establish circulation. Initially, the casing pressure rose very quickly to more than 3,000 psi. On the second attempt, the drill pipe pressure increased from 1,800 psi to 3,500 psi after pumping only 31 bbl of mud. With an entire drill pipe capacity of 187 bbl, this indicated the pipe was plugged. Further, the casing pressure did not reflect the pressure changes. It was concluded that one or more packoffs were present in the annulus.
An unsuccessful attempt was made to break the packoffs by pumping down the annulus. Subsequent efforts focused on bleeding off the annulus pressure and attempting to work the pipe to free the drill string, and a “lubricate and bleed” method was attempted. Large amounts of gas were recorded at surface, resulting in the annulus pressure dropping to 0 psi, and losses were also recorded. After filling up the hole with 13.3-lbm/gal mud and water, the well again began to flow. A 50-bbl mud cap using a 13.3-lbm/gal high-viscosity pill was pumped down the annulus but was unsuccessful in preventing gas from percolating to the surface.
When the annulus was bled off and the mud level was confirmed to be at surface, the pipe was worked. The drill string was torqued-up and continued to be worked. The string did not become free, moving 8 ft upward without releasing any torque.
The pipe was completely stuck, and circulation was impossible. The operator abandoned the drilled section of the well. The inside of the drill string was killed by isolating the inside diameter with cement or mechanical plugs. The drill string was perforated as deeply as possible to isolate the annulus using cement. A coiled-tubing unit was then used to cut the drill string, and the Tournasian formation was allowed to unload.
Lessons Learned
• The Tournasian partial mud-loss event occurred because the formation permeability and porosity were high to allow loss of whole mud (natural losses). This was evident by treating the losses with LCM. It is recommended that an open-hole formation integrity test (FIT) be performed after repairing the loss zone and regaining circulation. This helps ensure the wellbore pressure integrity is equivalent to the FIT recorded at the last shoe depth.
• If leak-off occurs before the equivalent shoe FIT is reached, wellbore maximum allowable surface pressure and kick tolerance should be recalculated at the loss-zone depth to accommodate the downgraded FIT.
• If creditable formation-pressure data is not available, the heaviest kill-mud weight possible should be used.
• Training in kick detection and BOP shut-in on all rigs is recommended.
The main lesson learned from this incident was the necessity for well-trained and experienced drilling crews and the importance of adequately sized mud-mixing and handling equipment.
The authors thank the management of Repsol Exploration and Boots & Coots for permission to present this paper.
This article is based on a presentation at the 2011 IADC Critical Issues Asia Pacific Conference & Exhibition, 23-24 November, Kuala Lumpur, Malaysia.