High-strength pipe caters to Arctic drilling
Steel chemistries, manufacturing processes improved to create drill string solution for temperatures to -60°C
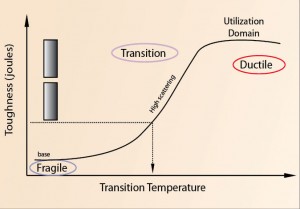
By Philippe Machcourt and Kamal El Bachiri, VAM Drilling
Extreme low temperatures and hostile drilling environments such as the Arctic are driving the industry to adapt their drilling programs and develop fit-for-purpose drill string solutions. Proprietary Arctic grades already exist for temperatures as low as -40°C. However, for high-strength drill pipe, it is necessary to meet the drilling loads associated with temperature conditions as low as -60°C.
The need for such drill pipe is derived from well topology constraints in regions such as Russia, Eastern Europe, the CIS, Alaska and Canada. The underlying issues are not uniquely related to the service temperature of these tubulars but rather to the risks associated with susceptible damage during ground transportation and surface handling, especially in Arctic fields (permafrost).
Controlling critical manufacturing parameters is a key factor to reach top-of-the-range products. Steel microstructure, chemical composition, cleanliness and control of the heat treatment process are important factors in high impact toughness on high-strength drill pipe. Controlling yield strength and hardness are instrumental for optimal product performance and to allow contractors and operators to safely and efficiently drill in these environments.
This article presents the appropriate steel chemistries and manufacturing controlled processes required to meet safe operating standards and performance-driven practices. This includes a range of parameters that must be considered by managers and engineers involved with specifications when planning wells and designing products for low-temperature environments.
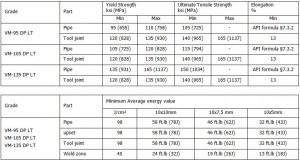
Low-temperature phenomenon
Embrittlement failure can be a concern for drill pipe operating in extreme low-temperature environments, particularly when combining high-toughness and high-strength steels. Steel subjected to shocks at these storage conditions (temperatures down to -60°C) can have unpredictable consequences. Certain conditions may require the use of drill strings with high ductility to achieve desired torsional and tensile strengths.
Low temperature refers to well environments where temperatures are below -20°C. The steel becomes brittle at low temperatures or at high strain rates (quick deformation at a high level of load between yield strength and ultimate tensile strength).
The phenomenon of brittle ductile transition, discovered during World War II with the Liberty ship steel failure in the North Sea, generates uncontrolled situations with short time failure, high crack propagation rates and high deviation or heterogeneities on steel ductility.
Today, the use of a range of high-strength steel grades, such as X-95, G-105, S-135 or higher, translates into a need for ductility while taking into account that the higher the yield strength, the lower the toughness.
Despite rigid precautions taken to control drilling operations (ROP reduction and drill pipe life reduction), fit-for-purpose, low-temperature steel grades have been customized for these drilling applications. Know-how as to environmental effects on steel has led to improved casting and rolling routes, improved heat treatment to reach controlled yield strength, restricted hardness, improved fracture toughness and resistance to high-speed crack propagation.

Steel making
Primary & secondary steel making
Both electric arc furnace and basic oxygen furnace processes are applicable to manufacturing low-alloy steels. The preferred elaboration route for low-temperature steel grades is the basic oxygen furnace, for which the resulting steel chemistry has an inherently low level of residual elements. These elements, such as copper and tin, are known to have a deleterious effect on steel’s sustainability to sulfide stress cracking.
Proprietary chemistries have been developed to manufacture drill pipe with high impact resistance at low temperatures. Chemistries exhibiting an optimum balance of chromium, nickel and molybdenum are key factors impacting toughness, in addition to the benefit of micro-alloying. It is also essential to keep residual elements, such as phosphorous and sulfur, at a minimum level through well-controlled steel elaboration practices. The limited addition of boron with controlled nitrogen and micro-alloys can be used to achieve a higher hardness.
Monitoring of secondary steel making is important to ensure tight heat-to-heat chemistry variations. These narrow ranges were defined based on Vallourec’s experience.
Knowledge developed with regards to the heat treatment of mother pipes and tooljoints provides additional robustness. Each individual heat is expected to repeatedly exhibit the same response to a given set of austenitizing and tempering furnaces parameters.
Process control, repeatability, steel cleanliness
Low variations in the heat-to-heat chemistry of green pipes subsequently allow for heat-treatment units to benefit from small scattering in steel response to heat treatment, thereby ensuring control of mechanical properties.
Refining and casting processes are adapted through internal procedures developed to achieve a cleanliness (macro and micro inclusions) for de-oxidation, refractories, nozzles, casting powder, etc, all of which are derived from sensitivity analyses of process parameters to control the inclusions level.
In compliance with quality assurance policies, several measurements are performed at a fixed frequency:
• Micro-cleanliness (evaluated according to the ASTM E45 methodology) refers to non-metallic inclusions. Typical results are: Type A, B & D = 1 and type C = 0.
• Macro-cleanliness controlled by in-house ultrasonic methods is used to evaluate the statistical amount of non-metallic inclusions.
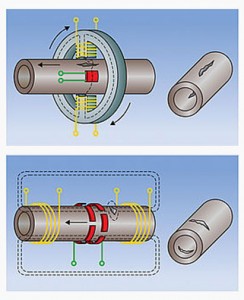
Hot deformation
Manufacturing process
Mother pipes are manufactured from bars of continuous cast steel and hot-rolled into continuous rolling mills using the Mannesmann effect.
Pipes are subsequently upsetted internally and externally by hot-forging deformation under controlled conditions. This process allows for a smooth profile of the internal and external part of the upset, one of the most sensitive parameters to ensure fatigue resistance properties. The internal upset profile is controlled by a multi-axis system to ensure high fatigue resistance (Miu > 3 in.).
Tooljoints are forged from bars produced from hot-deformed ingots. The manufacturing processes are controlled, such as minimum hot deformation ratio requirements, to increase impact toughness.
Process control
Continuous rolling mills and appropriate manufacturing procedures support the quality of the hollows. The hollows temperature homogeneity is achieved by tooling wear monitoring and replacement frequency. An inspection using in-line, non-destructive electromagnetic and ultrasonic tests (UT) will evaluate the products.
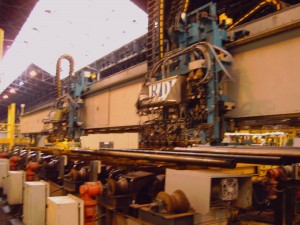
Heat treatment
Controlled mechanical properties
When using low-alloy carbon steel chemistries, the heat treatments aim to reach the desired mechanical properties for both tooljoints and mother pipe as a standard austenitization, quench and temper process.
Although the main purpose of austenitization is to allow transformation of the bulk of the as-rolled/as-forged steel microstructure (a variety of ferrite, pearlite and bainite structures), an optimized thermal cycle is expected to reach a complete precipitates dissolution without grain growth. Proper and efficient quenching should produce a homogeneous martensitic microstructure along the axis and through the wall thickness of each part.
Tempering after quenching is performed to reach a narrow range of mechanical properties, such as the yield strength and hardness.
In-house procedures are established during the development and qualification phases and implemented for production manufacturing to ensure that deviations from each identified parameter stay within acceptable and controlled limits.
Standard deviations of the process typically originate from dispersions on the pipe itself, the heat treatment lot, the heat, the test and eventually the size. A typical expression of the yield strength deviation can be expressed as:
σtotal=σheatlot∙σsize∙σtest
• Variations of properties along a pipe axis and around its circumference, between several heat treatment lots and several steel batches, are maintained at a low level.
• Numerical models of furnace thermal properties allow for optimal delivery of the heat to the pipe lot, taking into account the pipe sizes, allowing heat treatment with a narrow range of deviation.
• The tensile test itself also leads to a deviation that, in some instances, can be larger than the process deviation itself.
Efforts to control these deviations compared with conventional API manufacturing allow a reduction in dispersion by a factor of 2 on σtotal.
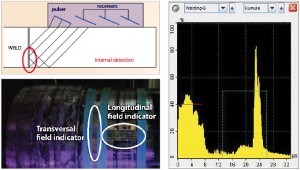
Nondestructive testing
Low-alloy carbon steels used by VAM Drilling for premium drill pipe have been selected in accordance with Vallourec’s guidelines to ensure absence of cracks upon quenching and subsequent handling.
To eliminate subsurface flaws, heat-treatment units are equipped with installations such as magnetic particle inspection for upset ends. Inspections of the drill pipe are performed at various stages of the manufacturing cycle:
• Pipe body: Automatic electromagnetic inspection and UT benches to search for internal and external longitudinal and transversal indications of presence of flaws;
• Upset areas: Dry magnetic particle inspection to search for internal and external longitudinal and transversal flaws;
• Friction weld: Automatic UT inspection to search for internal and external transversal flaws and wet magnetic particle inspection for external transversal flaws; and
• Tooljoint: Wet magnetic particle inspection under UV to search for external longitudinal and transversal flaws.
Drill pipe properties & guarantees
Taking into account manufacturing process controls combined with the latest technology developments, it is possible to obtain fully ductile behavior at temperatures as low as -60°C.
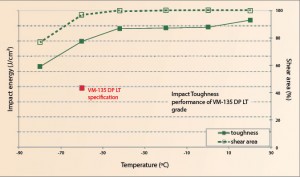
VAM’s VM-135 DP LT exhibits a fully ductile behavior at temperatures as low as -60°C, as shown on the transition curve in Figure 4. The ductile-to-brittle transition temperature is below -80°C.
The development of these products enabled high tolerance and controlled damage resistance to crack growth and propagation rate. Fracture toughness and crack tip opening displacements (CTOD) have been measured on various steel grades as per ASTM E399-06. The CTOD delta value gives the maximum acceptable notch size limiting crack initiation into the material at a given temperature. The fracture toughness value (Kmax) gives information on the ability of the material to absorb the energy due to a sudden shock.
These values are known to noticeably decrease with steel strength and are valuable parameters to track when drilling equipment is anticipated to be submitted to severe loads. The VM-135 DP LT presents a CTOD around 95∙10-3 mm and Kmax around 135 MPa∙√m with low-cycle fatigue performances.
Recommended practices
The material described in this article is specific to extreme storage conditions (down to -60°C), providing a high level of Charpy impact toughness in the tooljoint, pipe body and weld zone.
Additional precautions should be taken in handling, inspecting or breaking-in the pipes. They include:
• Use of a suitable dope when making up the connections on the rig floor and ensuring makeup torque values are adjusted for the friction factor of the dope.
• Connections should be properly inspected;
• No ice film on the threads;
• No shocks on connections;
• Ensure tongs are properly placed when making up at the rotary table or with a top drive;
• Ensure the top drive or tongs are properly calibrated, and use a calibrated torque indicator instead of a torque limiter;
• Pipes should be carefully handled to avoid shocks; and
• Frequency of in-service inspections can be reduced.
Conclusion
VAM Drilling has addressed the challenges associated with the development of a drill string solution for extreme low temperatures (-60°C) and hostile drilling conditions. The solution combines fit-for-purpose chemistries and controlling of manufacturing processes, which includes steel microstructure, chemical composition, cleanliness and heat treatment process control; all are critical to achieving high impact toughness on high-strength drill pipe.
Field guidelines pertaining to the use of products such as heavy-weight drill pipe, drill collar, pup joints, drill stem substitutes are also available. Additional work remains to be done to include the bottomhole assembly.