When strategy and organizational culture collide, culture wins
By Linda Hsieh, managing editor
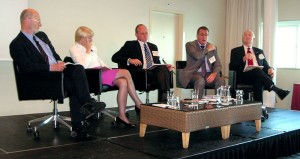
To all the companies out there still talking about and trying to figure out how to create an effective safety culture, Guy Boyd of Behavioural Science Technology (BST) has some news for you: There is no such thing as a safety culture.
There is only organizational culture and whether that culture supports safety efforts, Mr Boyd asserted during a panel session at the 2011 IADC Drilling HSE Europe Conference & Exhibition, 28-29 September in Amsterdam.
“An organization has a culture or a series of cultures which may be supportive of safety, or maybe they’re supportive of production, finance or quality. But it’s one culture, even it has many manifestations across departments, functions and teams,” said Mr Boyd, regional general manager EMEA for BST.
This organizational culture is created through leadership – not just by the CEO but by leadership at all levels. For example, a company can spend all the time and money in the world on safety management systems, but that won’t mean much if the organizational culture isn’t supportive of that safety management system. “First day a young guy comes out of training and on the job, they have someone take him under his arm and says, ‘I’m glad you’ve done your training, son, but let me show you how we really do it around here.’ That’s the point at which organizational culture takes over,” Mr Boyd explained.
“If strategy and culture collide, you can bet that culture will win,” he said.
Co-panelist John Thorogood, senior technical adviser for Drilling Global Consultant, advised the industry to take a closer look at high-reliability organizations (HROs) because it may prove valuable in drilling’s high-risk environment.
Citing a book titled “Drift Into Failure,” by Australian author Sidney Dekker, Mr Thorogood explained the book’s thesis stating that the complex organizations we’ve created are contributing to some major accidents. “It’s this chronic pressure on people to deliver results. We have very complex organizational and social relations where you can’t input into one and expect a predictable outcome,” he said. “This is a sign of a chaotic system.”
Preceding incidents, there are usually a series of incremental changes to procedures or accepted risk levels that are invisible to the people inside the system. “It’s only when you have accidents and you track back that you see all was not right. But it’s not obvious beforehand,” Mr Thorogood said.
In the interest of learning from these HROs, he provided five characteristics of high-reliability organizations. First, there is a preoccupation with failure. “It’s a chronic unease about safety and analytical errors and really following up on unexplained failures in the sense of, ‘Have I missed something?’ In our industry, focus on things like the integrity of DP systems is what might fall in this category,” he said.
Second is a reluctance to simplify interpretations. “We tend to simplify and eliminate stuff because we think it’s too complicated, too time-consuming and we have to get practical work done. Yet high-reliability organizations tend to resist that tendency and focus on chasing inconsistencies,” Mr Thorogood said.
The last three characteristics are sensitivity to operations, commitment to resilience and deference to expertise, and Mr Thorogood challenged the audience to think about whether these things can be built into the drilling industry culture and how we can take them forward into the future.
Professor Rhona Flin from the University of Aberdeen’s Industrial Psychology Research Centre based her discussion in the panel session on past and ongoing research. “Part of my thesis is, for senior managers to be able to reduce deviance and raise standards, they need to have a sense of reality,” Professor Flin said.
She believes that most of the studies available that look at how senior managers influence organizational safety culture pay insufficient attention to production demands. They all look at safety in isolation from the real world of running a business. “Often we don’t see the production demands and other competing financial drivers being factored in to these studies of senior management behavior,” she said.
The industry should also acknowledge that safety leadership can be difficult, and there are many barriers that senior managers and middle managers face trying to enact good safety leadership. “Quite a lot of it is tricky to do, for example, motivating subordinates to work safely or establishing effective disincentives to things like rule breaking,” she said.
Under a current study Professor Flin is involved with, managers from the energy industry are being interviewed about their jobs – what they can do in terms of safety leadership and what is difficult to do. Three themes are emerging from these interviews, and the first is establishing safety as an organizational priority. This means management must both act as a safety model and incorporate safety into decision making.
Second is setting and managing safety standards, and third is maintaining risk awareness.
“One thing we’re looking at with pilots and surgeons, which I think would be very relevant to drillers, is understanding their risk tolerance and how they’re calibrated on risk tolerance,” Professor Flin said.
Providing an operator’s perspective was the final panelist, David Martin, VP safety, environment and sustainable development for Shell Upstream International. He explained that, three to four years ago, his company moved away from a purely initiative-based safety approach in search of a more sustainable platform. This meant shifting safety from just a priority to an organizational core value.
The company also recognized that leadership on safety must be delivered from the top and consistently throughout the organization. Mr Martin recalled one time years ago when he was shopping with his family; he was an asset manager in Aberdeen at the time.
He was approached by a technician from one of his offshore platforms who said he noticed Mr Martin didn’t hold the handrails going down the stairs – why is that? The technician went on to say that he won’t believe Mr Martin anymore if he goes out to the platform and gives the crew rhetoric about holding the handrails. “(Safety) is something you have to live and breathe,” Mr Martin realized. “You set the culture and the tone by your actions.”
Shell also has been working toward simplifying its safety management system requirements. “We got considerable feedback from the contractor community that we complicate the hell out of things,” he said. From the nearly 7,000 mandatory requirements in safety management systems, Shell has launched a new control framework with only 600 mandatory items in that area.
“When you have so many requirements, you leave it up to the individual to make a choice on what’s important,” Mr Martin said. “If you can simplify that, you’ve got a greater chance of alignment on what’s important and what’s not important.”