Drilling contractors shepherd a rethinking of safety culture through focus on SIF prevention
Cause mapping, behavioral-based learnings are at the forefront of efforts to reduce the potential for serious injuries or fatalities on rigs
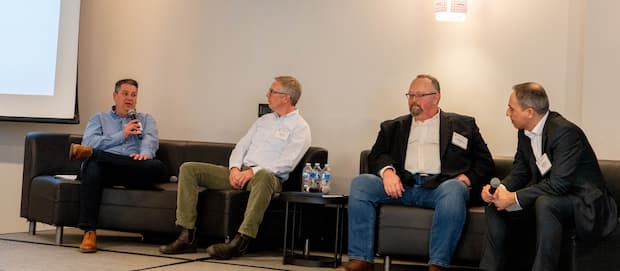
By Stephen Whitfield, Senior Editor
For decades, total recordable incident rate (TRIR) has been the standard key indicator for HSE performance in the oil and gas industry. It has proven valuable in providing a standardized safety metric. However, in recent years, HSE leaders have begun questioning whether the TRIR provides a truly comprehensive picture.
To get a better understanding of the safety risk, companies are increasingly pivoting their focus to exposures, such as unsafe conditions or behaviors, that have the potential to lead to a serious injury or fatality (SIF).
“Our leaders have enough foresight to look at things and notice that something’s wrong,” said William Arpe, HSE Specialist at Helmerich & Payne (H&P). “You can have an outstanding year in terms of recordables, but if you still have fatalities, something’s not right. It’s important to look at your incidents and identify some of the precursors within those events that led to those incidents.”
While the term SIF has become more familiar to drilling contractors in recent years, it has not yet become a metric that is systematically tracked as a key performance indicator. The US Occupational Safety and Health Administration (OSHA) does not require companies to track and evaluate the near-misses and other exposures that have the potential for SIFs.
However, the industry is starting to make that change anyway, recognizing the importance of investigating potential exposures to SIFs. In recent years, drilling contractors have launched initiatives to incorporate potential SIF tracking into their safety protocols. At the 2024 IADC HSE&T Conference in Houston on 6 February, a panel of drilling contractor HSE representatives outlined some of the steps that are being taken.
Rethinking the approach to incident investigations
Precision Drilling is in the midst of what Ryan D’Aunoy, Senior Manager – HSE Management Systems, called a “multi-year cultural and procedural shift” in its thinking, looking at its resource allocation, incident classification and investigations, critical risk identification and control and process design. The goal is to eliminate SIFs entirely. In 2021, the company implemented SIFs as a key safety metric and incorporated a SIF reduction target into its safety planning.
One of the key steps in this effort was the company’s decision to shift the focus and resources of its investigations from recordable incidents to SIFs, from what Mr D’Aunoy called a “fault focus” to one that’s centered on organizational learning.
Previously, incident investigations involved taking witness statements, with questions typically centered around finding fault – was a person following a procedure, and if not, why not? Now, the organization utilizes a hierarchical investigative blueprint, examining the systems, procedures and resources provided to workers at a SIF or SIF-potential event; the amount of monitoring provided by management; and then examining the human error that led to the event.
“We’re forcing ourselves to go in that hierarchy, look at the organization and the work that we design instead of just saying, ‘Why did that guy do it this way?’” Mr D’Aunoy said. “We have to look at whether a standard even existed and, if so, was that standard adequate? We don’t want to focus on what a person did or didn’t do if it’s our system and the work that we created that forced them to do that. No error is normal. Context drives behavior.”
Cause mapping, a visual method for analyzing the root causes of an incident, has also become an important part of Precision’s SIF investigation process.
Cause maps provide a visual explanation of why an incident occurred, connecting individual cause-and-effect relationships to reveal the system of causes behind an issue. Investigations back into the causes by asking “why” questions, like “Why did this happen?” The answers are written on a chart, and the investigation looks into why those causes happened.
In addition to the “why” questions, the cause mapping method also asks what was required to produce an effect. Anything that is required to produce an effect is a cause of that effect. Asking what was required allows investigators to build a detailed map that provides a complete representation of an issue.
“We’ve worked with our operational and HSE support personnel on learning and developing the criteria for our cause maps so we can understand where we’re good and where we need to get better at learning,” Mr D’Aunoy said. “The cause maps help our people understand junctures where decision points are being made, and help us figure out whether the procedure that we’ve asked them to do is even right, or do we need to put more controls in place?”
Precision Drilling also implemented a set of “Life-Saving Actions” to act as a guideline for its onsite personnel. The actions, which cover subjects such as working at height (protect yourself from a fall when working at height), mechanical lifting (plan lifting operations and control the area) and working in confined spaces (obtain authorization before entering a confined space), are designed to encourage employee diligence around situational awareness and risk reduction. “These are actions that employees can take to help protect themselves in potential SIF incidents,” Mr D’Aunoy said. “We look at these life-saving actions as our SIF precursor. Our employees understand those actions, and it’s easy for them to cue off of them.”
Empowering crews to observe their own behaviors
Last year, Transocean recorded eight serious near-hit dropped object incidents, or incidents where a dropped object nearly caused a SIF.
Those incidents provided an opportunity for the company to drive a conversation on mitigating SIF potential on its rigs, said Dan Haslam, Director – Operations Integrity and HSE at Transocean. That conversation focused on developing safeguards to mitigate SIFs.
One of the steps the company took was adopting Learning from Normal Work, where personnel examine their own behaviors while on the rig site to spot behaviors that have a positive impact on SIF prevention. These can include, for instance, a driller watching crew members work in the moments when they were not actively engaged in a task.
The program operates under the presumption that accidents and near-misses are rare compared with all the tasks that are actually completed successfully. Instead of learning only after things go wrong, more attention should be paid to how regular activities were completed, what the challenges were in completing those activities, and if they may have contained the seeds of a future incident.
Learning from Normal Work has been implemented by multiple drilling contractors, but the mechanics of its implementation vary. For Transocean, the program centers around review of CCTV footage showing positive actions spotted on the rig as identified by crew members, and study of potential lessons learned from those actions.
“We asked our teams to build a structure where, once a team finishes its work, we look at the footage,” Mr Haslam said. “Of all the things we ask our teams to check, they find the highest amount of weak signals and the most improvement opportunities just by watching themselves perform the work.
“You’ll hear conversations from the things they see when they’re not in the moment. When you’re learning from normal work, you can learn lessons even if nothing bad happened, and you can carry it through to the next time you perform that same activity.”
The company has also focused on testing the health of controls that mitigate or prevent SIFs through WorkSight. This digital assurance and verification program is peer-to-peer and behavior-based; workers note observations of safe work practices on the rig using a mobile app. Senior rig leadership can use these observations to verify the effective implementation of the company’s safety requirements and help them coach crews on hazard identifications.
Job by Design, a concept that aims to drive predictable outcomes by creating job plans that detail key procedural steps, accountabilities and corresponding personnel movement, has also helped Transocean personnel standardize the safe execution of work on the rig.
The job plans serve as a guidance in support of controlled procedures. Personnel are asked to draft these plans for the jobs they perform, using a template that’s accessible to anyone on the rig. They typically outline the optimal number of personnel needed to complete a given job, the travel paths of personnel and equipment during the job, and the potential for human-machine interface within key job steps, including DROPS hazards and specified zones.
Mr Haslam said the concept has provided a simple method for personnel to understand every facet of the work they perform on the rig. By writing down the details of their job in a standardized format, they have to think about every potential hazard they face in the course of completing their work.
“It’s a process where our teams look at the work they’re about to perform and make sure that they minimize or optimize the number of people that are exposed to the hazards,” Mr Haslam said. “If they’re in the red zone, they have to contemplate where they’re going to be when there is loading or moving equipment. We try and keep it as simple as we can.”
Focusing on the ‘what if’ instead of the outcome
H&P has been on a SIF journey for the past decade, Mr Arpe said, ever since the company suffered a pair of fatalities on its rigs in 2014. In 2015, the company kicked off an initiative to analyze past incidents, survey employees and develop steps to reduce the risk of future incidents.
In the years since, H&P has implemented the SIF Decision Tree, a tool that personnel use to determine if an incident had SIF potential, and the SIF Exposure Alert, a brief summary of an incident provided to rigs in order to raise awareness around SIF exposures.
The company also developed LifeBelts, a series of guidelines that set out clear, simple and consistent expectations for high-risk activities on the rigs. These rules are displayed on “nearly every available surface,” Mr Arpe said, at the company’s field and corporate work locations. This helps employees to focus their attention on controlling and removing exposures with the greatest risk.
“We’re focused on the ‘what if’ more than we are around the actual outcome,” he said. “When we started focusing on eliminating SIF exposure, we found that there was not a ton of readily available data that could help us to identify the exposures. We had to develop those systems and build the data ourselves.”
SIFs have become the primary metric by which H&P measures its safety performance, although the company still records TRIR. Mr Arpe noted the difficulty in interacting with operators who have not yet adopted potential SIFs as a key safety metric.
Since SIFs do not measure events that have actually happened, executing a SIF-focused safety protocol requires additional communication with the operator to help them understand the goals behind SIF prevention and why they deserve more attention than incidents where there was no potential for a serious injury.
“TRIR has been ingrained in the industry for a long time,” Mr Arpe said, “so having that conversation with a company or leadership from a company that is still heavily focused on TRIR is extremely difficult when you’re trying to explain why you’re putting so much energy in an event that had no outcome and no injury. It’s very easy for the client to get hung up on that, that you’re not devoting the same amount of energy to both events. We have to say, we care about all the injuries, but we cannot treat all incidents the same. They’re just not the same.” DC