UK government, industry look toward collaboration to drive down decommissioning costs on UKCS
Industry builds on lessons learned and new technologies, while OGA launches knowledge sharing P&A pilot and BEIS considers tax incentives for aging assets
By Eva Vigh, Editorial Coordinator
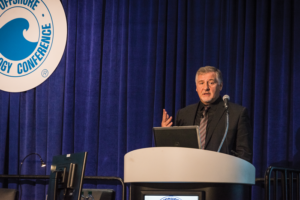
The Oil and Gas Authority (OGA) has committed to reduce decommissioning costs on the UK Continental Shelf (UKCS) by 35% relative to the 2015 base case cost, Gunther Newcombe, OGA Head of Operations, said. The OGA estimates that decommissioning aging platforms on the UKCS could cost an estimated £52 billion, but it appears that both the industry and UK government are pitching in to deliver cost savings.
“The government in the UK has listened carefully to the industry over the last few years,” Mr Newcombe said at an OTC panel session on 3 May in Houston. “We have an accountability to look at cost and efficiencies in decommissioning.”
For example, the OGA is striving for a 35% cost reduction in well plug and abandonment (P&A) operations, which are expected to account for 45% of the total decommissioning costs, he said. To help drive down this cost, the OGA recently launched a multi-operator P&A optimization pilot program to encourage knowledge sharing among operators, as well as to develop improved contracting models. The campaign will culminate with a collaborative well P&A program with the OGA in 2018 or 2019. “We need to have a different delivery capability model,” Mr Newcombe stressed. “We need something totally different to get the price right.”
Alongside the OGA, the UK’s Department of Business, Energy and Industrial Strategy (BEIS) is working to ensure decommissioning in the region occurs at the right cost at the right time. The agency, formerly the Department of Energy and Climate Change, has developed an assessment process that considers factors such as cost, environmental factors and safety risks to guide companies through best practices for decommissioning, said Wendy Kennedy, Chief Executive at BEIS’s Offshore Petroleum Regulator for Environment and Decommissioning unit. “We ask people to consider the different options that they could have,” she said. “We’re working very closely with the OGA to make sure the costs that companies come up with are the best costs and that they’ve thought about different ways of working the problems.”
As for decommissioning costs, BEIS places financial responsibility on companies that have had an operating interest in the field to ease the burden on UK taxpayers. However, they do so in a proportional way, depending on the percentage of field ownership, according to Ms Kennedy. If only one company owns a facility, the regulating body works with the company to determine a reasonable decommissioning payment, she said. As of now, approximately 10% of facilities on the UKCS have been decommissioned, and 55 decommissioning programs are in progress.
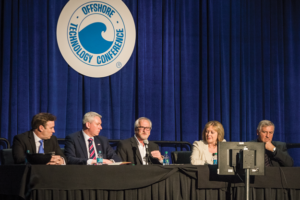
Looking at the future of decommissioning, BEIS is in consultation for a proposal to transfer tax history with asset purchase, meaning a company that purchases an asset would inherit all of its tax history. Since decommissioning in the region is fully tax deductible, the proposal would benefit new players on the UKCS, Ms Kennedy said. “I think it just gives a flavor of how much enthusiasm there is for working with the industry to come up with solutions that actually work,” she added.
For its part, the industry is also working to streamline decommissioning in the region. For example, BP has been able to apply lessons learned from decommissioning projects in the US Gulf of Mexico (GOM) to its operations in the Miller Field, northeast of Aberdeen, said Win Thornton, BP Vice President of Decommissioning.
At 17,000 tons, the Miller platform has one of heaviest steel jackets to be decommissioned in the North Sea, and full or partial jacket removal presents many technical challenges. However, drawing on their experience of briefing jackets in the GOM, BP has opted to remove the jacket in one piece, before towing it for a stage demolition in protected waters.
“There’s still room for improvement, and we’ll build on the lessons learned from interactions with other projects and operators,” Mr Thornton said. “I think we’re a long way along the road to success.”
On the technology side, the industry is working to develop innovative tools that will further reduce the cost of decommissioning, said Roger Esson, Chief Executive at Decom North Sea, an industry organization for the oil and gas late life and decommissioning sector. Mr Esson cited the recent world lifting record by Allseas, an offshore contractor in pipeline installation, heavy lift and subsea construction, in its Shell Brent Delta topside removal in April, as an example of a critical technological advancement.
The feat was achieved using Allseas’ dynamically positioned, single-lift installation/decommissioning vessel, the Pioneering Spirit. “On a global basis, there are many people interested in how that unit can be used to reduce the cost of decommissioning,” he said, adding that innovations are taking place everyday.
“But it’s one tool in the toolbox, and I think it’s fair to say that there isn’t one silver bullet that’s going to reduce cost in decommissioning.” DC