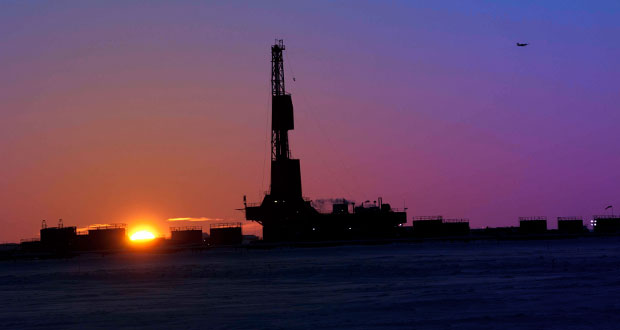
By Linda Hsieh, Editor & Publisher
Although this year’s SPE/IADC Inter-national Drilling Conference was held in Stavanger, Norway, one of the most interesting sessions I attended was actually focused on North American shales. Moderated by Chevron’s VP of Wells Kim McHugh and featuring executives from four of the biggest land drillers in North America – H&P, Nabors, Patterson-UTI and Precision Drilling – the panel showcased to the largely Europe-based and offshore-focused audience just how remarkable the ongoing US shale revolution continues to be, even at this mature stage.
Right off the bat, Ms McHugh opened the session by pointing out the misconception that the US shale and tight revolution is simple – almost cookie cutter: “The term factory is used often, but factory is really about using standardized processes. It’s repeatable, but the wells are different.”
She noted that Chevron drills in three different basins in the Permian across 15 development areas. “Each of those development areas has anywhere from six to 10 benches that we drill for, and each of those benches has different parameters that they have to be drilled in and different lithology. They’re not cookie cutter, but it is an efficient and performance-driven area.”
Just as operators and their shale wells are performance driven, so too are drilling contractors and their rigs. H&P VP Trey Adams noted that 40% of the company’s contracts are now performance based. “Basins are not homogenous. They require different things from us. From a rig equipment and technology standpoint, we have to continue to iterate and improve,” he said.
Not just about the rig
Contractors continue to modify their rigs to keep pace with the intensity of shale drilling. For example, rigs have larger structures and masts to accommodate the pipe needed to drill 2-3 mile-long laterals, said Andy Hendricks, Patterson-UTI President and CEO. But contractors are no longer focused on just the rig. “We’ve also evolved to downhole performance,” he said. “The rigs are not just judged on uptime but on how many feet and how many wells per year we are drilling.”
Innovation downhole is also coming through things like U-shaped wells, which Patterson-UTI now drills to help operators maximize reservoir exposure within their lease holding. The high build rates required to drill these types of wells means the driller can’t use rotary steerables, Mr Hendricks explained. “This is all done with conventional motors and MWD technology, in one run from the kickoff all the way around the bend and back around.”
Another way that contractors are improving efficiency is by leveraging automation and AI to support its drillers. Precision’s Alpha system, for example, takes over redundant and repeatable processes so the driller can focus on higher-value tasks, said President and CEO Kevin Neveu. Over a typical 15-day Permian well, Alpha’s automation can reduce a driller’s machine inputs – through joysticks, buttons and computer screens – from approximately 11,000 to less than 400, he said. “We eliminate human fatigue, human variance, human bias and human error. We can drill the pace-setter well every time now.”
As the US unconventionals market continues to mature, land drillers are now looking to scalability and collaboration to increase the economic value from automation and digitalization. “All of us are on a journey to deploy technology and automation, but if we are all going to invest a lot of money individually, the economic return is going to be compromised,” said Subodh Saxena, Senior VP at Nabors. “The collaboration concept is very, very important.”
While operators and contractors face different drilling challenges in different regions, this panel showcased just how much the world can continue to learn from the ultra-fast-moving unconventionals market and what can be achieved when all stakeholders come together to drive for performance and efficiency. DC