Seadrill: With Statoil active again, Norwegian market looking up for 2010
By Linda Hsieh, managing editor

In the Norwegian segment of the European drilling market, Statoil is a true giant. If it stamps one foot, the whole region will shake and tumble.
In late 2008, when recession hit the global economy, Statoil didn’t stamp its feet; more like, it fell asleep. Unsure how far rig rates would go down, the company began postponing signings of rig contracts, said Sveinung Lofthus, senior vice president – Europe for Seadrill. “We had about one and a half years where activities dried up,” he said.
In a market where one operator has about 75% of the market share, Mr Lofthus said, their inactivity meant the market nearly came to a standstill.
Thankfully, the giant appears to have woken up. “Lately they’ve come back on track. We recently signed up three big contracts with them. We sort of see that the whole market is turning from being in the low end and now coming back,” Mr Lofthus said. “I think the drilling programs that were planned in this part of the world have been falling behind, and there is a backlog on prospects that were going to be drilled.”
Seadrill’s three new contracts with Statoil, announced in Q1 this year, cover one semisubmersible and two jackups, one of which is a newbuild under construction.
Both the West Venture semi and West Epsilon jackup contracts were renewals on expiring arrangements. Under the new contract, the West Venture will drill for Statoil on the Norwegian Continental Shelf (NCS) until August 2015; the rig has been operating on the Troll Field for the past 10 years. The West Epsilon received a four-year contract, with a two-year extension option, that will be in direct continuation of the rig’s current assignment in the North Sea on Sleipner.
The newbuild jackup, named West Elara, received a five-year contract that is scheduled to start in Q3 2011. Seadrill stepped in when the Jurong Shipyard took over the rig from its original owner. “We entered into a contract with the yard to purchase this unit as long as we got a contract, and we managed to get the contract,” Mr Lofthus said.
The Gusto MSC CJ70 150A-design jackup will be able to drill in water depths up to 150 m (nearly 500 ft), making it one of the largest jackups in the world. Combined with its harsh-environment capacity, this rig is actually “going into more the semi competition market,” Mr Lofthus said. Construction is expected to be complete by Q1 2011.
Seadrill is not the only contractor to benefit from Statoil’s revival of activities either. The operator has signed up other multi-year rig contracts in late 2009 and early 2010, such as three-year deals for Saipem’s Scarabeo 5 semi and Dolphin’s Bideford Dolphin semi, both to begin in Q1 2011 and both in direct continuation of their current contracts.
“There is a general feeling that the market is coming back,” Mr Lofthus said. “When the oil price is $80-plus, it’s still a big driver for getting activity back on track again. We see that slowly coming back now.”
In comparison to Norway, the recovery does appear to be slightly slower in the UK, he said, although Seadrill did just move its West Phoenix semi out of Norway to drill on the UK Continental Shelf in the West of Shetland. The rig’s current contract with Total E&P Norge will not end until January 2012, and the new three-year contract will keep the rig employed until January 2015.
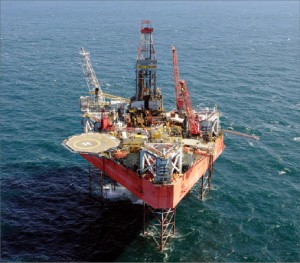
Like drilling activity, rig rates have tumbled over the past couple of years; unlike activity levels, they will be slower to come back. “Our jackup contracts went down about $45,000 to $50,000 per day, and semis are about $100,000 down,” Mr Lofthus said, and he doesn’t expect those rates to increase much in 2010. “This is still a decent level. The other level above this was more of a peak. I think operators have found the level they can accept, and if the market goes up, we will probably see longer terms compared with much higher dayrates.”
EFFICIENCY
Whether it’s Norway or the UK, whether working for a giant like Statoil or a small independent oil company, the maturity of the region demands a high degree of efficiency in order for many prospects to make economical sense.
“We see a lot of prospects in Norway, 50 to 60 million barrels of oil where if you can have efficient drilling and an oil price around $70, these fields will be developed because the infrastructure is there. We see a lot of drive now toward higher and higher efficiency to allow us to drill these fields,” Mr Lofthus said.
To provide that efficiency, which must be achieved without jeopardizing safety, contractors must focus on measurable targets such as meters per day, tripping speeds and connection times. “We need to deliver all these efficiency measures… In the time our clients drill four wells, they need to drill five to defend the investment. If we manage to be the contractor that can do that, and at the same time work controlled and in a safe way, they will preferably have us for the future.”
Mr Lofthus also believes there is a trend to move toward simpler wells in the region. “Sometimes you come to a point where these wells have become so complex, so difficult and so time-consuming that operators are going back to simpler wells. Simpler and shorter wells where we standardize wells and standardize equipment,” he said.
Batch-setting and jumping the BOP between wells and locations are now commonly used techniques on dynamically positioned rigs to improve efficiency. “We take away that loss of time when you have to retrieve the BOP, secure it on deck, etc,” he said.
Certainly there continue to be many complex wells such as multilaterals and complicated technologies like smart completions. However, for smaller pockets of oil, operators may need simpler wells that are faster to drill but more of them. “We will have that combination in Norway of the very complex and technologically driven wells and the easy wells with smaller pockets of oil where you have to get your cost down,” he said.
The same thoughts about simplification can be applied to equipment as well, Mr Lofthus said. Most rigs in the North Sea, certainly in Norway, have automatic handling of more or less everything on the rig floor. Yet rigs are starting to get so complex that they may need to be simplified in order to get the best out of them, he continued. “The focus going forward will be working very closely with our vendors to find ways of doing things smarter, simpler, safer and more efficiently.”
He also believes the industry needs to more often ask “Why?” and “What do we want to benefit from this?” when faced with new automation tools. “People are popping up with new ideas all the time. If you ask, ‘What’s the problem?’ sometimes you don’t get an answer. There should at least be a problem before you’re going to solve it.”
RIG SUPPLY
Looking at his own European division within Seadrill, Mr Lofthus noted that not only does he have to compete with other drilling contractors, in a way he also has to compete internally with Seadrill’s other divisions to keep rigs and activity in the European area. “The biggest disadvantage is actually cost. We have very high crew costs (in Norway). Where other areas have four crews, we have six crews because they’re on a 2-4 schedule,” he said. This not only means higher costs, but crews also have to work longer before they get the same experience.
“At the same time, we have an education system that gives us very skilled people, so we manage to run our rigs with fewer people than we do internationally.” A typical dual-activity drillship in Norway can operate with about 64 people, whereas internationally it would need 75 to 79 people, he said.
“The challenge we have in the whole sector is that we are a mature area, and the rigs and rig rates are set in a global market. We need to get really efficient operations to allow our operators to continue drilling,” he said. With the types of small pockets of oil that are prevalent in this region, “if you have high rig rates and slow progress, then it’s not of value anymore.”