Keithville Well Drilling to deploy new Schramm rig to Haynesville
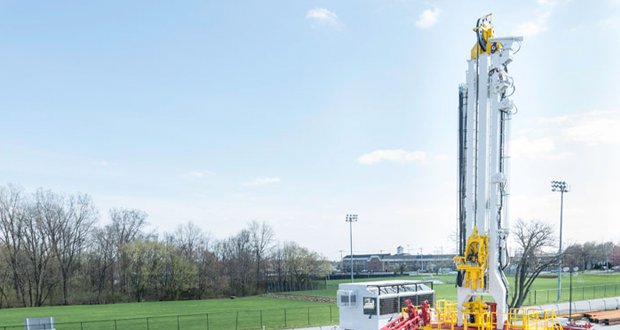

Keithville Well Drilling, a Louisiana-based drilling company, has purchased and accepted delivery of the Schramm T250XD, a land-based rig designed for shale drilling. The company plans to deploy the rig to the Haynesville Shale of Northwest Louisiana and East Texas.
“We are excited to begin using the T250XD rig, which we see as a direct answer to our industry’s need for smaller and more mobile top-hole drilling rigs for use in unconventional plays,” Keithville CEO Jeff Talley said. “We anticipate that utilizing the T250XD for top-hole drilling will enable us to safely and responsibly reduce cycle times and thus overall drilling costs, while also reducing the footprint of our drilling pads.”
Schramm’s electric-over-hydraulic drilling rig was introduced at the 2014 Offshore Technology Conference in Houston. The T250XD features increased top drive travel, added BOP clearance and an operator’s control room equipped with Schramm’s proprietary online integrated real-time documentation system Rig-ID. This web based library enables documentation access from remote operating centers around the globe via satellite or the Internet. The T250XD provides 250,000 lbs of hookload using Schramm’s patented Telemast technology and is equipped with its LoadSafe XD fully automated, hands-free pipe-handling system.
“We are very pleased with the opportunity to provide Keithville with our most innovative new rig, which was designed to increase the overall efficiency, safety and cost-effectiveness of shale drilling programs,” Schramm CEO Ed Breiner said.
Rig-ID is a trademark of Schramm. Telemast and LoadSafe are registered trademarks of Schramm.